PCB Layer Materials
A PCB consists of alternating layers of conductive and insulating materials bonded together under heat and pressure. The conductive layers are typically copper foil, while the insulating layers are usually made of a glass-reinforced epoxy laminate called FR-4.
Copper Foil
Copper is used for the conductive layers because of its excellent electrical conductivity, solderability, and resistance to corrosion. The thickness of the copper foil is measured in ounces per square foot, with common thicknesses being:
Copper Weight (oz) | Thickness (mm) |
---|---|
0.5 | 0.017 |
1 | 0.035 |
2 | 0.070 |
Thicker copper allows higher current carrying capacity but makes fine pitch traces and spaces more challenging. Thinner copper enables finer features but limits power handling.
FR-4 Laminate
FR-4 (Flame Retardant 4) is a composite material made of woven fiberglass cloth impregnated with an epoxy resin binder. It provides mechanical strength and electrical insulation between the copper layers.
Important properties of FR-4 include:
– High dielectric strength
– Good thermal stability
– Flame resistance
– Mechanical durability
The thickness of the FR-4 prepreg and core layers determines the overall thickness of the PCB. Standard FR-4 thicknesses range from 0.2mm to 3.2mm.
Solder Mask
A solder mask is applied over the outer copper layers of a PCB, covering the areas that should not be soldered. It prevents solder bridges, protects against oxidation, and provides electrical insulation.
Solder mask is typically a polymer ink that is silkscreened onto the board and then cured. The most common Solder Mask Colors are green, red, blue, black, and white.
Silkscreen
The silkscreen layer is used to add text and graphics to a PCB for assembly and identification purposes. It is typically a white polymer ink printed onto the solder mask.
Information printed on the silkscreen can include:
– Component outlines and reference designators
– Company logos and product branding
– Regulatory compliance marks
– Date codes and serial numbers
Types of PCB Layer Stackups
The number and arrangement of layers in a PCB Stackup depends on the complexity and requirements of the circuit. More layers allow for higher component density and signal routing options, but also increase manufacturing cost and design challenges.
Single Layer
A single layer PCB has conductive copper on only one side of the substrate. Components are mounted on the opposite side, with through-hole leads soldered to the copper.
Single layer boards offer the lowest cost and simplest manufacturing, but have limited routing density and are typically only used for very basic circuits.
Double Layer
A double layer PCB has copper on both sides of the substrate. Components can be mounted on either side, with electrical connections made by drilling through-holes and electroplating them with copper.
Double sided boards allow for much higher component density than single layer. They are the most common type of PCB.
Multi-Layer
A multi-layer PCB has three or more conductive layers laminated with insulating layers in between. The inner layers are used for signal routing, power distribution, and grounding. The outer layers are used for component mounting and interconnects.
The number of layers in a multi-layer PCB is always even, with common layer counts being 4, 6, 8, 10, and 12. Higher layer counts enable very dense designs but have diminishing returns in terms of cost and manufacturability.
Here are some typical multi-layer PCB stackups:
Layers | Stackup |
---|---|
4 | Signal – Ground – Power – Signal |
6 | Signal – Ground – Signal – Signal – Ground – Signal |
8 | Signal – Ground – Signal – Power – Signal – Ground – Signal – Signal |
The arrangement of signal, power, and ground layers in a multi-layer stackup has a major impact on signal integrity, power delivery, and EMI suppression. Careful stackup design is critical for high-speed and High-Frequency PCBs.
PCB Buildup Design Considerations
When designing the buildup of a PCB, engineers must balance the electrical, mechanical, and manufacturing requirements of the application. Some key design considerations include:
Layer Count
The number of layers in a PCB directly affects its routing density, signal integrity, power distribution, and cost. More layers provide more flexibility but also increase complexity.
Factors that influence the choice of layer count include:
– Number and types of components
– Signal speeds and frequencies
– Power requirements
– Electromagnetic compatibility (EMC)
– Size and weight constraints
– Budget and schedule
As a general rule, use the minimum number of layers that meet the functional and performance requirements of the design.
Dielectric Thickness
The thickness of the dielectric material between layers affects the impedance and propagation delay of signals. Thinner dielectrics enable finer trace geometries and higher routing density, but also increase the risk of signal integrity issues like crosstalk.
The dielectric thickness also determines the capacitance between power and ground planes, which impacts power delivery and decoupling.
Common dielectric thicknesses range from 2 to 8 mils (0.05 to 0.2 mm), with thinner dielectrics used for high-speed designs and thicker dielectrics used for high-voltage designs.
Copper Thickness
The thickness of the copper layers affects their current carrying capacity, voltage drop, and thermal performance. Thicker copper allows for higher power handling and lower resistance, but also increases the PCB’s weight and cost.
Signal traces typically use 0.5 or 1 oz copper, while power traces and planes may use 2 oz or thicker copper.
The Aspect Ratio of a trace’s width to its thickness also affects its impedance and current capacity. A good rule of thumb is to keep the aspect ratio below 10:1 to avoid manufacturing issues.
Via Types
Vias are holes drilled through a PCB to connect traces on different layers. The type and size of vias used in a design affect its routing density, signal integrity, and manufacturability.
