Introduction to Flexible PCBs
Flexible PCBs, also known as flex circuits or flexible printed circuit boards, have gained significant popularity in recent years due to their unique characteristics and versatile applications. Unlike traditional rigid PCBs, flexible PCBs are designed to bend, fold, and conform to various shapes and spaces, making them ideal for a wide range of industries, including consumer electronics, medical devices, aerospace, and automotive.
In this article, we will explore the key characteristics that make flexible PCBs so popular and discuss their advantages, applications, and manufacturing process.
What is a Flexible PCB?
A flexible PCB is a type of printed circuit board that consists of a thin, flexible substrate made of materials such as polyimide or polyester. The substrate is laminated with copper traces and other components, allowing for electrical connectivity and functionality. The flexibility of the substrate enables the PCB to bend, fold, and twist without damaging the circuits or components.
Advantages of Flexible PCBs
Flexible PCBs offer several advantages over traditional rigid PCBs, including:
- Space savings: Flexible PCBs can be bent and folded to fit into tight spaces, reducing the overall size and weight of electronic devices.
- Increased reliability: The flexibility of the substrate reduces stress on components and connections, improving the overall reliability of the device.
- Enhanced durability: Flexible PCBs can withstand repeated bending and flexing without breaking or losing functionality.
- Improved signal integrity: The thin, flexible substrate minimizes signal loss and interference, resulting in better signal integrity compared to rigid PCBs.
- Cost-effective: Flexible PCBs can reduce the number of connectors and cables required, lowering the overall cost of the device.
Key Characteristics of Flexible PCBs
Flexibility
The most obvious characteristic of flexible PCBs is their ability to bend and flex without damaging the circuits or components. This flexibility is achieved through the use of thin, flexible substrates and specialized manufacturing processes.
The degree of flexibility can vary depending on the specific application and design requirements. Some flexible PCBs are designed for a single bend or fold, while others can withstand multiple bends and twists.
Types of Flexible PCBs Based on Flexibility
Type | Description |
---|---|
Single-sided Flex | A flexible PCB with conductive traces on one side of the substrate. |
Double-sided Flex | A flexible PCB with conductive traces on both sides of the substrate. |
Multi-layer Flex | A flexible PCB with multiple layers of conductive traces separated by insulating layers. |
Rigid-Flex | A combination of rigid and flexible PCBs, with rigid sections for component mounting and flexible sections for interconnections. |
Thinness
Flexible PCBs are typically much thinner than rigid PCBs, with substrate thicknesses ranging from 0.05 mm to 0.2 mm. This thinness contributes to the overall flexibility of the PCB and allows for more compact and lightweight designs.
The thin profile of flexible PCBs also enables them to be used in applications where space is limited, such as wearable devices, medical implants, and compact consumer electronics.
High-Density Interconnects (HDI)
Flexible PCBs are capable of accommodating high-density interconnects, which means they can support a large number of components and traces in a small area. This is achieved through the use of fine-pitch traces, micro vias, and embedded components.
HDI technology enables the design of more complex and sophisticated electronic devices while maintaining a compact form factor. This is particularly important in applications such as smartphones, tablets, and medical devices, where space is at a premium.
Thermal Management
Flexible PCBs have unique thermal management requirements due to their thin profile and the close proximity of components. To ensure proper heat dissipation and prevent overheating, flexible PCBs often incorporate thermal management techniques such as:
- Thermal vias: Vias filled with thermally conductive material to transfer heat away from components.
- Thermal interface materials (TIMs): Materials such as thermal pads or adhesives that improve heat transfer between components and the PCB.
- Heat spreaders: Thin, thermally conductive layers that help distribute heat evenly across the PCB.
Effective thermal management is crucial for maintaining the reliability and performance of flexible PCBs, especially in high-power applications or environments with limited airflow.
Material Selection
The choice of materials for flexible PCBs is critical to their performance and durability. The most common substrate materials used in flexible PCBs are:
- Polyimide (PI): A high-temperature, chemically resistant polymer with excellent mechanical and electrical properties.
- Polyester (PET): A lower-cost alternative to polyimide, suitable for less demanding applications.
- Flexible copper-clad laminate (FCCL): A laminate consisting of a flexible substrate bonded to a thin layer of copper foil.
The selection of substrate material depends on factors such as the application requirements, operating temperature range, chemical exposure, and cost constraints.
In addition to the substrate, the choice of conductive materials, such as copper or silver, and the use of coverlay or solder mask for protection and insulation, also play a significant role in the performance and reliability of flexible PCBs.
