What is Surface Mount PCB Assembly?
Surface mount PCB assembly, also known as SMPCBAC, is a modern manufacturing process used to attach electronic components directly onto the surface of a printed circuit board (PCB). This technology has revolutionized the electronics industry by enabling the production of smaller, faster, and more reliable electronic devices.
In contrast to through-hole mounting, where component leads are inserted into drilled holes and soldered on the opposite side of the board, surface mount components are placed directly on top of the PCB and soldered in place. This process allows for greater component density, improved performance, and reduced manufacturing costs.
Advantages of Surface Mount PCB Assembly
- Miniaturization: SMPCBAC allows for smaller components and tighter spacing, resulting in more compact electronic devices.
- Increased reliability: Surface mount components have shorter leads and are more securely attached to the PCB, reducing the risk of mechanical and thermal stress.
- Faster assembly: Automated pick-and-place machines can quickly populate PCBs with surface mount components, increasing production speed and efficiency.
- Cost-effectiveness: Higher component density and automated assembly processes lead to reduced material and labor costs.
- Improved performance: Shorter lead lengths and reduced parasitic capacitance and inductance contribute to improved electrical performance and higher frequency capabilities.
The Surface Mount PCB Assembly Process
The SMPCBAC process involves several key steps to ensure proper component placement and soldering. These steps include:
1. Solder Paste Application
Solder paste, a mixture of tiny solder particles suspended in flux, is applied to the PCB’s surface using a stencil or screen printing process. The stencil ensures that the solder paste is deposited precisely on the component pads.
2. Component Placement
Surface mount components are placed onto the solder paste-coated pads using automated pick-and-place machines. These machines use vacuum nozzles or grippers to pick up components from tape reels or trays and place them accurately on the PCB.
3. Reflow Soldering
After component placement, the PCB undergoes a reflow soldering process. The board is passed through a reflow oven, which heats the solder paste to its melting point. As the solder melts, it forms a strong mechanical and electrical bond between the component leads and the PCB pads.
4. Inspection and Testing
Following the reflow soldering process, the assembled PCBs are inspected for defects using automated optical inspection (AOI) systems or manual visual inspection. Electrical testing is also performed to ensure proper functionality and adherence to specifications.
Choosing a Surface Mount PCB Assembly Company
When selecting an SMPCBAC partner, consider the following factors to ensure a successful collaboration:
- Technical capabilities: Ensure the company has experience with your specific product requirements, such as PCB complexity, component types, and manufacturing volumes.
- Quality control: Look for companies with robust quality management systems, such as ISO 9001 certification, and strict adherence to IPC standards.
- Manufacturing capacity: Consider the company’s production capacity and lead times to ensure they can meet your demand and delivery schedules.
- Customer support: Choose a partner that offers responsive communication, technical support, and a dedication to customer satisfaction.
- Cost-effectiveness: Compare pricing and value-added services among potential partners to find the best balance between cost and quality.
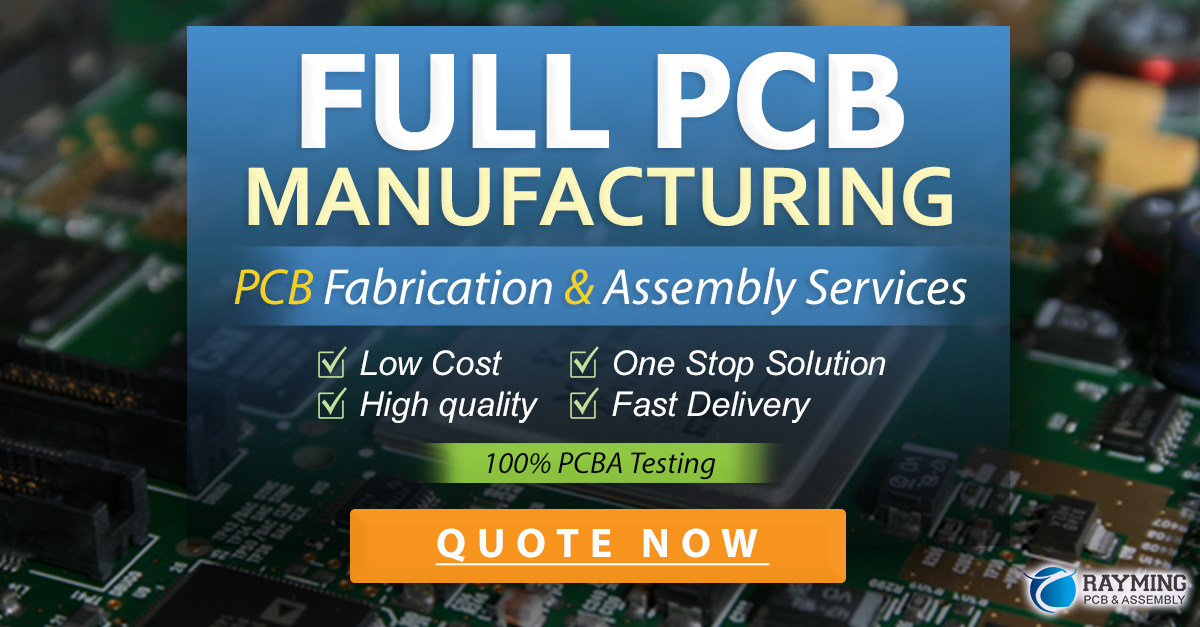
Top Surface Mount PCB Assembly Companies
