Introduction
Creating a prototype printed circuit board (PCB) is an essential step in the electronics design process. A PCB Prototype allows you to test and validate your design before committing to a full production run. As a professional PCB maker, I’m here to share 10 expert tips on how to make a PCB prototype that precisely meets your needs. Whether you’re an electronics hobbyist or a seasoned engineer, these strategies will help you create high-quality, functional prototypes efficiently and cost-effectively.
1. Clearly Define Your Requirements
Establish Design Goals and Constraints
Before you start designing your PCB prototype, it’s crucial to clearly define your requirements. Take the time to establish your design goals and constraints, including:
– Functional requirements
– Physical dimensions
– Power requirements
– Environmental factors (temperature, humidity, vibration, etc.)
– Cost constraints
– Timeframe
Documenting these requirements will guide your design decisions and help you create a prototype that aligns with your objectives.
Create a Detailed Specification Document
To ensure that your PCB prototype meets your exact needs, create a detailed specification document. This document should include:
– Schematic diagrams
– Bill of Materials (BOM)
– PCB layout requirements
– Component placement guidelines
– Testing and validation procedures
A well-defined specification document serves as a roadmap for your prototype development process and helps you communicate your requirements to your team or external partners.
2. Choose the Right PCB Design Software
Evaluate Your Design Needs
Selecting the right PCB design software is essential for creating a high-quality prototype. When evaluating your options, consider your specific design needs:
– Complexity of your PCB design
– Number of layers required
– Types of components used (SMD, through-hole, etc.)
– Integration with other tools (e.g., mechanical CAD software)
– Collaboration features for team-based design
Choosing a PCB design software that aligns with your needs will streamline your design process and help you create a more accurate and efficient prototype.
Popular PCB Design Software Options
Some popular PCB design software options include:
Software | Key Features |
---|---|
Altium Designer | Comprehensive feature set, 3D modeling, advanced routing tools |
Eagle | User-friendly interface, extensive component libraries, affordable |
KiCad | Free and open-source, schematic capture and PCB layout, active community |
OrCAD | Powerful simulation tools, hierarchical design, flexible licensing options |
Consider your budget, design requirements, and user preferences when selecting the best software for your PCB prototype development.
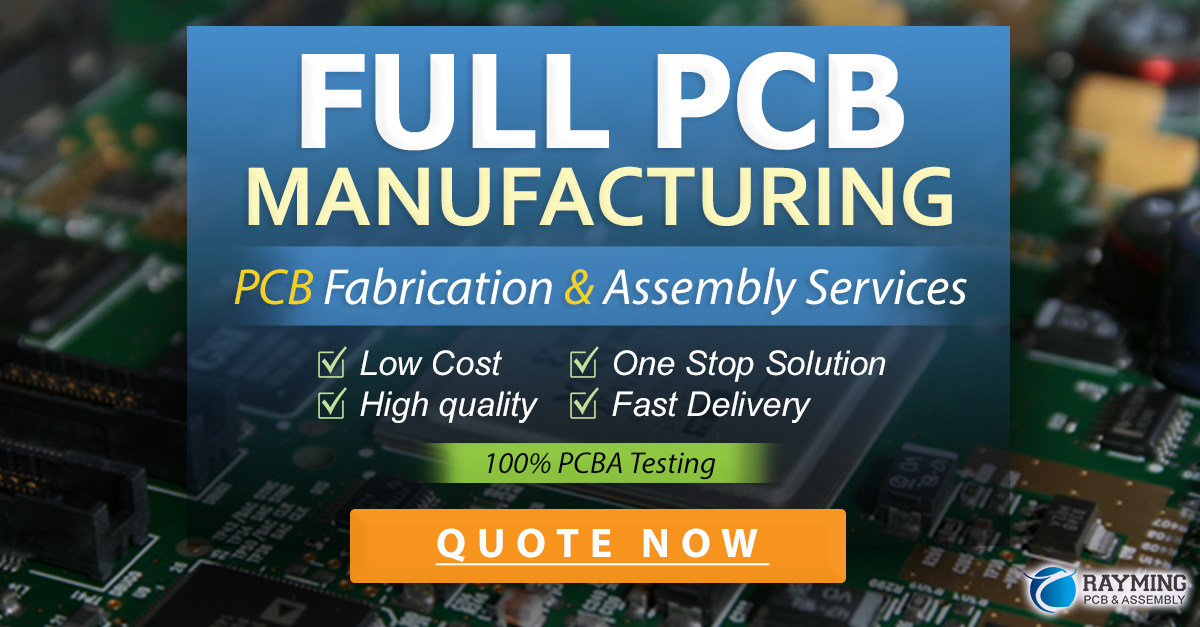
3. Create a Robust Schematic Design
Follow Best Practices for Schematic Creation
A well-designed schematic is the foundation of a successful PCB prototype. Follow these best practices when creating your schematic:
– Use a consistent and clear naming convention for components and nets
– Organize your schematic into logical hierarchical blocks
– Use appropriate symbols for components
– Include detailed notes and annotations
– Perform a thorough design review to catch errors early
By adhering to these best practices, you’ll create a schematic that is easier to understand, debug, and translate into a physical PCB layout.
Simulate and Verify Your Schematic
