Introduction to Countersinks and Counterbores in PCBs
When designing and manufacturing printed circuit boards (PCBs), it is crucial to understand the various drilling techniques used to create holes for component mounting and interconnections. Two common methods are countersinking and counterboring. Although these terms are often used interchangeably, they refer to distinct processes with specific applications in PCB fabrication.
In this article, we will explore the differences between countersinks and counterbores in PCBs, their purposes, and when to use each technique. By understanding these concepts, PCB designers and manufacturers can make informed decisions to optimize the functionality, reliability, and aesthetics of their boards.
What is a Countersink in PCBs?
Definition and Purpose
A countersink is a conical-shaped recess created at the top of a drilled hole in a PCB. The primary purpose of a countersink is to allow the head of a flathead screw or bolt to sit flush with or below the surface of the board. This technique is commonly used when mounting components or securing the PCB to an enclosure.
Countersink Angle and Depth
Countersinks are typically created using a drill bit with a specific angle, usually ranging from 82° to 90°. The most common angles are:
Angle | Application |
---|---|
82° | Flathead screws |
90° | Flush mounting |
The depth of the countersink depends on the size of the screw head and the thickness of the PCB. It is essential to calculate the appropriate depth to ensure a proper fit without compromising the structural integrity of the board.
Advantages of Countersinking
- Allows for flush mounting of components and hardware
- Provides a clean and professional appearance
- Reduces the risk of snagging or damaging components during handling
- Improves the overall mechanical stability of the PCB Assembly
What is a Counterbore in PCBs?
Definition and Purpose
A counterbore is a cylindrical recess created at the top of a drilled hole in a PCB, with a diameter larger than the hole itself. The primary purpose of a counterbore is to create a flat-bottomed recess that allows the head of a socket head cap screw or other hardware to sit flush with the surface of the board. Counterbores are often used when a deeper recess is required, or when using hardware with a larger head diameter.
Counterbore Diameter and Depth
The diameter of a counterbore is typically larger than the diameter of the screw head, allowing for some clearance. The depth of the counterbore depends on the height of the screw head and the thickness of the PCB. It is crucial to ensure that the counterbore depth is sufficient to accommodate the hardware without piercing through the other side of the board.
Advantages of Counterboring
- Accommodates hardware with larger head diameters
- Provides a flat surface for secure mounting
- Allows for the use of socket head cap screws, which have a higher tensile strength than flathead screws
- Offers increased mechanical stability for heavier components or high-stress applications
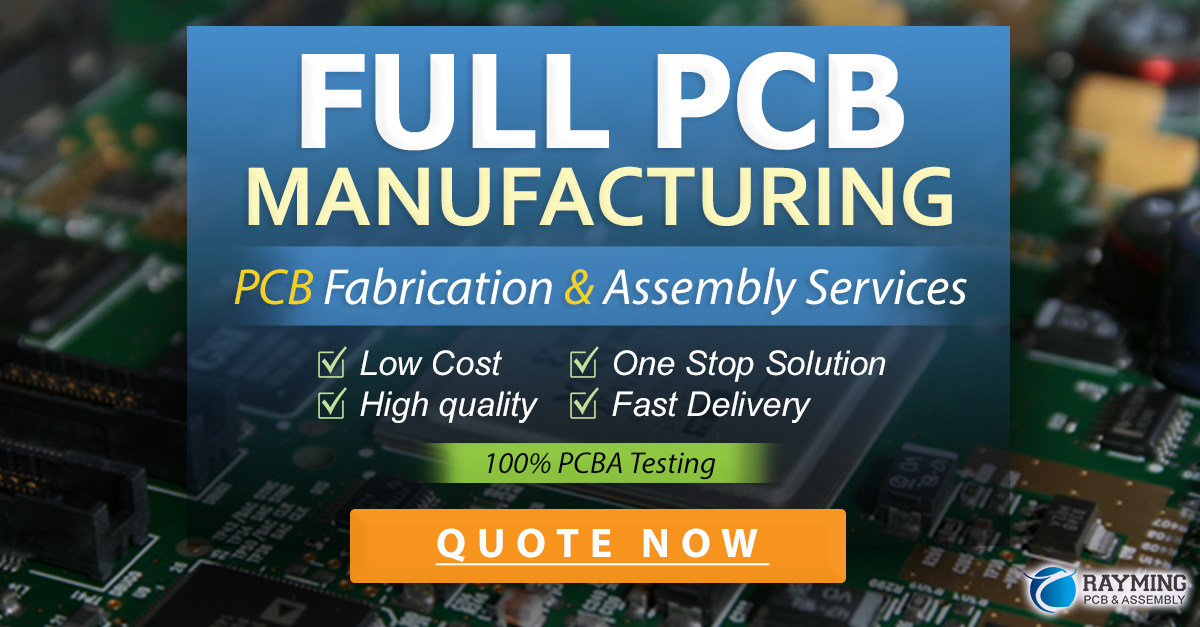
Countersink vs. Counterbore: Key Differences
Hole Geometry
The primary difference between a countersink and a counterbore lies in their hole geometry. A countersink features a conical recess, while a counterbore has a cylindrical recess with a flat bottom. This difference in shape affects the type of hardware that can be used and the overall appearance of the PCB assembly.