Company | Location | Specialties | Certifications |
---|---|---|---|
Foxconn | Taiwan, China | High-volume manufacturing, consumer electronics | ISO 9001, ISO 14001, IATF 16949 |
Jabil | USA, global presence | Medical devices, automotive, aerospace | ISO 9001, ISO 13485, AS9100 |
Flex | USA, global presence | Industrial, automotive, healthcare | ISO 9001, ISO 14001, IATF 16949 |
Celestica | Canada, global presence | Aerospace, defense, healthcare | ISO 9001, AS9100, ISO 13485 |
Sanmina | USA, global presence | Medical, industrial, automotive | ISO 9001, ISO 13485, IATF 16949 |
These companies represent just a few of the many reputable SMPCBAC providers worldwide. When evaluating potential partners, be sure to consider your specific requirements and conduct thorough research to find the best fit for your business.
Frequently Asked Questions (FAQ)
1. What is the difference between surface mount and Through-hole PCB assembly?
Surface mount PCB assembly involves placing components directly onto the surface of the PCB, while through-hole assembly requires inserting component leads into drilled holes and soldering them on the opposite side of the board. Surface mount technology allows for smaller components, higher density, and faster assembly compared to through-hole mounting.
2. Can surface mount and through-hole components be used on the same PCB?
Yes, it is possible to use both surface mount and through-hole components on the same PCB. This is called a mixed-technology or hybrid assembly. However, the assembly process becomes more complex and may require additional steps, such as wave soldering for through-hole components after the surface mount reflow process.
3. What is the smallest component size that can be used in surface mount PCB assembly?
The smallest surface mount components are known as 01005 packages, measuring just 0.4mm x 0.2mm. However, these ultra-small components require advanced assembly equipment and specialized handling techniques. More commonly used small components include 0201 (0.6mm x 0.3mm) and 0402 (1.0mm x 0.5mm) packages.
4. How do I ensure the quality of my surface mount PCB assembly?
To ensure the quality of your SMPCBAC, work with a reputable assembly partner that adheres to industry standards such as IPC-A-610. Implement a comprehensive quality management system that includes incoming material inspection, process control, and post-assembly testing. Regularly audit your assembly partner and maintain open communication to address any quality concerns promptly.
5. What is the typical turnaround time for surface mount PCB assembly?
Turnaround times for SMPCBAC vary depending on factors such as PCB complexity, component availability, and manufacturing volume. For small to medium-sized orders, typical turnaround times range from 5 to 15 working days. However, expedited services may be available for urgent projects, while larger orders may require longer lead times. Consult with your assembly partner to establish a suitable timeline for your specific needs.
Conclusion
Surface mount PCB assembly has become the dominant technology in the electronics manufacturing industry, enabling the production of smaller, faster, and more reliable devices. By understanding the SMPCBAC process and carefully selecting a trusted assembly partner, businesses can leverage this technology to bring their innovative products to market efficiently and cost-effectively.
As the demand for advanced electronic devices continues to grow, the importance of surface mount PCB assembly will only increase. By staying informed about the latest developments in SMPCBAC technology and best practices, companies can remain competitive and deliver high-quality products to their customers.
Leave a Reply