Introduction to PCBA Solutions in Shenzhen
Shenzhen, known as the “Silicon Valley of China,” has become a global hub for electronics manufacturing, particularly in the realm of printed circuit board assembly (PCBA). With its vast network of suppliers, skilled workforce, and state-of-the-art facilities, Shenzhen offers comprehensive PCBA solutions for businesses worldwide. In this article, we will explore the various aspects of Shenzhen’s PCBA industry and how you can leverage its capabilities to bring your electronic products to life.
What is PCBA?
PCBA, or printed circuit board assembly, is the process of assembling electronic components onto a printed circuit board (PCB) to create a functional electronic device. The process involves several steps, including:
- Solder paste application
- Component placement
- Reflow soldering
- Inspection and testing
By combining these steps, a bare PCB is transformed into a complete, functional Electronic Assembly ready for integration into a final product.
Why Choose Shenzhen for PCBA?
Shenzhen has emerged as a global leader in PCBA for several reasons:
-
Extensive Supply Chain: Shenzhen is home to countless suppliers of electronic components, PCBs, and related materials, ensuring a stable and cost-effective supply chain for PCBA projects.
-
Skilled Workforce: The city boasts a large pool of experienced engineers, technicians, and workers who specialize in electronics manufacturing, enabling high-quality PCBA services.
-
Advanced Infrastructure: Shenzhen has invested heavily in developing state-of-the-art manufacturing facilities, equipped with the latest technology and equipment to support efficient and reliable PCBA processes.
-
Competitive Pricing: Due to its well-established supply chain and economies of scale, Shenzhen offers highly competitive pricing for PCBA services, making it an attractive option for businesses looking to optimize their manufacturing costs.
PCBA Process Overview
To better understand the PCBA solutions available in Shenzhen, let’s take a closer look at the key steps involved in the process.
1. Solder Paste Application
The first step in the PCBA process is applying solder paste to the PCB. Solder paste is a mixture of tiny solder particles suspended in a flux medium. The paste is applied to the PCB using a stencil, which ensures precise placement and quantity of solder on the board’s pads.
2. Component Placement
Once the solder paste is applied, the electronic components are placed onto the PCB. This step is typically performed using automated pick-and-place machines, which rapidly and accurately position the components based on the PCB design files.
3. Reflow Soldering
After component placement, the PCB undergoes reflow soldering. In this step, the board is heated in a reflow oven, causing the solder paste to melt and form permanent electrical and mechanical connections between the components and the PCB.
4. Inspection and Testing
Finally, the assembLED PCB undergoes thorough inspection and testing to ensure its quality and functionality. This may include:
- Visual inspection
- Automated optical inspection (AOI)
- X-ray inspection
- In-circuit testing (ICT)
- Functional testing
By implementing rigorous quality control measures, Shenzhen PCBA factories can deliver consistently high-quality assemblies that meet or exceed customer expectations.
Choosing the Right PCBA Factory in Shenzhen
With numerous PCBA factories operating in Shenzhen, selecting the right partner for your project can be a daunting task. Here are some key factors to consider when evaluating potential PCBA factories:
1. Technical Capabilities
Assess the factory’s technical capabilities to ensure they can handle the complexity and specific requirements of your PCBA project. This includes:
- Experience with similar projects
- Equipment and technology
- Manufacturing processes and standards
- Quality control measures
2. Quality Management System
A robust quality management system is essential for ensuring consistent, high-quality PCBA output. Look for factories that have implemented recognized quality standards, such as ISO 9001, and have a proven track record of delivering quality products.
3. Communication and Support
Effective communication and support are crucial for a successful PCBA project. Choose a factory that is responsive, proactive, and willing to work closely with you throughout the manufacturing process. This includes providing regular updates, addressing any issues or concerns promptly, and offering technical support as needed.
