Introduction to PCB Optimization
Printed Circuit Board (PCB) assembly is a complex process that involves multiple steps, from design and manufacturing to testing and inspection. One of the most critical aspects of PCB Assembly is front-end data optimization, which plays a crucial role in ensuring the quality, reliability, and cost-effectiveness of the final product.
Front-end data optimization refers to the process of optimizing the design data before it is sent to the manufacturing process. This optimization process involves various techniques and tools to ensure that the design data is accurate, complete, and consistent, and that it meets the required specifications and standards.
Why is Front-End Data Optimization Important?
Front-end data optimization is essential for several reasons:
-
Quality Assurance: Optimizing the design data helps to identify and correct errors, inconsistencies, and potential issues before they become problems during manufacturing. This ensures that the final product meets the required quality standards and specifications.
-
Cost Reduction: By identifying and correcting issues early in the design phase, front-end data optimization helps to reduce the cost of manufacturing by minimizing the need for rework, scrap, and delays.
-
Time Savings: Optimizing the design data helps to streamline the manufacturing process, reducing the time required for setup, programming, and testing. This can significantly reduce the overall lead time for PCB assembly.
-
Improved Reliability: Front-end data optimization helps to ensure that the PCB is designed and manufactured to the highest standards of reliability, with minimal defects and failures.
Techniques for Front-End Data Optimization
There are several techniques and tools used for front-end data optimization in PCB assembly. Some of the most common techniques include:
Design Rule Checking (DRC)
Design Rule Checking (DRC) is a process of verifying that the PCB design meets the required design rules and constraints. DRC helps to identify and correct issues such as spacing violations, trace width violations, and other design rule violations that can affect the manufacturability and reliability of the PCB.
DRC is typically performed using specialized software tools that analyze the design data and report any violations or issues. These tools can be integrated into the PCB design software or used as standalone applications.
Gerber File Optimization
Gerber files are the standard format used for transferring PCB design data to the manufacturing process. Gerber file optimization involves verifying and optimizing the Gerber files to ensure that they are accurate, complete, and consistent.
Gerber file optimization typically involves the following steps:
-
Verification: The Gerber files are verified to ensure that they are complete and consistent, with no missing or incorrect data.
-
Panelization: The Gerber files are panelized to optimize the use of the PCB material and minimize waste.
-
Aperture Optimization: The apertures used in the Gerber files are optimized to ensure that they are consistent and accurate, with no overlaps or gaps.
-
Drill File Optimization: The drill files are optimized to ensure that the drill holes are correctly positioned and sized, with no missing or incorrect data.
Bill of Materials (BOM) Optimization
The Bill of Materials (BOM) is a critical component of the PCB design data, as it specifies the components and materials required for the PCB assembly. BOM optimization involves verifying and optimizing the BOM to ensure that it is accurate, complete, and consistent.
BOM optimization typically involves the following steps:
-
Verification: The BOM is verified to ensure that all the required components and materials are listed, with the correct part numbers, quantities, and specifications.
-
Standardization: The BOM is standardized to ensure that it uses consistent part numbers and descriptions, and that it follows the required format and conventions.
-
Optimization: The BOM is optimized to reduce the number of unique parts and materials, minimize the cost of components, and improve the availability and lead time of parts.
Component Placement Optimization
Component placement optimization involves optimizing the placement of components on the PCB to improve the manufacturability, reliability, and performance of the PCB.
Component placement optimization typically involves the following steps:
-
Placement Rule Checking: The component placement is verified to ensure that it meets the required placement rules and constraints, such as minimum spacing, orientation, and alignment.
-
Thermal Analysis: The component placement is analyzed to ensure that the PCB can dissipate heat effectively, and that the components are not exposed to excessive thermal stress.
-
Signal Integrity Analysis: The component placement is analyzed to ensure that the signal integrity of the PCB is maintained, with minimal crosstalk, reflections, and other signal integrity issues.
-
Manufacturing Optimization: The component placement is optimized to improve the manufacturability of the PCB, such as reducing the number of placement steps, minimizing the use of specialized equipment, and improving the accessibility of components for inspection and testing.
