What is a PCB Surface Finish?
A PCB surface finish is a coating applied to the exposed copper traces and pads on a printed circuit board. Its primary purpose is to protect the copper from oxidation and corrosion, which can occur due to exposure to air, moisture, and other environmental factors. Additionally, the surface finish enhances the solderability of the PCB, ensuring a reliable and strong connection between the components and the board during the assembly process.
Importance of Selecting the Right PCB Surface Finish
Choosing the appropriate surface finish for your PCB is essential for several reasons:
-
Protection: The right surface finish will protect the copper traces from oxidation and corrosion, extending the lifespan of your PCB.
-
Solderability: A suitable surface finish will enhance the solderability of the PCB, ensuring a strong and reliable connection between the components and the board.
-
Compatibility: Different surface finishes have varying compatibility with different assembly processes and components. Selecting the right finish ensures seamless integration and optimal performance.
-
Cost: Surface finishes vary in cost, and choosing the most cost-effective option that meets your requirements can help optimize your budget.
Common PCB Surface Finishes
There are several PCB surface finishes available, each with its unique properties, advantages, and disadvantages. Some of the most common surface finishes include:
1. Hot Air Solder Leveling (HASL)
Hot Air Solder Leveling (HASL) is one of the most widely used surface finishes in the PCB industry. The process involves dipping the PCB into a molten solder bath and then using hot air to level the solder on the surface. The result is a thin, uniform layer of solder that protects the copper and provides excellent solderability.
Advantages of HASL:
- Cost-effective
- Excellent solderability
- Good shelf life
- Suitable for both through-hole and surface mount components
Disadvantages of HASL:
- Uneven surface due to solder bumps
- Not suitable for fine-pitch components
- Potential for solder bridging
- Contains lead (not RoHS compliant)
2. Immersion Silver
Immersion Silver is a lead-free surface finish that involves depositing a thin layer of silver onto the copper surface through a chemical process. The silver layer provides excellent solderability and protection against oxidation.
Advantages of Immersion Silver:
- Excellent solderability
- Lead-free and RoHS compliant
- Suitable for fine-pitch components
- Provides a flat and even surface
Disadvantages of Immersion Silver:
- Higher cost compared to HASL
- Possible silver migration in harsh environments
- May tarnish over time
3. Electroless Nickel Immersion Gold (ENIG)
Electroless Nickel Immersion Gold (ENIG) is a two-layer surface finish consisting of a nickel layer followed by a thin gold layer. The nickel layer provides a barrier against copper diffusion, while the gold layer offers excellent solderability and protection against oxidation.
Advantages of ENIG:
- Excellent solderability
- Suitable for fine-pitch components
- Good shelf life
- Provides a flat and even surface
Disadvantages of ENIG:
- Higher cost compared to HASL and Immersion Silver
- Potential for black pad syndrome (BPS) due to improper plating process
- Gold layer may dissolve during multiple reflow processes
4. Organic Solderability Preservatives (OSP)
Organic Solderability Preservatives (OSP) are a class of surface finishes that involve applying a thin, organic coating onto the copper surface. The coating acts as a barrier against oxidation and provides good solderability.
Advantages of OSP:
- Cost-effective
- Lead-free and RoHS compliant
- Suitable for fine-pitch components
- Provides a flat and even surface
Disadvantages of OSP:
- Limited shelf life (typically 6-12 months)
- Requires proper handling and storage to maintain solderability
- Not suitable for multiple reflow processes
5. Immersion Tin
Immersion Tin is a lead-free surface finish that involves depositing a thin layer of tin onto the copper surface through a chemical process. The tin layer provides good solderability and protection against oxidation.