4. Cost and Lead Time
While cost is an important consideration, it should not be the sole deciding factor when selecting a PCBA factory. Strike a balance between competitive pricing and the factory’s ability to meet your quality, reliability, and lead time requirements.
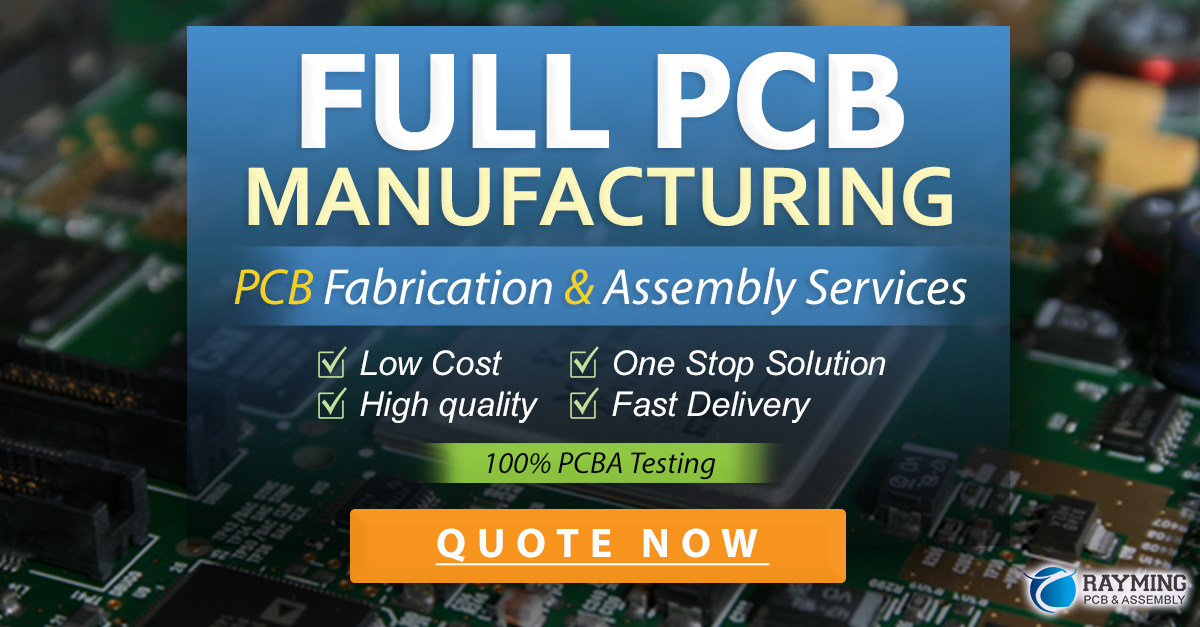
Visiting PCBA Factories Online
In the digital age, it’s easier than ever to explore and engage with PCBA factories in Shenzhen, even if you can’t visit them in person. Many factories now offer virtual tours, online consultations, and remote collaboration tools to help you evaluate their capabilities and discuss your project requirements.
When visiting PCBA factories online, consider the following:
-
Website Quality: A professional, informative, and user-friendly website can be an indicator of the factory’s commitment to communication and customer service.
-
Online Resources: Look for factories that provide helpful online resources, such as case studies, technical guides, and FAQs, to help you better understand their capabilities and approach to PCBA.
-
Virtual Tours: Some factories offer virtual tours of their facilities, allowing you to get a firsthand look at their equipment, processes, and working environment.
-
Online Communication Channels: Evaluate the factory’s availability and responsiveness through online communication channels, such as email, chat, or video conferencing, to gauge their level of support and collaboration.
By leveraging online resources and communication tools, you can effectively assess and engage with Shenzhen PCBA factories, even from a distance.
PCBA Project Case Studies
To illustrate the capabilities of Shenzhen’s PCBA factories, let’s examine a few real-world case studies.
Case Study 1: Wireless Smart Home Device
- Project: A smart home device manufacturer needed to produce a new line of wireless sensors and control units.
