Introduction
In the world of printed circuit boards (PCBs), solder resist plays a crucial role in protecting the copper traces and preventing short circuits. While green is the most common color for solder resist, red has been gaining popularity due to its eye-catching appearance. This article will explore the benefits of using Eye-catching Red solder resist in PCB manufacturing and its impact on the electronics industry.
What is Solder Resist?
Solder resist, also known as solder mask or PCB mask, is a protective coating applied to the surface of a PCB. Its primary purpose is to prevent solder from adhering to areas of the board where it is not intended, such as between copper traces. Solder resist also provides insulation and protection against environmental factors like dust, moisture, and mechanical damage.
Types of Solder Resist
There are two main types of solder resist:
-
Liquid Photoimageable Solder Resist (LPISM): This type of solder resist is applied as a liquid and then exposed to UV light through a photomask. The exposed areas harden, while the unexposed areas are washed away during development.
-
Dry Film Solder Resist (DFSR): DFSR is a solid film that is laminated onto the PCB surface. It is then exposed to UV light through a photomask and developed, similar to LPISM.
The Rise of Red Solder Resist
Traditionally, green has been the most common color for solder resist due to its high contrast against the copper traces, making it easier for manufacturers to inspect the boards for defects. However, in recent years, red solder resist has been gaining popularity for its eye-catching appearance and unique benefits.
Benefits of Red Solder Resist
-
Aesthetics: Red solder resist offers a striking visual contrast against the copper traces and other components on the PCB. This can make the board more visually appealing and help it stand out in a crowded market.
-
Improved Visibility: The high contrast between red solder resist and copper traces can make it easier for manufacturers to spot defects during inspection, potentially reducing the number of faulty boards that reach the market.
-
Branding Opportunities: Companies can use red solder resist as part of their branding strategy, incorporating it into their PCB designs to create a unique and recognizable look.
-
Differentiation: In industries where PCBs are visible to end-users, such as in consumer electronics or automotive applications, red solder resist can help differentiate a product from its competitors.
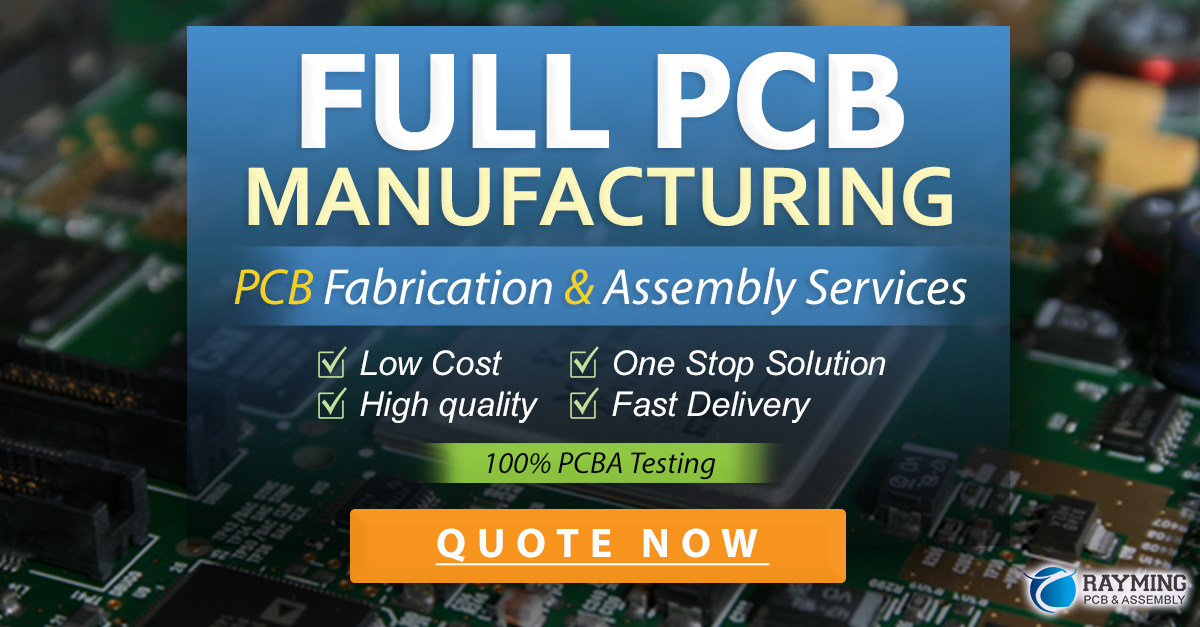
Applications of Red Solder Resist
Red solder resist can be used in a wide range of PCB applications, including:
- Consumer electronics (smartphones, tablets, laptops)
- Automotive electronics (infotainment systems, dashboards)
- Medical devices (diagnostic equipment, wearable devices)
- Industrial control systems (PLCs, HMIs)
- IoT devices (smart home appliances, wearables)
Designing with Red Solder Resist
When designing a PCB with red solder resist, there are several factors to consider to ensure optimal performance and manufacturability.
