When machining metal parts, holes are often drilled and then threaded with taps to create internal threads so that screws or bolts can be used to fasten parts together. Blind holes are holes that do not pass fully through the workpiece. Determining the appropriate tap depth is important for blind holes so that the tap reaches the full depth of the hole without extending beyond the bottom. In this article, we will examine how to calculate and set the correct tap depth for blind holes.
How to Determine Tap Depth for Blind Holes
There are a few key factors to consider when determining the appropriate depth to tap a blind hole:
Drilled Hole Depth
The depth of the drilled hole sets the maximum depth for tapping. For blind holes, the tap should not extend beyond the depth of the hole.
Allowance for Chips
When tapping, the teeth of the tap cut chips out of the hole to form threads. This causes the tap to extend slightly further into the hole than just the depth of the threads themselves. A typical allowance is 5-10% of the thread depth.
Thread Depth
The required threaded depth depends on the application and fastener size. Typical thread depths range from 1-1 1⁄2 times the fastener diameter.
Chamfer/Lead Depth
Most taps have a chamfer or lead-in at the tip. This non-threaded length at the start of the tap must also be allowed for. A typical chamfer is 1-3 thread pitches long.
Taking all of these factors into account, the tap depth can be calculated as:
Tap Depth = Drilled Hole Depth – Allowance for Chips – Thread Depth – Chamfer/Lead Depth
Let’s look at an example to demonstrate calculating tap depth for a blind hole.
Calculating Tap Depth Example
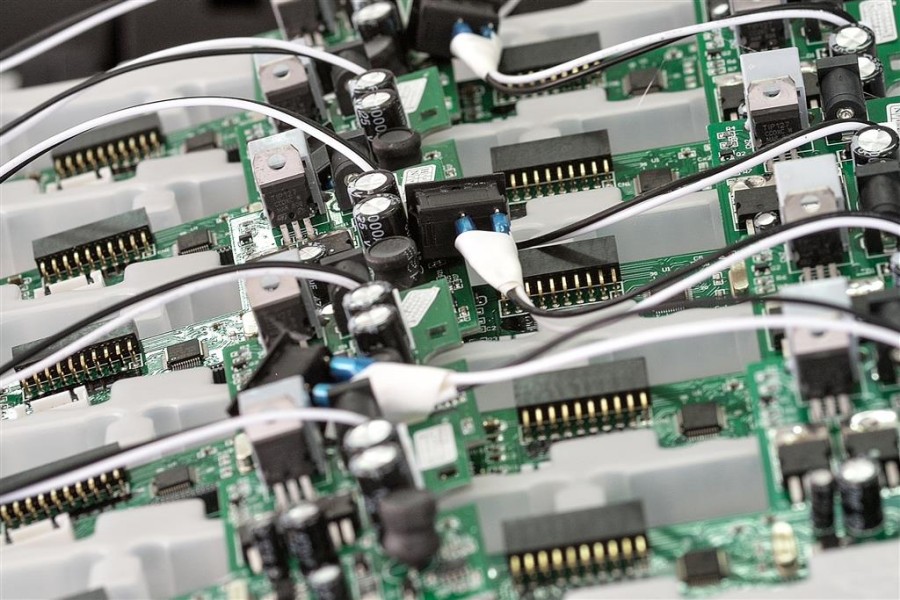
Say we have a 0.5 inch diameter blind hole drilled 1 inch deep in some steel that needs to be tapped for a 1/4-20 thread to attach a bracket.
- Drilled Hole Depth: 1 in
- Allowance for Chips: 0.05 in (0.1 in thread depth * 10% allowance)
- Thread Depth: 0.25 in (~1.5x screw diameter)
- Chamfer Depth: 0.05 in (0.05 in * 1 thread pitch of 20 TPI)
Plugging this into our tap depth formula:
Tap Depth = 1 in – 0.05 in – 0.25 in – 0.05 in = 0.65 in
So for this example hole, the tap should be set to extend 0.65 inches deep into the hole to reach the full thread depth without hitting the bottom.
Setting Tap Depth
There are two main ways to set the tap depth when tapping blind holes:
1. Tap Depth Stop
A tap depth stop can be attached to the tap or tap holder. This mechanical stop controls how far the tap can extend. The stop is set to the calculated tap depth distance. Depth stops are commonly used with drill presses, tapping heads, or tap handles.
2. Drill Press Depth Stop
For tapping blind holes on a drill press, the depth stop of the drill press can be used instead of a tap depth stop. The quill travel is limited by setting the depth stop to the tap depth distance. This method works well for occasional tapping in a machine shop.
