1. Choose the Right PCB Manufacturer
Choosing the right PCB manufacturer is the first and most important step in ensuring PCB Assembly success. Look for a manufacturer with experience in your industry, a proven track record of quality, and the ability to meet your specific needs.
Factors to Consider When Choosing a PCB Manufacturer
Factor | Description |
---|---|
Experience | Look for a manufacturer with experience in your industry and with the specific type of PCB you need. |
Quality | Check the manufacturer’s quality certifications and ask for references from previous clients. |
Capabilities | Make sure the manufacturer has the capabilities to meet your specific needs, such as the ability to handle high-volume orders or quick turnaround times. |
Communication | Choose a manufacturer with good communication skills and a willingness to work closely with you throughout the process. |
2. Design for Manufacturability
Designing your PCB with manufacturability in mind can help ensure a smooth and successful assembly process. This means considering factors such as component placement, trace width, and hole size.
Tips for Designing for Manufacturability
- Keep component placement in mind, ensuring that components are spaced appropriately and oriented correctly.
- Use appropriate trace widths and spacing to ensure proper signal integrity and to avoid manufacturing issues.
- Ensure that hole sizes are appropriate for the components being used and for the manufacturing process.
- Avoid using unnecessarily small components or tight tolerances that may be difficult to manufacture.
3. Use High-Quality Components
Using high-quality components is essential for ensuring the reliability and longevity of your PCB. Cheap or counterfeit components can lead to failures and other issues down the line.
Risks of Using Low-Quality Components
- Increased risk of component failure
- Reduced reliability and longevity of the final product
- Potential safety hazards
- Damage to the reputation of the manufacturer and the end customer
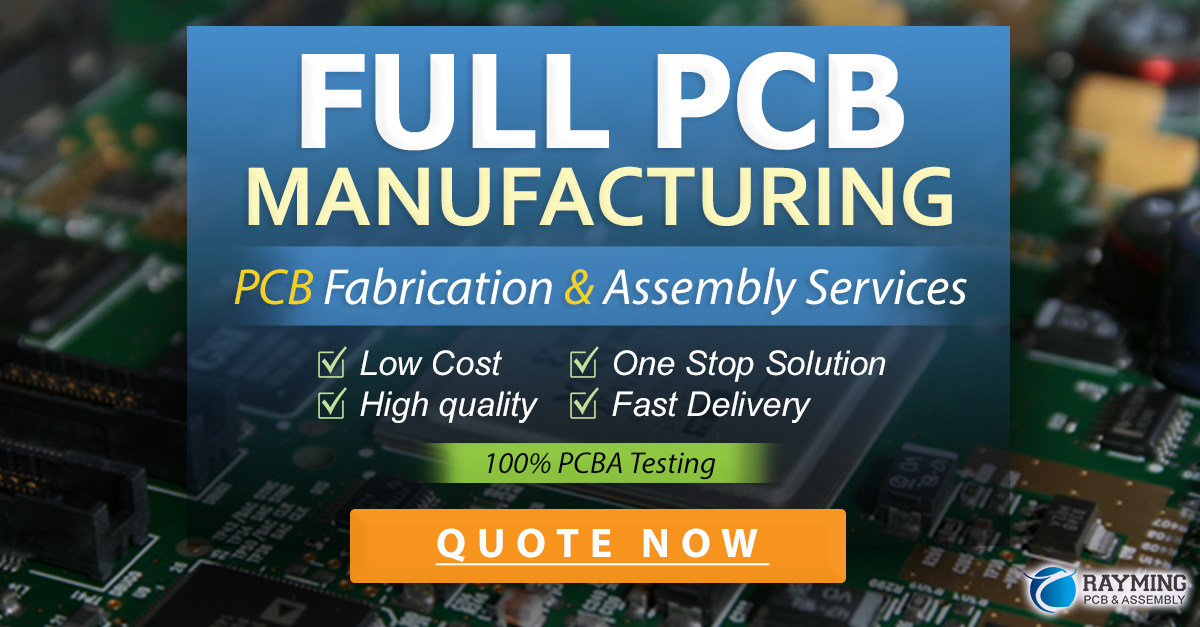
4. Conduct Thorough Testing
Conducting thorough testing throughout the PCB assembly process can help identify and address issues early on, before they become major problems. This includes testing individual components, sub-assemblies, and the final product.
Types of Testing to Consider
- In-circuit testing (ICT)
- Functional testing
- Boundary scan testing
- Burn-in testing
- Environmental testing
5. Use Automated Assembly Processes
Using automated assembly processes can help improve the speed, accuracy, and consistency of PCB assembly. This includes processes such as surface mount technology (SMT) and automated optical inspection (AOI).
