Introduction to Powder Spray Process
The powder spray process, also known as powder coating, is a widely used method for applying a protective and decorative finish to various products and components. This process involves the application of a dry powder, typically made from thermoplastic or thermoset polymers, onto the surface of a substrate using electrostatic charging and heat curing. Powder coating has gained popularity due to its durability, efficiency, and environmental friendliness compared to traditional liquid painting methods.
Advantages of Powder Spray Process
- Durability: Powder coatings provide excellent resistance to abrasion, corrosion, chemicals, and UV radiation, resulting in a long-lasting finish.
- Environmental friendliness: Powder coatings contain no solvents and produce minimal volatile organic compounds (VOCs), making them an eco-friendly alternative to liquid paints.
- Efficiency: Powder coating allows for a thicker, more uniform coating in a single application, reducing the need for multiple coats and minimizing waste.
- Cost-effectiveness: The powder spray process requires less energy and materials compared to liquid painting, resulting in lower overall costs.
- Versatility: Powder coatings can be applied to a wide range of materials, including metals, plastics, and composites, and are available in a variety of colors, textures, and finishes.
The Powder Spray Process Steps
The typical powder spray process consists of several key steps, which are outlined below:
1. Surface Preparation
Before applying the powder coating, the substrate surface must be properly prepared to ensure optimal adhesion and finish quality. The surface preparation steps include:
Cleaning
The substrate is thoroughly cleaned to remove dirt, oil, grease, and other contaminants that may interfere with the coating’s adhesion. Common cleaning methods include:
- Solvent cleaning: Using solvents like acetone or alcohol to dissolve and remove contaminants.
- Alkaline cleaning: Employing alkaline solutions to emulsify and remove stubborn contaminants.
- Mechanical cleaning: Utilizing abrasive methods like sandblasting or shot blasting to remove surface imperfections and create a rougher surface profile for better adhesion.
Pretreatment
After cleaning, the substrate may undergo a pretreatment process to enhance the coating’s adhesion and corrosion resistance. Common pretreatment methods include:
- Phosphating: Applying a thin layer of zinc or iron phosphate to the surface to improve adhesion and corrosion resistance.
- Chromating: Using chromate solutions to create a protective layer on the surface, particularly for aluminum substrates.
Drying
Once the surface is cleaned and pretreated, it must be thoroughly dried to remove any moisture that may affect the powder coating’s application and adherence.
2. Powder Application
The powder coating is applied to the prepared substrate using an electrostatic spray gun. The application process involves:
Electrostatic Charging
The powder particles are negatively charged as they pass through the spray gun, while the substrate is grounded or positively charged. This creates an electrostatic attraction between the powder and the substrate, allowing the powder to adhere to the surface.
Spraying Technique
The operator manipulates the spray gun to apply an even layer of powder across the substrate’s surface. Factors such as gun distance, velocity, and pattern are adjusted to achieve the desired coating thickness and uniformity.
Film Build Control
The powder coating thickness, or film build, is carefully controlled to ensure optimal performance and appearance. Common film thickness ranges from 1.8 to 3 mils (45 to 75 microns) for most applications.
3. Curing
After the powder coating is applied, the substrate is placed in a curing oven to melt and crosslink the powder particles, creating a smooth, durable finish. The curing process involves:
Oven Types
Convection ovens are the most common type used for powder coating curing. These ovens circulate hot air around the substrate to evenly heat and cure the coating. Other oven types, such as infrared or UV ovens, may be used for specialized applications.
Curing Temperature and Time
The curing temperature and time depend on the specific powder coating formulation and substrate material. Typical curing temperatures range from 350°F to 400°F (175°C to 205°C), with curing times of 10 to 20 minutes. Proper curing is critical to achieve optimal coating properties and adhesion.
4. Cooling and Inspection
After curing, the coated substrate is allowed to cool to room temperature before undergoing final inspection.
Cooling
The substrate is typically cooled in a controlled environment to prevent thermal shock and ensure a consistent finish.
Inspection
The finished product is visually inspected for defects such as orange peel, pinholes, or incomplete coverage. Additional tests, such as adhesion, thickness, and gloss measurements, may be performed to ensure the coating meets the required specifications.
