Introduction
Rogers RO4350 is a nickel-based superalloy known for its high strength and creep resistance properties at high temperatures. It was designed in the 1950s by researchers at the International Nickel Company to meet the demanding requirements of aircraft jet engine components operating under high stress and temperature conditions. Since then, RO4350 has become one of the most widely used superalloys in aerospace applications and remains an industry standard today. This article provides a comprehensive overview of Rogers RO4350, including its composition, properties, manufacturing process, applications, and usage considerations.
Composition
The composition of Rogers RO4350 is:
Element | Weight % |
---|---|
Nickel | Balance |
Chromium | 18-20% |
Cobalt | 15-17% |
Molybdenum | 2-3% |
Titanium | 2.1-2.8% |
Aluminum | 1.2-1.6% |
Iron | 0-1% |
Carbon | 0-0.08% |
Boron | 0.006-0.015% |
Zirconium | 0.03-0.07% |
RO4350 derives its high temperature strength from solid solution strengthening provided by refractory elements like molybdenum, tungsten, cobalt, and tantalum. Precipitation hardening from gamma prime and gamma double prime phases formed with nickel and aluminum also contributes to its strength. The careful balance of alloying elements gives RO4350 excellent creep rupture strength and thermal stability for prolonged exposure to temperatures up to 1200°F.
Properties
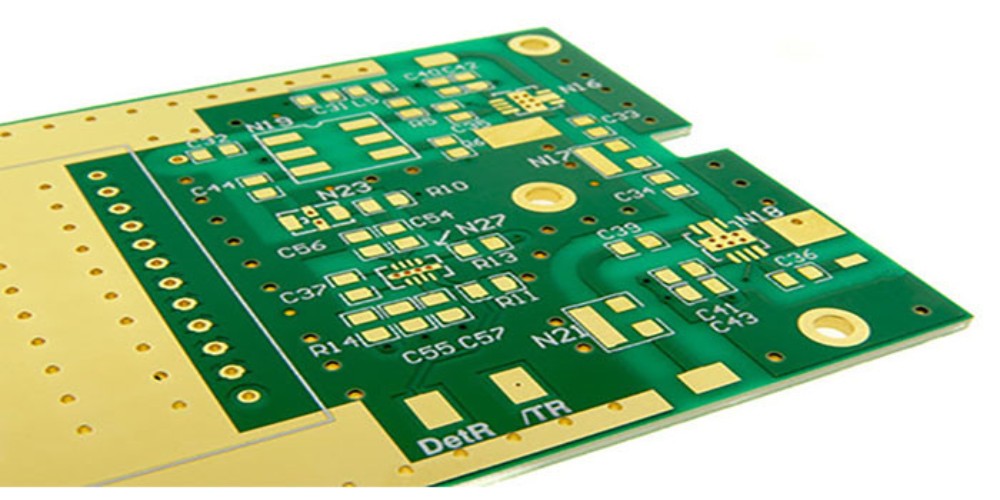
The outstanding properties of Rogers RO4350 that make it well suited for jet engine parts include:
- High tensile and yield strength at elevated temperatures up to 1300°F
- Excellent creep rupture strength for long duration exposure to high temperatures under load
- Good fatigue resistance and crack growth characteristics
- Excellent oxidation and corrosion resistance
- Higher ductility than typical cast nickel superalloys
- Good weldability relative to other precipitation hardening superalloys
- Lower coefficient of thermal expansion compared to austenitic steels
For example, RO4350 exhibits a tensile strength of around 90 ksi at 1200°F. Its stress-rupture properties exceed 100 hours at 1200°F at a stress level of 15 ksi. This combination of strength, creep resistance, and ductility is unmatched by other alloys.
Manufacturing Process
RO4350 is challenging to fabricate due to its precipitation hardening characteristics. The manufacturing process consists of multiple steps:
- Melting: Vacuum induction melting followed by vacuum arc remelting is used to achieve high purity and remove defects.
- Forging: Hot die forging reduces internal segregation issues and achieves favorable grain flow.
- Heat Treatment: Solution heat treatment dissolves gamma prime followed by aging to re-precipitate gamma prime particles. This develops the required strength.
- Machining: Intricate components are machined into final shape. Grinding and EDM are commonly used.
The processing requires careful control to develop the full properties of the alloy. Variations in heat treatment can significantly affect ductility, strength, and fatigue life.