Design Guidelines
-
Minimum Solder Resist Width: Ensure that the solder resist width between copper traces is sufficient to prevent solder bridging. The minimum width depends on the PCB manufacturer’s capabilities and the solder resist type used.
-
Solder Resist Clearance: Maintain adequate clearance between solder resist openings and component pads to allow for proper soldering.
-
Contrast Ratio: Choose a red solder resist with a high contrast ratio against the copper traces to improve visibility during inspection.
-
Compatibility: Verify that the chosen red solder resist is compatible with the PCB substrate material and the manufacturing process.
Color Matching
When specifying the color of red solder resist, it is essential to use a standardized color matching system to ensure consistency across different manufacturers and batches. The most common color matching systems used in the PCB industry are:
-
Pantone: Pantone is a widely used color matching system that provides a standardized set of colors. Each color is identified by a unique Pantone number, making it easy to communicate the desired color to the PCB manufacturer.
-
RAL: The RAL color system is another popular choice for color matching in the PCB industry. It offers a wide range of colors, including various shades of red, and is commonly used in Europe.
When working with a PCB manufacturer, provide the desired color using the appropriate color matching system and request a color sample for approval before proceeding with the full production run.
Manufacturing Process
The manufacturing process for PCBs with red solder resist is similar to that of boards with other solder resist colors. The main steps involved are:
-
Applying Solder Resist: The solder resist is applied to the PCB surface using either LPISM or DFSR methods.
-
Exposing and Developing: The solder resist is exposed to UV light through a photomask and then developed to remove the unexposed areas.
-
Curing: The solder resist is cured using heat to fully harden and adhere to the PCB surface.
-
Inspection: The PCB is inspected for defects, such as solder resist bridging or incomplete coverage.
-
Finishing: Any additional surface finishes, such as HASL or ENIG, are applied to the exposed copper areas.
Quality Control
To ensure the quality of PCBs with red solder resist, manufacturers employ various quality control measures throughout the production process.
Visual Inspection
Visual inspection is the first line of defense against defects. Inspectors check the PCBs for issues such as:
- Solder resist bridging
- Incomplete solder resist coverage
- Misaligned solder resist openings
- Color consistency
Automated Optical Inspection (AOI)
AOI systems use high-resolution cameras and advanced image processing algorithms to detect defects that may be missed by human inspectors. These systems can quickly scan the entire PCB surface and identify issues like solder resist bridging or incomplete coverage.
Electrical Testing
Electrical testing is performed to ensure that the PCB functions as intended. This includes continuity testing to verify that all connections are intact and insulation resistance testing to check for shorts or leakage between traces.
Troubleshooting Common Issues
Despite the best efforts of manufacturers, issues can sometimes arise with red solder resist. Here are some common problems and their potential solutions:
-
Solder Resist Bridging: This occurs when the solder resist fills the spaces between copper traces, causing short circuits. To prevent this, ensure that the minimum solder resist width is maintained and that the solder resist is properly cured.