Before moving on to the PCB layout phase, it’s essential to simulate and verify your schematic design. Use simulation tools integrated with your PCB design software to:
– Perform DC and AC analysis
– Verify the functionality of your circuit
– Identify potential issues or areas for optimization
– Ensure that your design meets your performance requirements
By simulating and verifying your schematic, you can catch design errors early and save time and resources in the long run.
4. Optimize Your PCB Layout
Consider Component Placement and Routing
An optimized PCB layout is critical for creating a functional and reliable prototype. When designing your PCB layout, consider:
– Component placement for optimal signal integrity and thermal management
– Routing techniques to minimize crosstalk and electromagnetic interference (EMI)
– Proper grounding and power distribution
– Manufacturability and assembly requirements
By carefully planning your component placement and routing, you’ll create a PCB layout that is more likely to function as intended and be easier to manufacture.
Utilize Design Rule Checks (DRC)
Design Rule Checks (DRC) are automated tools that help you identify and resolve layout issues before finalizing your PCB design. Common DRC checks include:
– Minimum trace width and spacing
– Hole size and pad dimensions
– Copper pour and clearance rules
– Silk screen and solder mask requirements
By running DRC checks throughout the layout process, you can catch potential manufacturing issues early and ensure that your PCB prototype meets industry standards and best practices.
5. Select the Right Components
Consider Availability and Lead Times
When selecting components for your PCB prototype, it’s essential to consider their availability and lead times. To avoid delays in your prototype development process:
– Choose components that are readily available from multiple suppliers
– Check lead times and plan accordingly
– Consider alternative components with similar specifications if your first choice is unavailable
– Order components early to account for potential delays
By proactively managing your component selection and procurement, you can minimize the risk of delays and ensure a smooth prototype development process.
Evaluate Component Quality and Reliability
In addition to availability, it’s crucial to evaluate the quality and reliability of the components you select for your PCB prototype. To ensure optimal performance and longevity:
– Choose components from reputable manufacturers with proven track records
– Review component datasheets and application notes
– Consider the environmental factors your prototype will be exposed to
– Perform thorough testing and validation of your selected components
By selecting high-quality, reliable components, you’ll create a PCB prototype that is more likely to meet your performance requirements and stand the test of time.
6. Utilize Rapid Prototyping Techniques
3D Printing for Enclosures and Mechanical Parts
Rapid prototyping techniques, such as 3D printing, can help you quickly create custom enclosures and mechanical parts for your PCB prototype. Benefits of using 3D printing include:
– Quick turnaround times
– Ability to create complex geometries
– Low-cost prototyping for small quantities
– Easy design iterations and modifications
By incorporating 3D-printed components into your PCB prototype, you can create a more comprehensive and functional prototype that closely resembles your final product.