Applications
The capability of Rogers RO4350 to retain strength at extremely high temperatures makes it ideally suited for critical jet engine components. Typical applications include:
- Turbine disks – Experience high centrifugal stresses up to 1200°F
- Turbine blades and vanes – Withstand thermal fatigue and oxidation up to 1300°F
- Combustor liners and cans – Contain combustion gases over 2000°F
- Exhaust components – Endure peak temperatures near 1500°F
- Fasteners – High strength requirements at elevated temperature
RO4350 allows jet engines to operate at higher temperatures and stresses, improving fuel efficiency and thrust. It is valued for both new and established engine designs from GE, Pratt & Whitney, Rolls-Royce, and others.
Usage Considerations
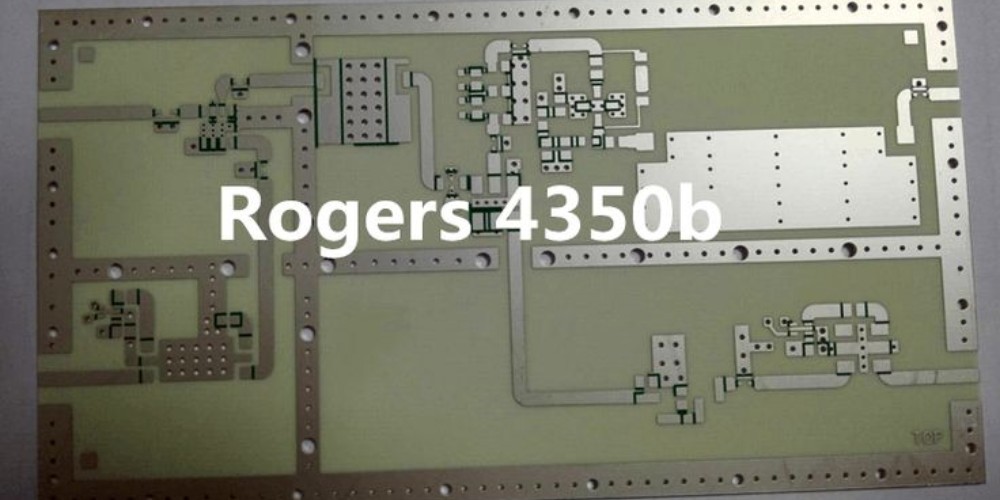
There are some important usage considerations when working with RO4350:
- Careful preheating is required during welding to avoid cracking
- Susceptible to strain-age cracking during forming operations
- Low thermal conductivity can lead to thermal fatigue issues
- Oxide scale spallation can occur under thermal cycling conditions
- Coatings may be required for oxidation resistance above 1100°C
- Stress relieving heat treatments should be performed after machining
Proper processing is critical to achieve optimal properties from this alloy. Overall, RO4350 requires advanced manufacturing techniques and engineering expertise compared to other materials. But the unmatched performance it enables has cemented its place as an indispensable aerospace alloy.
Frequently Asked Questions
What are the main advantages of Rogers RO4350?
The main advantages of RO4350 are its high strength at elevated temperatures up to 1300°F, excellent creep rupture strength, good fatigue resistance, and corrosion resistance. This combination of properties at high temperatures makes it ideal for critical jet engine components.
How does RO4350 compare to other nickel superalloys?
RO4350 has higher strength than most other nickel superalloys while retaining good ductility and fracture toughness. It has better creep rupture strength than Waspaloy or Rene 41. Its temperature capability falls between Udimet 720 and Inconel 718. Overall, RO4350 offers the best combined properties.
What kinds of components are made from RO4350?
Typical applications for RO4350 include turbine disks, turbine blades, combustor cans, exhaust components, fasteners, and other parts needing high strength at temperatures over 1000°F. It is widely used in hot section aerospace components.
What are some of the challenges in manufacturing parts from RO4350?
RO4350 can be difficult to fabricate due its precipitation hardening characteristics. Proper solution and aging heat treatments are critical. It is also prone to strain-age cracking during forging and forming. Tight controls over the entire manufacturing process are required.
Does RO4350 require special coatings or treatments?
Coatings may be required for RO4350 components seeing service temperatures above 1100°C to provide oxidation and corrosion resistance. Thermal barrier coatings on turbine blades are common. Stress relieving heat treatments after machining are also typically performed.
Leave a Reply