What is a PCB Surface Finish?
A PCB surface finish is a coating applied to the exposed copper traces and pads on a printed circuit board. Its primary purposes are to:
– Protect the copper from oxidation and corrosion
– Enhance solderability for component assembly
– Provide a smooth, level surface for improved contact with connectors and test points
– Improve the aesthetic appearance of the board
The surface finish is typically applied after the PCB fabrication process, which includes etching away unwanted copper, drilling holes, and applying solder mask. The choice of surface finish depends on various factors such as the intended use environment, component types, soldering methods, storage requirements, and budget.
Common Types of PCB Surface Finishes
There are several widely used PCB surface finishes, each with its own set of advantages and disadvantages. The most common options include:
- Hot Air Solder Leveling (HASL)
- Electroless Nickel Immersion Gold (ENIG)
- Immersion Silver (IAg)
- Immersion Tin (ISn)
- Organic Solderability Preservative (OSP)
Let’s examine each of these in more detail.
Hot Air Solder Leveling (HASL)
HASL is one of the most widely used and economical PCB surface finishes. The process involves dipping the board in a molten solder bath, then using hot air knives to blow off the excess solder, leaving a thin, level coating on the exposed copper.
Advantages:
– Low cost
– Excellent solderability
– Good shelf life (6-12 months)
– Suitable for through-hole and SMT components
Disadvantages:
– Not perfectly flat surface due to solder thinning at edges
– Potential for thermal shock to the PCB
– Not suitable for fine-pitch components
– Contains lead (not RoHS compliant unless using lead-free solder)
Property | HASL |
---|---|
Shelf Life | 6-12 months |
Solderability | Excellent |
Fine-pitch Compatibility | Poor |
Cost | Low |
Electroless Nickel Immersion Gold (ENIG)
ENIG is a two-layer metallic surface finish consisting of a thin gold layer over a nickel undercoat. The nickel provides a barrier against copper migration, while the gold protects the nickel from oxidation and enhances solderability.
Advantages:
– Flat, smooth surface ideal for fine-pitch components
– Excellent solderability and wettability
– Long shelf life (12+ months)
– RoHS compliant
– Good aluminum Wire Bonding compatibility
Disadvantages:
– Higher cost than HASL and OSP
– Potential for “black pad” defect due to improper plating process
– Not suitable for press-fit connectors
Property | ENIG |
---|---|
Shelf Life | 12+ months |
Solderability | Excellent |
Fine-pitch Compatibility | Excellent |
Cost | High |
Immersion Silver (IAg)
Immersion silver is a simple, single-layer surface finish that provides good solderability and stability. The process involves dipping the PCB in a silver salt solution, resulting in a thin layer of silver deposited on the exposed copper.
Advantages:
– Flat, smooth surface
– Good solderability
– Suitable for fine-pitch components
– RoHS compliant
– Lower cost than ENIG
Disadvantages:
– Shorter shelf life than ENIG (6-12 months)
– Prone to tarnishing over time
– Not recommended for high-sulfur environments
– Limited wire bonding compatibility
Property | Immersion Silver |
---|---|
Shelf Life | 6-12 months |
Solderability | Good |
Fine-pitch Compatibility | Good |
Cost | Medium |
Immersion Tin (ISn)
Immersion tin is another single-layer surface finish that offers good solderability and affordability. The PCB is dipped in a tin salt solution, resulting in a thin, uniform layer of tin on the copper surfaces.
Advantages:
– Flat surface suitable for fine-pitch components
– Good solderability
– Lower cost than ENIG and IAg
– RoHS compliant
Disadvantages:
– Shorter shelf life (3-6 months) due to tin whisker growth
– Tin whiskers can cause short circuits
– Not recommended for high-reliability applications
– Limited wire bonding compatibility
Property | Immersion Tin |
---|---|
Shelf Life | 3-6 months |
Solderability | Good |
Fine-pitch Compatibility | Good |
Cost | Low to Medium |
Organic Solderability Preservative (OSP)
OSP is a organic compound coating that protects the copper from oxidation and provides a solderable surface. It is applied by dipping the PCB in the OSP solution, resulting in a thin, transparent layer.
Advantages:
– Low cost
– Flat, smooth surface
– Suitable for fine-pitch components
– RoHS compliant
– Eliminates the need for a solder mask
Disadvantages:
– Short shelf life (3-6 months)
– Limited solderability compared to metallic finishes
– Not suitable for multiple reflow cycles
– Can be difficult to inspect visually
Property | OSP |
---|---|
Shelf Life | 3-6 months |
Solderability | Fair |
Fine-pitch Compatibility | Good |
Cost | Low |
Key Considerations When Choosing a PCB Surface Finish
When selecting a surface finish for your PCB, there are several key factors to consider:
-
Application Requirements: Consider the intended use environment, operating conditions, and reliability expectations for your PCB. High-reliability applications may require more robust finishes like ENIG, while cost-sensitive projects may opt for HASL or OSP.
-
Component Types: The types of components used on your board will influence the surface finish choice. Fine-pitch SMD components require flat, smooth surfaces like ENIG or IAg, while through-hole components are more forgiving and can use HASL.
-
Soldering Methods: Different soldering techniques have varying surface finish requirements. Wave Soldering is compatible with most finishes, while Reflow Soldering benefits from flat surfaces for better component placement accuracy.
-
Shelf Life: If your PCBs will be stored for an extended period before assembly, choose a finish with a longer shelf life like ENIG or IAg. OSP and ISn have shorter shelf lives due to their organic nature and tin whisker growth, respectively.
-
Cost: The surface finish can significantly impact the overall cost of your PCB. HASL and OSP are the most economical options, while ENIG and IAg are more expensive due to the use of precious metals and additional processing steps.