Benefits of Automated Assembly Processes
- Increased speed and efficiency
- Improved accuracy and consistency
- Reduced human error
- Ability to handle high-volume orders
6. Implement Quality Control Measures
Implementing quality control measures throughout the PCB assembly process can help ensure that the final product meets the required specifications and standards. This includes measures such as visual inspection, electrical testing, and X-ray inspection.
Quality Control Measures to Consider
- Visual inspection
- Automated optical inspection (AOI)
- X-ray inspection
- Electrical testing
- Functional testing
7. Use Proper Handling and Storage Techniques
Proper handling and storage of PCBs and components is essential for ensuring their quality and reliability. This includes using appropriate packaging materials, maintaining proper storage conditions, and following proper handling procedures.
Tips for Proper Handling and Storage
- Use appropriate packaging materials, such as anti-static bags and foam
- Maintain proper storage conditions, such as temperature and humidity control
- Follow proper handling procedures, such as using gloves and avoiding touching the surface of the PCB
- Implement a first-in, first-out (FIFO) inventory system to ensure that older components are used first
8. Monitor and Control the Assembly Environment
Monitoring and controlling the assembly environment can help ensure that the PCB assembly process is conducted under optimal conditions. This includes factors such as temperature, humidity, and air quality.
Environmental Factors to Monitor and Control
Factor | Optimal Range |
---|---|
Temperature | 68-77°F (20-25°C) |
Humidity | 30-50% RH |
Air Quality | Class 100,000 or better |
9. Use Reliable Soldering Techniques
Using reliable soldering techniques is essential for ensuring the quality and reliability of the final product. This includes using appropriate soldering temperatures, using the right type of solder, and following proper soldering procedures.
Soldering Techniques to Consider
- Wave soldering
- Reflow soldering
- Selective soldering
- Hand soldering
Tips for Reliable Soldering
- Use appropriate soldering temperatures for the specific components and PCB material
- Use the right type of solder, such as lead-free or leaded solder
- Follow proper soldering procedures, such as pre-heating and cooling
- Inspect solder joints visually and with X-ray to ensure quality
10. Continuously Improve Processes
Continuously improving PCB assembly processes can help ensure ongoing success and competitiveness. This includes implementing lean manufacturing principles, conducting root cause analysis of issues, and investing in new technologies and equipment.
Steps for Continuous Improvement
- Implement lean manufacturing principles, such as 5S and Kaizen
- Conduct root cause analysis of issues to identify and address underlying problems
- Invest in new technologies and equipment to improve efficiency and quality
- Provide ongoing training and education for employees to keep skills up-to-date
FAQ
1. What is the difference between through-hole and surface mount PCB assembly?
Through-hole PCB assembly involves inserting component leads through holes drilled in the PCB and soldering them in place on the opposite side. Surface mount PCB assembly involves placing components directly onto pads on the surface of the PCB and soldering them in place.
2. What is the purpose of using solder paste in PCB assembly?
Solder paste is used in surface mount PCB assembly to temporarily hold components in place before soldering. The paste contains tiny solder particles suspended in flux, which helps to clean and prepare the surfaces for soldering.
3. What is the role of a pick-and-place machine in PCB assembly?
A pick-and-place machine is used in surface mount PCB assembly to automatically place components onto the PCB. The machine uses a vacuum nozzle to pick up components from a feeder and place them onto the PCB with high precision and speed.
4. What is the purpose of using a stencil in PCB assembly?
A stencil is used in surface mount PCB assembly to apply solder paste to the pads on the PCB. The stencil is a thin metal sheet with openings that match the pads on the PCB. Solder paste is applied through the openings onto the pads, ensuring a precise and consistent amount of paste is applied.
5. What is the difference between lead-free and leaded solder?
Lead-free solder is a type of solder that does not contain lead, which is a toxic substance. Leaded solder, on the other hand, contains a small amount of lead. Lead-free solder is now widely used in PCB assembly due to regulations restricting the use of lead in electronic products.
Conclusion
PCB assembly is a complex process that requires careful planning, attention to detail, and ongoing improvement. By following the top 10 tips outlined in this article, manufacturers can ensure the success of their PCB assembly projects and deliver high-quality products to their customers. From choosing the right PCB manufacturer to implementing quality control measures and continuously improving processes, each step plays a critical role in achieving PCB assembly success.
Leave a Reply