Introduction to LED PCB
An LED PCB, or Light Emitting Diode Printed Circuit Board, is a specialized type of circuit board designed to support and control LED lights. These boards are essential components in various applications, from simple indicator lights to complex LED displays and lighting systems. LED PCBs offer numerous advantages, including energy efficiency, long lifespan, and versatility, making them increasingly popular in modern electronics.
Key Components of an LED PCB
- Substrate material (e.g., FR-4, aluminum, or flexible materials)
- Copper traces for electrical connections
- Solder mask for insulation and protection
- Silkscreen for labeling and identification
- LED components (surface mount or Through-Hole)
- Resistors for current limiting
- Connectors for power input and output
Types of LED PCBs
There are several types of LED PCBs, each designed for specific applications and requirements:
1. Rigid LED PCBs
Rigid LED PCBs are the most common type, using a solid substrate material such as FR-4. They offer excellent durability and heat dissipation, making them suitable for a wide range of applications.
2. Flexible LED PCBs
Flexible LED PCBs use a thin, bendable substrate material, allowing for unique shapes and configurations. These boards are ideal for applications requiring conformity to curved surfaces or tight spaces.
3. Aluminum LED PCBs
Aluminum LED PCBs feature an aluminum substrate, which provides superior heat dissipation compared to traditional FR-4 boards. This makes them well-suited for high-power LED applications that generate significant heat.
4. High-Density Interconnect (HDI) LED PCBs
HDI LED PCBs offer higher component density and more complex designs, enabling smaller form factors and advanced functionality. These boards are commonly used in miniaturized LED displays and compact lighting solutions.
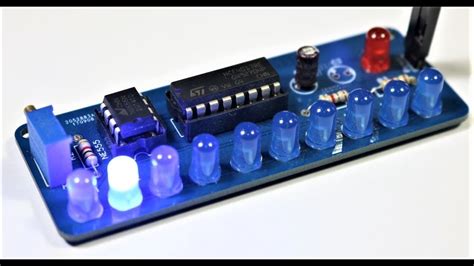
Advantages of LED PCBs
LED PCBs offer several key advantages over traditional lighting solutions:
-
Energy efficiency: LEDs consume significantly less power than incandescent or fluorescent lights, resulting in lower energy costs and reduced environmental impact.
-
Long lifespan: LED components can last up to 50,000 hours or more, minimizing maintenance and replacement costs.
-
Versatility: LED PCBs can be designed for a wide range of applications, from simple indicators to complex displays and lighting systems.
-
Compact size: LED components are small and can be densely packed on a PCB, enabling miniaturized designs and space-saving solutions.
-
Durability: LED PCBs are resistant to shock, vibration, and extreme temperatures, making them suitable for harsh environments.
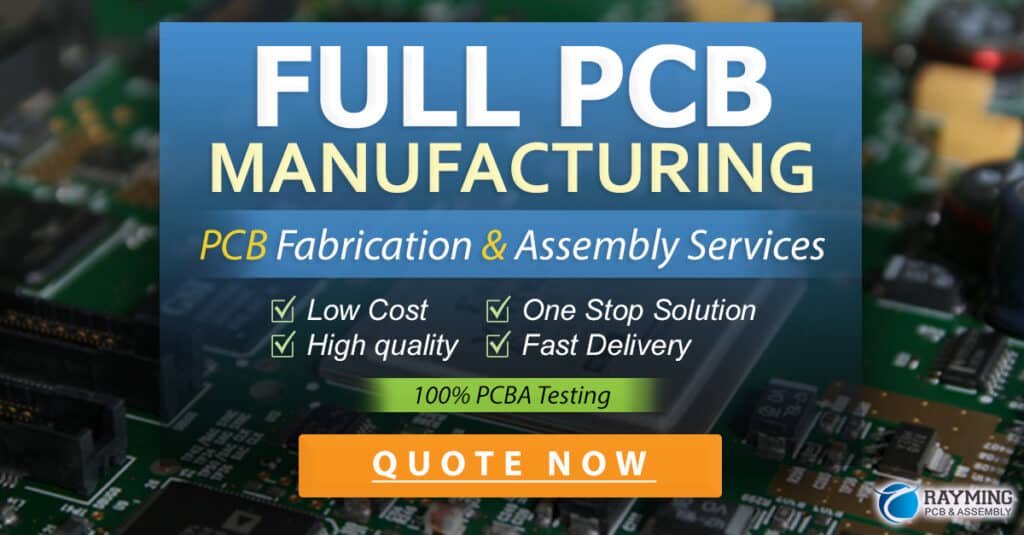
Applications of LED PCBs
LED PCBs are used in numerous applications across various industries:
1. Consumer Electronics
- Smartphones and tablets
- Laptops and computers
- Televisions and monitors
