Understanding the Basics of PCB Design
Before diving into the specifIC Guidelines, it’s essential to understand the basics of PCB design. A PCB is a flat board made of insulating material, such as fiberglass or plastic, with conductive copper traces etched onto its surface. These traces connect various electronic components, such as resistors, capacitors, and Integrated Circuits (ICs), to form a complete circuit.
PCBs can be single-sided, double-sided, or multi-layered, depending on the complexity of the circuit and the space constraints. The designer must consider factors such as component placement, trace routing, power distribution, signal integrity, and manufacturability while creating the PCB layout.
Guideline 1: Plan Your PCB Layout
Define the PCB Requirements
Before starting the PCB design, clearly define the requirements of your project. Consider the following factors:
- The purpose and functionality of the PCB
- The size and shape constraints
- The number of layers required
- The components to be used and their package types
- The power requirements and distribution
- The signal integrity and EMI/EMC considerations
- The manufacturing process and cost constraints
Create a Block Diagram
A block diagram is a high-level representation of the PCB’s functional blocks and their interconnections. It helps in visualizing the overall system architecture and identifying the critical subsystems. The block diagram should include:
- The main functional blocks (e.g., power supply, microcontroller, sensors, etc.)
- The interfaces between the blocks (e.g., I2C, SPI, UART, etc.)
- The power distribution and ground connections
- The input/output connectors and their pinouts
Component Placement
Proper component placement is crucial for optimizing the PCB layout and minimizing the trace lengths. Follow these guidelines:
- Place the components logically based on their functional blocks
- Keep the critical components close to each other to minimize trace lengths
- Consider the Component orientation for easy assembly and testing
- Leave sufficient space between components for routing and manufacturing
- Place the decoupling capacitors close to the power pins of ICs
- Keep the sensitive analog components away from noisy digital components
Guideline 2: Design for Signal Integrity
Trace Routing
Proper trace routing is essential for maintaining signal integrity and minimizing crosstalk and EMI. Follow these guidelines:
- Keep the traces as short and direct as possible
- Avoid sharp corners and use 45-degree angles for trace bends
- Maintain a consistent trace width based on the current carrying capacity
- Use appropriate trace spacing to minimize crosstalk
- Route the high-speed signals first and keep them away from other traces
- Use ground planes to provide a low-impedance return path for signals
- Consider the trace impedance matching for high-speed signals
Power Distribution
Proper power distribution is critical for ensuring stable and clean power supply to all components. Follow these guidelines:
- Use separate power planes for analog and digital circuits
- Provide sufficient copper pour for power and ground planes
- Use appropriate decoupling capacitors close to the power pins of ICs
- Use power and ground planes to minimize the loop area and reduce EMI
- Consider the current carrying capacity of traces and vias
- Use star routing or split power planes for sensitive analog circuits
Grounding
Proper grounding is essential for minimizing noise and ensuring signal integrity. Follow these guidelines:
- Use a single ground plane for the entire PCB, if possible
- Connect all ground pins of ICs to the ground plane using short traces or vias
- Avoid splitting the ground plane, unless necessary for isolation
- Use ground stitching vias to connect ground planes on different layers
- Keep the analog and digital grounds separate and connect them at a single point
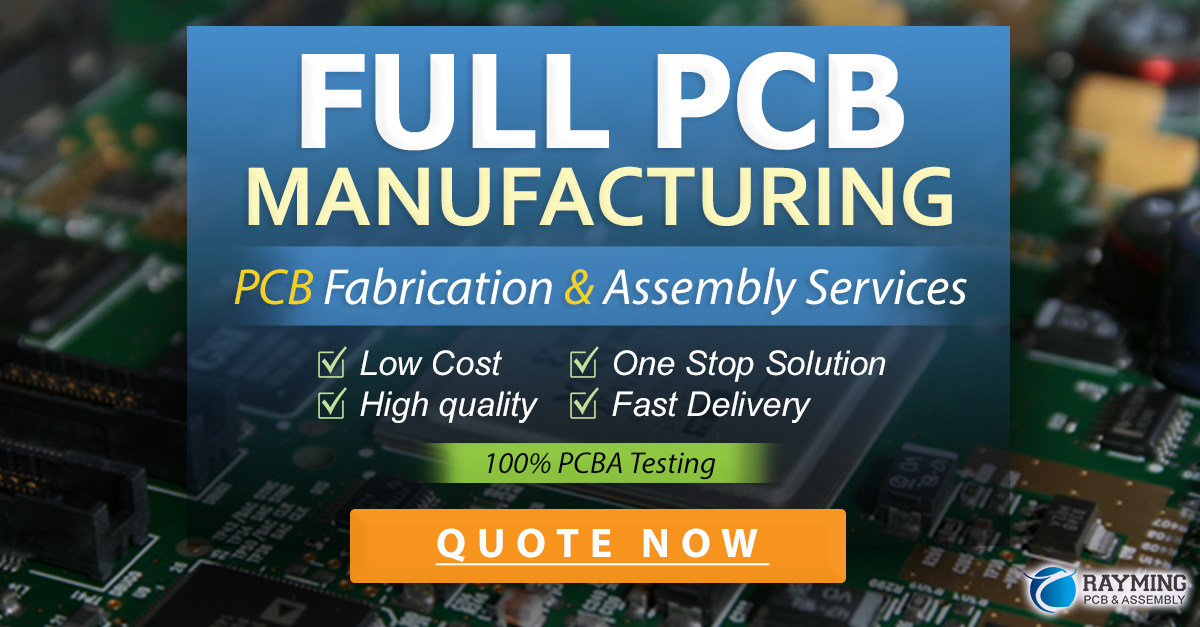
Guideline 3: Consider Manufacturability
Design for Assembly (DFA)
Designing for easy assembly can reduce manufacturing costs and improve the reliability of the PCB. Follow these guidelines:
- Use standard component packages and footprints
- Provide sufficient clearance around components for pick-and-place machines
- Avoid placing components too close to the PCB edges
- Use fiducials for accurate component placement
- Consider the orientation of components for easy assembly and soldering
- Use Surface Mount Devices (SMDs) whenever possible
Design for Testability (DFT)
Designing for testability can simplify the debugging and repair process of the PCB. Follow these guidelines:
- Provide test points for critical signals and power supplies
- Use boundary scan (JTAG) for testing complex ICs
- Provide sufficient clearance around test points for probing
- Consider the accessibility of components for manual testing and repair
- Use self-diagnostic features, such as LEDs or test signals, for easy troubleshooting
Design for Manufacturing (DFM)
Designing for manufacturability can reduce the production costs and improve the yield of the PCB. Follow these guidelines:
