Introduction to Gold-Plated Connectors
Gold-plated connectors are a type of electrical connector that uses a thin layer of gold plating over a base metal, such as copper or brass, to enhance the connector’s performance and durability. The gold plating provides several advantages over non-plated connectors, including improved conductivity, resistance to corrosion and oxidation, and better reliability in harsh environments.
Gold-plated connectors are widely used in various industries, such as:
– Telecommunications
– Aerospace
– Medical equipment
– Consumer electronics
– Military applications
Benefits of Gold Plating in Connectors
Gold plating offers several key benefits when used in electrical connectors:
-
Enhanced Conductivity: Gold is an excellent conductor of electricity, surpassed only by silver and copper. The gold plating on connectors ensures efficient and reliable transmission of electrical signals.
-
Corrosion Resistance: Gold is highly resistant to corrosion and oxidation, making gold-plated connectors suitable for use in harsh environments where exposure to moisture, chemicals, or extreme temperatures is common.
-
Durability: Gold-plated connectors have a longer lifespan compared to non-plated connectors, as the gold layer protects the base metal from wear and tear caused by repeated mating and unmating cycles.
-
Lower Contact Resistance: The gold plating helps maintain a low and stable contact resistance, which is crucial for ensuring reliable electrical connections and minimizing signal loss.
-
Improved Signal Integrity: Gold-plated connectors provide better signal integrity by reducing noise and interference, making them suitable for high-frequency and high-speed applications.
Types of Gold Plating
There are several types of gold plating used in electrical connectors, each with its own characteristics and applications:
Hard Gold Plating
Hard gold plating is a type of electroplated gold that contains small amounts of cobalt or nickel to increase its hardness and wear resistance. Hard gold plating is typically used in high-reliability applications, such as:
– Military and aerospace equipment
– Medical devices
– Telecommunications infrastructure
Characteristics of hard gold plating include:
– Thickness: 0.2 to 2.5 microns
– Hardness: 130 to 200 Knoop
– Purity: 99.7% to 99.9% gold
Soft Gold Plating
Soft gold plating is a pure gold layer without any alloying elements, making it softer and more ductile than hard gold plating. Soft gold plating is commonly used in applications where frequent mating and unmating cycles are required, such as:
– Consumer electronics
– Test and measurement equipment
– Automotive electronics
Characteristics of soft gold plating include:
– Thickness: 0.05 to 0.5 microns
– Hardness: 60 to 90 Knoop
– Purity: 99.9% to 99.99% gold
Selective Gold Plating
Selective gold plating involves applying gold plating only to specific areas of the connector, such as the contact points, while leaving the rest of the connector unplated. This approach helps reduce costs by minimizing the amount of gold used while still providing the benefits of gold plating where it matters most.
Selective gold plating is often used in:
– High-volume consumer electronics
– Cost-sensitive applications
– Connectors with complex geometries
Gold Thickness and Purity
The thickness and purity of the gold plating on connectors play a crucial role in determining the connector’s performance and durability.
Gold Thickness
The thickness of the gold plating is typically measured in microns (µm) and can range from 0.05 to 2.5 microns, depending on the application and type of gold plating used. Thicker gold plating generally provides better wear resistance and longer connector life, but it also increases the cost of the connector.
Common gold plating thicknesses and their applications include:
Thickness (µm) | Application |
---|---|
0.05 – 0.2 | Consumer electronics, low-cost applications |
0.2 – 0.8 | General-purpose connectors, industrial applications |
0.8 – 1.5 | High-reliability connectors, military applications |
1.5 – 2.5 | Extreme environments, aerospace applications |
Gold Purity
The purity of the gold plating is usually expressed as a percentage or in karats (K). Higher purity gold provides better conductivity and corrosion resistance but is also more expensive and softer, making it more susceptible to wear.
