Introduction to HAL lead-free
HAL lead-free is a type of Lead-free Solder alloy that is commonly used in the electronics industry. It is an acronym that stands for “High-reliability Alloy Lead-free”. HAL lead-free solders are designed to provide a reliable and durable alternative to traditional lead-based solders, which have been phased out due to environmental and health concerns.
The need for lead-free solders
Lead has been used in solders for many years due to its low melting point, excellent wetting properties, and good electrical conductivity. However, lead is a toxic substance that can have harmful effects on human health and the environment. In response to these concerns, governments around the world have implemented regulations to restrict the use of lead in electronics manufacturing.
The European Union’s Restriction of Hazardous Substances (RoHS) Directive, which came into effect in 2006, was one of the first major regulations to restrict the use of lead in electronics. The directive requires that all electronic and electrical equipment sold in the EU must not contain more than 0.1% lead by weight. Other countries, such as the United States, China, and Japan, have also implemented similar regulations.
As a result of these regulations, the electronics industry has had to develop alternative lead-free solder alloys that can provide similar performance and reliability to lead-based solders. HAL lead-free solders are one of the most widely used lead-free solder alloys in the industry today.
Composition of HAL lead-free solders
HAL lead-free solders are typically composed of a combination of tin (Sn), silver (Ag), and copper (Cu). The most common composition of HAL lead-free solder is Sn96.5Ag3.0Cu0.5, which contains 96.5% tin, 3.0% silver, and 0.5% copper by weight. This composition is often referred to as SAC305.
Other common compositions of HAL lead-free solders include:
Composition | Tin (Sn) | Silver (Ag) | Copper (Cu) |
---|---|---|---|
SAC105 | 98.5% | 1.0% | 0.5% |
SAC0307 | 99.0% | 0.3% | 0.7% |
SAC387 | 95.5% | 3.8% | 0.7% |
The specific composition of HAL lead-free solder can vary depending on the application and the desired properties of the solder joint. For example, higher silver content can improve the mechanical strength and thermal fatigue resistance of the solder joint, while higher copper content can improve the wetting properties and reduce the formation of Tin Whiskers.
Tin whiskers and HAL lead-free solders
Tin whiskers are thin, hair-like structures that can grow on the surface of tin-based solders over time. They can cause short circuits and other reliability issues in electronic devices. The growth of tin whiskers is a complex process that is influenced by various factors, such as the composition of the solder, the surface finish of the substrate, and the environmental conditions.
HAL lead-free solders are designed to reduce the risk of tin whisker formation by controlling the composition of the solder alloy. The addition of silver and copper to the tin-based solder can help to suppress the growth of tin whiskers by forming intermetallic compounds that stabilize the microstructure of the solder joint.
However, it is important to note that no solder alloy is completely immune to tin whisker formation. Proper design, manufacturing, and testing practices are still necessary to ensure the reliability and durability of electronic devices that use HAL lead-free solders.
Properties of HAL lead-free solders
HAL lead-free solders have several key properties that make them suitable for use in electronics manufacturing:
Melting point
The melting point of HAL lead-free solders is typically higher than that of lead-based solders. For example, the melting point of SAC305 is around 217-220°C, while the melting point of a typical lead-based solder (Sn63Pb37) is around 183°C. The higher melting point of HAL lead-free solders can require adjustments to the soldering process, such as higher soldering temperatures and longer dwell times.
Wetting properties
Wetting refers to the ability of the molten solder to spread and adhere to the surface of the substrate. Good wetting properties are important for achieving a strong and reliable solder joint. HAL lead-free solders generally have good wetting properties, although they may not be as good as lead-based solders. The addition of silver and copper to the solder alloy can help to improve the wetting properties.
Mechanical strength
The mechanical strength of a solder joint refers to its ability to withstand mechanical stresses and strains without failing. HAL lead-free solders generally have good mechanical strength, although they may not be as strong as lead-based solders. The addition of silver to the solder alloy can help to improve the mechanical strength of the solder joint.