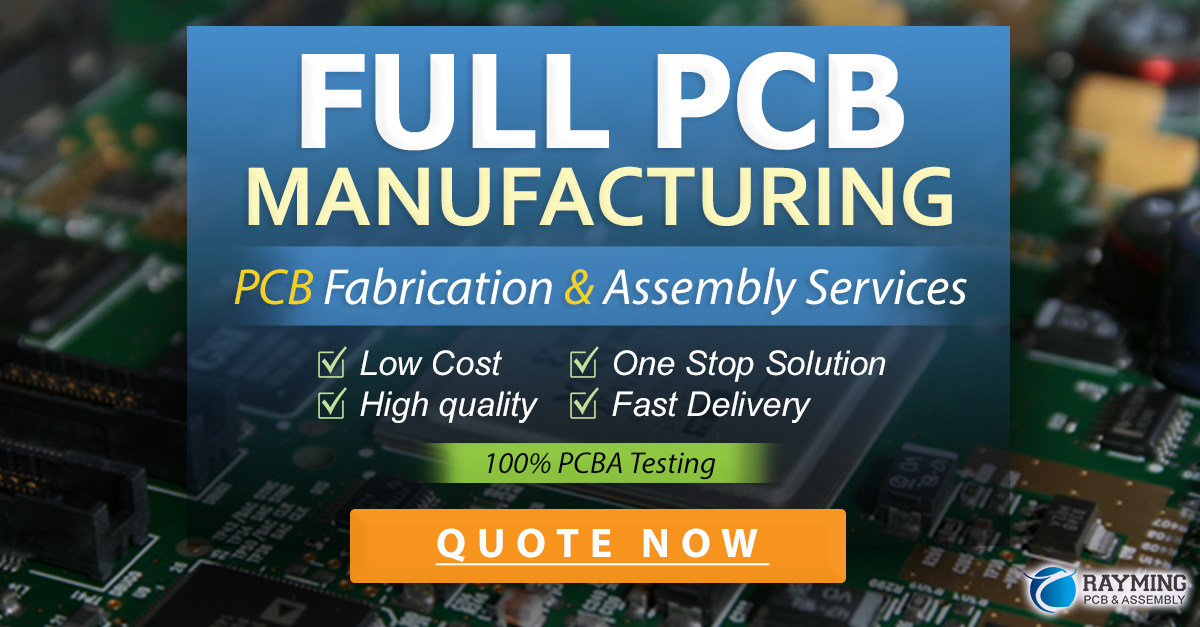
Applications of Flexible PCBs
Flexible PCBs find applications in a wide range of industries, thanks to their unique characteristics and advantages. Some of the most common applications include:
Consumer Electronics
Flexible PCBs are extensively used in consumer electronics, such as smartphones, tablets, laptops, and wearable devices. They enable compact, lightweight designs and allow for the integration of multiple functions within a single device.
Medical Devices
Flexible PCBs are well-suited for medical devices, particularly implantable and wearable devices. Their flexibility and biocompatibility make them ideal for applications such as pacemakers, hearing aids, and patient monitoring systems.
Automotive Electronics
The automotive industry has adopted flexible PCBs for various applications, including dashboard displays, engine control units, and sensors. Flexible PCBs offer reliability and durability in the harsh operating conditions encountered in automotive environments.
Aerospace and Defense
Flexible PCBs are used in aerospace and defense applications, such as avionics, satellites, and military equipment. Their ability to withstand extreme temperatures, vibrations, and shocks makes them suitable for these demanding applications.
Industrial Equipment
Flexible PCBs are employed in industrial equipment, such as robotics, automation systems, and test and measurement devices. They provide reliable interconnections and enable compact, modular designs.
Manufacturing Process of Flexible PCBs
The manufacturing process of flexible PCBs involves several steps, each of which requires specialized equipment and expertise. The main steps in the manufacturing process are:
- Substrate preparation: The flexible substrate is cleaned, and a thin layer of copper foil is laminated onto the substrate.
- Circuit design and patterning: The circuit design is created using CAD software, and the copper foil is patterned using photolithography and etching processes.
- Lamination: Additional layers of substrate and copper foil are laminated together to create a multi-layer flexible PCB.
- Drilling and plating: Holes are drilled through the PCB, and the holes are plated with copper to create electrical connections between layers.
- Component assembly: Electronic components are mounted onto the flexible PCB using surface mount technology (SMT) or through-hole technology (THT).
- Testing and inspection: The assembled flexible PCB undergoes various tests and inspections to ensure proper functionality and quality.
The manufacturing process of flexible PCBs requires strict process control and adherence to industry standards to ensure consistent quality and reliability.
Frequently Asked Questions (FAQ)
1. What is the difference between a flexible PCB and a rigid PCB?
A flexible PCB is made from a thin, flexible substrate that allows the PCB to bend and fold without damaging the circuits or components. In contrast, a rigid PCB is made from a solid, non-flexible substrate, such as FR-4, and cannot be bent or folded.
2. Can flexible PCBs be used in high-temperature applications?
Yes, flexible PCBs can be designed to withstand high temperatures by using appropriate substrate materials, such as polyimide, and by incorporating thermal management techniques. However, the specific temperature range depends on the materials and components used in the design.
3. Are flexible PCBs more expensive than rigid PCBs?
In general, flexible PCBs tend to be more expensive than rigid PCBs due to the specialized materials, manufacturing processes, and design considerations involved. However, the cost difference can be offset by the benefits of using flexible PCBs, such as reduced weight, improved reliability, and space savings.
4. Can flexible PCBs be repaired?
Repairing flexible PCBs can be more challenging than repairing rigid PCBs due to their thin, delicate nature. However, skilled technicians can perform repairs using specialized techniques, such as micro-soldering or conductive adhesives. In some cases, it may be more cost-effective to replace the entire flexible PCB Assembly rather than attempting a repair.
5. How long do flexible PCBs last?
The lifespan of a flexible PCB depends on various factors, such as the materials used, the operating conditions, and the level of stress and strain experienced by the PCB. With proper design, manufacturing, and handling, flexible PCBs can last for many years, even in demanding applications. Accelerated life testing and reliability studies can help predict the expected lifespan of a flexible PCB in a specific application.
Conclusion
Flexible PCBs have become increasingly popular due to their unique characteristics, such as flexibility, thinness, high-density interconnects, and thermal management capabilities. These characteristics enable the design of compact, lightweight, and reliable electronic devices across a wide range of industries, from consumer electronics to medical devices and aerospace applications.
As technology continues to advance and the demand for smaller, more complex electronic devices grows, flexible PCBs will likely play an even greater role in shaping the future of electronics. By understanding the key characteristics and advantages of flexible PCBs, designers and manufacturers can create innovative, high-performance products that meet the evolving needs of their customers.
Leave a Reply