Introduction
In manufacturing and engineering, holes are required in parts and components for various reasons like fastening, locating, alignment, weight reduction etc. Holes can be broadly classified into two categories – through holes and blind holes. As the names suggest, a through hole passes completely through the workpiece, while a blind hole extends only partially into the part. Both types of holes have their specific applications, but through holes are generally preferred over blind holes for several reasons. In this article, we will look at the differences between through and blind holes and examine why through holes are often a better design choice.
Differences Between Through Holes and Blind Holes
Here are the main differences between through holes and blind holes:
Parameter | Through Hole | Blind Hole |
---|---|---|
Definition | Extends completely through the workpiece | Extends only partially into the workpiece |
Manufacturing process | Can be manufactured by conventional drilling | Requires special tools like blind hole drilling machines or gun drilling |
Cost | Lower cost to manufacture | Higher cost due to special tooling required |
Chips removal | Chips can escape through the hole | Chips get accumulated inside the hole |
Inspectability | Can be easily inspected visually or with instruments | Difficult to inspect visually or with instruments due to limited access |
Stress concentration | Lower stress concentration | Higher stress concentration at the closed end |
Manufacturing Process
Through holes are relatively simple to manufacture and can be produced by conventional drilling processes on drill presses or CNC machines. However, blind holes require specialized deep hole drilling equipment like gun drilling machines that are designed to drill deep cavities. The additional cost of acquiring such capital equipment makes manufacturing blind holes more expensive.
Chips Removal
During drilling, the metal chips produced must be effectively removed from the hole to avoid buildup. In through holes, the chips can easily escape through the hole. But with blind holes, chip removal is harder due to the closed end, often requiring peck drilling and specialized evacuation systems. Poor chip control can damage the hole surface finish.
Inspectability
The full length of through holes is visible, allowing easy inspection of parameters like size, surface finish, hole position, etc. But only the opening of blind holes is accessible, making inspection with gauges or instruments difficult. Specialized techniques like Eddy current testing may be needed to evaluate blind hole properties.
Stress Concentration
The closed end of a blind hole causes stress concentration in that region, which can lead to premature fatigue failure. The open end of through holes has lower stress levels, improving fatigue life. This makes through holes preferable for highly stressed components.
Advantages of Through Holes
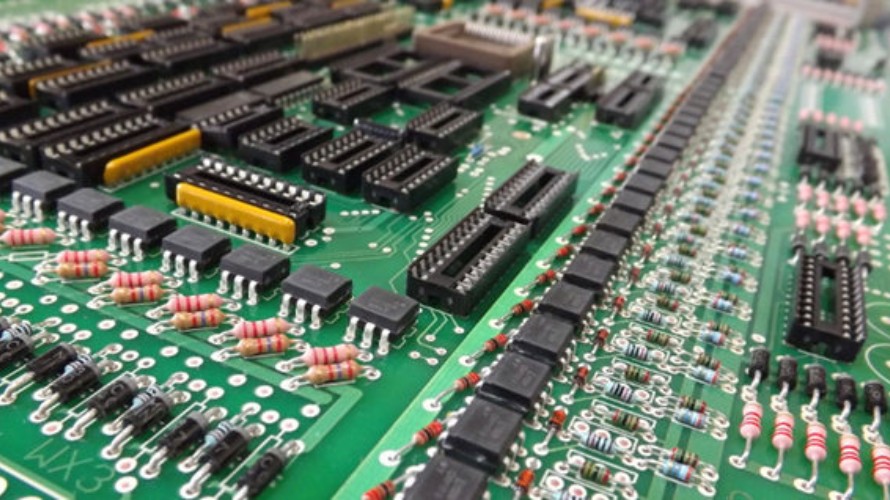
Based on the differences discussed earlier, here are some specific advantages of using through holes rather than blind holes:
1. Lower Manufacturing Cost
Through holes don’t require specialized deep drilling equipment and can be produced on any standard machining center. This makes them faster and cheaper to manufacture. Blind holes need additional operations to open them up, adding to cost.
2. Improved Hole Quality
The drilling process is more stable for through holes because chips can escape easily. This results in better dimensional accuracy, surface finish and hole roundness. Blind holes are prone to errors like taper and poor surface finish due to chip welding.
3. Easier Assembly
Components with through holes are easier to disassemble for maintenance because fasteners can be driven out from either side. For blind holes, fastener removal is only possible from one side. This maintainability advantage is important for machines and equipment.
4. Effective Cleaning
Because through holes are open on both sides, they can be flushed with cleaning solutions to remove grit, debris and coolant. Blind holes are difficult to clean properly due to limited access. Contaminants left in blind holes can lead to corrosion over time.
5. Facilitates Inline Inspection
For applications like jet engine turbine blades, inline inspection using techniques like eddy current, ultrasonic or borescope testing is required. This is only possible if through holes are designed. Blind holes do not allow inline inspection.
6. Improved Fatigue Life
The lower stress concentration of through holes makes them ideal for designing components subjected to cyclic stresses and vibrations like aircraft and automotive parts. The fatigue life of such dynamic components is enhanced with through holes.
7. Lower Tool Wear
The drilling tool only engages the workpiece material at the entrance in through holes. For blind holes, the tool is engaged along the full depth, leading to accelerated wear and breakage. Through holes allow faster production with lower tooling cost.
