How Pre-heaters Work
Pre-heaters work by transferring heat from a heating medium, such as steam, hot water, or hot oil, to the substance that needs to be heated. The heating medium and the substance to be heated are separated by a heat exchange surface, which allows heat to be transferred from the medium to the substance without direct contact.
There are several types of pre-heaters, each designed to suit specific applications and requirements. Some common types of pre-heaters include:
1. Shell and Tube Pre-heaters
Shell and tube pre-heaters consist of a bundle of tubes enclosed within a shell. The substance to be heated flows through the tubes, while the heating medium flows through the shell, surrounding the tubes. Heat is transferred from the medium to the substance through the walls of the tubes.
2. Plate Heat Exchangers
Plate heat exchangers consist of a series of thin, corrugated metal plates stacked together. The substance to be heated and the heating medium flow through alternate channels between the plates, allowing heat to be transferred from the medium to the substance.
3. Electric Pre-heaters
Electric pre-heaters use electric heating elements to heat the substance directly. They are typically used in applications where precise temperature control is required, or where the use of a heating medium is not practical.
Benefits of Using Pre-heaters
Using pre-heaters in industrial processes offers several benefits, including:
1. Improved Process Efficiency
By preheating the substance before it enters the main processing unit, pre-heaters ensure that the substance is at the optimal temperature for the intended process. This reduces the amount of energy required to bring the substance up to the desired temperature, resulting in improved process efficiency and reduced energy costs.
2. Enhanced Product Quality
Pre-heaters help to maintain consistent temperatures throughout the manufacturing process, which is essential for ensuring product quality. By preheating the substance to the correct temperature, pre-heaters help to minimize temperature fluctuations that can lead to variations in product quality.
3. Increased Equipment Lifespan
Pre-heaters help to reduce thermal stress on process equipment by ensuring that the substance enters the equipment at the correct temperature. This reduces the risk of thermal shock and other temperature-related damage, which can extend the lifespan of the equipment.
Applications of Pre-heaters
Pre-heaters are used in a wide range of industrial processes, including:
1. Food and Beverage Processing
In the food and beverage industry, pre-heaters are used to heat ingredients before they are processed. For example, in the production of dairy products, milk is preheated before it is pasteurized to ensure that it reaches the correct temperature for the pasteurization process.
2. Chemical Processing
In the chemical industry, pre-heaters are used to heat reactants before they enter a chemical reactor. By preheating the reactants, pre-heaters help to ensure that the reaction occurs at the optimal temperature, resulting in improved reaction rates and product yields.
3. Oil and Gas Processing
In the oil and gas industry, pre-heaters are used to heat crude oil before it is refined. Preheating the crude oil reduces its viscosity, making it easier to pump and process. Pre-heaters are also used to heat natural gas before it is processed to remove impurities and moisture.
4. Power Generation
In power generation plants, pre-heaters are used to heat water before it enters a boiler. By preheating the water, pre-heaters help to improve the efficiency of the boiler, reducing fuel consumption and emissions.
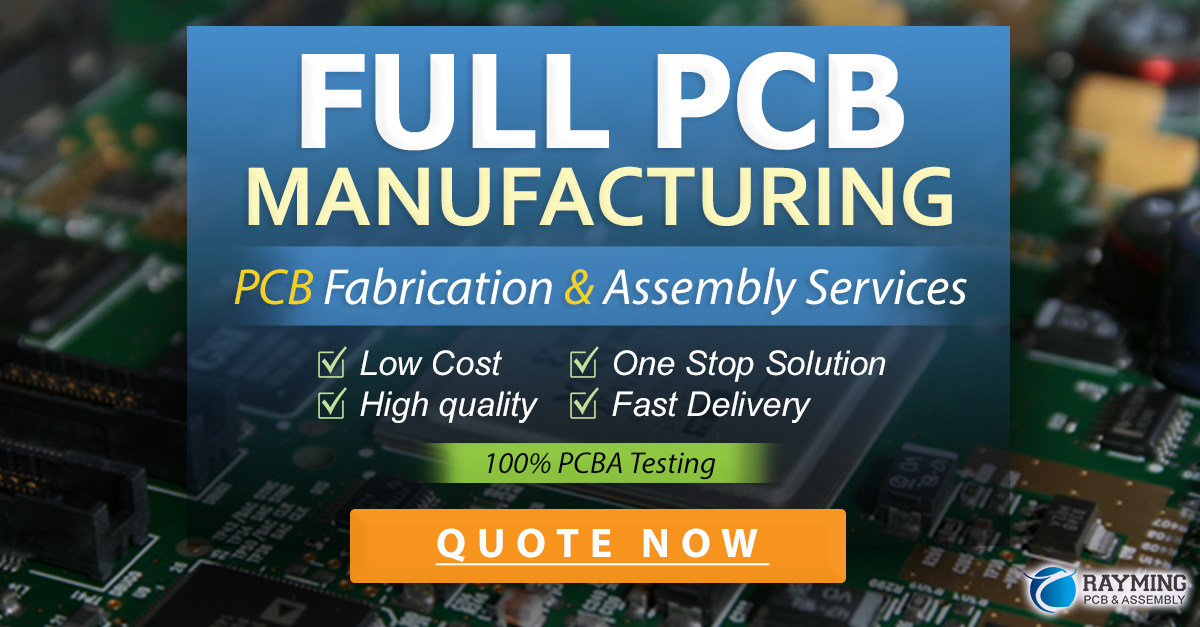
Factors to Consider When Selecting a Pre-heater
When selecting a pre-heater for a specific application, several factors need to be considered, including:
1. Heat Transfer Requirements
The heat transfer requirements of the application will determine the type and size of pre-heater required. Factors to consider include the temperature range, heat transfer rate, and the properties of the substance to be heated.