Hardware Compatibility
Countersinks are designed to accommodate flathead screws, which have a conical head that matches the angle of the countersink. Counterbores, on the other hand, are compatible with socket head cap screws and other hardware with cylindrical heads. The choice between a countersink and a counterbore often depends on the specific hardware requirements of the PCB assembly.
Application Differences
Countersinks are commonly used in applications where a flush or low-profile mounting is desired, such as in consumer electronics or when space is limited. Counterbores are often employed in industrial or high-reliability applications, where stronger hardware and a more secure mounting are required.
Choosing Between a Countersink and a Counterbore
When deciding whether to use a countersink or a counterbore in your PCB design, consider the following factors:
-
Component requirements: Evaluate the mounting needs of the components and hardware used in your PCB assembly. Some components may require specific screw types or head sizes, which will dictate the choice between a countersink and a counterbore.
-
Mechanical strength: Assess the mechanical stresses that the PCB will be subjected to during operation. If high tensile strength is required, a counterbore with socket head cap screws may be the better option. For less demanding applications, a countersink with flathead screws may suffice.
-
PCB Thickness: Consider the thickness of your PCB when selecting the appropriate drilling technique. Thinner boards may not have sufficient depth to accommodate a counterbore, making a countersink the more suitable choice.
-
Aesthetic considerations: In applications where the appearance of the PCB is important, such as in consumer products, countersinks may provide a cleaner and more streamlined look. Counterbores, while functional, may be less visually appealing.
Best Practices for Implementing Countersinks and Counterbores
To ensure the success of your PCB design and manufacturing process, follow these best practices when implementing countersinks and counterbores:
-
Adhere to manufacturer specifications: Always refer to the manufacturer’s datasheets and guidelines for the specific components and hardware you are using. Follow their recommendations for hole sizes, screw types, and mounting requirements.
-
Use appropriate drill bits: Select drill bits that are designed for creating countersinks or counterbores, with the correct angles and diameters. Using the wrong drill bit can result in an improper fit or damage to the PCB.
-
Minimize the risk of breakout: When drilling countersinks or counterbores, be cautious not to penetrate through the other side of the PCB. Breakout can weaken the board and lead to mechanical failure. Use controlled depth drilling techniques and verify the PCB thickness to prevent this issue.
-
Consider the impact on signal integrity: The presence of countersinks or counterbores can affect the signal integrity of the PCB, particularly in high-frequency applications. Evaluate the potential impact of these features on your circuit’s performance and make appropriate design adjustments if necessary.
-
Communicate clearly with your manufacturer: When submitting your PCB design for fabrication, provide clear instructions and specifications regarding countersinks and counterbores. Include detailed drawings, dimensions, and any specific requirements to ensure that the manufacturer understands your needs.
FAQ
1. Can countersinks and counterbores be used together in the same PCB?
Yes, countersinks and counterbores can be used together in the same PCB design. The choice between the two depends on the specific requirements of each component and mounting location.
2. Are there any limitations on the size of countersinks or counterbores in PCBs?
The size of countersinks and counterbores is limited by the thickness of the PCB and the diameter of the drilled hole. It is essential to ensure that the depth of the countersink or counterbore does not exceed the thickness of the board, and that the diameter is appropriate for the size of the hardware being used.
3. How do countersinks and counterbores affect the cost of PCB fabrication?
Implementing countersinks and counterbores may increase the cost of PCB fabrication, as they require additional drilling operations and may necessitate the use of specialized drill bits. However, the cost impact is typically minor compared to the overall benefits of using these techniques for component mounting and mechanical stability.
4. Can countersinks and counterbores be used in multilayer PCBs?
Yes, countersinks and counterbores can be used in multilayer PCBs. However, it is important to consider the layer stack-up and ensure that the depth of the countersink or counterbore does not interfere with the internal layers or compromise the structural integrity of the board.
5. Are there any automated design tools that can help with creating countersinks and counterbores in PCB layouts?
Many PCB Design Software packages include tools for automatically creating countersinks and counterbores based on user-defined parameters. These tools can help streamline the design process and ensure consistency across the board. However, it is still important for designers to review and verify the generated features to ensure they meet the specific requirements of the project.
Conclusion
Understanding the difference between countersinks and counterbores is essential for creating reliable and efficient PCB designs. By selecting the appropriate technique for each component and mounting requirement, designers can optimize the mechanical stability, signal integrity, and overall performance of their PCB assemblies.
When implementing countersinks and counterbores, it is crucial to adhere to manufacturer guidelines, use the correct drill bits, and carefully consider the impact on PCB thickness and signal integrity. By following best practices and clearly communicating with manufacturers, PCB designers can ensure that their boards are fabricated to the highest standards of quality and reliability.
As PCB technology continues to evolve, the importance of proper hole preparation techniques, such as countersinking and counterboring, will only grow. By staying informed and adapting to new challenges, PCB designers and manufacturers can continue to push the boundaries of innovation and create cutting-edge electronic devices that meet the ever-increasing demands of the industry.
Leave a Reply