Thermal fatigue resistance
Thermal fatigue is a common failure mode in solder joints that is caused by repeated thermal cycling (heating and cooling) of the joint. HAL lead-free solders generally have good thermal fatigue resistance, although they may not be as resistant as lead-based solders. The addition of silver to the solder alloy can help to improve the thermal fatigue resistance of the solder joint.
Electrical conductivity
Electrical conductivity is an important property for solder joints in electronic devices, as it affects the ability of the joint to carry electrical current. HAL lead-free solders generally have good electrical conductivity, although they may not be as conductive as lead-based solders. The addition of silver to the solder alloy can help to improve the electrical conductivity of the solder joint.
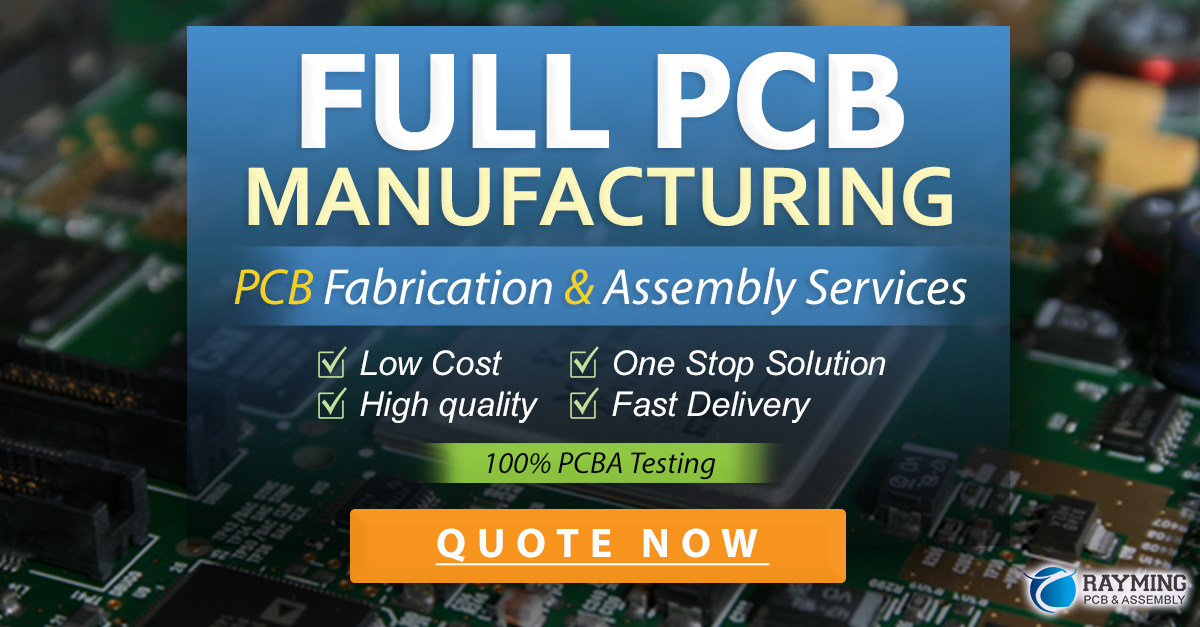
Applications of HAL lead-free solders
HAL lead-free solders are used in a wide range of electronic applications, including:
Consumer electronics
Consumer electronics, such as smartphones, tablets, and laptops, are one of the largest markets for HAL lead-free solders. These devices require high-reliability solder joints that can withstand the stresses of daily use and frequent handling.
Automotive electronics
Automotive electronics, such as engine control units, sensors, and infotainment systems, are another important application for HAL lead-free solders. These devices must be able to withstand the harsh environmental conditions and vibrations that are common in automotive applications.
Aerospace and defense electronics
Aerospace and defense electronics, such as avionics systems and military communications equipment, also require high-reliability solder joints that can withstand extreme environmental conditions and long service lives. HAL lead-free solders are commonly used in these applications due to their excellent mechanical strength and thermal fatigue resistance.