- Use standard PCB sizes and shapes
- Avoid using very small or very large components
- Provide sufficient spacing between components and traces for etching and soldering
- Use appropriate solder mask and silkscreen for component identification and protection
- Consider the minimum hole size and drill bit size for through-hole components
- Use appropriate copper weight and thickness for the PCB
- Follow the manufacturer’s design rules and guidelines
Guideline 4: Document and Review Your Design
Schematic Design
A well-organized and properly annotated schematic is essential for understanding the circuit and troubleshooting any issues. Follow these guidelines:
- Use meaningful and consistent component designators and labels
- Provide clear and concise notes and comments for important information
- Use appropriate symbols and footprints for components
- Group related components and circuits together
- Use appropriate net names and labels for signals
- Perform a design rule check (DRC) to catch any errors or inconsistencies
PCB Layout
A well-documented and properly formatted PCB layout is essential for manufacturing and assembly. Follow these guidelines:
- Use appropriate layer stackup and color codes
- Provide clear and concise notes and comments for important information
- Use appropriate silkscreen and solder mask for component identification and protection
- Provide a comprehensive Bill of Materials (BOM) with component details
- Generate Gerber files and drill files for manufacturing
- Perform a design rule check (DRC) to catch any errors or violations
Design Review
Conducting a thorough design review can catch any issues or improvements before the PCB goes into production. Follow these guidelines:
- Review the schematic and PCB layout with other engineers or experts
- Check for any design rule violations or inconsistencies
- Verify the component placement, orientation, and footprints
- Check the power distribution and grounding scheme
- Verify the signal integrity and EMI/EMC considerations
- Consider the manufacturability, assembly, and testability aspects
- Incorporate any feedback and suggestions from the review process
FAQs
-
What is the importance of a well-designed PCB?
A well-designed PCB ensures the proper functioning, reliability, and manufacturability of the electronic product. It minimizes signal integrity issues, reduces EMI/EMC problems, and simplifies the assembly and testing process, ultimately leading to a higher-quality and cost-effective product. -
What are the key factors to consider while planning a PCB layout?
The key factors to consider while planning a PCB layout include: - The purpose and functionality of the PCB
- The size and shape constraints
- The number of layers required
- The components to be used and their package types
- The power requirements and distribution
- The signal integrity and EMI/EMC considerations
-
The manufacturing process and cost constraints
-
How can I ensure proper signal integrity in my PCB design?
To ensure proper signal integrity in your PCB design, follow these guidelines: - Keep the traces as short and direct as possible
- Avoid sharp corners and use 45-degree angles for trace bends
- Maintain a consistent trace width based on the current carrying capacity
- Use appropriate trace spacing to minimize crosstalk
- Route the high-speed signals first and keep them away from other traces
- Use ground planes to provide a low-impedance return path for signals
-
Consider the trace impedance matching for high-speed signals
-
What are some best practices for designing a manufacturable PCB?
Some best practices for designing a manufacturable PCB include: - Use standard component packages and footprints
- Provide sufficient clearance around components for pick-and-place machines
- Avoid placing components too close to the PCB edges
- Use fiducials for accurate component placement
- Consider the orientation of components for easy assembly and soldering
- Use surface mount devices (SMDs) whenever possible
-
Follow the manufacturer’s design rules and guidelines
-
Why is it important to document and review the PCB design?
Documenting and reviewing the PCB design is important for several reasons: - It helps in understanding the circuit and troubleshooting any issues
- It ensures that the design is free of errors and inconsistencies
- It verifies that the design meets the requirements and constraints
- It improves the manufacturability and assembly of the PCB
- It facilitates communication and collaboration among the design team and stakeholders
- It serves as a reference for future modifications and iterations of the design
By following these PCB Design Guidelines and best practices, you can create high-quality, reliable, and manufacturable PCBs that meet your project requirements and exceed customer expectations. Remember to plan your layout carefully, design for signal integrity and manufacturability, document your design thoroughly, and conduct design reviews to catch any issues early in the development process.
Leave a Reply