Printed circuit boards (PCBs) are essential components in virtually all modern electronic devices. As electronics manufacturing grows globally, the PCB industry has expanded to meet demand. There are now hundreds of PCB manufacturers around the world producing rigid, flexible, and rigid-flex PCBs using the latest fabrication technologies.
This article will examine the top global PCB manufacturers by revenue, capabilities, and reputation. We will also discuss the key factors to consider when selecting a PCB manufacturing partner.
Major Global PCB Manufacturers
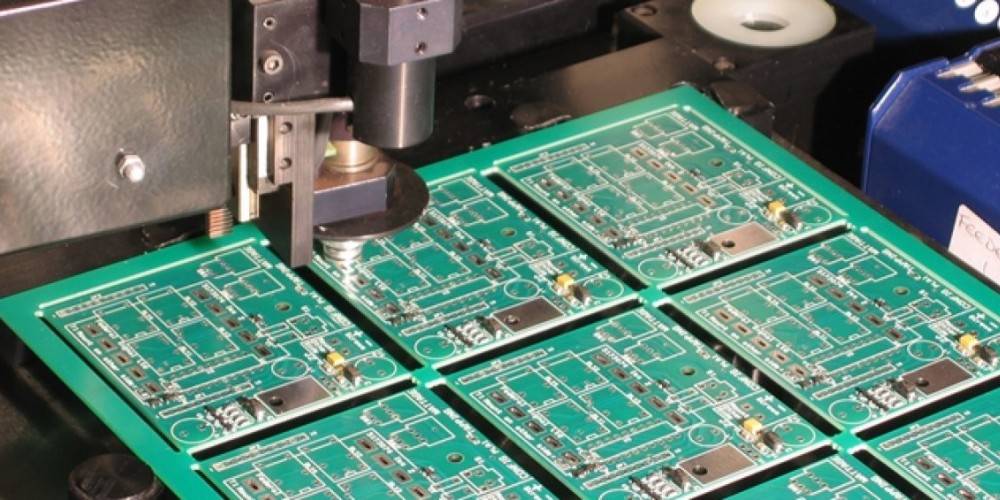
The PCB industry is dominated by manufacturers based in China and Taiwan. Many of the largest companies are Taiwan-based firms with most of their production capacity located in mainland China.
Here are the 5 largest global PCB manufacturers by annual revenue:
Company | Location | 2021 Revenue (US$ millions) |
---|---|---|
Nippon Mektron | Japan | $4,028 |
Unimicron Technology | Taiwan | $3,749 |
Zhen Ding Tech | Taiwan | $3,472 |
Tripod Technology | Taiwan | $3,115 |
Ibiden | Japan | $2,987 |
These top PCB manufacturers operate dozens of factories around the world and serve a diverse customer base across consumer electronics, telecommunications, automotive, industrial, and other industries.
Some other major global PCB manufacturers include AT&S (Austria), TTM Technologies (US), Shennan Circuits (China), Compeq (Taiwan), WUS Printed Circuit (China), Kinwong (Hong Kong), and Shinko Electric (Japan).
Capabilities of Leading PCB Manufacturers
The top PCB manufacturers have continued investing in their capabilities and capacities to meet rising demand and serve a broad range of end markets. Here are some of the key capabilities of these global leaders:
Advanced PCB Technologies
- HDI PCBs – High density interconnect (HDI) PCBs enable miniaturization and higher component density. They have fine lines/spaces (<100 μm), microvias, and often incorporate blind and buried vias.
- Rigid-flex PCBs – Rigid-flex PCBs combine rigid and flexible materials in a single board. They allow 3D design flexibility and miniaturization.
- IC substrates – IC substrates are used in semiconductor packaging. Main PCB suppliers also manufacture these high-precision substrates.
- High frequency PCBs – These boards support high-speed signals for RF, microwave, and other applications. They require specialized dielectric materials.
- Metal core PCBs – These boards use a metal core substrate for enhanced thermal performance. Key for LED lighting and power electronics.
Scaling Production
- High-volume SMT assembly – Top PCB manufacturers operate large-scale SMT lines to support high-volume PCB assembly needs.
- Automation – They utilize automation in manufacturing processes for optimal productivity and precision.
- Global production network – Multiple manufacturing sites around the world located close to key customer hubs.
- Vertically integrated – Many firms are backward integrated into raw materials and forwards into electronics assembly.
