Introduction to Soldermask and Its Importance in PCB Manufacturing
Soldermask, also known as solder resist or solder mask, is a crucial component in the manufacture of printed circuit boards (PCBs). It is a thin, protective layer applied to the copper traces of a PCB to prevent solder bridges from forming between closely spaced pads, thereby ensuring the reliability and functionality of the circuit board. Soldermask also provides protection against oxidation and corrosion of the copper traces, enhancing the durability of the PCB.
In addition to its practical functions, soldermask also serves an aesthetic purpose by giving the PCB its distinctive color. While soldermask is available in various colors such as red, blue, yellow, black, and white, green is by far the most commonly used color in PCB fabrication. This article will explore the reasons behind the popularity of green soldermask and its advantages over other colors.
The Role of Soldermask in PCB Fabrication
Before delving into the specifics of green soldermask, it is essential to understand the role of soldermask in the PCB manufacturing process. The primary functions of soldermask are:
-
Insulation: Soldermask acts as an insulating layer, preventing short circuits caused by accidental solder bridges between adjacent pads or traces.
-
Protection: The soldermask layer protects the copper traces from oxidation, corrosion, and mechanical damage, thereby extending the lifespan of the PCB.
-
Solder Control: Soldermask helps to control the flow of solder during the soldering process, ensuring that solder only adheres to the exposed metal pads and not to the protected areas.
-
Aesthetics: Soldermask gives the PCB a clean, professional appearance and can be used to display text, logos, or other markings on the board’s surface.
The Advantages of Green Soldermask
1. Enhanced Contrast and Visibility
One of the primary reasons for the widespread use of green soldermask is its excellent contrast against the white silkscreen markings commonly used on PCBs. The high contrast between green and white makes it easier for technicians to read text, identify components, and inspect the board for any defects or irregularities.
In comparison, other soldermask colors, such as black or blue, may not provide sufficient contrast against the silkscreen markings, leading to reduced visibility and potential difficulties in PCB assembly and inspection.
2. Improved Eye Comfort During Inspection
The human eye is most sensitive to green light, which falls in the middle of the visible light spectrum. As a result, green soldermask is less straining on the eyes during prolonged periods of PCB inspection and assembly.
In contrast, colors at the extreme ends of the visible spectrum, such as red or blue, can cause more eye strain and fatigue over extended periods. This is particularly important in industrial settings where technicians may spend several hours working on PCBs.
3. Better Photoimageable Properties
Green soldermask has excellent photoimageable properties, which means it can be precisely patterned using photolithography techniques. This allows for the creation of high-resolution, well-defined openings in the soldermask layer, exposing the underlying copper pads for soldering.
The photoimageable properties of green soldermask are superior to those of other colors, particularly darker shades like black or blue. This results in better soldermask coverage, fewer defects, and improved overall quality of the PCB.
4. Widespread Availability and Cost-Effectiveness
Due to its popularity, green soldermask is widely available from most PCB manufacturers and suppliers. This widespread availability ensures a consistent supply of green soldermask materials, reducing the likelihood of production delays or shortages.
Moreover, the high demand for green soldermask has led to increased competition among suppliers, resulting in lower prices compared to other soldermask colors. This cost-effectiveness makes green soldermask an attractive option for PCB manufacturers looking to minimize production costs without compromising on quality.
5. Proven Reliability and Industry Acceptance
Green soldermask has been used in PCB fabrication for several decades and has a proven track record of reliability and performance. Its long history of successful use in various applications, ranging from consumer electronics to aerospace and military systems, has made it the preferred choice for many PCB designers and manufacturers.
The widespread industry acceptance of green soldermask also means that it is compatible with a wide range of PCB materials, manufacturing processes, and soldering techniques. This compatibility ensures a smooth and efficient production process, reducing the risk of errors or complications.
Other Soldermask Colors and Their Applications
While green is the most common soldermask color, other colors are used in specific applications or for aesthetic purposes. Some examples include:
-
Red: Red soldermask is sometimes used in high-reliability applications, such as aerospace or military systems, due to its high visibility and contrast against other colors.
-
Blue: Blue soldermask is occasionally used for aesthetic reasons, particularly in consumer electronics where a distinctive appearance is desired.
-
Black: Black soldermask is used in some high-end audio equipment and luxury consumer products for its sleek, modern appearance.
-
White: White soldermask is rarely used due to its low contrast against the silkscreen markings and its tendency to show dirt and stains more easily than other colors.
Despite these alternative colors, green remains the most popular choice for the majority of PCB applications due to its superior performance, reliability, and cost-effectiveness.