- Gaming devices and peripherals
2. Automotive Industry
- Interior lighting (dashboard, cabin, and accent lights)
- Exterior lighting (headlights, taillights, and turn signals)
- Infotainment systems and displays
3. Lighting Industry
- Residential and commercial lighting fixtures
- Street lighting and outdoor illumination
- Stage and entertainment lighting
4. Medical Devices
- Diagnostic equipment (e.g., endoscopes and microscopes)
- Therapy devices (e.g., phototherapy and light therapy)
- Medical displays and imaging systems
5. Signage and Advertising
- Digital billboards and displays
- Retail signage and product displays
- Wayfinding and directional signs
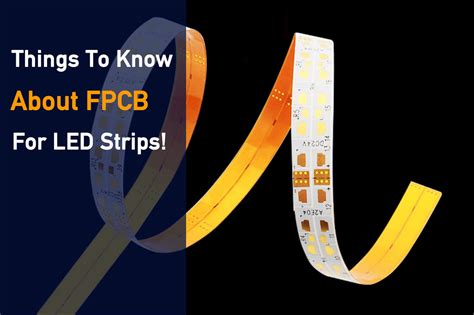
Designing LED PCBs
Designing an LED PCB involves several key considerations to ensure optimal performance, reliability, and longevity:
1. Component Selection
Choose appropriate LED components based on the desired color, brightness, viewing angle, and power requirements. Consider the LED package type (surface mount or through-hole) and ensure compatibility with the PCB design.
2. Current Limiting
LEDs require current limiting to prevent damage and ensure consistent brightness. Use resistors or dedicated LED drivers to control the current flowing through each LED.
3. Thermal Management
Effective thermal management is crucial for LED PCBs, as excessive heat can reduce LED lifespan and performance. Use appropriate substrate materials, copper pour, and thermal vias to dissipate heat away from the LEDs.
4. Power Distribution
Design power distribution networks to ensure consistent voltage and current across all LED components. Consider the number of LEDs, their arrangement, and the total power consumption when planning power traces and connectors.
5. Layout and Routing
Optimize the PCB layout and routing to minimize signal interference, reduce voltage drop, and ensure proper current flow. Follow best practices for trace width, spacing, and via placement to achieve reliable connections and avoid manufacturing issues.
Manufacturing LED PCBs
The manufacturing process for LED PCBs involves several steps to ensure high quality and reliability:
-
PCB Fabrication: The PCB design files are used to create the physical board, including the substrate, copper traces, solder mask, and silkscreen.
-
Component Placement: LED components and other parts are placed on the PCB using automated pick-and-place machines or manual assembly methods.
-
Soldering: The placed components are soldered to the PCB using reflow ovens (for surface mount components) or wave soldering (for through-hole components).
-
Inspection and Testing: The assembled LED PCBs undergo visual inspection and electrical testing to ensure proper functionality and adherence to specifications.
-
Conformal Coating (optional): A protective coating may be applied to the PCB to enhance durability and resistance to environmental factors such as moisture, dust, and chemicals.