Breadboarding for Initial Circuit Validation
Breadboarding is a rapid prototyping technique that allows you to quickly validate your circuit design before committing to a full PCB prototype. Advantages of breadboarding include:
– Quick and easy setup
– Ability to make fast modifications and iterations
– Low cost for initial proof-of-concept testing
– Opportunity to test different components and configurations
By using breadboarding to validate your circuit design, you can identify and address potential issues early in the prototype development process, saving time and resources in the long run.
7. Consider Manufacturing Processes
Understand PCB Fabrication Techniques
When designing your PCB prototype, it’s essential to understand the various PCB fabrication techniques and their implications for your design. Common fabrication techniques include:
– Through-hole technology (THT)
– Surface mount technology (SMT)
– Mixed assembly (combining THT and SMT)
– Flexible and rigid-flex PCBs
Each fabrication technique has its own set of design guidelines, limitations, and cost considerations. By understanding these factors, you can design a PCB prototype that is optimized for your chosen manufacturing process.
Design for Manufacturing (DFM) Guidelines
To ensure the manufacturability of your PCB prototype, follow Design for Manufacturing (DFM) guidelines. DFM guidelines help you create designs that are easier to fabricate, assemble, and test, leading to higher yields and lower costs. Key DFM considerations include:
– Minimum trace width and spacing
– Pad sizes and shapes
– Drill hole sizes and spacing
– Solder mask and silkscreen requirements
– Component placement and orientation
By adhering to DFM guidelines, you’ll create a PCB prototype that is more likely to be successfully manufactured and assembled, reducing the risk of delays and additional costs.
8. Plan for Assembly and Testing
Develop an Assembly Plan
Before sending your PCB prototype to manufacturing, develop a comprehensive assembly plan. This plan should include:
– BOM with component sourcing information
– Assembly instructions and diagrams
– Solder paste and stencil specifications
– Pick-and-place machine programming
– Hand assembly requirements
A well-defined assembly plan will help ensure that your PCB prototype is assembled correctly and efficiently, minimizing the risk of errors and delays.
Create a Testing and Validation Strategy
To ensure that your PCB prototype meets your performance requirements, create a thorough testing and validation strategy. This strategy should include:
– Functional testing to verify that your prototype performs as intended
– Environmental testing (temperature, humidity, vibration, etc.) to assess durability
– Electromagnetic compatibility (EMC) testing to ensure compliance with regulations
– Stress testing to identify potential failure points
– Automated and manual testing procedures
By developing a comprehensive testing and validation strategy, you’ll be able to identify and address any issues with your PCB prototype before moving on to full-scale production.
9. Collaborate with Experienced Partners
Work with Reputable PCB Manufacturers
Collaborating with experienced and reputable PCB manufacturers can help ensure the success of your prototype development process. When selecting a PCB manufacturer, consider:
– Their experience with your specific PCB technology and application
– Quality control processes and certifications (e.g., ISO 9001, UL, IPC)
– Prototype and production capabilities
– Lead times and pricing
– Customer support and communication
By working with a trusted PCB manufacturer, you’ll benefit from their expertise, resources, and support throughout the prototype development process.
Engage with PCB Assembly Providers
In addition to PCB manufacturers, consider engaging with experienced PCB assembly providers for your prototype development. PCB assembly providers offer:
– Expertise in component sourcing and procurement
– Advanced assembly capabilities (SMT, THT, mixed assembly)
– In-circuit and functional testing services
– Design for Assembly (DFA) guidance and support
– Rapid prototyping and low-volume production options
By collaborating with a skilled PCB assembly provider, you can streamline your prototype development process and ensure that your PCB is assembled and tested to the highest standards.
