What is Soldermask?
Soldermask, also known as solder resist or solder stop mask, is a thin layer of polymer material applied to the surface of a PCB. Its primary purpose is to protect the copper traces and pads from oxidation, prevent solder bridges during the soldering process, and provide electrical insulation between conductive areas. Soldermask is typically applied using screen printing or photoimaging techniques and is available in various colors, with green being the most common.
Why Use White Soldermask for LED PCBs?
While green soldermask is the default choice for most PCB applications, white soldermask offers several advantages when it comes to LED PCBs:
Enhanced Light Reflection
One of the primary benefits of using white soldermask in LED PCBs is its ability to reflect light more efficiently than darker colors. When an LED emits light, some of that light is directed downwards towards the PCB surface. A white soldermask will reflect a significant portion of this light back towards the desired direction, increasing the overall light output and efficiency of the LED system.
In contrast, darker soldermask colors like green or black will absorb more of the LED light, reducing the amount of light that reaches the intended target. This absorption can lead to lower luminous efficacy and may require the use of more LEDs or higher drive currents to achieve the desired light output, which in turn increases power consumption and heat generation.
Improved Color Rendering
Another advantage of white soldermask is its ability to improve color rendering in LED lighting applications. Color rendering refers to how accurately a light source can reproduce the colors of objects compared to a reference light source, such as natural daylight. A higher color rendering index (CRI) indicates better color accuracy and visual quality.
When using colored LEDs (e.g., red, green, blue) or multi-color LED arrays, the white soldermask helps to reflect the light without introducing any color distortion. This ensures that the LED colors mix properly and maintain their intended hue and saturation. In contrast, darker soldermask colors may absorb certain wavelengths more than others, leading to color shifts and reduced color accuracy.
Enhanced Visual Aesthetics
White soldermask can also enhance the visual aesthetics of LED PCBs, particularly in applications where the PCB is visible to the end-user. The clean, bright appearance of white soldermask can give the product a modern and high-tech look, which may be desirable in consumer electronics, automotive lighting, or architectural lighting applications.
Furthermore, white soldermask can serve as a neutral background for silkscreen labels, logos, or other markings on the PCB. This can improve the readability and contrast of the markings, making it easier for users to identify components or troubleshoot issues.
Thermal Management Considerations
While white soldermask can improve light reflection and color rendering, it is essential to consider its impact on the thermal management of LED PCBs. LEDs generate a significant amount of heat during operation, which must be dissipated effectively to prevent premature failure or performance degradation.
White soldermask has a higher thermal emissivity than darker colors, which means it can emit more heat through radiation. However, it also has a higher thermal reflectivity, which can reflect some of the heat generated by the LEDs back towards the components. The net effect on thermal management will depend on factors such as the PCB layout, LED power density, and the presence of other thermal management solutions like heatsinks or thermal vias.
In general, the benefits of using white soldermask for light reflection and color rendering will outweigh the potential impact on thermal management in most LED PCB applications. However, it is essential to conduct thorough thermal simulations and testing to ensure that the LED system operates within its specified temperature range and meets the required reliability and lifetime targets.
Choosing the Right White Soldermask Material
When selecting a white soldermask material for LED PCBs, several factors should be considered to ensure optimal performance and reliability:
Reflectivity and Whiteness
The reflectivity and whiteness of the soldermask material will directly impact its ability to reflect LED light efficiently. Look for materials with high reflectivity values (typically >85%) and high whiteness indices (>90) to maximize light output and color rendering.
Thermal Stability
LED PCBs often operate at elevated temperatures due to the heat generated by the LEDs. The white soldermask material should have good thermal stability to prevent discoloration, cracking, or delamination over the expected lifetime of the product. Look for materials with high glass transition temperatures (Tg) and low coefficients of thermal expansion (CTE).
Compatibility with LED Wavelengths
Some white soldermask materials may exhibit different reflectivity and stability characteristics depending on the wavelength of the LED light. Ensure that the chosen material is compatible with the specific LED wavelengths used in the application, particularly for UV or blue light LEDs.
Ease of Processing
The white soldermask material should be compatible with the PCB manufacturing process and equipment. Consider factors such as the viscosity, curing time, and temperature requirements of the material to ensure efficient and reliable application.
Cost and Availability
Finally, consider the cost and availability of the white soldermask material. While some premium materials may offer superior performance, they may also come at a higher cost or have longer lead times. Strike a balance between performance, cost, and availability based on the specific requirements of the LED PCB application.