Troubleshooting LED PCBs
When encountering issues with LED PCBs, consider the following troubleshooting steps:
-
Check Power Supply: Verify that the PCB is receiving the correct voltage and current from the power source. Use a multimeter to measure the input voltage and ensure it matches the design specifications.
-
Inspect Solder Joints: Examine the solder joints for any signs of poor connection, such as cold joints, bridges, or insufficient solder. Rework or resolder any problematic joints as needed.
-
Test LED Components: Use a multimeter or LED tester to verify the functionality of individual LED components. Replace any faulty or damaged LEDs.
-
Review Current Limiting: Ensure that the current limiting resistors or drivers are properly sized and functioning correctly. Measure the current flowing through the LEDs and compare it to the expected values.
-
Check PCB Traces: Inspect the PCB traces for any signs of damage, such as cracks, cuts, or corrosion. Use a continuity tester to verify the integrity of the electrical connections.
Future Trends in LED PCBs
As technology advances, LED PCBs continue to evolve and improve:
-
Miniaturization: Smaller LED components and higher-density PCB designs enable more compact and lightweight solutions.
-
Intelligent Control: Integration of smart sensors, microcontrollers, and wireless connectivity allows for more sophisticated LED control and automation.
-
Improved Efficiency: Advancements in LED technology and driver circuits lead to higher luminous efficacy and lower power consumption.
-
Sustainable Materials: Eco-friendly PCB Substrates and LED components are being developed to reduce environmental impact and improve recyclability.
-
Flexible and Stretchable Designs: Advances in flexible and stretchable electronics enable LED PCBs to conform to complex shapes and surfaces, opening up new application possibilities.
FAQ
1. What is the difference between an LED PCB and a regular PCB?
An LED PCB is specifically designed to support and control LED components, while a regular PCB can be used for various electronic applications. LED PCBs often have unique features, such as thermal management and current limiting, to ensure optimal LED performance and longevity.
2. Can I use any type of LED with an LED PCB?
No, it is essential to select LED components that are compatible with the specific LED PCB design. Factors such as LED package type, power requirements, and color should be considered when choosing LEDs for a particular PCB.
3. How do I ensure proper thermal management for my LED PCB?
Effective thermal management can be achieved through various methods, such as using appropriate substrate materials (e.g., aluminum), incorporating copper pour and thermal vias, and designing adequate spacing between LED components. It is also important to consider the operating environment and provide sufficient ventilation or heatsinking if necessary.
4. What is the lifespan of an LED PCB?
The lifespan of an LED PCB depends on several factors, including the quality of components, thermal management, and operating conditions. Properly designed and maintained LED PCBs can last for tens of thousands of hours, often surpassing the longevity of traditional lighting solutions.
5. Are LED PCBs more expensive than traditional lighting solutions?
While LED PCBs may have a higher initial cost compared to traditional lighting solutions, they often provide long-term cost savings due to their energy efficiency, long lifespan, and reduced maintenance requirements. The total cost of ownership for LED PCBs is typically lower when considering the entire product lifecycle.
Conclusion
LED PCBs have revolutionized the lighting industry, offering numerous advantages over traditional solutions. With their energy efficiency, long lifespan, versatility, and compact size, LED PCBs have become essential components in a wide range of applications, from consumer electronics to automotive, medical, and signage industries.
Designing and manufacturing LED PCBs requires careful consideration of various factors, such as component selection, current limiting, thermal management, and power distribution. By following best practices and staying up-to-date with the latest trends and technologies, engineers and manufacturers can create innovative and reliable LED PCB solutions that meet the ever-evolving demands of the market.
As the world continues to prioritize energy efficiency and sustainability, the future of LED PCBs looks bright. With ongoing advancements in miniaturization, intelligent control, and eco-friendly materials, LED PCBs are poised to play an increasingly vital role in shaping the future of lighting and electronics.
Leave a Reply