1. Choosing the Right PCB Manufacturer
Selecting a reliable and experienced PCB manufacturer is the first step in ensuring a successful prototyping process. Consider the following factors when choosing a PCB manufacturer:
- Experience and expertise in PCB Prototyping
- Quality control processes and certifications (e.g., ISO 9001, UL, IPC)
- Turnaround time and pricing
- Customer support and communication
Top 5 PCB Manufacturers for Prototyping
Manufacturer | Location | Specialties | Certifications |
---|---|---|---|
PCBWay | China | Quick-turn, low-cost | ISO 9001, UL, IPC |
OSH Park | USA | Small-batch, open-source | ISO 9001, IPC |
Seeed Studio | China | Fusion PCB, assembly | ISO 9001, UL, IPC |
Eurocircuits | Europe | Medium-volume, high-quality | ISO 9001, UL, IPC |
Sierra Circuits | USA | High-complexity, quick-turn | ISO 9001, AS9100, IPC |
2. Design for Manufacturability (DFM)
To ensure a smooth transition from prototyping to production, it is essential to follow Design for Manufacturability (DFM) guidelines. DFM involves designing your PCB in a way that optimizes its manufacturability, reducing the risk of defects and delays. Some key DFM considerations include:
- Maintaining proper trace width and spacing
- Avoiding acute angles and sharp corners
- Using standard component sizes and footprints
- Providing adequate clearance for vias and mounting holes
3. Material Selection
The choice of PCB material can significantly impact the performance, reliability, and cost of your prototype. Common PCB materials include:
- FR-4: A standard, cost-effective material suitable for most applications
- High-Tg FR-4: Offers better thermal stability and mechanical properties than standard FR-4
- Polyimide: Ideal for high-temperature and flexible applications
- Aluminum: Used for heat dissipation in power electronics
Consider the specific requirements of your application, such as temperature range, dielectric constant, and mechanical stress, when selecting the appropriate PCB material.
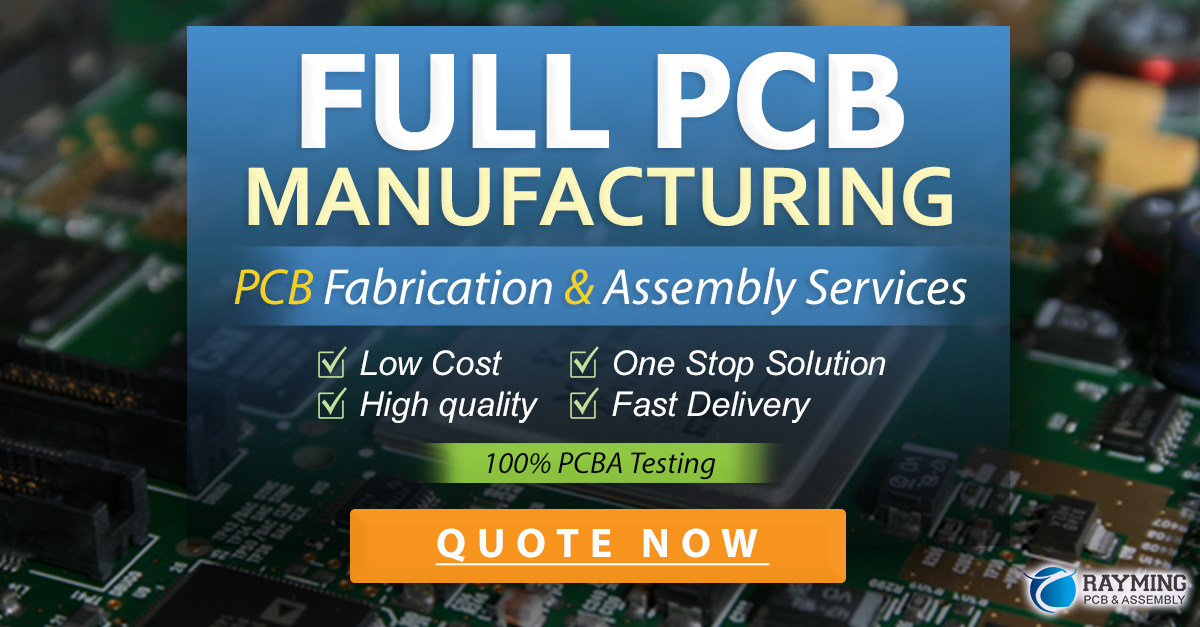
4. Layer Stack-up
The layer stack-up of your PCB refers to the arrangement of conductive and insulating layers. A well-designed layer stack-up can improve signal integrity, reduce electromagnetic interference (EMI), and optimize manufacturing costs. Some best practices for layer stack-up design include:
- Using a symmetrical stack-up to minimize warping
- Placing signal layers close to the power and ground planes to reduce noise
- Avoiding unnecessary layers to reduce cost and complexity
- Considering the impedance requirements of high-speed signals
5. Component Placement and Routing
Proper component placement and routing are critical for ensuring the functionality and reliability of your PCB Prototype. Follow these guidelines to optimize your component placement and routing:
- Group related components together to minimize trace lengths
- Place decoupling capacitors close to power pins
- Route high-speed signals on inner layers to reduce EMI
- Use ground planes to provide a low-impedance return path
- Avoid routing traces under components to facilitate assembly and rework
6. Solder Mask and Silkscreen
Solder mask and silkscreen are important features that protect your PCB and provide useful information for assembly and debugging. When designing your solder mask and silkscreen, consider the following:
- Choose a contrasting color for the solder mask to improve visibility
