What are PCB tolerances?
PCB (Printed Circuit Board) tolerances refer to the acceptable range of variation in the physical dimensions and properties of a PCB during the manufacturing process. These tolerances are essential to ensure that the PCB functions as intended and fits properly within the designed system. Understanding and adhering to PCB Tolerances is crucial for achieving a high-quality and reliable end product.
Types of PCB Tolerances
There are several types of tolerances that need to be considered when designing and manufacturing a PCB:
-
Dimensional Tolerances: These tolerances relate to the physical dimensions of the PCB, such as length, width, thickness, and hole sizes.
-
Electrical Tolerances: These tolerances pertain to the electrical properties of the PCB, including conductor width, spacing, and impedance.
-
Material Tolerances: These tolerances involve the properties of the materials used in PCB Fabrication, such as the dielectric constant and thermal expansion coefficient.
-
Assembly Tolerances: These tolerances apply to the placement and alignment of components on the PCB during the assembly process.
Why are PCB Tolerances Important?
PCB tolerances play a vital role in ensuring the proper functioning, reliability, and manufacturability of a PCB. Here are some key reasons why PCB tolerances are important:
1. Functionality
Adhering to PCB tolerances ensures that the PCB functions as intended. Deviations from the specified tolerances can lead to issues such as signal integrity problems, impedance mismatches, and short circuits. By maintaining the required tolerances, designers can guarantee that the PCB will perform optimally within the designed system.
2. Reliability
PCB tolerances contribute to the overall reliability of the final product. When tolerances are not met, it can result in mechanical stress, poor electrical connections, and reduced durability. By adhering to the specified tolerances, manufacturers can minimize the risk of failures and ensure that the PCB can withstand the intended operating conditions.
3. Manufacturability
PCB tolerances are crucial for the manufacturability of the board. If the tolerances are too tight, it can lead to increased manufacturing costs and lower yields. On the other hand, if the tolerances are too loose, it can result in poor quality and inconsistent performance. Striking the right balance between design requirements and manufacturing capabilities is essential for cost-effective and efficient PCB production.
4. Compatibility
PCB tolerances ensure compatibility with other components and systems. When designing a PCB, it is important to consider the tolerances of the components that will be mounted on the board, as well as the tolerances of the enclosure or system in which the PCB will be installed. Proper tolerance management ensures that all components fit together seamlessly and function as intended.
Common PCB Tolerance Specifications
To effectively design and manufacture PCBs, it is essential to understand common tolerance specifications. Here are some key tolerance specifications that are often encountered in PCB design and manufacturing:
1. Trace Width and Spacing
Trace width and spacing tolerances refer to the acceptable variations in the width of the copper traces and the spacing between them. These tolerances are critical for maintaining signal integrity and preventing short circuits. The specific tolerances depend on the PCB fabrication process and the design requirements.
Trace Width | Minimum Spacing |
---|---|
0.1 mm | 0.1 mm |
0.2 mm | 0.2 mm |
0.3 mm | 0.3 mm |
0.4 mm | 0.4 mm |
2. Hole Size and Placement
Hole size and placement tolerances relate to the acceptable variations in the diameter and location of holes drilled in the PCB. These holes are used for mounting components, vias, and connectors. Maintaining accurate hole sizes and placement is crucial for proper component fit and alignment.
Hole Diameter | Tolerance |
---|---|
0.5 mm | ±0.05 mm |
1.0 mm | ±0.1 mm |
2.0 mm | ±0.15 mm |
3.0 mm | ±0.2 mm |
3. Board Thickness
Board thickness tolerances specify the acceptable range of variation in the thickness of the PCB substrate. The thickness of the PCB affects its mechanical strength, thermal dissipation, and impedance characteristics. Maintaining consistent board thickness is important for ensuring the overall performance and reliability of the PCB.
Nominal Thickness | Tolerance |
---|---|
0.8 mm | ±0.1 mm |
1.6 mm | ±0.15 mm |
2.4 mm | ±0.2 mm |
4. Solder Mask and Silkscreen
Solder mask and silkscreen tolerances define the acceptable variations in the application of solder mask and silkscreen on the PCB. Solder mask helps prevent short circuits and provides protection against environmental factors, while silkscreen is used for labeling and identification. Maintaining accurate solder mask and silkscreen tolerances enhances the PCB’s reliability and ease of assembly.