Advantages of Immersion Tin:
- Good solderability
- Lead-free and RoHS compliant
- Cost-effective compared to ENIG
- Suitable for fine-pitch components
Disadvantages of Immersion Tin:
- Potential for Tin Whiskers, which can cause short circuits
- Limited shelf life compared to ENIG
- May require additional processing steps to mitigate tin whisker growth
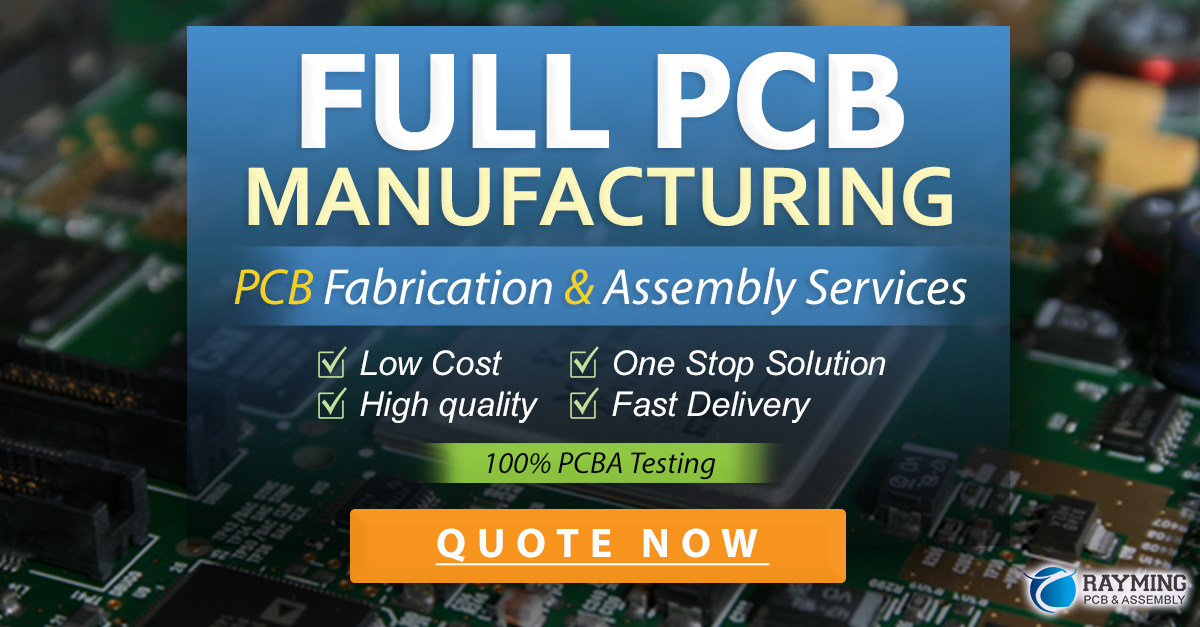
Factors to Consider When Choosing a PCB Surface Finish
When selecting the right surface finish for your PCB, there are several factors to consider:
-
Application Requirements: Consider the specific requirements of your application, such as operating environment, temperature range, and expected lifespan of the PCB.
-
Component Compatibility: Ensure that the chosen surface finish is compatible with the components used in your design, especially for fine-pitch and BGA components.
-
Assembly Process: Consider the assembly process used for your PCB, as different surface finishes may have varying compatibility with different soldering techniques.
-
Cost: Evaluate the cost of the surface finish in relation to your budget and the overall cost of the PCB.
-
Shelf Life: Consider the shelf life of the surface finish, especially if your PCBs will be stored for an extended period before assembly.
-
Environmental Regulations: Ensure that the selected surface finish complies with relevant environmental regulations, such as RoHS and REACH.
Comparison of PCB Surface Finishes
Surface Finish | Solderability | Shelf Life | Fine-Pitch Compatibility | Cost | RoHS Compliance |
---|---|---|---|---|---|
HASL | Excellent | Good | Limited | Low | No (contains lead) |
Immersion Silver | Excellent | Good | Suitable | Moderate | Yes |
ENIG | Excellent | Excellent | Suitable | High | Yes |
OSP | Good | Limited | Suitable | Low | Yes |
Immersion Tin | Good | Moderate | Suitable | Moderate | Yes |
FAQ
-
Q: What is the most cost-effective PCB surface finish?
A: Hot Air Solder Leveling (HASL) and Organic Solderability Preservatives (OSP) are generally the most cost-effective PCB surface finishes. -
Q: Which surface finish is best for fine-pitch components?
A: Immersion Silver, ENIG, OSP, and Immersion Tin are all suitable for fine-pitch components due to their flat and even surface. -
Q: Is HASL RoHS compliant?
A: No, HASL is not RoHS compliant as it contains lead. For RoHS compliance, consider lead-free alternatives such as Immersion Silver, ENIG, OSP, or Immersion Tin. -
Q: What is the shelf life of OSP?
A: The shelf life of OSP is typically limited to 6-12 months, after which the solderability may degrade. Proper handling and storage are crucial to maintain its effectiveness. -
Q: Can ENIG withstand multiple reflow processes?
A: ENIG can withstand multiple reflow processes, but the gold layer may dissolve over time, potentially affecting solderability. It is essential to consider the number of reflow cycles when selecting ENIG as a surface finish.
Conclusion
Selecting the right surface finish for your PCB is a critical decision that impacts the performance, reliability, and longevity of your electronic device. By understanding the properties, advantages, and disadvantages of each surface finish and considering factors such as application requirements, component compatibility, assembly process, cost, shelf life, and environmental regulations, you can make an informed choice that best suits your specific needs.
Remember, there is no one-size-fits-all solution when it comes to PCB surface finishes. Each project may have unique requirements that dictate the most suitable option. Consulting with your PCB manufacturer and assembly partner can provide valuable insights and guidance in making the right decision.
Investing time and effort in selecting the appropriate surface finish will contribute to the overall success of your PCB design and help ensure that your electronic device performs optimally in its intended environment.
Leave a Reply