Benefits of Front-End Data Optimization
Front-end data optimization provides several benefits for PCB assembly, including:
-
Improved Quality: By identifying and correcting issues early in the design phase, front-end data optimization helps to improve the quality of the final product, with fewer defects and failures.
-
Reduced Cost: Front-end data optimization helps to reduce the cost of PCB assembly by minimizing the need for rework, scrap, and delays, and by optimizing the use of materials and components.
-
Faster Time-to-Market: By streamlining the manufacturing process and reducing the lead time for PCB assembly, front-end data optimization helps to accelerate the time-to-market for new products.
-
Enhanced Reliability: Front-end data optimization helps to ensure that the PCB is designed and manufactured to the highest standards of reliability, with minimal defects and failures, and improved performance and durability.
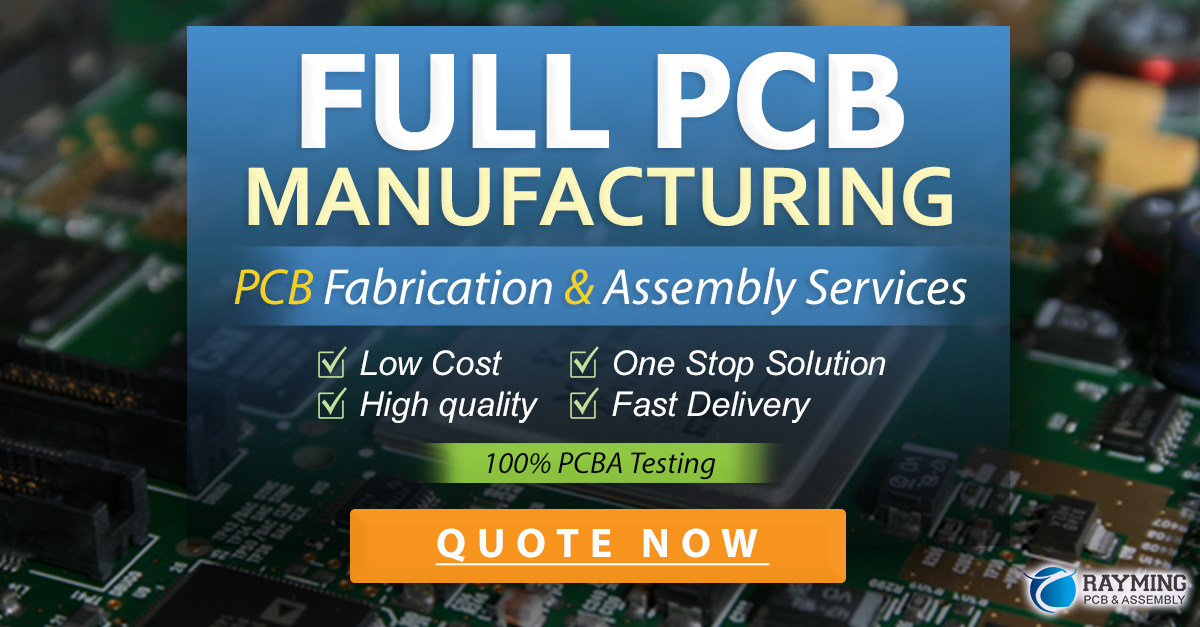
Tools for Front-End Data Optimization
There are several tools available for front-end data optimization in PCB assembly, including:
PCB Design Software
PCB design software, such as Altium Designer, Cadence OrCAD, and Mentor Graphics PADS, includes built-in tools for design rule checking, component placement optimization, and signal integrity analysis. These tools help to optimize the design data before it is sent to manufacturing.
Gerber File Viewers and Editors
Gerber file viewers and editors, such as GC-Prevue, CAM350, and ViewMate, allow users to view, verify, and edit Gerber files to ensure that they are accurate, complete, and consistent. These tools can also be used for panelization and aperture optimization.
BOM Management Software
BOM management software, such as Arena BOMControl, OpenBOM, and SiliconExpert, helps to manage and optimize the bill of materials for PCB assembly. These tools allow users to verify and standardize the BOM, reduce the number of unique parts, and improve the availability and lead time of components.