Feature | Tolerance |
---|---|
Solder Mask | ±0.05 mm |
Silkscreen | ±0.1 mm |
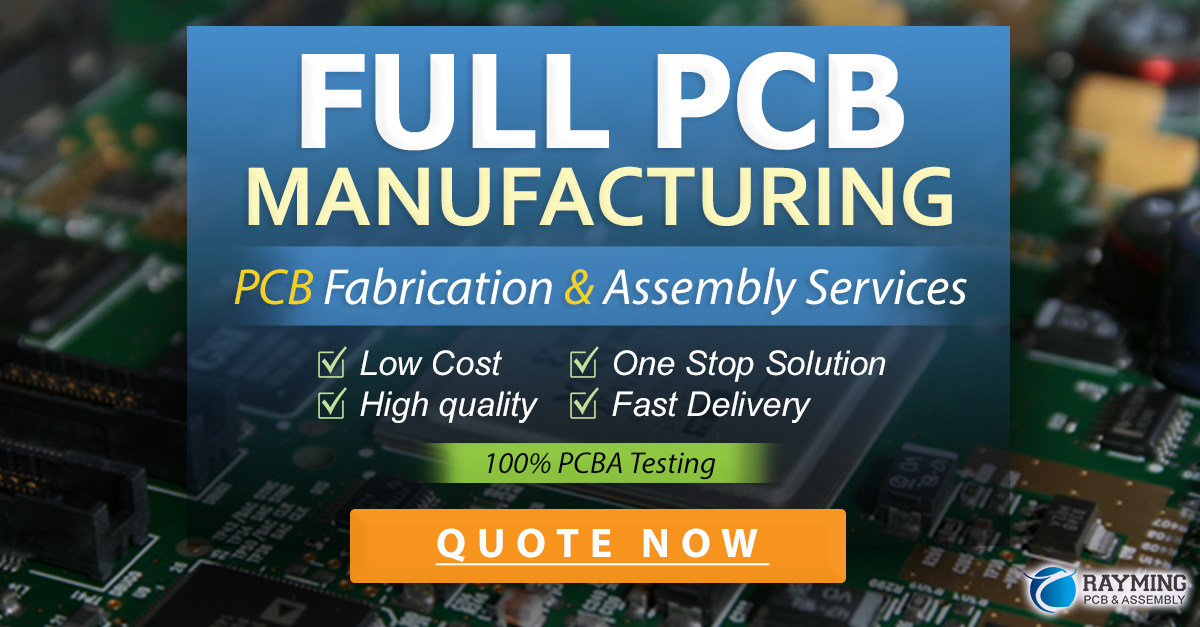
Designing for PCB Tolerances
To ensure that a PCB meets the required tolerances and functions as intended, designers must consider several factors during the design process:
1. Design Rules
Adhering to established design rules is crucial for maintaining PCB tolerances. These rules specify the minimum trace widths, spacing, hole sizes, and other parameters that must be followed to ensure manufacturability and reliability. Designers should consult with the PCB manufacturer to understand their specific design rules and capabilities.
2. Material Selection
The choice of PCB materials can impact the achievable tolerances. Different substrate materials have varying properties, such as dielectric constant, thermal expansion coefficient, and dimensional stability. Designers should select materials that are compatible with the desired tolerances and the intended application of the PCB.
3. Layer Stack-up
The layer stack-up of a PCB refers to the arrangement of copper layers and dielectric materials. Proper layer stack-up design is essential for maintaining controlled impedance, minimizing crosstalk, and achieving the required electrical performance. Designers should work closely with the PCB manufacturer to optimize the layer stack-up for the specific design requirements and tolerances.
4. Component Placement
Component placement plays a significant role in PCB tolerances. Designers should consider the tolerances of the components themselves, as well as the tolerances of the PCB features that interact with them, such as pads and holes. Proper component placement helps ensure reliable soldering, reduces mechanical stress, and facilitates efficient assembly.
Manufacturing Considerations
In addition to design considerations, several manufacturing factors influence PCB tolerances:
1. Fabrication Process
The choice of PCB fabrication process can impact the achievable tolerances. Different manufacturing technologies, such as standard etching, high-density interconnect (HDI), and microvias, have varying capabilities in terms of trace widths, spacing, and hole sizes. Designers should select a fabrication process that aligns with the required tolerances and the complexity of the PCB design.