Medical electronics
Medical electronics, such as pacemakers and imaging equipment, require high-reliability solder joints that can withstand the rigors of long-term implantation or frequent use. HAL lead-free solders are commonly used in these applications due to their excellent biocompatibility and resistance to corrosion.
Challenges and considerations for using HAL lead-free solders
While HAL lead-free solders offer many benefits over traditional lead-based solders, there are also some challenges and considerations that must be taken into account when using them:
Higher soldering temperatures
As mentioned earlier, HAL lead-free solders typically have higher melting points than lead-based solders. This means that higher soldering temperatures and longer dwell times may be required to achieve a good solder joint. These higher temperatures can pose challenges for heat-sensitive components and substrates, and may require adjustments to the soldering process.
Compatibility with surface finishes
The compatibility of HAL lead-free solders with different surface finishes is an important consideration in electronics manufacturing. Some surface finishes, such as immersion silver and electroless nickel/immersion gold (ENIG), are more compatible with HAL lead-free solders than others. It is important to select a surface finish that is compatible with the solder alloy being used to ensure good wetting and a reliable solder joint.
Rework and repair
Rework and repair of HAL lead-free solder joints can be more challenging than with lead-based solders due to the higher melting point and different wetting properties of the solder alloy. Special care must be taken to avoid damaging the substrate or components during rework and repair operations.
Cost considerations
HAL lead-free solders are generally more expensive than lead-based solders due to the higher cost of the raw materials (tin, silver, and copper). This higher cost must be balanced against the environmental and health benefits of using lead-free solders, as well as the potential long-term reliability benefits.
Frequently Asked Questions (FAQ)
Q: What does HAL stand for in HAL lead-free solder?
A: HAL stands for “High-reliability Alloy Lead-free”. It is a type of lead-free solder alloy that is designed to provide high reliability and durability in electronic applications.
Q: What is the most common composition of HAL lead-free solder?
A: The most common composition of HAL lead-free solder is Sn96.5Ag3.0Cu0.5, which contains 96.5% tin, 3.0% silver, and 0.5% copper by weight. This composition is often referred to as SAC305.
Q: Why are lead-free solders necessary in electronics manufacturing?
A: Lead-free solders are necessary due to environmental and health concerns associated with the use of lead in electronics. Many countries have implemented regulations, such as the European Union’s RoHS Directive, that restrict the use of lead in electronic and electrical equipment.
Q: What are some of the key properties of HAL lead-free solders?
A: Some of the key properties of HAL lead-free solders include a higher melting point than lead-based solders, good wetting properties, good mechanical strength, good thermal fatigue resistance, and good electrical conductivity.
Q: What are some of the challenges and considerations for using HAL lead-free solders?
A: Some of the challenges and considerations for using HAL lead-free solders include higher soldering temperatures, compatibility with surface finishes, rework and repair challenges, and cost considerations.
Conclusion
HAL lead-free solders are an important development in the electronics industry, providing a reliable and durable alternative to traditional lead-based solders. As environmental and health concerns continue to drive the transition to lead-free electronics, HAL lead-free solders are likely to play an increasingly important role in the future of electronics manufacturing.
While there are challenges and considerations associated with using HAL lead-free solders, the benefits in terms of reliability, durability, and environmental sustainability make them a valuable tool for electronics manufacturers. By understanding the properties and applications of HAL lead-free solders, as well as the challenges and considerations involved in using them, manufacturers can make informed decisions about the best solder alloys and processes for their specific needs.
As the electronics industry continues to evolve and new technologies emerge, it is likely that HAL lead-free solders will continue to be an important part of the manufacturing landscape. By staying up-to-date with the latest developments and best practices in lead-free soldering, manufacturers can ensure that they are well-positioned to meet the demands of the future.
Leave a Reply