2. Material Compatibility
The materials used in the construction of the pre-heater must be compatible with the substance being heated and the heating medium. This is particularly important in applications where corrosive or abrasive substances are being processed.
3. Pressure and Temperature Ratings
The pre-heater must be designed to withstand the pressure and temperature conditions of the application. This includes the maximum operating pressure and temperature, as well as any fluctuations that may occur during operation.
4. Maintenance and Cleaning Requirements
The pre-heater should be designed to facilitate easy maintenance and cleaning. This includes features such as removable tube bundles or plates, and access points for inspection and cleaning.
Maintenance and Troubleshooting of Pre-heaters
To ensure optimal performance and longevity, pre-heaters require regular maintenance and troubleshooting. Some common maintenance and troubleshooting tasks include:
1. Cleaning
Pre-heaters should be cleaned regularly to remove any fouling or scaling that may occur during operation. Fouling and scaling can reduce heat transfer efficiency and increase pressure drop, leading to reduced performance and increased energy consumption.
2. Inspections
Regular inspections should be carried out to identify any signs of wear, damage, or leaks. This includes inspecting the heat exchange surfaces, gaskets, and seals for signs of deterioration or damage.
3. Calibration
The temperature and pressure sensors used to control the pre-heater should be calibrated regularly to ensure accurate readings. Inaccurate readings can lead to suboptimal performance and increased energy consumption.
4. Troubleshooting
If the pre-heater is not performing as expected, troubleshooting should be carried out to identify the cause of the problem. Common issues include fouling, scaling, leaks, and sensor failures.
Frequently Asked Questions (FAQ)
1. What is the difference between a pre-heater and a heat exchanger?
A pre-heater is a type of heat exchanger that is used to raise the temperature of a substance before it enters the main processing unit. Heat exchangers are a broader category of equipment that includes pre-heaters, as well as other types of equipment used to transfer heat between two or more substances.
2. Can pre-heaters be used for cooling applications?
While pre-heaters are primarily used for heating applications, they can also be used for cooling applications in some cases. In cooling applications, the pre-heater is used to cool the substance before it enters the main processing unit.
3. What is the most common type of pre-heater?
The most common type of pre-heater is the shell and tube pre-heater. Shell and tube pre-heaters are widely used in industrial applications due to their simple design, high heat transfer efficiency, and ability to handle a wide range of substances and operating conditions.
4. How often should pre-heaters be cleaned?
The frequency of cleaning required for a pre-heater depends on the specific application and the properties of the substance being heated. In general, pre-heaters should be cleaned whenever there is a noticeable decrease in performance, or at least once per year.
5. What are the signs that a pre-heater needs to be replaced?
Signs that a pre-heater needs to be replaced include excessive fouling or scaling, leaks, and reduced heat transfer efficiency. If the pre-heater is no longer able to maintain the desired temperature or pressure, or if the cost of maintenance and repairs becomes excessive, it may be time to consider replacing the unit.
Type of Pre-heater | Advantages | Disadvantages |
---|---|---|
Shell and Tube | Simple design, high heat transfer efficiency, wide range of applications | Can be prone to fouling and scaling, may require frequent cleaning |
Plate Heat Exchanger | Compact design, easy to clean, high heat transfer efficiency | Limited pressure and temperature range, may be prone to leaks |
Electric | Precise temperature control, no heating medium required | Limited heat transfer capacity, high operating costs |
In conclusion, pre-heaters are essential components in many industrial processes, providing a means of raising the temperature of a substance before it enters the main processing unit. By ensuring that the substance is at the optimal temperature for the intended process, pre-heaters help to improve process efficiency, enhance product quality, and extend equipment lifespan.
When selecting a pre-heater for a specific application, it is important to consider factors such as heat transfer requirements, material compatibility, pressure and temperature ratings, and maintenance and cleaning requirements. Regular maintenance and troubleshooting are also essential to ensure optimal performance and longevity.
By understanding the function and benefits of pre-heaters, as well as the factors to consider when selecting and maintaining them, industrial manufacturers can optimize their processes and achieve better results.
Leave a Reply