2. Quality Control
Robust quality control measures are essential for maintaining PCB tolerances throughout the manufacturing process. PCB Manufacturers employ various inspection and testing techniques, such as automated optical inspection (AOI), X-ray inspection, and electrical testing, to ensure that the fabricated boards meet the specified tolerances. Adequate quality control helps identify and rectify any deviations from the desired tolerances.
3. Supplier Selection
Choosing a reliable and experienced PCB manufacturer is crucial for achieving the required tolerances. Designers should work with manufacturers who have a proven track record of delivering high-quality PCBs and have the necessary capabilities to meet the specific tolerance requirements. Effective communication and collaboration between the designer and the manufacturer are essential for successful PCB production.
Frequently Asked Questions (FAQ)
-
What happens if PCB tolerances are not met?
If PCB tolerances are not met, it can lead to various issues, such as poor functionality, reduced reliability, and compatibility problems. Deviations from the specified tolerances can cause signal integrity issues, short circuits, mechanical stress, and difficulties in component assembly. -
How can I ensure that my PCB design meets the required tolerances?
To ensure that your PCB design meets the required tolerances, follow these steps: - Adhere to the established design rules and guidelines provided by the PCB manufacturer.
- Select appropriate materials that are compatible with the desired tolerances.
- Optimize the layer stack-up for controlled impedance and electrical performance.
- Consider the tolerances of components and their placement on the PCB.
-
Communicate effectively with the PCB manufacturer to understand their capabilities and limitations.
-
What are the consequences of overly tight or loose PCB tolerances?
Overly tight PCB tolerances can lead to increased manufacturing costs, lower yields, and potential difficulties in fabrication. On the other hand, overly loose tolerances can result in poor quality, inconsistent performance, and reduced reliability. It is important to strike a balance between design requirements and manufacturing capabilities to achieve cost-effective and reliable PCB production. -
How can I verify that the manufactured PCB meets the specified tolerances?
To verify that the manufactured PCB meets the specified tolerances, several inspection and testing techniques can be employed, such as: - Automated optical inspection (AOI) to check for dimensional accuracy and defects.
- X-ray inspection to examine internal layers and vias.
- Electrical testing to verify the functionality and performance of the PCB.
- Cross-sectional analysis to measure the thickness and spacing of copper features.
-
Coordinate measuring machines (CMMs) to precisely measure the physical dimensions of the PCB.
-
What should I do if I encounter tolerance issues during PCB production?
If you encounter tolerance issues during PCB production, take the following steps: - Communicate the issues to the PCB manufacturer and provide detailed information about the deviations from the specified tolerances.
- Work collaboratively with the manufacturer to identify the root cause of the tolerance issues and determine appropriate corrective actions.
- Review and adjust the PCB design if necessary to accommodate the manufacturing capabilities and limitations.
- Implement stricter quality control measures to prevent similar issues in future production runs.
- Consider alternative manufacturing processes or suppliers if the tolerance issues persist.
Conclusion
Understanding and managing PCB tolerances is crucial for designing and manufacturing high-quality and reliable printed circuit boards. Tolerances encompass various aspects, including dimensional accuracy, electrical properties, material characteristics, and assembly considerations. By adhering to established design rules, selecting appropriate materials, optimizing layer stack-up, and considering component placement, designers can ensure that their PCB designs meet the required tolerances.
Moreover, effective collaboration with PCB manufacturers, robust quality control measures, and careful supplier selection are essential for achieving the desired tolerances consistently. Regular communication, inspection, and testing throughout the manufacturing process help identify and rectify any deviations from the specified tolerances.
By understanding the importance of PCB tolerances and implementing best practices in design and manufacturing, engineers and manufacturers can produce PCBs that function as intended, exhibit high reliability, and meet the demands of various applications. Continual advancements in PCB manufacturing technologies and materials further enable the achievement of tighter tolerances and more complex designs.
As the electronics industry continues to evolve, staying updated with the latest tolerance specifications, design guidelines, and manufacturing capabilities is essential for successful PCB Development. By embracing a comprehensive approach to PCB tolerances, designers and manufacturers can deliver innovative and reliable electronic products that meet the ever-increasing demands of modern applications.
Leave a Reply