What is ENIG?
ENIG is a two-step process that involves depositing a layer of nickel on the copper pads of a PCB, followed by a thin layer of gold. The nickel layer serves as a barrier between the copper and the gold, preventing the formation of intermetallic compounds that can weaken the solder joint. The gold layer provides excellent solderability and protection against oxidation and contamination.
The ENIG Process
The ENIG process consists of several steps:
- Cleaning: The PCB is thoroughly cleaned to remove any contaminants or oxides from the copper surface.
- Microetching: The copper surface is slightly etched to improve adhesion of the nickel layer.
- Activation: The copper surface is activated using a palladium-based solution to promote the deposition of nickel.
- Electroless Nickel Plating: A thin layer of nickel (typically 3-6 µm) is deposited on the copper surface using an autocatalytic chemical reaction.
- Immersion Gold Plating: A thin layer of gold (typically 0.05-0.2 µm) is deposited on the nickel surface using an immersion plating process.
- Rinsing and Drying: The PCB is rinsed with deionized water and dried.
Advantages of ENIG
ENIG offers several advantages over other PCB Surface Finishes:
- Excellent Solderability: The gold layer provides excellent wettability and solderability, ensuring reliable solder joints.
- Corrosion Resistance: The nickel layer acts as a barrier, protecting the copper from corrosion and oxidation.
- Durability: ENIG is a durable surface finish that can withstand multiple reflow cycles and storage in harsh environments.
- Flatness: The thin layers of nickel and gold maintain the flatness of the PCB, which is essential for fine-pitch components.
- Wire Bonding: The gold surface is suitable for wire bonding applications.
- RoHS Compliance: ENIG is a lead-free and RoHS-Compliant surface finish.
Disadvantages of ENIG
Despite its many advantages, ENIG also has some disadvantages:
- Cost: ENIG is more expensive than other surface finishes like HASL (Hot Air Solder Leveling) or OSP (Organic Solderability Preservative).
- Black Pad: In some cases, a defect known as “black pad” can occur, where the nickel layer separates from the copper surface due to excessive phosphorus content in the electroless nickel bath.
- Brittle Solder Joints: Thick nickel layers (>6 µm) can lead to brittle solder joints, especially when exposed to high-stress conditions.
Applications of ENIG
ENIG is widely used in various applications, including:
- High-Density Interconnect (HDI) PCBs: ENIG’s flatness and fine-pitch compatibility make it suitable for HDI PCBs used in smartphones, tablets, and other compact electronic devices.
- Automotive Electronics: The durability and corrosion resistance of ENIG make it ideal for Automotive PCBs exposed to harsh environments.
- Aerospace and Defense: ENIG’s reliability and resistance to oxidation make it a preferred choice for aerospace and defense applications.
- Medical Devices: The biocompatibility and durability of ENIG make it suitable for medical device PCBs.
- Industrial Electronics: ENIG’s robust performance and long shelf life make it suitable for industrial electronics exposed to harsh conditions.
Comparison of ENIG with Other Surface Finishes
ENIG is one of several PCB Surface Finishes available, each with its own advantages and disadvantages. Here’s a comparison of ENIG with other common surface finishes:
Surface Finish | Advantages | Disadvantages |
---|---|---|
ENIG | – Excellent solderability – Corrosion resistance – Durability – Flatness – Wire bondable |
– Higher cost – Potential for black pad defect – Brittle solder joints with thick nickel |