Powder Coating Formulations
Powder coatings are formulated using a combination of resins, pigments, fillers, and additives to achieve the desired properties and appearance. The two main types of powder coating formulations are:
Thermoset Powders
Thermoset powders, such as epoxy, polyester, and acrylic, undergo an irreversible chemical reaction during the curing process, creating a highly cross-linked, durable finish. These powders offer excellent mechanical properties, chemical resistance, and heat stability.
Thermoplastic Powders
Thermoplastic powders, such as nylon, polyethylene, and PVC, melt and flow during the curing process but do not undergo a chemical reaction. These powders can be remelted and reshaped, making them suitable for applications requiring flexibility or post-forming.
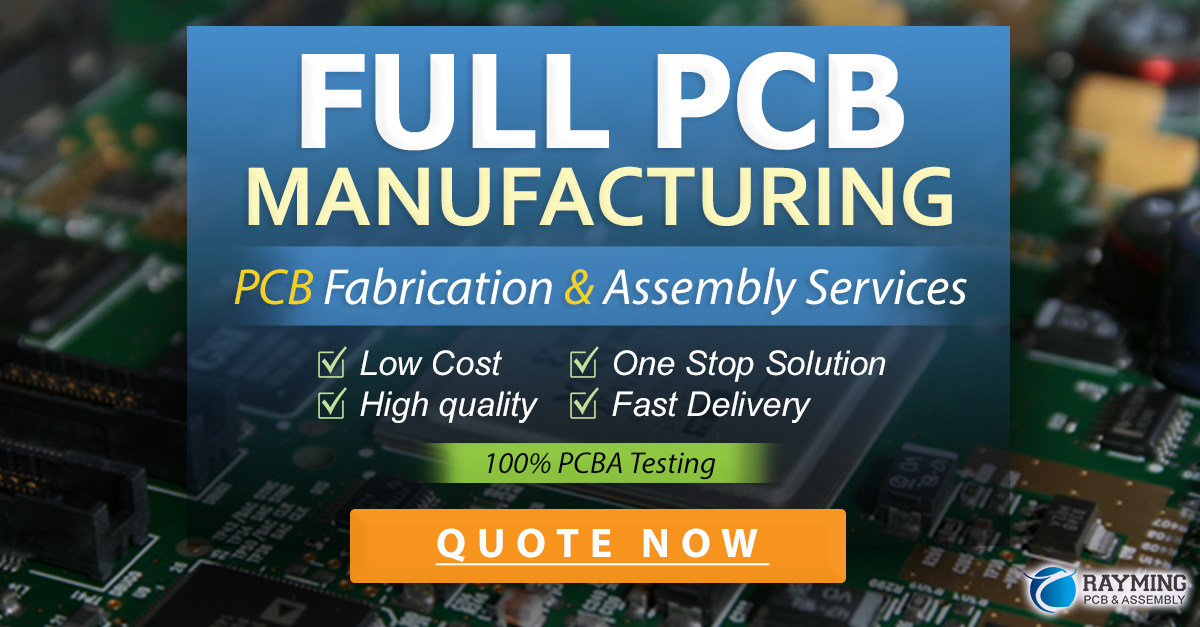
Powder Coating Equipment
The powder spray process requires specialized equipment to ensure efficient and consistent application. Key equipment components include:
Powder Spray Guns
Electrostatic powder spray guns are designed to charge and dispense the powder coating onto the substrate. There are two main types of spray guns:
- Corona guns: These guns use a high-voltage electrode to charge the powder particles as they pass through the gun’s nozzle.
- Tribo guns: These guns charge the powder particles through friction as they pass through a specially designed nozzle.
Powder Pumps and Hoppers
Powder pumps are used to transport the powder from the hopper, where it is stored, to the spray gun. The hopper is a container that holds the powder and feeds it into the pump.
Powder Booths
Powder coating is typically performed in enclosed booths to contain overspray and facilitate powder recovery. There are two main types of powder booths:
- Cartridge booth: These booths use replaceable cartridge filters to capture overspray and allow clean air to be exhausted.
- Cyclone booth: These booths employ a cyclonic air flow to separate the overspray from the air, allowing the powder to be collected for reuse.
