What is Solder?
Solder is a metal alloy that typically consists of tin (Sn) and lead (Pb) in varying proportions. The most common solder alloy is Sn63Pb37, which contains 63% tin and 37% lead by weight. However, due to environmental and health concerns associated with lead, lead-free solder alloys have gained popularity in recent years.
Solder has a relatively low melting point compared to the metals it joins. When heated above its melting point, solder becomes a liquid and flows into the joint, creating a strong bond as it cools and solidifies. The melting point of solder varies depending on its composition, with eutectic alloys having a specific melting point and non-eutectic alloys having a melting range.
Solder Classification
Solder can be classified based on various factors, including composition, melting point, application, and form factor. Let’s explore each classification in detail.
Classification by Composition
Lead-based Solder
Traditionally, lead-based solder alloys were widely used due to their excellent wetting properties, low melting point, and good electrical conductivity. The most common lead-based solder alloys include:
- Sn63Pb37 (63% tin, 37% lead)
- Sn60Pb40 (60% tin, 40% lead)
- Sn62Pb36Ag2 (62% tin, 36% lead, 2% silver)
However, the use of lead-based solder has been restricted or banned in many countries due to environmental and health concerns. The European Union’s Restriction of Hazardous Substances (RoHS) directive and similar regulations have led to the adoption of lead-free solder alloys.
Lead-free Solder
Lead-free solder alloys have been developed as an alternative to lead-based solder. These alloys typically contain tin (Sn) as the primary component, along with other elements such as silver (Ag), copper (Cu), bismuth (Bi), and indium (In). Some common lead-free solder alloys include:
- Sn96.5Ag3.0Cu0.5 (SAC305)
- Sn99.3Cu0.7 (Sn99.3)
- Sn96.5Ag3.5 (Sn96.5)
- Sn42Bi58 (Sn42)
Lead-free solder alloys have different melting points, wetting properties, and mechanical characteristics compared to lead-based solder. They often require higher soldering temperatures and may have different joint reliability and appearance.
Classification by Melting Point
Solder can also be classified based on its melting point or melting range. The melting point is a critical factor in determining the suitable soldering temperature and the compatibility of solder with the materials being joined.
Eutectic Solder
Eutectic solder alloys have a specific melting point at which the solid phase transforms directly into the liquid phase without a pasty range. Eutectic solder alloys have excellent wetting properties and form strong, reliable joints. Examples of eutectic solder alloys include:
- Sn63Pb37 (melting point: 183°C)
- Sn42Bi58 (melting point: 138°C)
Non-eutectic Solder
Non-eutectic solder alloys have a melting range, where the solid and liquid phases coexist over a temperature range. The melting range is defined by the liquidus and solidus temperatures. Non-eutectic solder alloys may have a pasty range during soldering, which can affect joint formation and reliability. Examples of non-eutectic solder alloys include:
- Sn60Pb40 (melting range: 183-190°C)
- Sn96.5Ag3.0Cu0.5 (melting range: 217-220°C)
The choice between eutectic and non-eutectic solder depends on the specific application, soldering process, and desired joint characteristics.
Classification by Application
Solder can be classified based on its intended application or the specific requirements of the soldering process.
Electronics Solder
Electronics solder is used for soldering electronic components, printed circuit boards (PCBs), and electrical connections. It is typically designed to have good wetting properties, electrical conductivity, and joint reliability. Electronics solder can be further classified based on specific applications, such as:
- Wave soldering: Used for soldering through-hole components on PCBs.
- Reflow soldering: Used for soldering surface-mount components on PCBs.
- Hand soldering: Used for manual soldering of components and repairs.
Plumbing Solder
Plumbing solder is used for joining copper pipes and fittings in plumbing systems. It is designed to have good wetting properties, corrosion resistance, and joint strength. Plumbing solder typically contains lead, but lead-free alternatives are also available to comply with regulations.
Brazing Solder
Brazing solder is used for joining metals at higher temperatures than traditional soldering. Brazing solder alloys have higher melting points and provide stronger joints compared to standard solder alloys. Brazing solder is commonly used in applications that require high-strength joints, such as in automotive, aerospace, and HVAC industries.
Classification by Form Factor
Solder can be classified based on its physical form or packaging, which affects its ease of use and suitability for different soldering processes.
