What are PCB Tolerances?
PCB tolerances refer to the acceptable variations in the dimensions and properties of a PCB during the manufacturing process. These tolerances are necessary because it is virtually impossible to manufacture a PCB with exact dimensions and specifications every single time. Tolerances allow for slight deviations from the ideal measurements while still ensuring that the PCB functions as intended.
Types of PCB Tolerances
There are several types of tolerances that must be considered when designing and manufacturing a PCB. Some of the most important tolerances include:
- Track width tolerances
- Isolation gap tolerances
- Hole size tolerances
- Copper thickness tolerances
- Solder mask tolerances
- Silkscreen tolerances
In this article, we will focus on track width and isolation gap tolerances, as they are critical to the performance and reliability of a PCB.
Track Width Tolerances
Track width, also known as trace width, refers to the width of the copper tracks on a PCB. These tracks are responsible for carrying electrical signals between components on the board. The width of the tracks is determined by several factors, including the current carrying capacity, the required impedance, and the available space on the PCB.
Factors Affecting Track Width Tolerances
Several factors can influence the track width tolerances on a PCB:
-
Manufacturing process: The manufacturing process used to create the PCB can have a significant impact on track width tolerances. Different processes, such as etching, plating, or milling, have their own inherent tolerances that must be accounted for.
-
Material properties: The properties of the PCB material, such as the copper weight and the substrate material, can affect track width tolerances. For example, thicker copper layers may require wider tolerances due to the increased difficulty in etching fine features.
-
PCB design: The design of the PCB itself can influence track width tolerances. Features such as sharp angles, long parallel tracks, and high-density layouts can make it more challenging to maintain tight tolerances.
Calculating Track Width Tolerances
To calculate the appropriate track width tolerances for your PCB design, you need to consider the following factors:
- The minimum and maximum track widths allowed by your PCB manufacturer
- The copper weight of the PCB
- The desired current carrying capacity of the tracks
- The required impedance of the tracks
Based on these factors, you can use standard formulas or consult with your PCB manufacturer to determine the appropriate track width tolerances for your design.
Track Width Tolerance Examples
To better understand track width tolerances, let’s consider a few examples:
Copper Weight (oz) | Minimum Track Width (mm) | Maximum Track Width (mm) | Tolerance (±mm) |
---|---|---|---|
0.5 | 0.15 | 0.20 | 0.025 |
1.0 | 0.20 | 0.30 | 0.05 |
2.0 | 0.30 | 0.40 | 0.05 |
In these examples, the tolerance represents the acceptable deviation from the nominal track width. For instance, a 0.20mm track with a tolerance of ±0.025mm could have an actual width between 0.175mm and 0.225mm and still be considered within the acceptable range.
Isolation Gap Tolerances
Isolation gaps, also known as clearances, refer to the minimum distance between two conductive features on a PCB, such as tracks, pads, or vias. These gaps are essential for preventing short circuits and ensuring the proper functioning of the PCB.
Factors Affecting Isolation Gap Tolerances
Several factors can influence the isolation gap tolerances on a PCB:
-
Voltage requirements: The voltage levels present on the PCB can dictate the minimum isolation gaps required to prevent arcing or leakage currents.
-
Manufacturing process: As with track width tolerances, the manufacturing process used to create the PCB can affect isolation gap tolerances. Some processes may have limitations on how small the gaps can be reliably produced.
-
PCB design: The complexity of the PCB design, including the density of components and tracks, can make it more challenging to maintain consistent isolation gaps.
Calculating Isolation Gap Tolerances
To calculate the appropriate isolation gap tolerances for your PCB design, you need to consider the following factors:
- The voltage levels present on the PCB
- The minimum isolation gaps allowed by your PCB manufacturer
- The PCB material and its dielectric strength
- The applicable industry standards or regulations
Based on these factors, you can determine the minimum isolation gaps required for your design and work with your PCB manufacturer to establish appropriate tolerances.
Isolation Gap Tolerance Examples
Let’s look at a few examples of isolation gap tolerances:
Voltage Level (V) | Minimum Isolation Gap (mm) | Tolerance (±mm) |
---|---|---|
<50 | 0.15 | 0.05 |
50-100 | 0.20 | 0.05 |
100-150 | 0.25 | 0.05 |
In these examples, the tolerance represents the acceptable deviation from the minimum isolation gap. For instance, a minimum isolation gap of 0.20mm with a tolerance of ±0.05mm could have an actual gap between 0.15mm and 0.25mm and still be considered within the acceptable range.