Common types of vias include:
– Through vias – drilled through the entire board
– Blind vias – drilled from an outer layer to an inner layer
– Buried vias – drilled between inner layers only
Through vias are the simplest and cheapest, but consume the most board area. Blind and buried vias enable higher density routing but are more expensive to fabricate.
The diameter of a via’s drill hole and Annular Ring also impact its electrical and mechanical properties. Smaller vias allow tighter routing but have higher inductance and are more prone to manufacturing defects.
Impedance Control
Controlling the characteristic impedance of PCB traces is critical for maintaining signal integrity, especially at high frequencies. Impedance mismatches can cause reflections, ringing, and other issues that degrade signal quality.
The main factors that affect a trace’s impedance are:
– The width and thickness of the trace
– The distance between the trace and reference plane(s)
– The dielectric constant of the substrate material
PCB designers use calculators and field solvers to determine the geometry needed to achieve a target impedance, typically 50 ohms for single-ended traces and 100 ohms for differential pairs.
Accurate impedance control requires careful control of the PCB fabrication process, including the dielectric thickness, copper thickness, and etching tolerances. Many high-speed designs specify impedance requirements as part of the fabrication drawing.
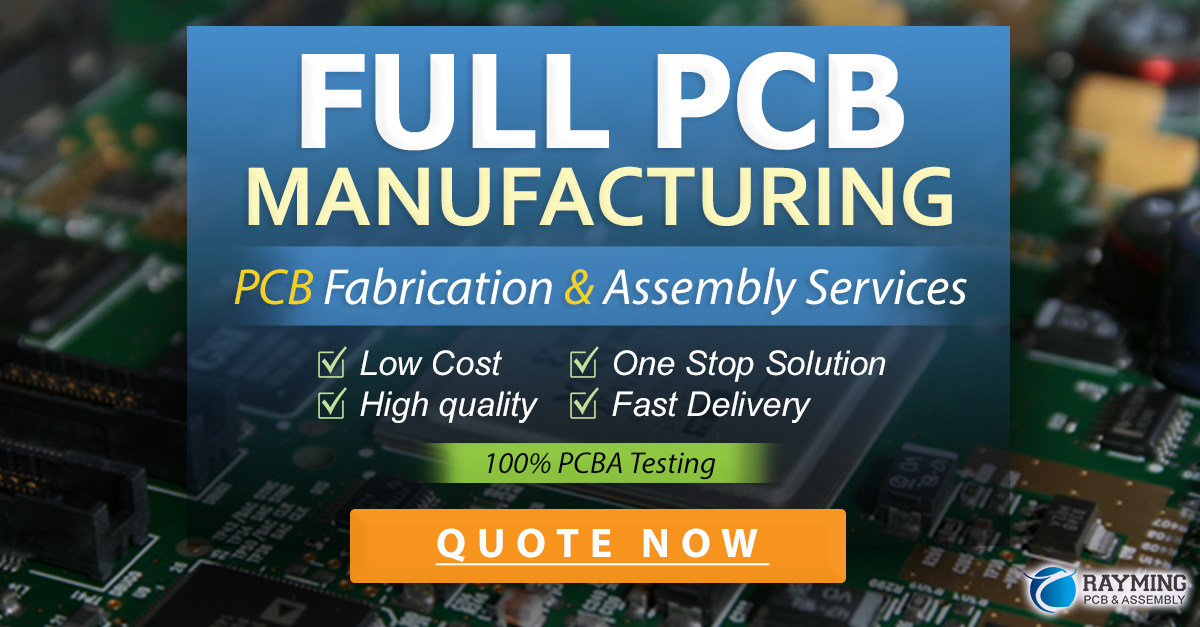
Frequently Asked Questions
What is the most common PCB layer stackup?
The most common PCB layer stackup is a 4-layer board with a signal-ground-power-signal arrangement. This provides a good balance of routing density, signal integrity, and power delivery for many applications.
How much does adding layers increase the cost of a PCB?
Adding layers to a PCB increases its material and processing costs, with each additional layer typically adding 20-30% to the total cost. However, the incremental cost per layer decreases as the total layer count increases.
What is the maximum number of layers in a PCB?
There is no hard limit to the number of layers in a PCB, but practical and economic considerations usually limit designs to 50 layers or less. The most complex PCBs, such as those used in supercomputers and networking equipment, can have over 100 layers.
How does the PCB buildup affect signal integrity?
The PCB buildup has a major impact on signal integrity, especially at high speeds and frequencies. The key factors are the dielectric thickness, trace geometry, and reference plane arrangement.
Thinner dielectrics and narrower traces result in higher impedance and more coupling between signals. Careful stackup design is needed to maintain controlled impedances, minimize crosstalk, and ensure proper grounding and shielding.
What materials other than FR-4 are used in PCBs?
While FR-4 is the most common PCB material, other laminates are used for specialty applications. These include:
– High-frequency materials like Rogers RO4000 and Isola I-Tera
– High-temperature materials like polyimide and PEEK
– Flexible materials like polyimide and PET
– Metal-core materials for LED lighting and power electronics
The choice of laminate material depends on the electrical, thermal, mechanical, and environmental requirements of the application.
Leave a Reply