What is a Core PCB?
A core PCB, also known as the substrate or base material, is the insulating layer that forms the backbone of a printed circuit board. It is typically made of a dielectric material, such as FR-4 (a glass-reinforced epoxy laminate), which provides electrical insulation and mechanical support for the copper traces, components, and other features of the PCB.
The core PCB can be a single layer or multiple layers, depending on the complexity and requirements of the circuit design. In multi-layer PCBs, the core layers are sandwiched between additional layers of prepreg (pre-impregnated fiberglass) and copper foil to create a complete stackup.
Functions of the Core PCB
The core PCB serves several important functions in a printed circuit board:
-
Mechanical support: The core provides a stable and rigid foundation for the PCB, ensuring that the board maintains its shape and integrity during manufacturing, assembly, and use.
-
Electrical insulation: The dielectric material of the core PCB acts as an insulator, preventing short circuits and unintended electrical connections between different layers and components of the board.
-
Thermal management: The core PCB plays a role in dissipating heat generated by the components and traces on the board. The thermal properties of the core material can affect the overall thermal performance of the PCB.
-
Signal integrity: The core material’s dielectric constant and loss tangent can impact the signal integrity of high-speed circuits. Choosing the right core material is crucial for maintaining signal quality and minimizing signal distortion.
Common Core PCB Materials
There are several materials commonly used for core PCBs, each with its own set of properties and advantages:
Material | Description | Advantages |
---|---|---|
FR-4 | Glass-reinforced epoxy laminate | Low cost, good mechanical strength, suitable for most applications |
High Tg FR-4 | FR-4 with higher glass transition temperature | Improved thermal stability, better performance in high-temperature environments |
Polyimide | High-performance polymer | Excellent thermal and chemical resistance, suitable for harsh environments |
Rogers | High-frequency laminates | Low dielectric constant and loss tangent, ideal for RF and microwave applications |
Aluminum | Metal-based PCB | Excellent thermal conductivity, used for high-power and heat-sensitive applications |
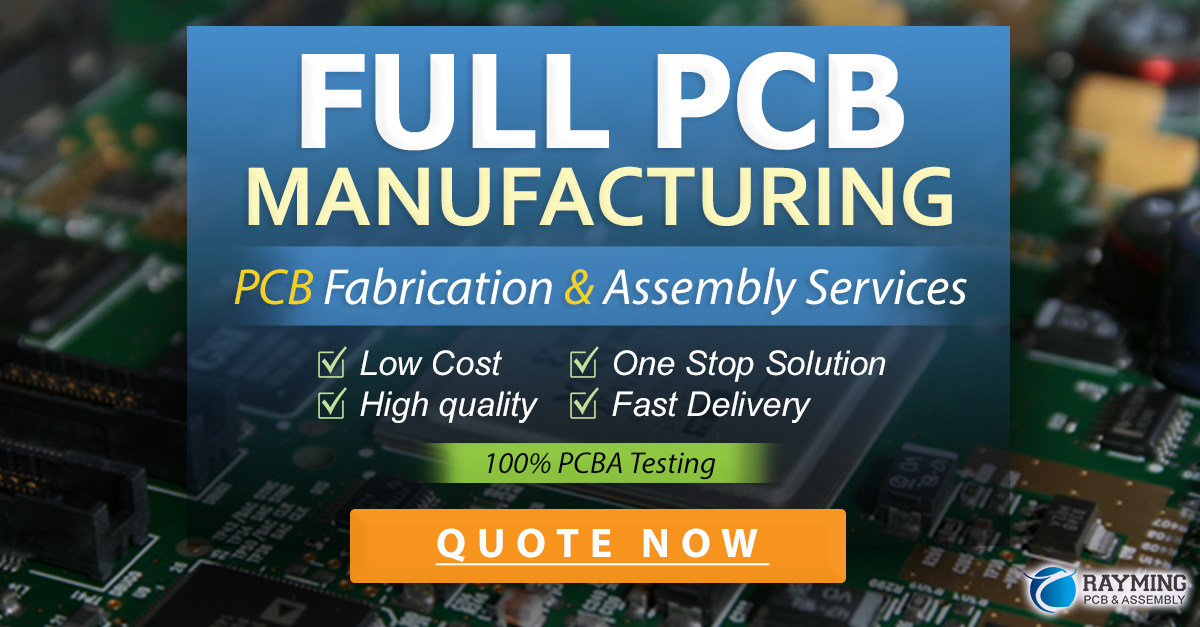
Factors to Consider When Choosing a Core PCB Material
When selecting a core PCB material, several factors should be considered:
-
Electrical properties: The dielectric constant, loss tangent, and breakdown voltage of the material should be appropriate for the intended application and signal requirements.
-
Thermal properties: The thermal conductivity and glass transition temperature (Tg) of the material should be suitable for the expected operating temperature range and power dissipation of the PCB.