Key Factors in Determining Tap Depth
To recap, the key factors that go into determining the appropriate tap depth for blind holes are:
- Drilled Hole Depth – The maximum depth the tap can extend
- Allowance for Chips – Extra depth for tap teeth to clear chips, typically 5-10% of thread depth
- Thread Depth – Required thread length based on fastener size, typically 1-1 1/2 times fastener diameter
- Chamfer/Lead Depth – Length of the chamfer or lead-in at the start of the tap, usually 1-3 thread pitches
Carefully calculating the tap depth and setting depth stops prevents the tap from extending too far into blind holes. This avoids damage to the tap and ensures full thread depth for secure fastener connections. Understanding proper tap depth helps machinists efficiently tap strong internal threads in blind hole applications.
Common Questions About Tap Depths for Blind Holes
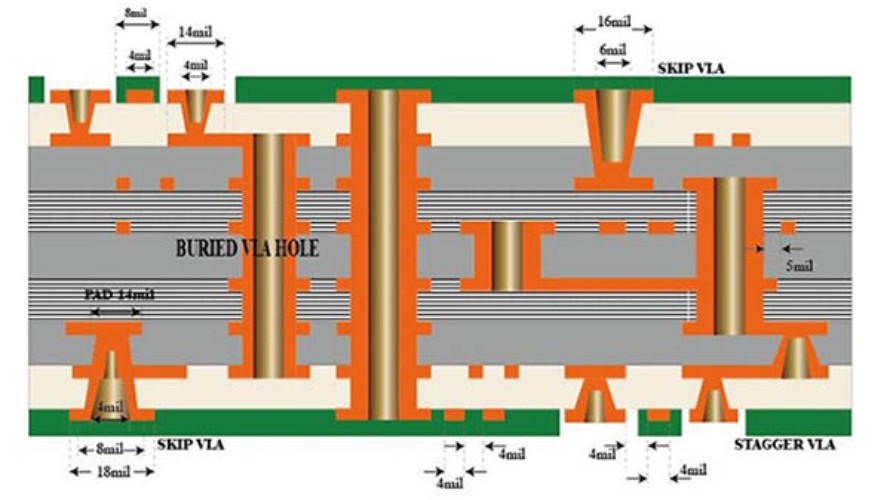
What happens if a blind hole is tapped too deep?
Tapping a blind hole too deep can result in a few issues:
- The tap teeth may jam at the bottom and break off in the hole. Broken taps can be difficult to remove.
- Without chip clearance, the excess chips may get compressed at the hole bottom. This can degrade thread quality.
- The threads at the end of the hole may not form properly if the tap goes beyond the drilled depth.
- Backing the tap out after going too deep can damage the newly formed threads.
How much extra hole depth is needed for through holes?
For through holes that pass completely through the workpiece, extra depth is needed for chip clearance. Typically an extra 10-20% of the hole diameter is added to the hole depth. This allows chips to freely eject from the hole without jamming.
Should any oil/lubricant be used when tapping blind holes?
Yes, a tapping fluid or light machine oil should still be applied before tapping blind holes. Proper lubrication reduces friction, cuts down on built-up heat, and helps flush out chips from the hole. For blind hole tapping, a thicker fluid helps carry chips out of the hole as the tap retracts.
What’s the best tap style for tapping deep blind holes?
For deep blind holes, a spiral point or spiral fluted tap often works best. The spiral flutes provide excellent chip evacuation that helps prevent chip jams in deep holes. The spiral point design also reduces thrust and torque required compared to a standard tap.
How do you clear chips when tapping a blind hole?
Frequently retracting the tap allows chips to clear from blind holes. A smooth reciprocating motion lets chips fall free from the flutes. High pressure air can be blown into the hole to help eject chips. Guide bushings can help align small taps for easy retraction. Large deep holes may require special chip evacuation systems.
Can coolant be used when tapping blind holes?
Yes, coolant or cutting fluid can help with chip evacuation and cooling when tapping blind holes. The fluid should be delivered at low pressure into the top of the hole. Too high pressure can force chips to pack at the hole bottom. Low pressure delivery is ideal for getting fluid into the hole while allowing chips to come out.
Conclusion
Determining the correct tap depth is important when tapping blind holes to ensure full thread depth and prevent tap breakage at the bottom of the hole. The depth is calculated from the drilled hole depth, accounting for allowances for chips, thread depth, and chamfer/lead in length. Setting tap stops or drill press depth stops at the calculated depth allows for accurately tapping blind holes repeatedly. Understanding proper tap depth setup helps machinists reliably tap strong internal threads in blind hole applications.
Leave a Reply