Introduction to PCB Surface Finishes
Printed Circuit Boards (PCBs) are essential components in modern electronics, providing a platform for connecting and supporting electronic components. One crucial aspect of PCB manufacturing is the application of surface finishes, which serve various purposes, including protection against oxidation, enhanced solderability, and improved electrical conductivity. In this comprehensive article, we will delve into the world of PCB Prototype surface finishes, exploring their types, characteristics, and applications.
The Importance of PCB Surface Finishes
PCB surface finishes play a vital role in ensuring the reliability and longevity of electronic devices. They provide several key benefits:
- Protection against oxidation: Surface finishes act as a barrier, preventing the exposed copper on the PCB from oxidizing and deteriorating over time.
- Enhanced solderability: Certain surface finishes, such as HASL and ENIG, improve the solderability of the PCB, making it easier to attach components during the assembly process.
- Improved electrical conductivity: Some surface finishes, like silver and gold, offer excellent electrical conductivity, minimizing signal loss and ensuring optimal performance.
- Aesthetics: Surface finishes can also enhance the visual appeal of PCBs, giving them a professional and polished look.
Types of PCB Surface Finishes
There are several types of PCB surface finishes available, each with its own unique properties and advantages. Let’s explore some of the most common ones:
1. HASL (Hot Air Solder Leveling)
HASL is one of the most widely used PCB surface finishes. In this process, the PCB is dipped into a molten solder bath, and then hot air is used to blow off the excess solder, leaving a thin, uniform layer on the exposed copper surfaces. HASL provides excellent solderability and is relatively inexpensive compared to other surface finishes.
Advantages of HASL:
– Good solderability
– Cost-effective
– Suitable for most applications
– Provides a reliable and durable finish
Disadvantages of HASL:
– Uneven surface due to the nature of the process
– Not suitable for fine-pitch components
– Potential for solder bridging
– Limited shelf life
2. ENIG (Electroless Nickel Immersion Gold)
ENIG is a two-layer surface finish that consists of a nickel layer deposited on the copper surface, followed by a thin layer of gold. The nickel layer provides a barrier against copper diffusion, while the gold layer offers excellent solderability and protection against oxidation.
Advantages of ENIG:
– Flat and uniform surface
– Suitable for fine-pitch components
– Excellent solderability
– Long shelf life
– Good electrical conductivity
– Suitable for wire bonding
Disadvantages of ENIG:
– Higher cost compared to HASL
– Potential for black pad syndrome (brittle nickel-phosphorus layer)
– Gold can dissolve into the solder joint during assembly
3. OSP (Organic Solderability Preservative)
OSP is a chemical coating that is applied to the exposed copper surfaces of the PCB. It forms a thin, transparent layer that protects the copper from oxidation and provides good solderability. OSP is an environmentally friendly and cost-effective surface finish option.
Advantages of OSP:
– Cost-effective
– Environmentally friendly
– Flat and uniform surface
– Suitable for fine-pitch components
– Good solderability
Disadvantages of OSP:
– Limited shelf life (typically 6-12 months)
– Not suitable for multiple reflow cycles
– Can be damaged by handling and cleaning processes
4. Immersion Silver
Immersion silver is a chemical process that deposits a thin layer of silver onto the exposed copper surfaces of the PCB. It provides excellent solderability and good electrical conductivity. Immersion silver is often used as a more cost-effective alternative to ENIG.
Advantages of Immersion Silver:
– Good solderability
– Excellent electrical conductivity
– Flat and uniform surface
– Suitable for fine-pitch components
– Cost-effective compared to ENIG
Disadvantages of Immersion Silver:
– Potential for silver migration and dendrite growth
– Limited shelf life (typically 6-12 months)
– Can tarnish over time
5. Immersion Tin
Immersion tin is a chemical process that deposits a thin layer of tin onto the exposed copper surfaces of the PCB. It provides good solderability and is often used as a lead-free alternative to HASL.