Common gold purities used in electrical connectors include:
Purity | Percentage | Application |
---|---|---|
24K | 99.9% | High-reliability connectors, military applications |
23K | 95.8% | General-purpose connectors, industrial applications |
22K | 91.7% | Consumer electronics, cost-sensitive applications |
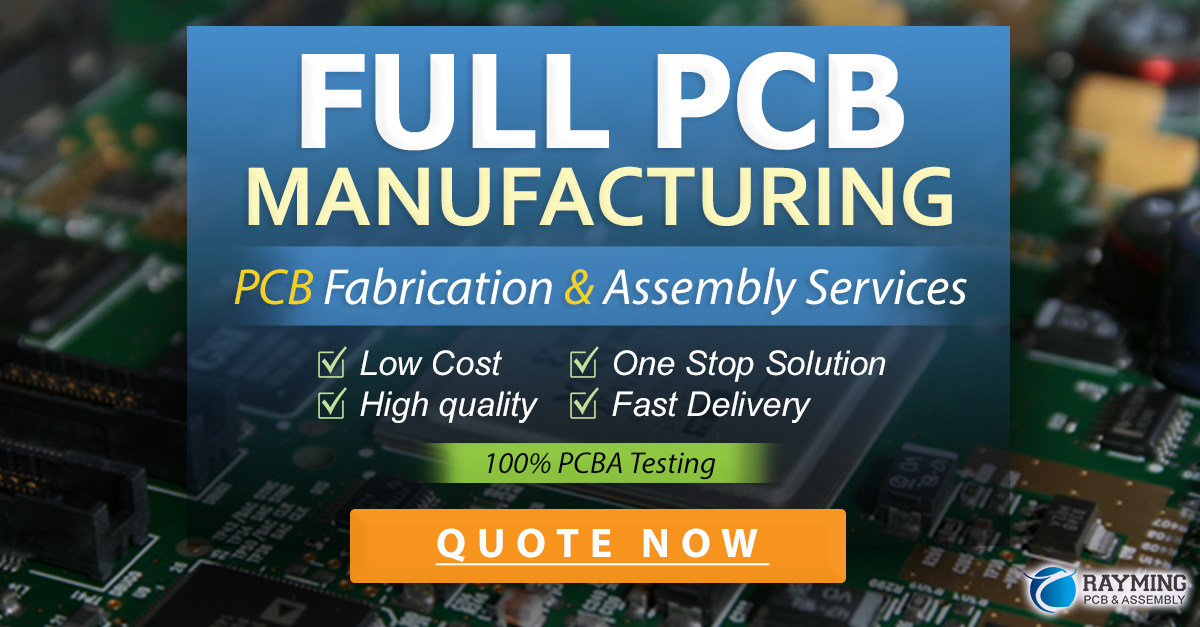
Plated Gold Edge Connectors
Plated gold edge connectors are a specific type of connector commonly used in printed circuit boards (PCBs) to establish electrical connections between boards or between a board and a backplane. These connectors feature a row of gold-plated contacts along the edge of the PCB, which mate with a corresponding socket or slot connector.
Advantages of Plated Gold Edge Connectors
Plated gold edge connectors offer several advantages over other types of PCB Connectors:
-
Simplicity: Edge connectors provide a simple and cost-effective way to establish electrical connections without the need for additional hardware or soldering.
-
High Density: Edge connectors can accommodate a large number of contacts in a small space, making them suitable for applications requiring high-density interconnects.
-
Reliability: The gold plating on the contacts ensures reliable and low-resistance electrical connections, even in harsh environments.
-
Ease of Installation: Edge connectors allow for easy installation and removal of PCBs, facilitating maintenance and upgrades.