Curing Ovens
As mentioned earlier, curing ovens are used to melt and crosslink the powder coating, creating a durable finish. Convection ovens are the most common type, but infrared and UV ovens may be used for specific applications.
Powder Coating Applications
Powder coating is used in a wide range of industries and applications, including:
Automotive Components
Powder coating is extensively used in the automotive industry for coating wheels, bumpers, engine components, and interior parts. It provides excellent durability, corrosion resistance, and aesthetic appeal.
Architectural Products
Powder coating is widely used for coating aluminum extrusions, window frames, door handles, and other architectural components. It offers superior weatherability and color retention compared to liquid paints.
Appliances and Electronics
Powder coating is used to coat household appliances, such as refrigerators, washing machines, and ovens, as well as electronic enclosures and components. It provides a durable, attractive finish that resists wear and corrosion.
Furniture and Lighting
Powder coating is used to coat metal furniture, such as chairs, tables, and shelving, as well as lighting fixtures and components. It offers a wide range of color and texture options, as well as excellent durability and resistance to chipping and scratching.
Agricultural and Construction Equipment
Powder coating is used to protect and enhance the appearance of agricultural and construction equipment, such as tractors, excavators, and scaffolding. It provides superior resistance to abrasion, corrosion, and UV exposure in harsh outdoor environments.
Frequently Asked Questions (FAQ)
1. What are the main advantages of powder coating over liquid painting?
Powder coating offers several advantages over liquid painting, including:
- Superior durability and resistance to abrasion, corrosion, and chemicals
- Eco-friendliness, with minimal VOC emissions and waste
- Thicker, more uniform coatings in a single application
- Lower overall costs due to reduced material and energy consumption
- Wide range of colors, textures, and finishes
2. Can powder coating be applied to non-metal substrates?
Yes, powder coating can be applied to various non-metal substrates, such as plastics, composites, and MDF (medium-density fiberboard). However, these substrates may require specialized pretreatment processes or conductive primers to ensure proper adhesion and coverage.
3. How does the curing process affect the final powder coating properties?
The curing process is critical to achieving optimal powder coating properties. Proper curing temperature and time ensure that the powder particles melt, flow, and crosslink to form a smooth, durable finish. Under-curing can result in poor adhesion, while over-curing can lead to coating degradation and discoloration.
4. What factors influence the choice between thermoset and thermoplastic powder coatings?
The choice between thermoset and thermoplastic powder coatings depends on the specific application requirements. Thermoset powders are preferred for applications demanding high mechanical strength, chemical resistance, and heat stability. Thermoplastic powders are suitable for applications requiring flexibility, impact resistance, or post-forming capabilities.
5. How can powder coating defects be prevented or minimized?
To prevent or minimize powder coating defects, consider the following best practices:
- Ensure thorough surface preparation, including cleaning and pretreatment
- Maintain consistent powder application parameters, such as gun settings and booth conditions
- Control the curing process, ensuring proper temperature and time
- Regularly maintain and calibrate powder coating equipment
- Use high-quality, compatible powder coatings and substrates
Conclusion
The powder spray process is a versatile and efficient method for applying protective and decorative coatings to a wide range of products and components. By understanding the key steps, equipment, and formulations involved in the process, manufacturers can optimize their powder coating operations to achieve superior results. As industries continue to prioritize sustainability and performance, the demand for powder coating is expected to grow, driving further advancements in technology and application techniques.
Powder Coating Process Step | Key Actions |
---|---|
Surface Preparation | Cleaning, Pretreatment, Drying |
Powder Application | Electrostatic Charging, Spraying Technique, Film Build Control |
Curing | Oven Type Selection, Temperature and Time Control |
Cooling and Inspection | Controlled Cooling, Visual and Quantitative Inspection |
Powder Coating Formulation | Characteristics |
---|---|
Thermoset Powders | Epoxy, Polyester, Acrylic; Highly cross-linked, Durable |
Thermoplastic Powders | Nylon, Polyethylene, PVC; Melt and flow, Flexible, Post-formable |
By adhering to best practices and leveraging the advantages of powder coating, manufacturers can produce high-quality, long-lasting finishes that meet the demanding requirements of various industries and applications.
Leave a Reply