Manufacturing Execution Systems (MES)
Manufacturing Execution Systems (MES), such as Aegis FactoryLogix, Cogiscan Track, Trace and Control, and iTAC MES, provide real-time visibility and control over the PCB assembly process. These systems can capture and analyze data from the manufacturing process to identify issues and optimize the process for improved quality, efficiency, and cost-effectiveness.
Best Practices for Front-End Data Optimization
To achieve the best results from front-end data optimization, it is important to follow some best practices, including:
-
Early Collaboration: Collaborate with the manufacturing team early in the design phase to ensure that the design data is optimized for manufacturability and reliability.
-
Standardization: Use standardized design rules, component libraries, and BOM formats to ensure consistency and accuracy across the design and manufacturing process.
-
Continuous Improvement: Continuously monitor and analyze the manufacturing process to identify opportunities for improvement and optimization.
-
Automation: Use automated tools and processes for design rule checking, Gerber file optimization, BOM management, and other front-end data optimization tasks to reduce errors and improve efficiency.
-
Training and Education: Provide training and education to the design and manufacturing teams to ensure that they have the skills and knowledge required for effective front-end data optimization.
Frequently Asked Questions (FAQ)
1. What is front-end data optimization in PCB assembly?
Front-end data optimization refers to the process of optimizing the design data before it is sent to the manufacturing process. This optimization process involves various techniques and tools to ensure that the design data is accurate, complete, and consistent, and that it meets the required specifications and standards.
2. Why is front-end data optimization important for PCB assembly?
Front-end data optimization is important for PCB assembly because it helps to ensure the quality, reliability, and cost-effectiveness of the final product. By identifying and correcting issues early in the design phase, front-end data optimization helps to reduce the cost of manufacturing, improve the reliability of the PCB, and accelerate the time-to-market for new products.
3. What are some common techniques for front-end data optimization in PCB assembly?
Some common techniques for front-end data optimization in PCB assembly include design rule checking (DRC), Gerber file optimization, bill of materials (BOM) optimization, and component placement optimization. These techniques help to verify and optimize the design data to ensure that it meets the required specifications and standards.
4. What tools are available for front-end data optimization in PCB assembly?
There are several tools available for front-end data optimization in PCB assembly, including PCB design software, Gerber file viewers and editors, BOM management software, and manufacturing execution systems (MES). These tools help to automate and streamline the front-end data optimization process, reducing errors and improving efficiency.
5. What are some best practices for effective front-end data optimization in PCB assembly?
Some best practices for effective front-end data optimization in PCB assembly include early collaboration with the manufacturing team, standardization of design rules and formats, continuous improvement through monitoring and analysis, automation of optimization tasks, and training and education for the design and manufacturing teams. By following these best practices, organizations can achieve optimal results from their front-end data optimization efforts.
Technique | Description | Benefits |
---|---|---|
Design Rule Checking (DRC) | Verifies that the PCB design meets the required design rules and constraints | Identifies and corrects issues early in the design phase, improves manufacturability and reliability |
Gerber File Optimization | Verifies and optimizes Gerber files for accuracy, completeness, and consistency | Ensures accurate and consistent data transfer to manufacturing, reduces errors and waste |
Bill of Materials (BOM) Optimization | Verifies and optimizes the BOM for accuracy, completeness, and consistency | Reduces the cost of components, improves availability and lead time of parts |
Component Placement Optimization | Optimizes the placement of components on the PCB for manufacturability, reliability, and performance | Improves signal integrity, thermal performance, and manufacturing efficiency |
Conclusion
Front-end data optimization is a critical aspect of PCB assembly that helps to ensure the quality, reliability, and cost-effectiveness of the final product. By using various techniques and tools, such as design rule checking, Gerber file optimization, BOM optimization, and component placement optimization, organizations can optimize their design data before it is sent to manufacturing, reducing errors, improving efficiency, and accelerating time-to-market.
To achieve the best results from front-end data optimization, it is important to follow best practices such as early collaboration, standardization, continuous improvement, automation, and training and education. By investing in front-end data optimization, organizations can improve the quality and reliability of their PCBs, reduce costs, and gain a competitive advantage in the market.
Leave a Reply