-
Environmental Compliance: If your product must comply with RoHS (Restriction of Hazardous Substances) regulations, avoid leaded HASL and opt for lead-free finishes like ENIG, IAg, ISn, or OSP.
-
Aesthetics: The appearance of the PCB may be important for certain applications. ENIG provides an attractive gold finish, while OSP results in a more subdued, transparent appearance. HASL and IAg have a more industrial look.
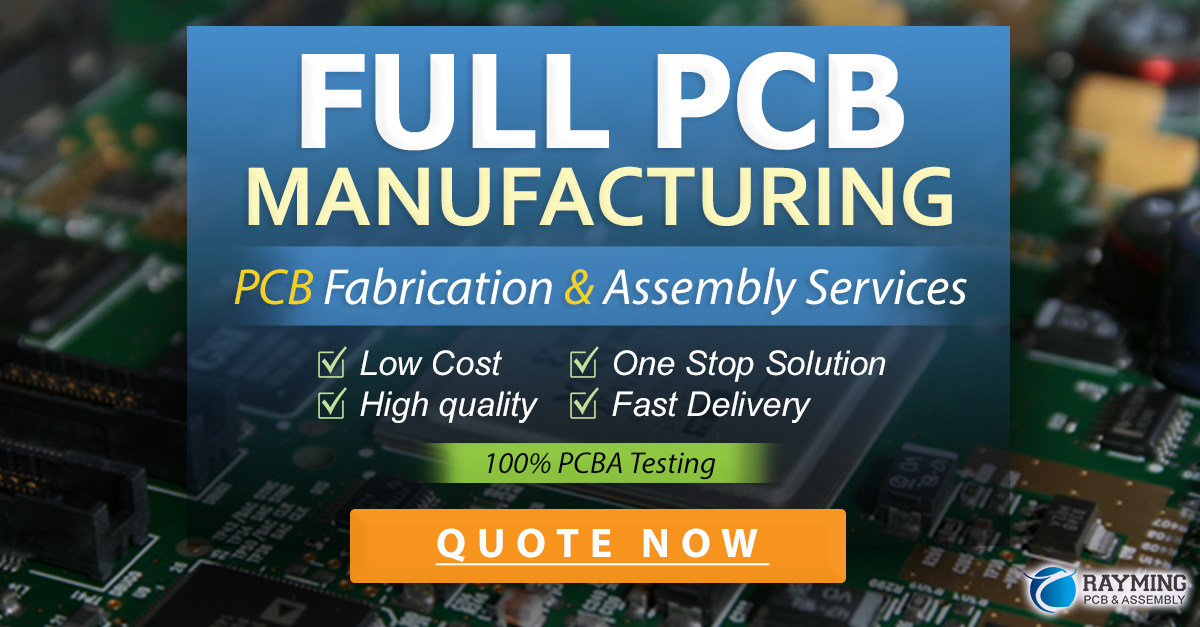
Frequently Asked Questions (FAQ)
-
What is the most cost-effective PCB surface finish?
The most cost-effective PCB surface finishes are typically HASL (Hot Air Solder Leveling) and OSP (Organic Solderability Preservative). These finishes require fewer processing steps and materials compared to options like ENIG (Electroless Nickel Immersion Gold) or Immersion Silver, resulting in lower overall costs. -
Which surface finish is best for high-reliability applications?
For high-reliability applications, ENIG is often the preferred choice. The combination of a nickel undercoat and a thin gold layer provides excellent solderability, flat surfaces for fine-pitch components, and long shelf life. ENIG also offers good resistance to corrosion and wear, making it suitable for demanding environments. -
Can I mix different surface finishes on the same PCB?
While it is technically possible to use different surface finishes on the same PCB, it is generally not recommended. Mixing finishes can lead to uneven soldering, inconsistent appearance, and potential reliability issues. It is best to choose a single surface finish that meets the requirements for all components and areas of the board. -
How does the surface finish affect the soldering process?
The surface finish can impact the soldering process in several ways. Flat, smooth finishes like ENIG, IAg, and ISn provide better contact with component leads and more consistent solder joints. HASL, with its slightly uneven surface, may require more solder or a longer dwell time to achieve reliable connections. OSP, being an organic coating, may require a more active flux to remove the coating and promote solder wetting. -
What is the typical shelf life for PCBs with different surface finishes?
Surface Finish | Typical Shelf Life |
---|---|
HASL | 6-12 months |
ENIG | 12+ months |
Immersion Silver | 6-12 months |
Immersion Tin | 3-6 months |
OSP | 3-6 months |
It’s important to note that shelf life can vary depending on storage conditions, with factors like humidity, temperature, and air quality playing a role in the longevity of the surface finish.
Conclusion
Selecting the right PCB surface finish is a critical decision that balances technical requirements, cost, and manufacturability. By understanding the properties, advantages, and disadvantages of the most common finishes – HASL, ENIG, IAg, ISn, and OSP – you can make an informed choice that best suits your specific application.
Consider factors such as the intended use environment, component types, soldering methods, shelf life, cost, environmental compliance, and aesthetics when evaluating surface finish options. Remember that while some finishes may excel in certain areas, they may have drawbacks in others, so prioritize your requirements accordingly.
If you’re unsure about the best surface finish for your PCB, consult with your PCB manufacturer or an experienced design professional. They can provide valuable insights and recommendations based on your specific needs and help you navigate the selection process.
Ultimately, choosing the right PCB surface finish is key to ensuring the reliability, performance, and longevity of your electronic device. By making an informed decision and working closely with your manufacturing partners, you can create a high-quality PCB that meets your technical and economic goals.
Leave a Reply