Printed circuit boards (PCBs) are an essential component of most modern electronic devices. They provide the physical platform to mount and interconnect electronic components using conductive copper traces etched from copper sheets laminated onto a non-conductive substrate.
While PCBs may seem simple in concept, designing and manufacturing them involves complex processes that require substantial investments in equipment and labor. This results in significant costs that are ultimately passed down to the end-user of the electronics.
Below we explore the key factors that make PCB fabrication an expensive process:
Raw Materials
The raw materials that go into making PCBs are themselves costly to procure.
Copper
Copper is the primary conductive material used to create the traces on a PCB. High purity copper foil is required to allow for the accurate etching of fine trace patterns.
The price of copper has increased over 300% in the last 20 years. Copper prices are influenced by various economic and geopolitical factors affecting its supply and demand.
Show Image<p class=”text-center”>Price of Copper 1990-2023. Source: <a href=”https://www.macrotrends.net/1476/copper-prices-historical-chart-data”>Macrotrends</a></p>
Laminates
The substrate material on which copper traces are etched are made from glass reinforced epoxy resins, commonly referred to as FR-4 laminates. These laminates provide the mechanical structure to PCBs.
The raw materials to manufacture laminates are petroleum derivatives, whose prices vary with crude oil prices. Limited competition among laminate suppliers also leads to higher prices.
Solder Masks and Legend Inks
Additional coatings like solder masks and legend inks are applied on PCBs to protect copper traces from oxidation and mark component outlines. These coatings are made from specialty polymers and inks that are relatively expensive.
Fabrication Process Costs
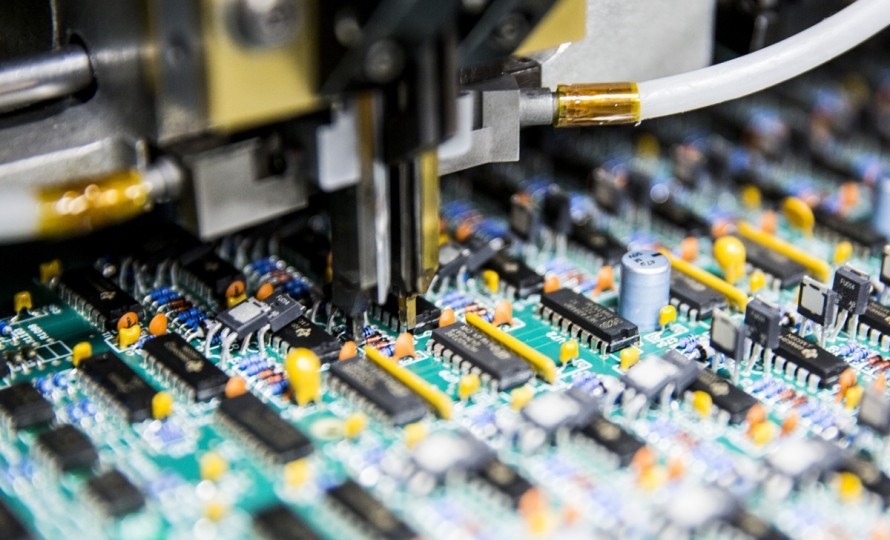
PCB fabrication involves many complex processes that require expensive equipment operated by skilled personnel.
Design Costs
Every PCB design starts with electronic circuit schematics that are translated into physical PCB layouts using specialized CAD software tools. This requires engineers with expertise in PCB design principles. Their efforts incur labor costs.
Complex designs need rigorous verification using PCB modeling and analysis software to avoid costly errors in fabrication. This adds to the design overheads.
Equipment Costs
Fabricating PCBs necessitates large investments in equipment like:
- Photolithography machines to transfer circuit patterns onto boards.
- Wet chemical process lines for etching, stripping and electroplating.
- Mechanical drilling machines.
- Solder mask and silkscreen printers.
- Automated optical inspection (AOI) systems.
The cost of this equipment runs into millions of dollars and they require significant maintenance expenditures as well. These costs are depreciated over time and built into the board fabrication charges.
Labor Costs
PCB fabrication facilities require many highly skilled technicians and process engineers to operate the equipment and maintain processes. Their labor costs contribute to the overall expenditure.
Testing and Inspection
To ensure quality, fabricated PCBs undergo comprehensive testing and inspection using techniques like:
- Flying probe testing to verify shorts and opens by checking electrical connectivity.
- X-ray inspection to detect faults in inner layer alignments.
- Automated optical inspection (AOI) to visually detect defects.
- Impedance testing using network analyzers to measure signal integrity.
Performing these tests requires additional equipment investments and skilled labor, adding to cost.
Waste Treatment
The chemicals used in PCB fabrication like etchants, strippers and electroplating baths need special handling and waste treatment before disposal. Proper waste treatment facilities have considerable cost implications.
Operational Expenses
PCB fabricators have significant fixed costs related to plant infrastructure and operations. These ultimately reflect in the pricing of the boards.
Facility Costs
PCB fabrication plants require large factory spaces with stringent temperature and humidity controls to maintain process stability. These specialized facilities are expensive to construct and maintain.
Utility Costs
Operating the plant infrastructure and production equipment consumes considerable amounts of electricity and water. These utility costs are substantial.
Insurance and Taxes
PCB fabricators also have to account for insurance premiums to cover equipment and liabilities. Local taxes and regulations also contribute to operational expenses.