-
Incomplete Coverage: If the solder resist does not fully cover the intended areas, it can lead to exposed copper and potential short circuits. This can be caused by insufficient solder resist application or improper exposure and development. Ensure that the solder resist is applied evenly and that the exposure and development times are correct.
-
Color Inconsistency: Variations in the red color between different batches or manufacturers can be a concern for companies looking to maintain a consistent brand image. To minimize this issue, use a standardized color matching system and request color samples before proceeding with full production.
-
Adhesion Issues: Poor adhesion between the solder resist and the PCB surface can lead to peeling or flaking of the solder resist. This can be caused by contamination on the PCB surface or incompatibility between the solder resist and the substrate material. Ensure that the PCB surface is clean and that the chosen solder resist is compatible with the substrate.
Future Trends
As the demand for eye-catching and visually appealing PCBs continues to grow, we can expect to see more innovations in solder resist technology and color options.
New Color Options
While red solder resist is gaining popularity, manufacturers are also experimenting with other colors, such as blue, yellow, and orange. These colors can offer unique aesthetic appeal and potentially improve visibility for specific applications.
Improved Performance
Solder resist manufacturers are continually working to improve the performance of their products, including better adhesion, higher resolution, and enhanced durability. These advancements will enable PCB designers to create more complex and reliable boards with eye-catching solder resist colors.
Sustainable Materials
As the electronics industry becomes more focused on sustainability, we may see the development of eco-friendly solder resist materials that are biodegradable or made from renewable resources. These materials could help reduce the environmental impact of PCB manufacturing while still providing the necessary protection and aesthetic appeal.
Frequently Asked Questions (FAQ)
-
Q: Is red solder resist more expensive than green solder resist?
A: Red solder resist may be slightly more expensive than green due to the pigments used, but the cost difference is generally minimal and should not significantly impact the overall cost of the PCB. -
Q: Can red solder resist be used for all types of PCBs?
A: Red solder resist can be used for most types of PCBs, including rigid, flexible, and rigid-flex boards. However, it is essential to ensure that the chosen solder resist is compatible with the substrate material and the manufacturing process. -
Q: Does red solder resist affect the electrical properties of the PCB?
A: The color of the solder resist does not directly affect the electrical properties of the PCB. However, the quality and consistency of the solder resist application can impact the board’s performance, regardless of the color used. -
Q: How do I specify the desired shade of red when ordering PCBs?
A: To ensure consistency, use a standardized color matching system, such as Pantone or RAL, when specifying the desired shade of red. Provide the PCB manufacturer with the appropriate color code and request a color sample for approval before proceeding with the full production run. -
Q: Can red solder resist be used in combination with other colors on the same PCB?
A: Yes, red solder resist can be used in combination with other colors, such as green or blue, on the same PCB. This can create unique aesthetic effects and help differentiate between different areas of the board. However, keep in mind that using multiple solder resist colors may increase the complexity and cost of the manufacturing process.
Conclusion
Red solder resist offers a unique and eye-catching alternative to the traditional green solder mask used in PCB manufacturing. With its striking visual appearance and potential benefits for improved visibility and branding, red solder resist is gaining popularity across various industries.
When designing PCBs with red solder resist, it is essential to consider factors such as minimum solder resist width, clearance, contrast ratio, and compatibility with the substrate material. By following design guidelines and working closely with PCB manufacturers, designers can create visually appealing and high-performing boards that stand out in the market.
As the demand for differentiation and aesthetics in PCBs continues to grow, we can expect to see further innovations in solder resist technology, including new color options, improved performance, and sustainable materials. By staying informed about these trends and understanding the benefits and challenges of using eye-catching red solder resist, PCB designers and manufacturers can create products that meet the evolving needs of the electronics industry.
Leave a Reply