Introduction to Rigid-Flex PCBs
Rigid-flex PCBs are a type of printed circuit board that combines both rigid and flexible substrates into a single board. This unique combination allows for the benefits of both rigid and Flexible PCBs to be realized in a single design. Rigid-flex PCBs offer several advantages over traditional flexible PCBs, making them an attractive option for many electronic projects.
What is a Rigid-Flex PCB?
A rigid-flex PCB is a hybrid board that consists of rigid PCB sections connected by flexible PCB sections. The rigid sections provide structural support and allow for the mounting of components, while the flexible sections allow for the board to be bent or folded into various shapes to fit into tight spaces or conform to unique packaging requirements.
Advantages of Rigid-Flex PCBs
Rigid-flex PCBs offer several key advantages over traditional flexible PCBs:
-
Increased Reliability: By combining rigid and flexible sections into a single board, rigid-flex PCBs eliminate the need for connectors between separate rigid and flexible boards. This reduces the number of potential failure points and improves overall reliability.
-
Space Savings: Rigid-flex PCBs allow for more compact packaging by enabling the board to be folded or bent to fit into tight spaces. This can result in significant space savings compared to using separate rigid and flexible boards.
-
Improved Signal Integrity: The elimination of connectors between rigid and flexible sections reduces signal loss and improves signal integrity. This is particularly important for high-speed applications.
-
Reduced Assembly Costs: By combining rigid and flexible sections into a single board, assembly costs can be reduced since there are fewer parts to assemble and less wiring required.
Rigid-Flex PCB Design Considerations
When designing a rigid-flex PCB, there are several key considerations to keep in mind:
Bend Radius
The bend radius is the minimum radius that the flexible section of the board can be bent without causing damage. It is important to design the flexible section with a sufficient bend radius to ensure reliability and prevent damage during assembly or use.
Layer Stack-Up
The layer stack-up of a rigid-flex PCB is critical to its performance and reliability. It is important to carefully consider the number and arrangement of layers in both the rigid and flexible sections to ensure proper signal integrity and mechanical stability.
Material Selection
The materials used in a rigid-flex PCB must be carefully selected to ensure compatibility and reliability. The flexible section typically uses a polyimide substrate, while the rigid section uses a standard FR-4 substrate. The adhesives used to bond the layers together must also be carefully selected to ensure proper adhesion and flexibility.
Coverlay
The coverlay is a protective layer that is applied over the flexible section of the board to provide insulation and protection against damage. The coverlay material and thickness must be carefully selected to ensure flexibility and reliability.
Applications of Rigid-Flex PCBs
Rigid-flex PCBs are used in a wide range of applications where space is limited, and reliability is critical. Some common applications include:
Aerospace and Defense
Rigid-flex PCBs are widely used in aerospace and defense applications where space is at a premium, and reliability is essential. They are commonly used in avionics systems, satellite communications, and military equipment.
Medical Devices
Rigid-flex PCBs are also commonly used in medical devices where space is limited, and reliability is critical. They are used in a range of applications, including implantable devices, diagnostic equipment, and surgical instruments.
Consumer Electronics
Rigid-flex PCBs are increasingly being used in consumer electronics applications where space is limited, and packaging is a key consideration. They are commonly used in smartphones, tablets, and wearable devices.
Automotive Electronics
Rigid-flex PCBs are also being used in automotive electronics applications where space is limited, and reliability is critical. They are commonly used in infotainment systems, driver assistance systems, and vehicle networking applications.
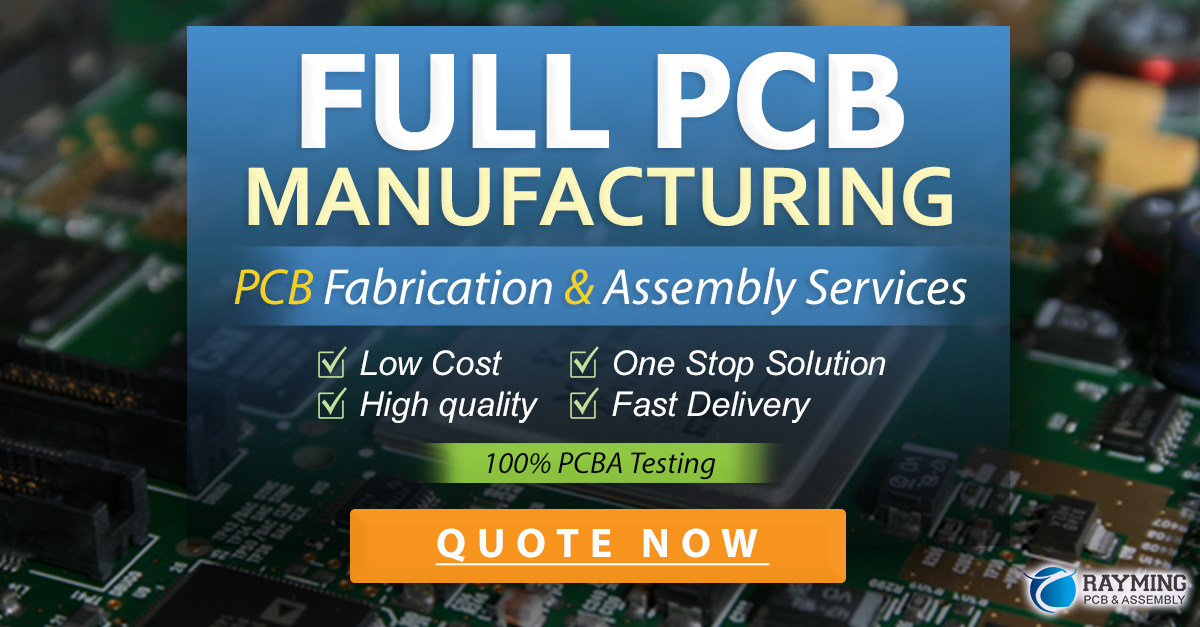
Rigid-Flex PCB Manufacturing Process
The manufacturing process for rigid-flex PCBs is more complex than for standard rigid or flexible PCBs due to the need to combine both rigid and flexible substrates into a single board. The key steps in the manufacturing process include:
Layer Preparation
The first step in the manufacturing process is to prepare the individual layers of the board. This involves printing the circuit patterns onto the substrates using a photolithography process.
