What is an Anti-reflective soldermask?
An anti-reflective soldermask, also known as a black soldermask, is a type of coating applied to printed circuit boards (PCBs) to reduce light reflection and improve the overall aesthetics of the board. This soldermask is particularly useful in applications where light reflection from the PCB surface could interfere with the proper functioning of the device or negatively impact its appearance.
Composition and properties of anti-reflective soldermasks
Anti-reflective soldermasks are typically composed of epoxy-based materials that are formulated to absorb light rather than reflect it. These materials often contain black pigments, such as carbon black or other dark pigments, which give the soldermask its characteristic black color.
The key properties of an anti-reflective soldermask include:
-
Low reflectivity: The primary purpose of an anti-reflective soldermask is to minimize light reflection from the PCB surface. This is achieved through the use of dark pigments and special formulations that absorb incoming light.
-
Durability: Anti-reflective soldermasks must be able to withstand the harsh conditions encountered during PCB manufacturing and assembly processes, as well as the operating environment of the final product.
-
Electrical insulation: Like other types of soldermasks, anti-reflective soldermasks provide electrical insulation between the copper traces on the PCB, preventing short circuits and ensuring proper functioning of the device.
-
Compatibility with various surface finishes: Anti-reflective soldermasks should be compatible with common PCB surface finishes, such as HASL (Hot Air Solder Leveling), ENIG (Electroless Nickel Immersion Gold), and OSP (Organic Solderability Preservative).
Applications of anti-reflective soldermasks
Anti-reflective soldermasks are used in a wide range of applications where light reflection from the PCB surface could cause issues. Some of the most common applications include:
Optical devices
In optical devices, such as cameras, scanners, and displays, light reflection from the PCB can interfere with the proper functioning of the device. For example, in a digital camera, light reflecting off the PCB could cause glare or unwanted artifacts in the captured image. By using an anti-reflective soldermask, these issues can be minimized, ensuring optimal performance of the optical device.
Automotive electronics
Modern vehicles are equipped with numerous electronic systems, including displays, sensors, and control modules. In these applications, light reflection from the PCBs can cause readability issues with displays or interfere with the operation of light-sensitive sensors. Anti-reflective soldermasks help to mitigate these problems, ensuring reliable performance of automotive electronic systems.
Medical devices
Medical devices, such as patient monitors, imaging equipment, and diagnostic tools, often incorporate PCBs with light-sensitive components. Light reflection from the PCB surface can interfere with the accurate operation of these components, potentially leading to incorrect readings or diagnoses. By using anti-reflective soldermasks, medical device manufacturers can ensure the reliability and accuracy of their products.
Consumer electronics
In consumer electronics, such as smartphones, tablets, and laptops, the aesthetic appeal of the device is often just as important as its functionality. Anti-reflective soldermasks can help to create a sleek, professional appearance by eliminating unsightly light reflection from the PCB surface. This is particularly important in devices with transparent or translucent enclosures, where the PCB is visible to the user.
Advantages of using anti-reflective soldermasks
Using an anti-reflective soldermask offers several advantages over traditional green or other colored soldermasks:
-
Improved device performance: By minimizing light reflection, anti-reflective soldermasks can help to improve the performance of light-sensitive components and ensure the proper functioning of the device.
-
Enhanced aesthetics: The black color of anti-reflective soldermasks creates a professional, high-tech appearance that can enhance the perceived quality and value of the end product.
-
Reduced eye strain: In devices with displays, such as smartphones and laptops, light reflection from the PCB can cause eye strain and fatigue. Anti-reflective soldermasks help to reduce this effect, providing a more comfortable user experience.
-
Better contrast and readability: In devices with displays, anti-reflective soldermasks can improve the contrast and readability of the display by reducing glare and reflections.
-
Compatibility with various surface finishes: Anti-reflective soldermasks are compatible with a wide range of PCB surface finishes, making them a versatile choice for many applications.