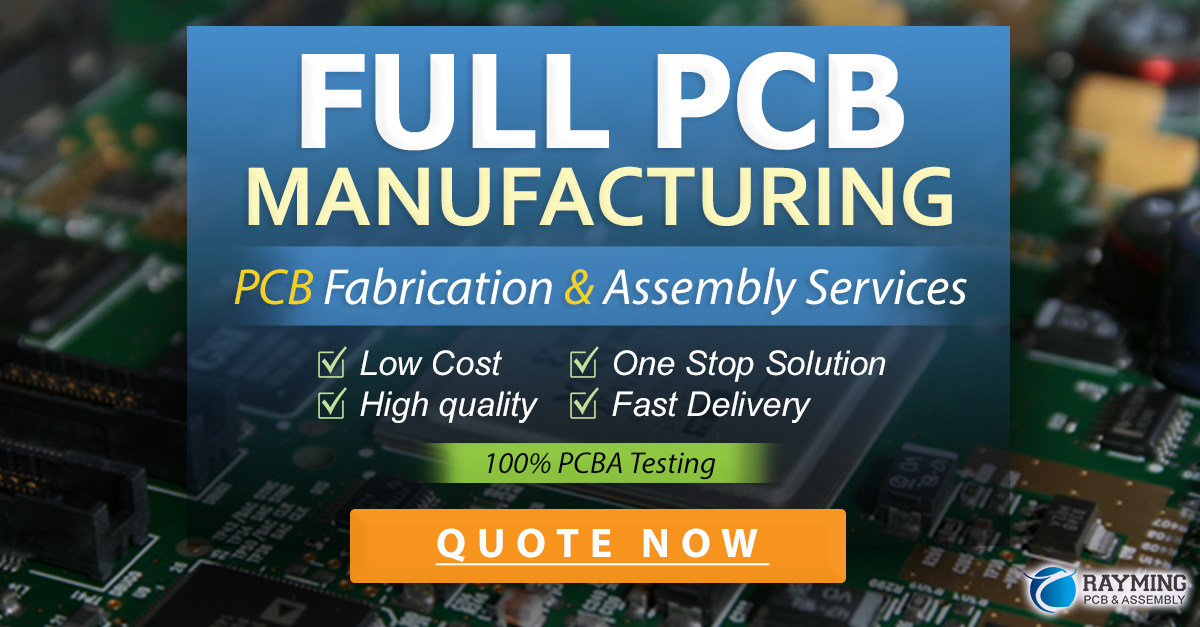
Frequently Asked Questions (FAQ)
1. Is green soldermask always the best choice for PCB fabrication?
While green soldermask is the most common and generally preferred choice, there may be specific applications where other colors are more suitable. For example, red soldermask may be preferred in high-reliability applications where enhanced visibility is critical.
2. Can I specify a custom soldermask color for my PCB?
Yes, most PCB manufacturers offer the option to specify custom soldermask colors. However, custom colors may be subject to minimum order quantities and additional costs compared to standard colors like green.
3. Does the choice of soldermask color affect the functionality of the PCB?
In most cases, the soldermask color does not directly affect the functionality of the PCB. However, some colors may have slightly different properties in terms of photoimageability, adhesion, or resistance to environmental factors, which could indirectly impact the PCB’s performance.
4. Are there any disadvantages to using green soldermask?
There are no significant disadvantages to using green soldermask. Its widespread use and proven reliability make it a safe and effective choice for most PCB applications.
5. Can I change the soldermask color on an existing PCB design?
Yes, it is generally possible to change the soldermask color on an existing PCB design. However, this may require some adjustments to the design files and could incur additional costs, particularly if the new color requires different processing or materials.
Conclusion
Green soldermask has become the industry standard for PCB fabrication due to its numerous advantages, including enhanced contrast and visibility, improved eye comfort during inspection, better photoimageable properties, widespread availability, cost-effectiveness, and proven reliability.
While other soldermask colors are available for specific applications or aesthetic purposes, green remains the most popular choice for the majority of PCB manufacturing. Its superior performance and long history of successful use make it the preferred option for PCB designers and manufacturers worldwide.
As PCB technology continues to evolve, it is likely that green soldermask will maintain its position as the go-to choice for most applications. However, advances in materials science and manufacturing processes may lead to the development of new soldermask formulations that offer even better performance, reliability, and cost-effectiveness in the future.
Regardless of these potential future developments, the current widespread use and acceptance of green soldermask in the PCB industry ensure that it will remain a crucial component in the fabrication of high-quality, reliable printed circuit boards for years to come.
Soldermask Color | Advantages | Disadvantages |
---|---|---|
Green | – High contrast against silkscreen – Easy on the eyes during inspection – Excellent photoimageable properties – Widely available and cost-effective – Proven reliability and industry acceptance |
– None significant |
Red | – High visibility and contrast in specific applications | – Less common and may be more expensive – May not be as easy on the eyes during prolonged inspection |
Blue | – Aesthetic appeal in consumer electronics | – Lower contrast against silkscreen – May be less photoimageable than green – Less common and may be more expensive |
Black | – Sleek, modern appearance in high-end products | – Low contrast against silkscreen – May be less photoimageable than green – Less common and may be more expensive |
White | – Unique appearance in specific applications | – Low contrast against silkscreen – Shows dirt and stains easily – Rarely used in PCB fabrication |
Leave a Reply