Quality Systems
- ISO-certified – Globally recognized quality management certification is maintained.
- IATF 16949 certified – This automotive-specific quality system certification is held by major suppliers.
- Testing/inspection – Rigorous testing and inspection methodologies ensure quality and reliability.
- RoHS/REACH compliance – Manufacturing processes meet hazardous substance regulations.
Factors in Selecting a PCB Manufacturer
Choosing the right PCB partner is critical to any electronics project. Here are some key factors to evaluate manufacturers on:
- Technical capabilities – Assess if the supplier has done similar projects and has the equipment, expertise, and quality systems needed for your PCB production.
- Capacity – Choose a manufacturing partner with available production capacity and flexibility to meet your volume needs.
- Location – Determine if the location enables responsive communication and efficient logistics to your operations.
- Cost – Get accurate pricing that strikes the right balance of cost and capabilities. Check for hidden costs.
- Quality – Review quality certifications, process controls, test capabilities, and past performance to minimize defects.
- Service – Gauge responsiveness in communication, design support capabilities, and change management flexibility.
- Delivery – Ensure manufacturing lead times, on-time delivery rates, and logistics reliability meet your schedule needs.
By examining these aspects, you can find the right PCB partner to produce your boards affordably, reliably, and on time.
Trends Shaping the Global PCB Market
Several trends are impacting PCB manufacturers and ushering new opportunities:
Miniaturization
Devices continue to shrink, driving demand for HDI PCBs, flexible PCBs, and advanced packaging. High density interconnects require finer features and thinner materials.
5G Infrastructure
5G is spurring sizeable investments in telecom infrastructure and RF PCBs to enable faster data rates. This drives demand for high-frequency PCBs.
Automotive Electronics
Vehicles are incorporating more electronics for connectivity, safety, and electrification. Automotive PCB production requires stringent quality standards.
IoT Growth
Proliferation of connected devices as part of the Internet of Things leads to high-mix, lower-volume PCB production.
Smart Factory Investment
Manufacturers are adopting Industry 4.0 solutions for automation, data exchange, and production monitoring to optimize efficiency.
Sustainability
PCB companies are taking steps to enhance energy efficiency, reduce emissions, and utilize greener chemistries as part of sustainability initiatives.
Frequently Asked Questions
What are the key benefits of using a top global PCB manufacturer?
Choosing one of the leading global PCB manufacturers provides several advantages:
- Access to advanced manufacturing capabilities and the latest technologies
- High-volume production capacity for lower costs through economies of scale
- Multiple production facilities to provide regional manufacturing support
- Established quality systems and process controls for reliability
- Experience supporting complex, high-tech PCB applications
- Financial stability to invest in capabilities and capacity
How is the PCB industry being impacted by the rise of electric vehicles (EVs)?
The fast growth in electric vehicles is positively influencing the PCB industry. EVs contain significantly more electronics for battery management, power conversion, and motor control. This leads to greater PCB content per vehicle. PCBs for EVs require high reliability and thermal performance. Demand for metal core PCBs is increasing accordingly.
What new PCB technologies are emerging for advanced applications?
Some newer PCB technologies include:
- Embedded die technology – Chips or components are embedded within the PCB for improved performance.
- Higher frequency materials – New dielectric materials enable PCB signal transmission above 100 GHz.
- Flex-rigid-flex PCBs – Allow integration of multiple rigid and flexible substrates into a single package.
- Stretchable circuits – Screens printed on flexible materials that can stretch and morph while maintaining conductivity.
How is 5G driving changes in PCB fabrication and design?
5G’s high frequencies and bandwidths require PCBs with precise impedance control, low loss, and consistent performance at high speeds. Key design aspects include:
- Tight laminate thickness and dielectric tolerance
- Minimal signal loss materials
- Tightly coupled differential signals
- Impedance control throughout signal path
- Dense component layouts
- Thermal management
Advanced PCB processes like laser direct imaging (LDI) enable the fine features and tolerances needed.
What key innovations are improving PCB manufacturing efficiency?
- Direct imaging for faster throughput and precise small features
- Increased automation in assembly and inspection
- Advanced data analytics to optimize production
- Additive processes like inkjet printing to eliminate etching
- Virtual prototyping using simulations and 3D models
- Seamless design-to-manufacturing data transfer
- Supply chain integration for just-in-time material delivery
These innovations help streamline processes, reduce defects, improve precision, and provide greater manufacturing flexibility.
Leave a Reply