Profit Margins
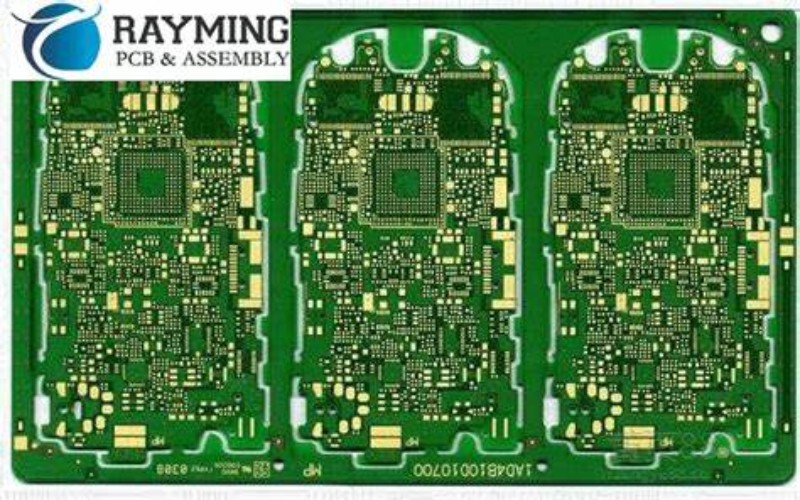
As commercial enterprises, PCB fabricators build in profit margins to remain financially viable businesses. Most fabricators target 10-15% profit on their pricing to the electronics industry.
Impact of Complexity
The complexity of the PCB design directly impacts the fabrication costs. Here are some examples:
Board Layer Count
Multi-layer boards with large layer counts (>12) require more process steps, materials, equipment usage and labor to fabricate. This exponentially increases their cost.
Board Size
Larger PCBs reduce the number of boards that can be fabricated on a panel. This lowers fabrication throughput and drives up cost.
High Density Interconnects
Densely packed traces and pads on boards require more accurate photolithography and drilling, increasing tooling costs.
Tight Tolerances
Precise dimensional and electrical tolerances call for more rigorous testing and inspection which adds cost.
Advanced Materials
Specialty materials like ceramic substrates or RF materials are more expensive than standard FR-4 laminates.
Supply and Demand Dynamics
The economics of supply and demand also influence PCB pricing:
Limited Fabricators
There are fewer than 2000 qualified PCB fabricators worldwide creating a supply shortage. This allows fabricators to keep prices high, especially for quick-turn orders.
High Demand
The electronics industry is in a phase of rapid innovation and growth across sectors like consumer, automotive, aerospace, medical, etc. This is fueling enormous demand for PCBs. Peak demand conditions enable fabricators to charge higher prices.
Commoditization Pressure
On the other hand, PCB fabrication is also becoming increasingly commoditized, encouraging price competition among fabricators. This creates downward pressure on prices.
Summary
In summary, PCB fabrication involves substantial raw material, equipment, labor and operational costs. The need to maintain profitability necessitates relatively high pricing levels to the electronics industry. And complexity of designs along with market dynamics further influence pricing trends.
Frequently Asked Questions
How are PCBs priced?
PCB prices are generally determined by the following key factors:
- Base price per square inch depending on layer count. This accounts for bulk of cost.
- Additional charges for more board layers.
- Surcharges for advanced PCB finishes like ENIG, Immersion Silver etc.
- Adders for smaller quantity orders.
- Premiums for faster delivery lead times.
- Complexity factors like density, line width, tolerances etc.
Most PCB fabricators have online pricing calculators that provide price estimates based on these parameters.
Why are multilayer PCBs more expensive?
Fabricating multilayer PCBs with 4, 6 or more layers adds substantial costs in materials, processes and labor compared to 2-layer boards, including:
- Additional raw material cost for inner layer copper and prepreg bonding sheet.
- Increased drilling costs due to close tolerance requirements.
- Additional steps for lamination, deburring, via preparation etc.
- Higher scrap rates due to complexity.
- More expensive testing (x-ray, impedance etc)
- Lower panel utilization and throughput.
This escalates the fabrication costs rapidly with every additional board layer.
How can I reduce PCB fabrication costs?
You can lower your PCB fabrication costs by:
- Optimizing board layout for simplicity and efficiency.
- Using the least number of layers required.
- Selecting larger minimum line/space widths.
- Specifying slightly relaxed tolerance requirements.
- Ordering prototyping volumes to avail lower prices.
- Comparing quotes from multiple fabricators.
- Consolidating orders to get high quantity discounts.
- Using standard FR-4 material rather than high-end laminates.
- Choosing cheaper PCB finishes like HASL, OSP or Immersion Tin.
Is HDI PCB technology more expensive?
Yes, high density interconnect (HDI) PCB fabrication using microvias and thinner traces is more expensive compared to conventional PCBs due to:
- Added raw material cost for build-up dielectric films.
- Additional fabrication steps for microvias and thin cores.
- More process development time.
- Lower yield rates due to fine features.
- Need for specialized imaging and drilling equipment.
- Higher requirements for inspection and testing.
However, the benefits of miniaturization and multilayer integration using HDI offset its cost premium for many applications.
Are flex-rigid PCBs costlier than rigid PCBs?
Yes, flex-rigid PCBs that combine rigid and flexible substrates in one assembly are generally much more expensive than conventional rigid PCBs. Reasons include:
- Dual set of raw materials for flexible and rigid portions.
- Complex fabrication process including bonding and lamination.
- Lower panel utilization due to smaller flexible components.
- Challenging testing requirements due to mix of technologies.
- Additional process steps for contours and bends.
- Lower overall production throughput and yield.
The unique integration benefits of flex-rigid PCBs justify the cost premium for certain products.
Leave a Reply