The Basics of Through-hole PCB Assembly
Components and PCB Design
Through-hole PCB Assembly involves the use of components with long leads that are inserted into drilled holes on the PCB. These components can include resistors, capacitors, inductors, diodes, transistors, and integrated circuits (ICs) in various package types, such as DIP (Dual Inline Package) and SIP (Single Inline Package).
When designing a PCB for through-hole assembly, engineers must consider several factors:
- Hole size: The drilled holes must be large enough to accommodate the component leads while maintaining the structural integrity of the PCB.
- Pad size: The copper pads surrounding the holes should be sized appropriately to ensure proper soldering and electrical connection.
- Component spacing: Adequate spacing between components is necessary to avoid physical interference and to facilitate manual soldering if required.
Assembly Process
The through-hole PCB assembly process typically involves the following steps:
- PCB fabrication: The bare PCB is manufactured with the necessary drilled holes and copper traces.
- Component placement: The through-hole components are inserted into the corresponding holes on the PCB, either manually or using automated insertion machines.
- Soldering: The component leads are soldered to the copper pads on the opposite side of the board, creating a secure mechanical and electrical connection. This can be done manually using a soldering iron or through wave soldering, where the entire board is passed over a molten solder bath.
- Inspection and testing: The assembled PCB undergoes visual inspection and electrical testing to ensure proper functionality and adherence to quality standards.
Advantages of Through-hole PCB Assembly
Mechanical Strength
One of the primary advantages of through-hole PCB assembly is the superior mechanical strength it offers compared to surface-mount technology. The leads of through-hole components extend through the PCB and are soldered on the opposite side, creating a strong physical connection that can withstand greater stress and vibration. This makes through-hole assembly ideal for applications that require high reliability, such as:
- Aerospace and military equipment
- Automotive electronics
- Industrial control systems
- Medical devices
Ease of Manual Assembly and Repair
Through-hole components are generally easier to handle and install manually compared to their surface-mount counterparts. This can be advantageous in low-volume production runs or prototyping, where the cost of automated assembly equipment may not be justified. Additionally, through-hole boards are often easier to repair and modify, as the components can be more readily accessed and replaced using manual soldering techniques.
Thermal Management
The leads of through-hole components, which extend through the PCB, can act as heat dissipators, allowing for better thermal management compared to surface-mount devices. This can be particularly beneficial in high-power applications or when dealing with components that generate significant amounts of heat, such as power transistors or voltage regulators.
Disadvantages of Through-hole PCB Assembly
Size and Density Limitations
One of the main drawbacks of through-hole PCB assembly is the limited component density and larger board size compared to surface-mount designs. Through-hole components are generally larger and require more space on the PCB due to the drilled holes and the need for adequate spacing between components. This can result in bulkier and heavier PCBs, which may not be suitable for applications where space and weight are critical factors, such as mobile devices or wearable electronics.
Higher Assembly Costs
Through-hole PCB assembly can be more time-consuming and labor-intensive compared to surface-mount assembly, particularly when done manually. The need for drilling holes and the more complex soldering process can increase production costs, especially in high-volume manufacturing. However, for low-volume runs or projects requiring manual assembly, through-hole PCBs may still be a cost-effective option.
Limited Component Availability
As surface-mount technology has become increasingly popular, some newer electronic components may only be available in surface-mount packages. This can limit the design options for through-hole PCBs and may require the use of adapters or carrier boards to incorporate surface-mount devices into a through-hole design.
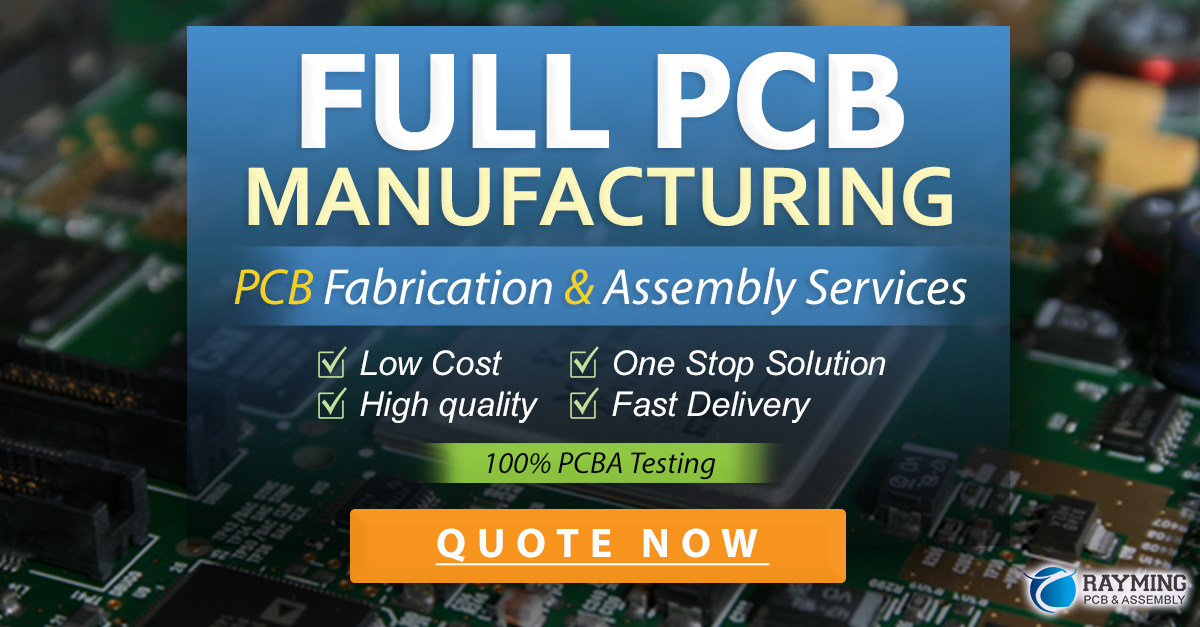
Comparison with Surface-Mount Technology (SMT)
Surface-mount technology has gained significant popularity in recent years due to its advantages in terms of component density, board size, and assembly efficiency. SMT components are mounted directly onto the surface of the PCB without the need for drilled holes, allowing for smaller and more compact designs.