Solder Wire
Solder wire is the most common form of solder used in electronics and general soldering applications. It consists of a solder alloy core surrounded by a flux coating. Solder wire is available in various diameters, alloy compositions, and flux types to suit different soldering needs. The flux helps to remove oxides from the metal surfaces and promotes better wetting and joint formation.
Solder Paste
Solder paste is a mixture of fine solder particles suspended in a flux medium. It is commonly used in surface-mount technology (SMT) for reflow soldering of electronic components. Solder paste is applied to the PCB using a stencil or syringe, and the components are placed on top. During reflow soldering, the solder particles melt and form a strong bond between the components and the PCB pads.
Solder Bar
Solder bar is a solid form of solder alloy used in wave soldering machines and other bulk soldering processes. Solder bars are melted in a solder pot or bath, and the molten solder is used to create a solder wave or fountain for soldering through-hole components on PCBs.
Solder Preforms
Solder preforms are precisely shaped pieces of solder alloy used in specific soldering applications. They are available in various shapes, such as rings, discs, washers, and custom designs. Solder preforms ensure consistent solder volume and placement in critical soldering joints, such as in automotive electronics and high-reliability applications.
Solder Selection Considerations
When selecting solder for a specific application, several factors need to be considered to ensure optimal soldering results and joint reliability.
Melting Point
The melting point or melting range of the solder alloy should be compatible with the materials being joined and the soldering process. The soldering temperature should be high enough to melt the solder and allow proper wetting, but not so high that it damages the components or the substrate.
Wetting Properties
Wetting refers to the ability of molten solder to flow and spread on the metal surfaces being joined. Good wetting properties ensure proper joint formation and strong bonding. Factors that affect wetting include the solder alloy composition, flux type, surface cleanliness, and soldering temperature.
Mechanical Properties
The mechanical properties of the solder joint, such as strength, ductility, and fatigue resistance, are important for the long-term reliability of the soldered assembly. The choice of solder alloy and the soldering process parameters influence the mechanical properties of the joint.
Electrical Conductivity
In electronics applications, the electrical conductivity of the solder joint is crucial for proper signal transmission and power delivery. The solder alloy composition and joint geometry affect the electrical conductivity of the soldered connection.
Environmental and Health Considerations
The environmental impact and health risks associated with certain solder alloys, particularly lead-based solder, should be considered. Compliance with regulations such as RoHS and the use of lead-free solder alternatives are important factors in solder selection.
Cost and Availability
The cost and availability of solder alloys and soldering materials should be considered in the selection process. Some specialty solder alloys may have higher costs or limited availability compared to standard alloys.
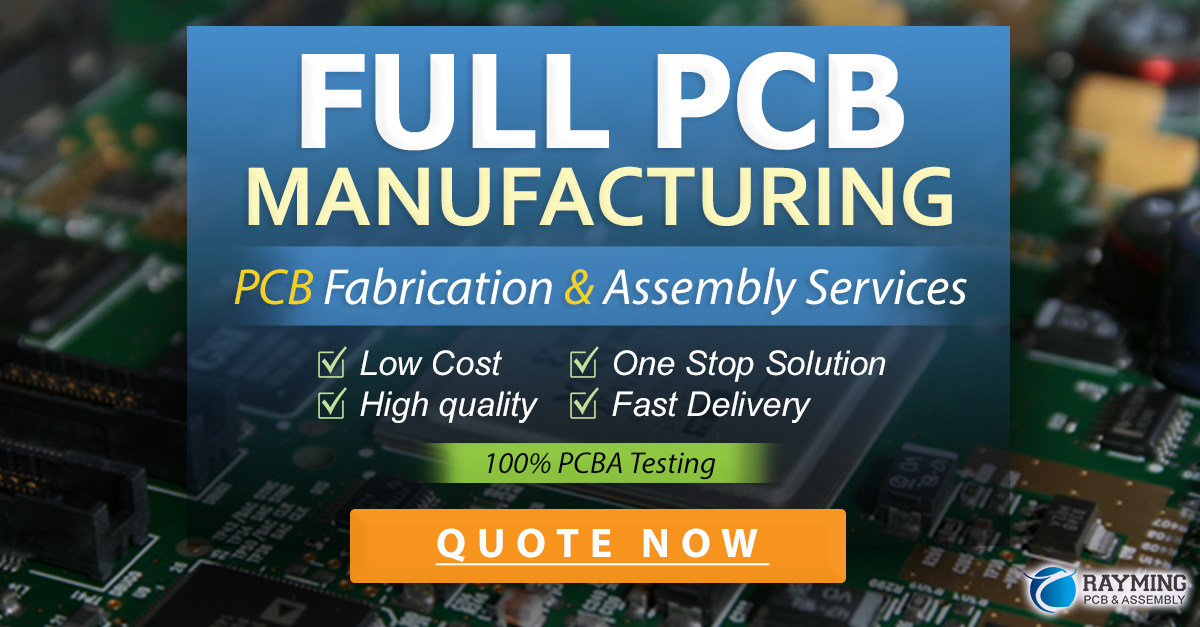
Frequently Asked Questions (FAQ)
-
Q: What is the difference between soldering and welding?