- Challenges: The project required the integration of multiple wireless protocols, including Wi-Fi, Bluetooth, and Zigbee, as well as the development of Custom PCBs and enclosures.
- Solution: The chosen Shenzhen PCBA factory worked closely with the client to design and optimize the PCBs, source the necessary components, and develop a custom manufacturing process to ensure the reliable production of the smart home devices.
- Result: The factory successfully delivered the first batch of devices within the agreed-upon timeframe, meeting the client’s quality and performance requirements. The client went on to establish a long-term partnership with the factory for ongoing production and future product development.
Case Study 2: Automotive Electronics
- Project: An automotive electronics supplier needed to outsource the production of a new line of in-vehicle infotainment systems.
- Challenges: The project required compliance with strict automotive quality standards, such as IATF 16949, as well as the ability to handle high-volume production and just-in-time delivery.
- Solution: The selected Shenzhen PCBA factory had extensive experience in automotive electronics manufacturing and was certified to IATF 16949. They worked with the client to establish a robust quality management system, implement lean manufacturing principles, and optimize the supply chain to ensure timely delivery of the infotainment systems.
- Result: The factory consistently met the client’s quality, cost, and delivery targets, enabling the successful launch and ongoing production of the in-vehicle infotainment systems. The client continued to collaborate with the factory for future automotive electronics projects.
These case studies demonstrate the versatility and capabilities of Shenzhen’s PCBA factories in handling diverse and complex projects across various industries.
Frequently Asked Questions (FAQs)
-
Q: What is the minimum order quantity (MOQ) for PCBA services in Shenzhen?
A: MOQs can vary among factories, but many Shenzhen PCBA factories offer low MOQs, sometimes as low as 100 pieces, to accommodate smaller-scale projects and startups. However, larger MOQs may be required for more complex or customized projects. -
Q: How long does it typically take to complete a PCBA project in Shenzhen?
A: Lead times for PCBA projects depend on various factors, such as project complexity, component availability, and production volume. On average, a typical PCBA project may take 4-8 weeks from start to finish, but expedited services are often available for time-sensitive projects. -
Q: Can Shenzhen PCBA factories handle both prototype and mass production?
A: Yes, many Shenzhen PCBA factories offer services for both prototype and mass production. They can support clients throughout the entire product lifecycle, from initial concept development and prototyping to full-scale production and post-production support. -
Q: How can I ensure the quality of my PCBA project when working with a Shenzhen factory?
A: To ensure the quality of your PCBA project, choose a factory with a strong quality management system, such as ISO 9001 certification, and a proven track record of delivering high-quality products. Clearly communicate your quality requirements, and consider implementing additional quality control measures, such as third-party inspections or on-site visits, to verify the factory’s processes and output. -
Q: What should I prepare before approaching a Shenzhen PCBA factory with my project?
A: Before engaging with a Shenzhen PCBA factory, prepare a detailed project brief that includes: - PCB design files (e.g., Gerber files, schematics, BOMs)
- Product specifications and requirements
- Target production volume and timeline
- Quality and certification requirements
- Any special considerations or customization needs
Having a well-prepared project brief will help the factory better understand your requirements and provide a more accurate quotation and project plan.
Conclusion
Shenzhen’s PCBA industry offers a comprehensive range of solutions for businesses looking to bring their electronic products to life. With its extensive supply chain, skilled workforce, advanced infrastructure, and competitive pricing, Shenzhen has become a global hub for PCBA services.
By understanding the PCBA process, carefully selecting the right factory partner, and leveraging online resources and communication tools, you can effectively navigate the Shenzhen PCBA landscape and achieve success in your electronic product development and manufacturing endeavors.
As you embark on your PCBA project, remember to prioritize quality, communication, and collaboration to ensure the best possible outcomes. With the right approach and partnership, Shenzhen’s PCBA solutions can help you turn your electronic product vision into a reality.
Leave a Reply