Aspect | Through-hole PCB Assembly | Surface-Mount Technology (SMT) |
---|---|---|
Component size | Larger | Smaller |
Board density | Lower | Higher |
Assembly cost | Higher for high-volume production | Lower for high-volume production |
Manual assembly | Easier | More challenging |
Mechanical strength | Higher | Lower |
Thermal management | Better | Adequate |
Component availability | Limited for newer components | Wider range |
Despite the advantages of SMT, through-hole PCB assembly remains a viable and preferred choice for many applications, particularly those requiring high reliability, ease of manual assembly, or better thermal management.
Applications of Through-hole PCB Assembly
Through-hole PCB assembly finds use in a wide range of industries and applications, including:
- Aerospace and military: Through-hole PCBs are often used in aerospace and military equipment due to their high reliability and ability to withstand harsh environmental conditions.
- Automotive electronics: The mechanical strength and thermal management capabilities of through-hole assemblies make them suitable for automotive applications, such as engine control units and power distribution systems.
- Industrial control systems: Through-hole PCBs are commonly used in industrial control systems, where reliability and ease of maintenance are critical factors.
- Medical devices: Some medical devices, particularly those requiring high reliability or manual assembly, may employ through-hole PCB assembly techniques.
- Prototyping and low-volume production: Through-hole assembly can be a cost-effective choice for prototyping and low-volume production runs, where the benefits of automated SMT assembly may not justify the associated costs.
Future of Through-hole PCB Assembly
While surface-mount technology continues to dominate the electronics industry, through-hole PCB assembly is likely to maintain its presence in specific applications and niche markets. As technology advances, some of the limitations of through-hole assembly may be addressed through innovations in component packaging, PCB materials, and assembly processes.
One example of this is the development of press-fit technology, which allows for the mechanical insertion of through-hole components into a PCB without the need for soldering. This technique combines the benefits of through-hole assembly’s mechanical strength with the efficiency of solderless assembly.
Additionally, the growing demand for more environmentally-friendly electronics manufacturing processes may lead to advancements in lead-free soldering techniques and materials, further improving the sustainability of through-hole PCB assembly.
Frequently Asked Questions (FAQ)
-
What is the difference between through-hole and surface-mount PCB assembly?
Through-hole PCB assembly involves inserting component leads through drilled holes in the PCB and soldering them on the opposite side, while surface-mount assembly involves mounting components directly onto the surface of the PCB without the need for drilled holes. -
When is through-hole PCB assembly preferred over surface-mount technology?
Through-hole PCB assembly is often preferred in applications that require high mechanical strength, better thermal management, ease of manual assembly, or high reliability. Examples include aerospace, military, automotive, and industrial control systems. -
Are through-hole components becoming obsolete?
While surface-mount components have become increasingly popular, through-hole components are still widely used and are not considered obsolete. Many applications continue to rely on through-hole PCB assembly, and some components are still exclusively available in through-hole packages. -
Can through-hole and surface-mount components be used on the same PCB?
Yes, it is possible to design a PCB that incorporates both through-hole and surface-mount components. This is known as a mixed-technology or hybrid assembly, and it allows designers to take advantage of the benefits of both assembly methods. -
Is through-hole PCB assembly more expensive than surface-mount assembly?
The cost comparison between through-hole and surface-mount assembly depends on various factors, such as the volume of production, the complexity of the PCB design, and the level of automation used. In general, through-hole assembly can be more cost-effective for low-volume production or manual assembly, while surface-mount assembly is more efficient and cost-effective for high-volume production with automated assembly processes.
In conclusion, through-hole PCB assembly remains a reliable and widely-used method for mounting electronic components onto printed circuit boards. Despite the growing popularity of surface-mount technology, through-hole assembly continues to offer unique advantages in terms of mechanical strength, thermal management, and ease of manual assembly. As technology advances, through-hole PCB assembly is likely to maintain its relevance in specific applications and industries, while also benefiting from innovations in component packaging, materials, and assembly processes.
Leave a Reply