Disadvantages of Through Holes
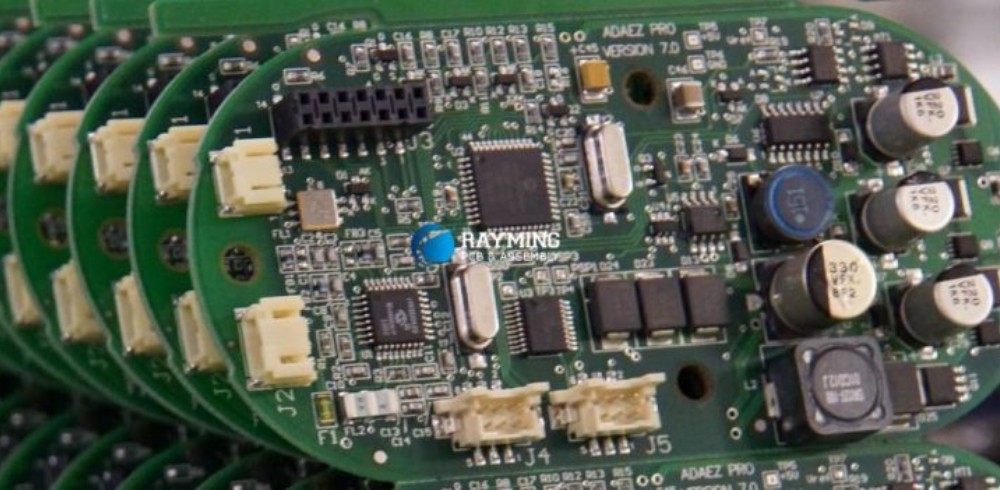
Despite the many advantages, through holes also have some limitations and disadvantages in certain situations:
- Weakens the structure by removing more material compared to a blind hole of the same diameter. This needs to be considered in the design.
- Requires access to both sides of the workpiece. Not suitable for one-sided applications.
- May not be preferred for sealing applications like hydraulic cylinders where leakage through the hole needs to be prevented.
- Coolant, lubricant or grease can leak out of through holes. Retention of these fluids may require blind holes in some cases.
- Generally not preferred for aesthetic reasons in visible components where the opposite hole should not be visible.
Applications Where Through Holes Work Better
Considering the pros and cons, here are some examples of applications where through holes are typically preferred:
Machine Frames
The frame and structural members of heavy machines like machine tools, presses and industrial robots require several drilled holes for assembly of components. Through holes allow easy bolt insertion and removal during maintenance. Blind holes would be inefficient and weaken the structure.
Aircraft Components
Aircraft skins, ribs, bulkheads and engine parts have millions of fastener holes. These must be through holes because of inline inspection requirements and also for lightning protection by allowing current to pass through the structure.
Automotive Parts
The cylinder head, wheels, axle housing, control arms and other chassis components in automobiles use through holes for mounting bolts and other fasteners. This makes assembly and disassembly easier.
Medical Equipment
Equipment like surgical tables, MRI machines and radiotherapy systems often need to be dismantled for cleaning and sterilization. Through holes in side frames, braces and bases allow easy access to fasteners.
Jigs and Fixtures
Jigs and fixtures are temporary workholding devices used in manufacturing. They require lots of holes and slots on the workholding surface for clamps and locators. Through holes allow flexible positioning of these clamping elements.
Conclusion
Through holes are generally the preferred design choice compared to blind holes for their lower manufacturing cost, improved quality, accessibility, inspectability and structural integrity. However, blind holes may be necessary in situations that require fluid retention, structural strength or aesthetic appeal. The intended application should guide the selection between through holes and blind holes during the design process. With the advancement of specialized machine tools, even blind holes can be produced efficiently today. But in most cases, the benefits of through holes like faster production, easier assembly and maintenance outweigh the downsides.
FAQ
Why are through holes easier to manufacture than blind holes?
Through holes can be manufactured by conventional twist drilling which is the most common and cost-effective holemaking process. But blind holes require specialized deep hole drilling equipment like gundrills. The high capital and tooling cost makes blind holes more expensive to produce.
How does chip evacuation differ between through holes and blind holes?
In through holes, chips can escape freely through the hole after being cut by the drill. But with blind holes, chips get accumulated at the closed end of the hole. This requires peck drilling and proper evacuation techniques to prevent chip welding and damage to the hole.
Why is inspection of through holes easier compared to blind holes?
Since a through hole is open on both sides, its full length is easily visible for inspection with go/no go gauges, coordinate measuring machines or borescopes. The closed end of blind holes cannot be inspected visually or with most instruments.
How does a blind hole increase stress concentration?
The intersection of the hole with the lower surface acts as a geometric stress riser. The rapid change in cross section concentrates force into a smaller area, increasing stress levels. Through holes avoid this because stresses can equalize along the full length of the hole.
When would blind holes be preferred over through holes?
For applications requiring fluid retention, sealing, and avoiding leakage, blind holes would be preferred. Also for aesthetic reasons, like not showing an open hole on the opposite side. Structural strength may require blind holes if reducing cross section with through holes is undesirable.
Leave a Reply