A: Soldering and welding are both metal joining processes, but they differ in the temperature range and the way the base metals are joined. Soldering involves melting a filler metal (solder) with a lower melting point than the base metals, while welding involves melting and fusing the base metals themselves at high temperatures. -
Q: Can lead-free solder be used for all soldering applications?
A: Lead-free solder alloys can be used for most soldering applications, including electronics and plumbing. However, some specific applications may still require the use of lead-based solder due to its unique properties or legacy designs. It’s important to consider the specific requirements and regulations of each application when choosing between lead-based and lead-free solder. -
Q: What is flux, and why is it used in soldering?
A: Flux is a chemical compound used in soldering to remove oxides and other contaminants from the metal surfaces being joined. It promotes better wetting and flow of the molten solder, ensuring a strong and reliable solder joint. Flux can be applied separately or incorporated into the solder wire or paste. -
Q: How do I choose the right solder alloy for my application?
A: Choosing the right solder alloy depends on several factors, such as the melting point, wetting properties, mechanical properties, electrical conductivity, and environmental considerations. Consider the specific requirements of your application, the materials being joined, and the soldering process when selecting a solder alloy. Consult solder manufacturers’ guidelines and specifications to determine the most suitable alloy for your needs. -
Q: Can solder joints be reworked or repaired?
A: Yes, solder joints can be reworked or repaired if necessary. Reworking involves removing the existing solder joint and resoldering the connection using fresh solder. Repair techniques, such as adding additional solder or using specialized repair fluxes, can be used to fix defective or damaged solder joints. However, proper techniques and tools should be used to ensure the integrity and reliability of the reworked or repaired joint.
Conclusion
Solder is a vital component in the assembly and manufacturing of electronic devices, printed circuit boards, and various metal structures. Understanding the different types of solder and their classifications based on composition, melting point, application, and form factor is crucial for selecting the appropriate solder for specific soldering needs.
Lead-based solder alloys have been widely used in the past, but environmental and health concerns have led to the adoption of lead-free solder alternatives. Solder can also be classified based on its melting point, with eutectic and non-eutectic alloys having different melting behaviors and joint characteristics.
The choice of solder depends on the intended application, such as electronics soldering, plumbing, or brazing. Solder form factors, including wire, paste, bar, and preforms, offer different options for various soldering processes.
When selecting solder, factors such as melting point, wetting properties, mechanical properties, electrical conductivity, environmental considerations, cost, and availability should be taken into account.
By understanding the different types of solder and their classifications, engineers, technicians, and hobbyists can make informed decisions when choosing solder for their projects. Proper solder selection and soldering techniques ensure reliable and high-quality solder joints, leading to the successful assembly and performance of electronic devices and metal structures.
Solder Alloy | Composition | Melting Point/Range (°C) | Application |
---|---|---|---|
Sn63Pb37 | 63% tin, 37% lead | 183 | Electronics (lead-based) |
Sn96.5Ag3.0Cu0.5 | 96.5% tin, 3% silver, 0.5% copper | 217-220 | Electronics (lead-free) |
Sn99.3Cu0.7 | 99.3% tin, 0.7% copper | 227 | Electronics (lead-free) |
Sn42Bi58 | 42% tin, 58% bismuth | 138 | Low-temperature applications |
Sn60Pb40 | 60% tin, 40% lead | 183-190 | Plumbing (lead-based) |
Leave a Reply