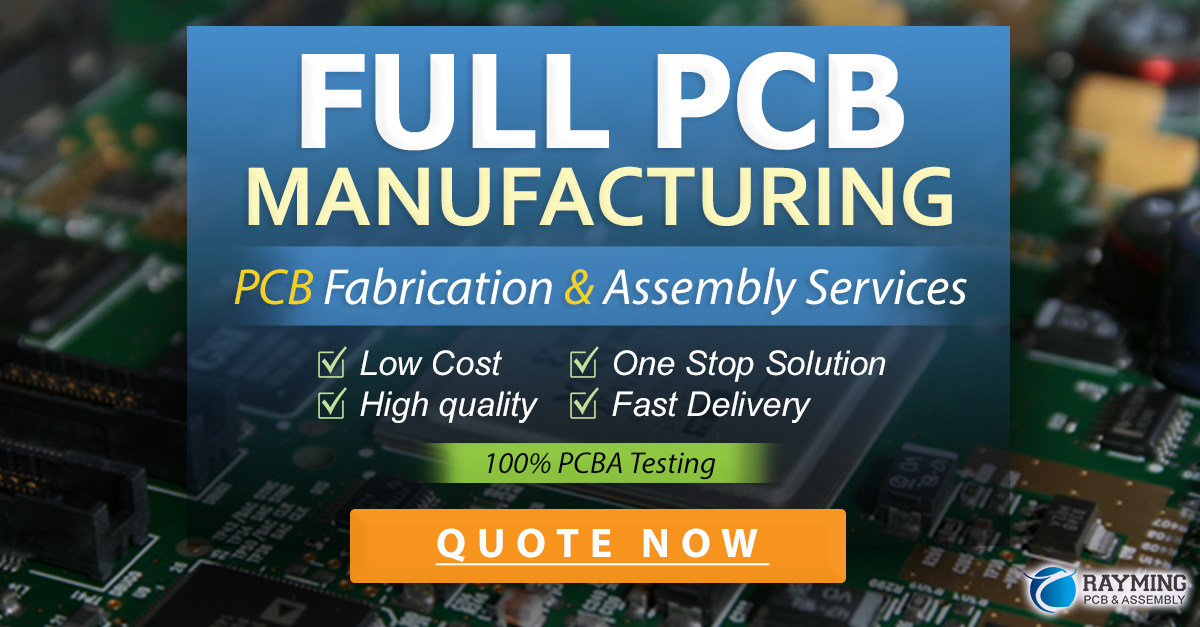
Challenges and considerations
While anti-reflective soldermasks offer numerous benefits, there are some challenges and considerations to keep in mind when using them:
-
Cost: Anti-reflective soldermasks may be more expensive than traditional green or other colored soldermasks due to the special formulations and pigments used in their manufacture.
-
Processing requirements: Applying an anti-reflective soldermask may require specialized equipment or processing steps, which can increase production costs and lead times.
-
Inspection challenges: The black color of anti-reflective soldermasks can make it more difficult to visually inspect the PCB for defects or issues during the manufacturing process. This may require the use of specialized inspection equipment or techniques.
-
Compatibility with other components: In some cases, the black color of anti-reflective soldermasks may not be compatible with certain components or materials used in the device. This should be carefully considered during the design and material selection process.
Conclusion
Anti-reflective soldermasks, also known as black soldermasks, are a valuable tool for reducing light reflection and improving the performance and aesthetics of PCBs in a wide range of applications. By understanding the properties, advantages, and challenges associated with anti-reflective soldermasks, engineers and designers can make informed decisions when selecting materials for their projects.
As technology continues to advance, the demand for anti-reflective soldermasks is likely to grow, driven by the increasing complexity and sensitivity of electronic devices. By staying up-to-date with the latest developments in soldermask technology, manufacturers can ensure that their products meet the highest standards of performance, reliability, and aesthetic appeal.
Frequently Asked Questions (FAQ)
-
What is the primary purpose of an anti-reflective soldermask?
The primary purpose of an anti-reflective soldermask is to minimize light reflection from the surface of a printed circuit board (PCB). This helps to improve the performance of light-sensitive components and enhance the overall aesthetics of the device. -
What are some common applications for anti-reflective soldermasks?
Anti-reflective soldermasks are commonly used in optical devices, automotive electronics, medical devices, and consumer electronics. They are particularly useful in applications where light reflection from the PCB could interfere with the proper functioning of the device or negatively impact its appearance. -
How do anti-reflective soldermasks differ from traditional green soldermasks?
Anti-reflective soldermasks are formulated using special epoxy-based materials and dark pigments, such as carbon black, to absorb light rather than reflect it. Traditional green soldermasks, on the other hand, do not have these light-absorbing properties and may reflect more light from the PCB surface. -
Are there any challenges associated with using anti-reflective soldermasks?
Yes, some challenges associated with using anti-reflective soldermasks include potentially higher costs due to specialized formulations and pigments, additional processing requirements, difficulties in visual inspection due to the black color, and possible compatibility issues with certain components or materials. -
What are the key properties of an anti-reflective soldermask?
The key properties of an anti-reflective soldermask include low reflectivity, durability, electrical insulation, and compatibility with various PCB surface finishes. These properties ensure that the soldermask can effectively minimize light reflection while providing the necessary protection and functionality for the PCB.
Article length: 1131 words.
Leave a Reply