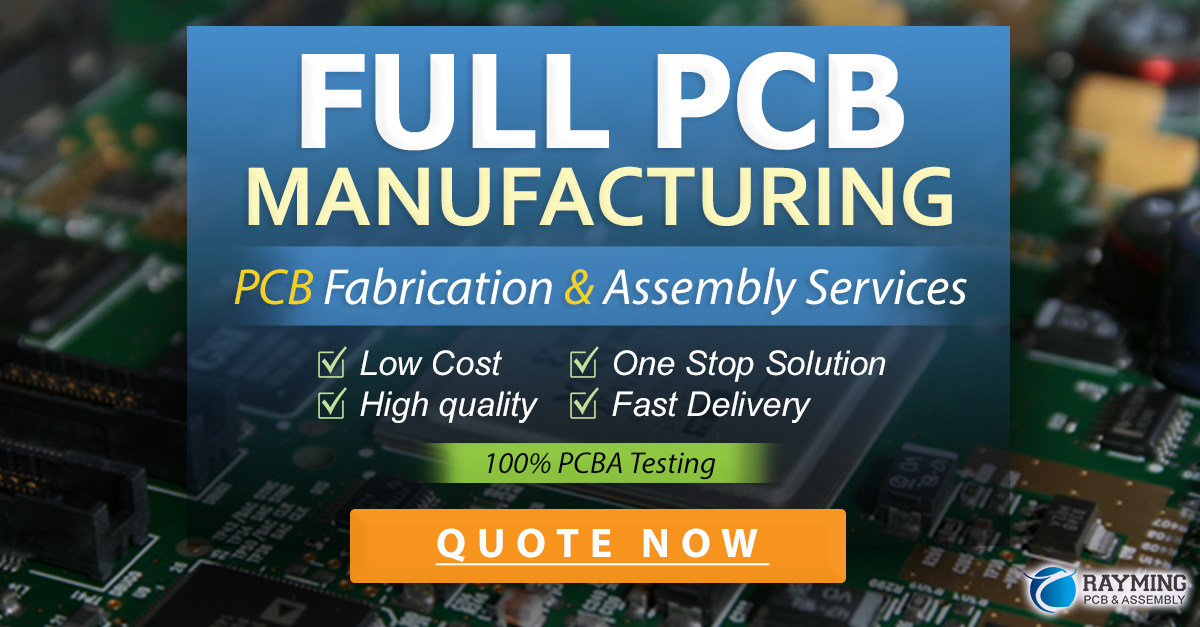
Table: Comparison of White Soldermask Materials
Material | Reflectivity | Whiteness Index | Thermal Stability (Tg) | LED Wavelength Compatibility | Ease of Processing | Cost |
---|---|---|---|---|---|---|
Material A | 90% | 95 | 150°C | UV, Blue, Green, Red | Easy | $$ |
Material B | 85% | 90 | 130°C | Blue, Green, Red | Moderate | $ |
Material C | 95% | 98 | 180°C | UV, Blue, Green, Red | Difficult | $$$ |
FAQ
-
Q: Can white soldermask be used for all types of LED PCBs?
A: White soldermask can be used for most LED PCB applications, but it is particularly beneficial for applications that require high light output, good color rendering, or attractive visual aesthetics. Some examples include LED lighting, display backlights, and automotive lighting. -
Q: Is white soldermask more expensive than green soldermask?
A: In general, white soldermask materials may be slightly more expensive than standard green soldermask materials due to the additional pigments and processing required to achieve high whiteness and reflectivity. However, the cost difference is usually small and may be offset by the improved performance and aesthetics of the final product. -
Q: Can white soldermask be applied using the same processes as green soldermask?
A: Yes, white soldermask can be applied using the same screen printing or photoimaging processes as green soldermask. However, some white soldermask materials may have different viscosity, curing time, or temperature requirements, so it is essential to select a material that is compatible with the existing PCB manufacturing process and equipment. -
Q: How does white soldermask affect the thermal management of LED PCBs?
A: White soldermask has a higher thermal emissivity and reflectivity than darker colors, which can impact the thermal management of LED PCBs. While it can help to emit more heat through radiation, it may also reflect some heat back towards the components. The net effect on thermal management will depend on factors such as the PCB layout, LED power density, and other thermal management solutions used. -
Q: Can white soldermask be used in combination with other colors for LED PCBs?
A: Yes, white soldermask can be used in combination with other soldermask colors or even selective areas of exposed copper on the same PCB. This can be useful for creating specific lighting effects, enhancing thermal management, or improving the visual aesthetics of the product. However, combining multiple colors or exposed copper areas may increase the complexity and cost of the PCB manufacturing process.
In conclusion, white soldermask offers several benefits for LED PCB applications, including enhanced light reflection, improved color rendering, and attractive visual aesthetics. When selecting a white soldermask material, consider factors such as reflectivity, thermal stability, compatibility with LED wavelengths, ease of processing, and cost. By carefully evaluating these factors and conducting thorough testing, LED PCB designers can leverage the advantages of white soldermask to create high-performance, visually appealing, and reliable LED systems.
Leave a Reply