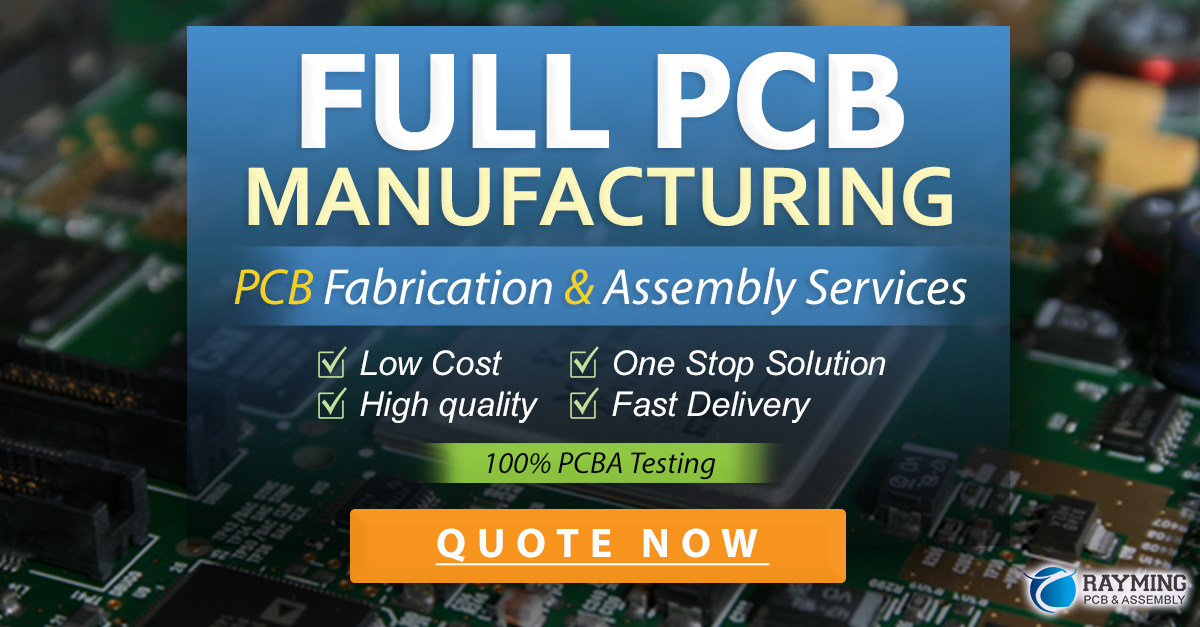
Managing PCB Tolerances in Your Designs
To effectively manage PCB tolerances in your designs, consider the following tips:
-
Communicate with your PCB manufacturer: Discuss your design requirements and tolerances with your PCB manufacturer early in the design process. They can provide valuable insights and guidance based on their experience and capabilities.
-
Use design for manufacturing (DFM) principles: Incorporate DFM principles into your PCB designs to ensure that they are manufacturable and can be produced with the desired tolerances. This may involve adjusting track widths, isolation gaps, or other design features to accommodate manufacturing constraints.
-
Perform tolerance analysis: Use tolerance analysis tools to evaluate the impact of tolerances on your PCB design. These tools can help you identify potential issues and optimize your design for manufacturability.
-
Consider the impact of tolerances on assembly: PCB tolerances can also affect the assembly process, particularly when it comes to component placement and soldering. Ensure that your design accounts for these tolerances to avoid assembly issues.
-
Document and communicate tolerances: Clearly document the required tolerances in your PCB design files and communicate them to all stakeholders, including your PCB manufacturer and assembly partner. This helps ensure that everyone is working towards the same goals and reduces the risk of misunderstandings or errors.
Frequently Asked Questions
- What happens if the track width or isolation gap tolerances are not met?
If the track width or isolation gap tolerances are not met, it can lead to various issues, such as: - Increased resistance in the tracks, leading to voltage drops or heat generation
- Insufficient isolation between conductive features, increasing the risk of short circuits or signal crosstalk
-
Difficulty in manufacturing the PCB, resulting in lower yields or higher costs
-
How can I ensure that my PCB design meets the required tolerances?
To ensure that your PCB design meets the required tolerances: - Communicate with your PCB manufacturer and understand their capabilities and limitations
- Use DFM principles and guidelines when designing your PCB
- Perform tolerance analysis to identify and address potential issues
-
Clearly document and communicate the required tolerances to all stakeholders
-
Can I use tighter tolerances to improve the performance of my PCB?
While using tighter tolerances can potentially improve the performance of your PCB, it also comes with some trade-offs: - Tighter tolerances may increase the manufacturing cost of the PCB
- Not all PCB Manufacturers can consistently achieve very tight tolerances
-
Tighter tolerances may make the PCB more difficult to manufacture, leading to lower yields or longer lead times
-
How do I choose the right tolerances for my PCB design?
Choosing the right tolerances for your PCB design involves considering several factors: - The functional requirements of your PCB, such as the required current carrying capacity or impedance
- The manufacturing capabilities of your PCB manufacturer
- The applicable industry standards or regulations
-
The cost and lead time implications of different tolerance levels
-
What are the most common issues related to PCB tolerances?
Some of the most common issues related to PCB tolerances include: - Inconsistent track widths or isolation gaps, leading to performance or reliability issues
- Difficulty in manufacturing the PCB due to overly tight tolerances
- Increased manufacturing costs or lead times due to tight tolerances
- Misunderstandings or miscommunications regarding the required tolerances between the PCB designer and manufacturer
Conclusion
Understanding and managing manufacturing tolerances, particularly track width and isolation gap tolerances, is crucial for ensuring the performance, reliability, and manufacturability of your PCB designs. By considering the factors that affect these tolerances, calculating the appropriate values, and effectively communicating with your PCB manufacturer, you can create PCB designs that meet your requirements while being cost-effective and producible.
Remember to incorporate DFM principles, perform tolerance analysis, and clearly document and communicate your tolerance requirements to all stakeholders. By doing so, you can minimize the risk of issues related to PCB tolerances and ensure the success of your PCB projects.
Leave a Reply