Introduction to Component orientation
Component orientation is a fundamental concept in the field of engineering and manufacturing. It refers to the specific positioning and alignment of components within a system or assembly. The proper orientation of components is crucial for ensuring optimal performance, reliability, and functionality of the final product. In this article, we will delve into the details of component orientation, its importance, and the various factors that influence it.
Understanding the Basics of Component Orientation
Definition and Concept
Component orientation can be defined as the spatial arrangement and alignment of individual components within a larger system or assembly. It involves determining the precise position, rotation, and orientation of each component relative to a reference point or coordinate system. The orientation of components is typically specified using a set of standardized conventions and notations, such as the Cartesian coordinate system or the use of angles and vectors.
Importance of Proper Component Orientation
Ensuring proper component orientation is essential for several reasons:
-
Functionality: The correct orientation of components ensures that they function as intended. Misaligned or incorrectly oriented components can lead to malfunctions, reduced efficiency, or complete failure of the system.
-
Compatibility: Proper orientation ensures that components fit together seamlessly and interact correctly with adjacent components. Misalignment can result in interference, gaps, or improper mating of components.
-
Durability: Correctly oriented components are less likely to experience undue stress, wear, or damage during operation. Improper orientation can lead to increased friction, vibration, or excessive loading, which can reduce the lifespan of components.
-
Aesthetics: In some cases, component orientation plays a role in the visual appeal and overall aesthetics of the final product. Misaligned components can detract from the desired appearance and give an impression of poor quality or workmanship.
Factors Influencing Component Orientation
Several factors must be considered when determining the optimal orientation of components:
-
Design Intent: The intended function and purpose of the component within the overall system should guide its orientation. The orientation should facilitate the desired interaction and behavior of the component.
-
Manufacturing Constraints: The manufacturing processes and techniques used to produce the components may impose certain limitations on their orientation. For example, the orientation may need to accommodate the direction of machining operations or the flow of molten material during casting.
-
Assembly Requirements: The ease and efficiency of assembling the components into the final product should be considered. The orientation should allow for straightforward and error-free assembly, minimizing the risk of misalignment or incorrect installation.
-
Mechanical Loads: The orientation of components should account for the anticipated mechanical loads and stresses they will experience during operation. Components should be oriented to distribute loads evenly and minimize the risk of failure or deformation.
-
Thermal Considerations: In systems where heat transfer is a concern, the orientation of components can impact their thermal performance. Proper orientation can facilitate efficient heat dissipation or minimize thermal expansion and contraction.
Types of Component Orientation
There are several common types of component orientation used in various engineering and manufacturing contexts:
Axial Orientation
Axial orientation refers to the alignment of components along a common axis. This type of orientation is often used for cylindrical or elongated components, such as shafts, bearings, or gears. The components are positioned end-to-end, with their longitudinal axes aligned.
Radial Orientation
Radial orientation involves arranging components around a central point or axis, forming a circular or radial pattern. This type of orientation is commonly used in applications such as wheels, turbines, or rotary machines. The components are positioned at equal angular intervals around the central axis.
Planar Orientation
Planar orientation refers to the alignment of components within a flat or two-dimensional plane. This type of orientation is often used for printed circuit boards (PCBs), where electronic components are mounted on a flat substrate. The orientation of components on a PCB is critical for ensuring proper electrical connections and avoiding interference.
Spatial Orientation
Spatial orientation involves the three-dimensional arrangement of components within a system or assembly. This type of orientation is relevant in complex mechanical systems, such as engines, robotics, or aerospace applications. The components are positioned and oriented in three-dimensional space, considering factors such as clearance, accessibility, and functionality.
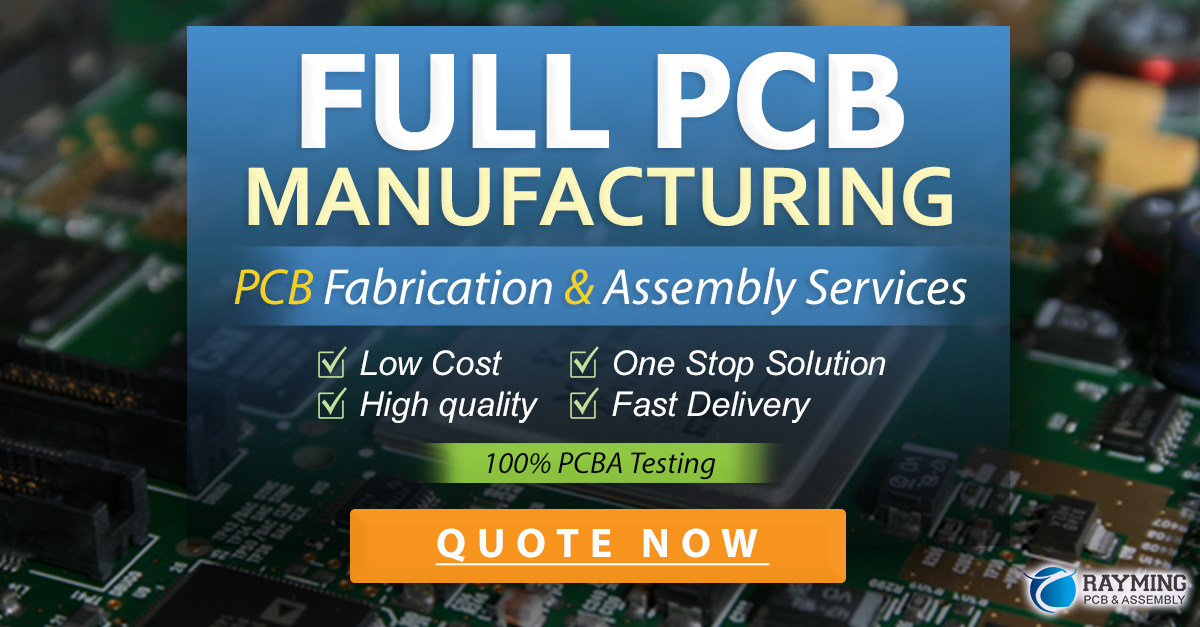
Techniques for Ensuring Proper Component Orientation
To ensure proper component orientation during the design and manufacturing process, several techniques and practices can be employed:
Design for Manufacturing (DFM)
Design for Manufacturing (DFM) is an approach that considers the manufacturability of components during the design phase. DFM principles guide designers to create components that are easy to manufacture and assemble, taking into account factors such as orientation, accessibility, and simplicity. By incorporating DFM principles, designers can minimize the risk of orientation-related issues and streamline the manufacturing process.