Lamination
The next step is to laminate the layers together using heat and pressure. The flexible layers are typically laminated first, followed by the rigid layers.
Drilling and Plating
After lamination, the board is drilled to create the necessary holes for component mounting and interconnects. The holes are then plated with copper to provide electrical connectivity between layers.
Coverlay Application
The coverlay is then applied over the flexible sections of the board to provide insulation and protection against damage.
Solder Mask and Silkscreen
The final step is to apply the solder mask and silkscreen to the board. The solder mask provides insulation and protection against short circuits, while the silkscreen provides labeling and identification of components and features.
Advantages of Rigid-Flex PCBs over Flexible PCBs
While flexible PCBs offer many advantages over rigid PCBs, rigid-flex PCBs offer several key advantages over flexible PCBs:
Increased Reliability
Rigid-flex PCBs eliminate the need for connectors between rigid and flexible sections, reducing the number of potential failure points and improving overall reliability.
Space Savings
Rigid-flex PCBs allow for more compact packaging by enabling the board to be folded or bent to fit into tight spaces. This can result in significant space savings compared to using separate rigid and flexible boards.
Improved Signal Integrity
The elimination of connectors between rigid and flexible sections reduces signal loss and improves signal integrity. This is particularly important for high-speed applications.
Reduced Assembly Costs
By combining rigid and flexible sections into a single board, assembly costs can be reduced since there are fewer parts to assemble and less wiring required.
FAQs
What is the difference between rigid-flex PCBs and flexible PCBs?
Rigid-flex PCBs combine both rigid and flexible substrates into a single board, while flexible PCBs use only flexible substrates. Rigid-flex PCBs offer increased reliability, space savings, improved signal integrity, and reduced assembly costs compared to flexible PCBs.
What are the key design considerations for rigid-flex PCBs?
The key design considerations for rigid-flex PCBs include bend radius, layer stack-up, material selection, and coverlay. It is important to carefully consider each of these factors to ensure proper performance and reliability.
What are the common applications for rigid-flex PCBs?
Rigid-flex PCBs are commonly used in aerospace and defense, medical devices, consumer electronics, and automotive electronics applications where space is limited, and reliability is critical.
How does the manufacturing process for rigid-flex PCBs differ from standard PCBs?
The manufacturing process for rigid-flex PCBs is more complex than for standard rigid or flexible PCBs due to the need to combine both rigid and flexible substrates into a single board. The key steps in the manufacturing process include layer preparation, lamination, drilling and plating, coverlay application, and solder mask and silkscreen application.
What are the advantages of using rigid-flex PCBs over flexible PCBs?
The advantages of using rigid-flex PCBs over flexible PCBs include increased reliability, space savings, improved signal integrity, and reduced assembly costs. Rigid-flex PCBs eliminate the need for connectors between rigid and flexible sections, reducing the number of potential failure points and enabling more compact packaging.
Conclusion
Rigid-flex PCBs offer a unique combination of the benefits of both rigid and flexible PCBs, making them an attractive option for many electronic projects. By combining rigid and flexible substrates into a single board, rigid-flex PCBs offer increased reliability, space savings, improved signal integrity, and reduced assembly costs compared to traditional flexible PCBs.
When designing a rigid-flex PCB, it is important to carefully consider key factors such as bend radius, layer stack-up, material selection, and coverlay to ensure proper performance and reliability. Rigid-flex PCBs are commonly used in a wide range of applications, including aerospace and defense, medical devices, consumer electronics, and automotive electronics.
While the manufacturing process for rigid-flex PCBs is more complex than for standard PCBs, the benefits they offer make them a compelling choice for many electronic projects. As technology continues to advance and the demand for smaller, more reliable electronic devices grows, rigid-flex PCBs are likely to play an increasingly important role in the electronics industry.
Leave a Reply