HASL (Hot Air Solder Leveling) | – Low cost – Good solderability – Suitable for through-hole components |
– Not suitable for fine-pitch components – Uneven surface – Potential for thermal shock damage |
OSP (Organic Solderability Preservative) | – Low cost – Flat surface – Suitable for fine-pitch components |
– Limited shelf life – Potential for poor solderability if not stored properly – Not suitable for multiple reflow cycles |
Immersion Silver | – Excellent solderability – Low cost – Flat surface – Suitable for fine-pitch components |
– Limited shelf life – Potential for tarnishing and oxidation – Not suitable for high-sulfur environments |
Immersion Tin | – Good solderability – Low cost – Flat surface – Suitable for fine-pitch components |
– Limited shelf life – Potential for tin whiskers – Not suitable for high-temperature applications |
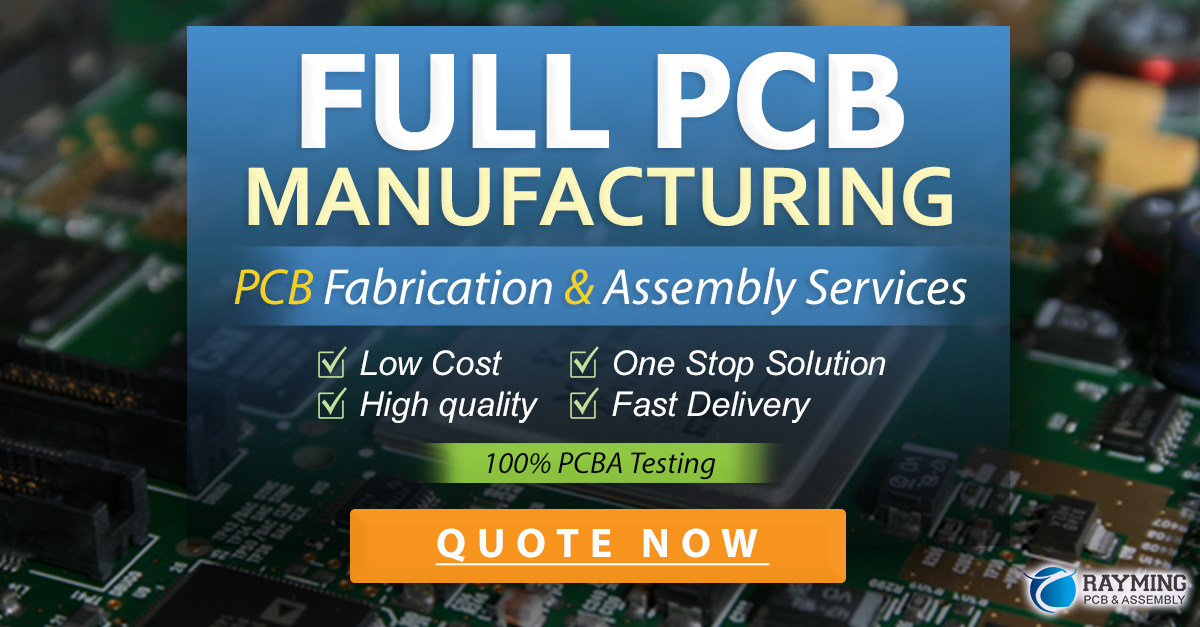
Choosing the Right Surface Finish
When selecting a surface finish for your PCB, consider the following factors:
- Application Requirements: Consider the specific requirements of your application, such as environmental conditions, shelf life, and solderability.
- Component Compatibility: Ensure that the surface finish is compatible with the components used on the PCB, especially for fine-pitch and BGA components.
- Cost: Evaluate the cost of the surface finish in relation to the overall project budget and the expected production volume.
- Reliability: Assess the reliability of the surface finish based on factors such as corrosion resistance, durability, and potential for defects.
- Manufacturing Capabilities: Verify that your PCB manufacturer has the necessary equipment and expertise to apply the chosen surface finish consistently and reliably.
FAQ
-
Q: What is the difference between ENIG and ENEPIG?
A: ENEPIG (Electroless Nickel Electroless Palladium Immersion Gold) is similar to ENIG but has an additional layer of palladium between the nickel and gold layers. This extra layer provides better solder joint reliability and wire bonding performance but at a higher cost. -
Q: Can ENIG be used for both lead-free and leaded soldering?
A: Yes, ENIG is compatible with both lead-free and leaded soldering processes. -
Q: How does the shelf life of ENIG compare to other surface finishes?
A: ENIG has a longer shelf life compared to OSP and immersion silver, typically 12 months or more when stored properly. However, it is still recommended to use ENIG-coated PCBs as soon as possible to ensure the best solderability. -
Q: Is ENIG suitable for high-temperature applications?
A: Yes, ENIG can withstand higher temperatures compared to other surface finishes like immersion tin, making it suitable for high-temperature applications. -
Q: Can ENIG be reworked?
A: Yes, ENIG can be reworked using standard soldering techniques. However, care must be taken to avoid damaging the nickel and gold layers during the rework process.
In conclusion, ENIG is a popular and reliable surface finish for PCBs, offering excellent solderability, corrosion resistance, and durability. While it may be more expensive than some other surface finishes, its superior performance and long shelf life make it a preferred choice for many applications, including high-density interconnect PCBs, automotive electronics, aerospace and defense, medical devices, and industrial electronics.
When selecting a surface finish for your PCB, consider the specific requirements of your application, component compatibility, cost, reliability, and your manufacturer’s capabilities. By understanding the advantages and disadvantages of ENIG and other surface finishes, you can make an informed decision that ensures the best performance and reliability for your PCB.
Leave a Reply