10. Continuously Iterate and Improve
Analyze Prototype Performance and Gather Feedback
Once your PCB prototype is assembled and tested, it’s crucial to analyze its performance and gather feedback from stakeholders. Use this information to:
– Identify areas for improvement in your design
– Optimize component selection and placement
– Refine your manufacturing and assembly processes
– Gather input from end-users and customers
By continuously analyzing your prototype’s performance and gathering feedback, you can make data-driven decisions to improve your design and better meet your target market’s needs.
Implement Design Improvements for Future Iterations
Based on the insights gained from analyzing your prototype’s performance and gathering feedback, implement design improvements for future iterations. This may involve:
– Updating your schematic and PCB layout
– Selecting alternative components
– Modifying your manufacturing and assembly processes
– Incorporating new features or functionality
By continuously iterating and improving your PCB prototype, you’ll create a more refined, reliable, and competitive product that meets your exact needs.
Frequently Asked Questions (FAQ)
-
How long does it typically take to develop a PCB prototype?
The time required to develop a PCB prototype depends on various factors, such as the complexity of your design, the availability of components, and the capabilities of your chosen PCB manufacturer and assembly provider. On average, a simple PCB prototype can be developed in 1-2 weeks, while more complex designs may take several weeks or even months. -
What are the costs associated with creating a PCB prototype?
The costs of creating a PCB prototype can vary widely depending on factors such as the size and complexity of your design, the number of layers, the components used, and the quantity of prototypes required. Simple, low-quantity prototypes may cost a few hundred dollars, while more complex designs or higher quantities can cost several thousand dollars. It’s essential to obtain quotes from multiple PCB manufacturers and assembly providers to find the best balance between cost and quality for your specific needs. -
What are some common mistakes to avoid when developing a PCB prototype?
Some common mistakes to avoid when developing a PCB prototype include: - Not clearly defining your requirements and specifications
- Overlooking the importance of component selection and availability
- Failing to follow best practices for schematic and PCB layout design
- Not considering manufacturing and assembly processes during the design phase
- Inadequate testing and validation of your prototype
- Not gathering and incorporating feedback from stakeholders and end-users
By being aware of these common pitfalls and taking proactive steps to avoid them, you can streamline your PCB prototype development process and create a more successful end product.
- How can I ensure that my PCB prototype meets industry standards and regulations?
To ensure that your PCB prototype meets industry standards and regulations, consider the following: - Familiarize yourself with relevant standards, such as IPC, UL, and ISO
- Work with PCB manufacturers and assembly providers that are certified and compliant with these standards
- Follow best practices for PCB design, including Design for Manufacturing (DFM) and Design for Assembly (DFA) guidelines
- Conduct thorough testing and validation, including environmental and electromagnetic compatibility (EMC) testing
- Stay up-to-date with changes in industry standards and regulations and adapt your designs accordingly
By prioritizing compliance with industry standards and regulations, you’ll create a PCB prototype that is more reliable, safe, and competitive in the marketplace.
- What should I consider when scaling up from a PCB prototype to full-scale production?
When scaling up from a PCB prototype to full-scale production, consider the following factors: - Ensure that your design is optimized for manufacturability and assembly at higher volumes
- Re-evaluate your component selections for availability and cost at larger quantities
- Consider the capabilities and capacity of your chosen PCB manufacturer and assembly provider
- Plan for adequate testing and quality control processes to maintain product consistency and reliability
- Assess the financial and logistical implications of scaling up, including capital investment, inventory management, and supply chain coordination
By carefully planning and executing your transition from prototype to full-scale production, you’ll be better positioned to bring a successful, high-quality product to market.
Conclusion
Creating a PCB prototype that meets your exact needs requires careful planning, attention to detail, and collaboration with experienced partners. By following the 10 expert tips outlined in this article, you’ll be well-equipped to navigate the PCB prototype development process and create a functional, reliable, and competitive product. Remember to clearly define your requirements, choose the right tools and components, optimize your design for manufacturing and assembly, and continuously iterate and improve based on performance data and stakeholder feedback. With these strategies in mind, you’ll be on your way to creating a successful PCB prototype that lays the foundation for a thriving electronics product.
Leave a Reply