-
Mechanical properties: The material’s strength, stiffness, and dimensional stability should be adequate to withstand the mechanical stresses encountered during manufacturing, assembly, and use.
-
Cost: The cost of the core material should be balanced against the required performance and reliability of the PCB.
-
Manufacturability: The chosen material should be compatible with the PCB manufacturing processes, such as drilling, etching, and lamination.
Core PCB Thickness
The thickness of the core PCB is another important consideration in PCB design. The core thickness can affect the mechanical strength, signal integrity, and thermal management of the board.
Common core thicknesses for FR-4 PCBs include:
- 0.005″ (0.13 mm)
- 0.010″ (0.25 mm)
- 0.020″ (0.51 mm)
- 0.030″ (0.76 mm)
- 0.060″ (1.57 mm)
Thicker cores provide greater mechanical stability and better thermal performance but may increase the overall thickness and weight of the PCB. Thinner cores allow for more compact designs and better signal integrity but may be more susceptible to warping and mechanical stress.
Core PCB in Multi-Layer Boards
In multi-layer PCBs, the core layers form the foundation of the stackup, with additional layers of prepreg and copper foil added to create the complete board.
A typical 4-layer PCB Stackup might consist of:
- Top copper layer
- Prepreg
- Core (with embedded copper layers)
- Prepreg
- Bottom copper layer
The number and arrangement of layers in a multi-layer PCB depend on the complexity of the circuit, the signal and power requirements, and the desired performance characteristics.
PCB Core vs. Prepreg
While the core PCB and prepreg are both essential components of a multi-layer PCB, they serve different purposes:
-
Core PCB: The core is a fully cured, rigid material that provides the main structural support for the PCB. It has a fixed thickness and contains embedded copper layers.
-
Prepreg: Prepreg is a partially cured, malleable material that is used to bond the core and copper layers together during the lamination process. It flows and fills in gaps, creating a solid bond between layers. Prepreg does not contain embedded copper.
Challenges in Core PCB Design and Manufacturing
Designing and manufacturing PCBs with core materials can present several challenges:
-
Warping: Thin cores or unbalanced Copper Distribution can lead to warping of the PCB during manufacturing, which can cause issues with component assembly and reliability.
-
Drilling: Thick cores or hard materials can make drilling more difficult, requiring specialized drill bits and careful process control to avoid damage or inaccuracies.
-
Impedance control: Maintaining consistent impedance in high-speed designs can be challenging, requiring careful selection of core materials and precise control of trace geometries and spacing.
-
Thermal management: Dissipating heat effectively from high-power components can be difficult, requiring the use of thermal vias, heat sinks, or specialized core materials with high thermal conductivity.
FAQ
1. What is the most common material used for core PCBs?
FR-4, a glass-reinforced epoxy laminate, is the most widely used core material for PCBs due to its low cost, good mechanical strength, and suitability for a wide range of applications.
2. Can a PCB have multiple core layers?
Yes, multi-layer PCBs can have multiple core layers, depending on the complexity and requirements of the circuit design. The core layers are typically sandwiched between layers of prepreg and copper foil to create the complete stackup.
3. How does the core material affect signal integrity?
The dielectric constant and loss tangent of the core material can impact signal integrity, particularly in high-speed circuits. Materials with lower dielectric constants and loss tangents, such as Rogers laminates, are often used for RF and microwave applications to minimize signal distortion.
4. What factors should be considered when choosing a core PCB thickness?
When selecting a core PCB thickness, consider the mechanical strength, signal integrity, and thermal management requirements of the board. Thicker cores provide better mechanical stability and thermal performance, while thinner cores allow for more compact designs and better signal integrity.
5. How does the core PCB differ from prepreg in a multi-layer board?
The core PCB is a fully cured, rigid material that provides the main structural support for the PCB and contains embedded copper layers. Prepreg, on the other hand, is a partially cured, malleable material used to bond the core and copper layers together during lamination and does not contain embedded copper.
Conclusion
The core PCB is the foundation of a printed circuit board, providing mechanical support, electrical insulation, thermal management, and signal integrity. Understanding the properties and functions of the core material is crucial for designing, manufacturing, and assembling high-quality, reliable PCBs.
When selecting a core PCB material and thickness, it is essential to consider the electrical, thermal, mechanical, and cost requirements of the application. Common core materials include FR-4, high Tg FR-4, polyimide, Rogers laminates, and aluminum, each with its own set of advantages and drawbacks.
In multi-layer PCBs, the core layers work in conjunction with prepreg and additional copper layers to create a complete stackup that meets the needs of the circuit design. Designers and manufacturers must carefully balance the challenges of warping, drilling, impedance control, and thermal management to ensure the success of the final product.
By understanding the core PCB and its role in the overall performance and reliability of a printed circuit board, engineers and technicians can make informed decisions throughout the design and manufacturing process, ultimately leading to better, more reliable electronic devices.
Leave a Reply