Advantages of Immersion Tin:
– Good solderability
– Lead-free and RoHS compliant
– Flat and uniform surface
– Suitable for fine-pitch components
Disadvantages of Immersion Tin:
– Potential for tin whiskers, which can cause short circuits
– Limited shelf life (typically 6-12 months)
– Can be prone to oxidation over time
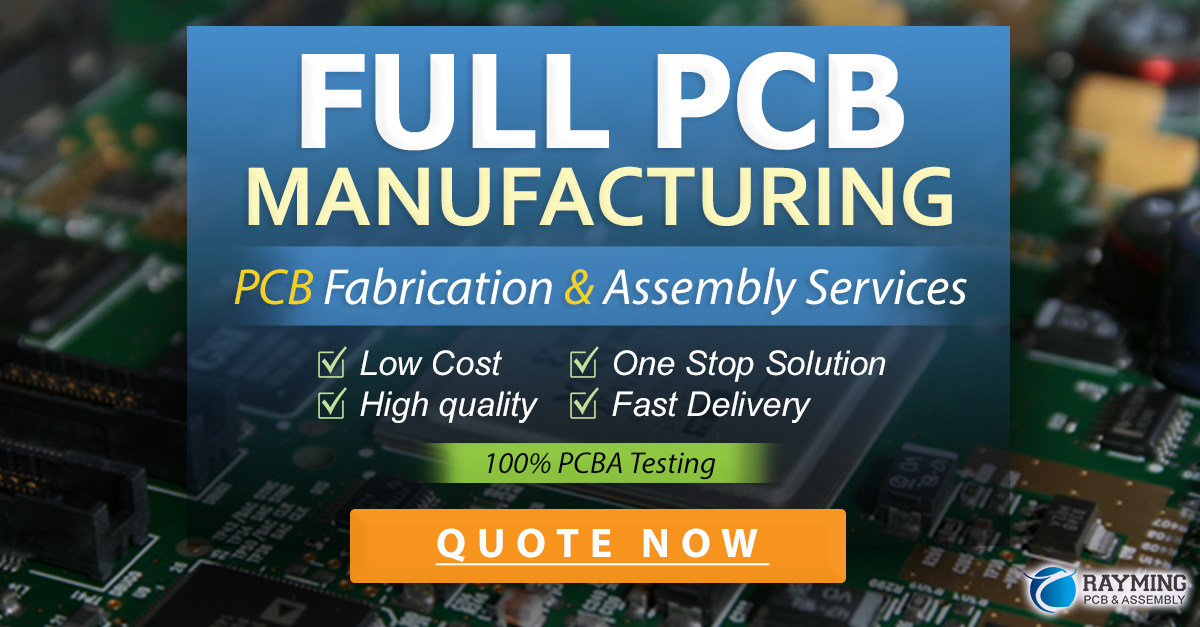
Choosing the Right PCB Surface Finish
Selecting the appropriate PCB surface finish depends on several factors, including:
- Application requirements: Consider the specific needs of your application, such as electrical conductivity, solderability, and environmental conditions.
- Component compatibility: Ensure that the chosen surface finish is compatible with the components used in your design, especially for fine-pitch and BGA components.
- Manufacturing process: Take into account the manufacturing capabilities of your PCB fabricator and the compatibility of the surface finish with the assembly process.
- Cost: Evaluate the cost implications of each surface finish option and choose the one that provides the best balance between performance and budget.
- Shelf life: Consider the expected shelf life of your product and choose a surface finish that can withstand the required storage duration.
PCB Surface Finish Comparison
To help you make an informed decision, here’s a comparison table of the most common PCB surface finishes:
Surface Finish | Solderability | Shelf Life | Fine-Pitch Compatibility | Cost |
---|---|---|---|---|
HASL | Good | Limited | Limited | Low |
ENIG | Excellent | Long | Excellent | High |
OSP | Good | Limited | Good | Low |
Immersion Silver | Excellent | Limited | Excellent | Moderate |
Immersion Tin | Good | Limited | Good | Moderate |
Frequently Asked Questions (FAQ)
-
Q: What is the most cost-effective PCB surface finish?
A: HASL and OSP are generally the most cost-effective PCB surface finishes. However, the choice ultimately depends on your specific application requirements and budget. -
Q: Which surface finish is best for fine-pitch components?
A: ENIG and Immersion Silver are excellent choices for fine-pitch components due to their flat and uniform surface. -
Q: How long does ENIG surface finish last?
A: ENIG has a long shelf life and can last several years under proper storage conditions. -
Q: Can I use HASL for lead-free applications?
A: While HASL traditionally uses a lead-based solder, lead-free HASL options are available for RoHS-Compliant applications. -
Q: Which surface finish is the most environmentally friendly?
A: OSP is considered the most environmentally friendly PCB surface finish as it does not involve the use of heavy metals and has a minimal environmental impact.
Conclusion
PCB surface finishes play a crucial role in ensuring the reliability, solderability, and longevity of electronic devices. From the cost-effective HASL to the high-performance ENIG, each surface finish has its own advantages and disadvantages. By understanding the characteristics and applications of different surface finishes, you can make an informed decision when designing and manufacturing your PCB Prototypes.
At RAYPCB, we offer a wide range of PCB surface finish options to cater to your specific requirements. Our experienced team can guide you in selecting the most suitable surface finish for your project, ensuring optimal performance and reliability. With our state-of-the-art manufacturing facilities and strict quality control processes, you can trust RAYPCB to deliver high-quality PCB prototypes with the perfect surface finish for your application.
Leave a Reply