Tolerance Analysis
Tolerance analysis is a technique used to assess the impact of dimensional variations on the overall assembly and functionality of a system. It involves analyzing the allowable deviations in component dimensions and orientations to ensure that the final assembly meets the desired specifications. Tolerance analysis helps identify potential orientation-related issues and guides the selection of appropriate tolerances for each component.
Assembly Simulations
Assembly simulations are computer-aided tools that allow designers to virtually assemble components and assess their orientation and fit. These simulations provide a visual representation of the assembly process and can highlight potential interference, misalignment, or orientation issues. By using assembly simulations, designers can identify and resolve orientation-related problems before physical prototyping or manufacturing.
Datum Referencing
Datum referencing is a technique used to establish a common reference frame for positioning and orienting components within an assembly. Datums are chosen reference points, lines, or planes that serve as a basis for measuring and aligning components. By using a consistent datum referencing system, designers can ensure that components are oriented correctly relative to each other and the overall assembly.
Quality Control and Inspection
Quality control and inspection procedures play a crucial role in verifying the proper orientation of components during manufacturing and assembly. These procedures may include visual inspections, dimensional checks, or functional tests to ensure that components are oriented correctly and meet the specified requirements. Quality control measures help identify and correct orientation-related issues before the final product is released.
Case Studies and Examples
To illustrate the importance and application of component orientation, let’s consider a few real-world examples:
Automotive Engine Assembly
In an automotive engine, the orientation of components such as pistons, connecting rods, and crankshafts is critical for proper operation and durability. The pistons must be oriented correctly within the cylinders to ensure efficient combustion and minimize wear. The connecting rods must be aligned with the crankshaft journals to transmit power effectively. Proper orientation of these components is achieved through precise machining, assembly procedures, and quality control measures.
Printed Circuit Board (PCB) Design
In PCB design, the orientation of electronic components is crucial for ensuring proper electrical connections and avoiding interference. Components such as integrated circuits (ICs), capacitors, and resistors must be oriented correctly on the PCB to align with the designated footprints and pads. Incorrect orientation can lead to short circuits, signal integrity issues, or manufacturing defects. PCB designers use specialized software tools and adhere to industry standards to ensure proper component orientation.
Aerospace Fastener Installation
In aerospace applications, the orientation of fasteners, such as bolts and rivets, is critical for structural integrity and safety. Fasteners must be installed in the correct orientation to ensure proper engagement and load distribution. Incorrect orientation can lead to reduced strength, loosening, or failure of the fastened joint. Aerospace manufacturers follow strict installation procedures and use specialized tools to ensure the correct orientation of fasteners.
Frequently Asked Questions (FAQ)
-
What is the difference between axial and radial orientation?
Axial orientation refers to the alignment of components along a common axis, typically end-to-end. Radial orientation involves arranging components around a central point or axis, forming a circular or radial pattern. -
How does component orientation affect the functionality of a system?
Proper component orientation ensures that the components function as intended and interact correctly with adjacent components. Misaligned or incorrectly oriented components can lead to malfunctions, reduced efficiency, or complete failure of the system. -
What are some techniques used to ensure proper component orientation during the design and manufacturing process?
Techniques used to ensure proper component orientation include Design for Manufacturing (DFM), tolerance analysis, assembly simulations, datum referencing, and quality control and inspection procedures. -
Why is component orientation important in printed circuit board (PCB) design?
In PCB design, the orientation of electronic components is crucial for ensuring proper electrical connections and avoiding interference. Incorrect orientation can lead to short circuits, signal integrity issues, or manufacturing defects. -
How does component orientation impact the durability and lifespan of a product?
Correctly oriented components are less likely to experience undue stress, wear, or damage during operation. Improper orientation can lead to increased friction, vibration, or excessive loading, which can reduce the lifespan of components.
Conclusion
Component orientation is a critical aspect of engineering and manufacturing that directly impacts the functionality, compatibility, durability, and aesthetics of a product. Proper orientation ensures that components function as intended, fit together seamlessly, and withstand the intended mechanical and thermal loads. Various factors, such as design intent, manufacturing constraints, assembly requirements, and environmental considerations, influence the optimal orientation of components.
To ensure proper component orientation, techniques such as Design for Manufacturing (DFM), tolerance analysis, assembly simulations, datum referencing, and quality control measures are employed. These techniques help identify and resolve orientation-related issues during the design and manufacturing process, minimizing the risk of errors and ensuring the overall quality of the final product.
Real-world examples, such as automotive engine assembly, PCB design, and aerospace fastener installation, highlight the importance of component orientation in various industries. By understanding and applying the principles of component orientation, engineers and manufacturers can create products that are reliable, efficient, and meet the desired specifications.
As technology advances and products become increasingly complex, the significance of component orientation will only continue to grow. By staying informed about best practices and emerging techniques in this field, professionals can stay ahead of the curve and deliver high-quality products that meet the evolving needs of their customers.
Leave a Reply