- Provide adequate clearance around pads and vias to prevent solder bridging
- Include component identifiers, polarity markers, and test points on the silkscreen
- Ensure that silkscreen text is legible and properly aligned
7. Testing and Validation
Before finalizing your PCB prototype, it is essential to perform thorough testing and validation to ensure that it meets your design requirements. Some common testing methods include:
- Visual inspection: Check for manufacturing defects, component placement, and soldering quality
- Continuity testing: Verify that all connections are properly made and there are no short circuits
- Functional testing: Test the PCB’s performance under various operating conditions
- Boundary scan testing: Use JTAG or other boundary scan techniques to test complex digital circuits
Based on the testing results, make necessary revisions to your design and repeat the prototyping process until you achieve satisfactory results.
8. Documentation and Version Control
Maintaining accurate documentation and version control throughout the PCB prototyping process is crucial for tracking changes, collaborating with team members, and ensuring reproducibility. Some best practices for documentation and version control include:
- Use a version control system (e.g., Git) to manage your design files
- Maintain a clear and consistent file naming convention
- Include detailed component and assembly instructions
- Document any design changes and their rationale
- Store all project-related documents in a centralized location accessible to all team members
By following these documentation and version control practices, you can streamline your prototyping process and minimize the risk of errors and miscommunication.
FAQ
-
Q: How long does PCB prototyping usually take?
A: The turnaround time for PCB prototyping varies depending on the complexity of the design and the manufacturer’s capabilities. Typically, it can range from a few days to a couple of weeks. -
Q: What is the minimum order quantity (MOQ) for PCB Prototypes?
A: Many PCB manufacturers offer low MOQs for prototyping, sometimes as low as one or two pieces. However, the cost per unit may be higher for small quantities. -
Q: Can I assemble the PCB prototype myself, or should I use a professional assembly service?
A: If you have the necessary skills and equipment, you can assemble the PCB prototype yourself. However, for complex designs or high-quality requirements, it is recommended to use a professional assembly service. -
Q: What should I do if my PCB prototype fails to meet the design requirements?
A: If your PCB prototype fails to meet the design requirements, analyze the test results to identify the root cause of the issue. Make necessary revisions to your design and repeat the prototyping process until you achieve satisfactory results. -
Q: How can I reduce the cost of PCB prototyping?
A: To reduce the cost of PCB prototyping, consider the following options: - Optimize your design to minimize the number of layers and components
- Choose a cost-effective PCB material and manufacturing process
- Order in larger quantities to take advantage of volume discounts
- Compare prices from multiple PCB manufacturers and choose the most competitive offer
By paying attention to these eight essential matters, you can ensure a successful and efficient PCB prototyping process, setting the foundation for a smooth transition to full-scale production.
Leave a Reply