Applications of Plated Gold Edge Connectors
Plated gold edge connectors are used in a wide range of applications, including:
- Computer peripherals (e.g., graphics cards, sound cards)
- Industrial control systems
- Telecommunications equipment
- Medical devices
- Military and aerospace electronics
Design Considerations for Plated Gold Edge Connectors
When designing or selecting plated gold edge connectors, several factors should be considered to ensure optimal performance and reliability:
-
Contact Pitch: The spacing between the contacts on the edge connector, typically measured in millimeters (mm). Smaller pitch connectors allow for higher contact density but may require more precise manufacturing and alignment.
-
Number of Contacts: The total number of contacts on the edge connector, which determines the maximum number of electrical connections that can be established.
-
Gold Plating Specifications: The thickness and purity of the gold plating on the contacts, which should be selected based on the application requirements and environmental conditions.
-
PCB Thickness: The thickness of the PCB that the edge connector will be used with, as this affects the dimensions and mechanical properties of the connector.
-
Mating Cycles: The expected number of mating and unmating cycles the connector will undergo during its lifetime, which influences the choice of gold plating type and thickness.
Maintenance and Handling of Gold-Plated Connectors
Proper maintenance and handling of gold-plated connectors are essential to ensure their long-term performance and reliability.
Cleaning Gold-Plated Connectors
Over time, gold-plated connectors may accumulate dust, debris, or contaminants that can degrade their performance. To clean gold-plated connectors:
- Use a soft, lint-free cloth or brush to gently remove any loose debris.
- For more stubborn contaminants, use a cleaning solution specifically designed for electrical contacts, such as isopropyl alcohol or a specialized contact cleaner.
- Avoid using abrasive materials or excessive force, as this can damage the gold plating.
Handling Gold-Plated Connectors
When handling gold-plated connectors, it is important to follow these guidelines to prevent damage:
- Avoid touching the contact surfaces with bare hands, as skin oils can contaminate the gold plating and degrade its performance.
- Use anti-static tools and equipment when working with gold-plated connectors to prevent electrostatic discharge (ESD) damage.
- Store gold-plated connectors in a clean, dry, and controlled environment to minimize exposure to dust, moisture, and extreme temperatures.
Inspecting Gold-Plated Connectors
Regular inspection of gold-plated connectors can help identify potential issues before they lead to failures. When inspecting connectors, look for:
- Signs of wear, damage, or deformation on the contact surfaces.
- Discoloration or tarnishing of the gold plating, which may indicate corrosion or contamination.
- Loose or missing contacts, which can cause intermittent or open connections.
If any issues are identified during the inspection, the affected connectors should be cleaned, repaired, or replaced as necessary.
Frequently Asked Questions (FAQ)
-
Q: What is the difference between hard and soft gold plating?
A: Hard gold plating contains small amounts of cobalt or nickel to increase its hardness and wear resistance, making it suitable for high-reliability applications. Soft gold plating is a pure gold layer that is softer and more ductile, making it ideal for applications with frequent mating and unmating cycles. -
Q: How does gold thickness affect connector performance?
A: Thicker gold plating generally provides better wear resistance and longer connector life, but it also increases the cost of the connector. The choice of gold thickness depends on the application requirements and environmental conditions. -
Q: Can gold-plated connectors be used in high-temperature environments?
A: Yes, gold-plated connectors can be used in high-temperature environments, as gold is stable and resistant to oxidation at elevated temperatures. However, the base metal and any additional plating layers must also be suitable for the specific temperature range. -
Q: How often should gold-plated connectors be cleaned?
A: The cleaning frequency for gold-plated connectors depends on the application and environmental conditions. In general, connectors should be cleaned whenever a degradation in performance is observed or during regular maintenance intervals. -
Q: Are gold-plated connectors compatible with Lead-free Soldering processes?
A: Yes, gold-plated connectors are compatible with lead-free soldering processes. However, the gold plating thickness should be controlled to prevent the formation of brittle gold-tin intermetallic compounds, which can degrade the solder joint reliability.
Conclusion
Gold-plated connectors, including plated gold edge connectors, offer numerous benefits over non-plated connectors, such as enhanced conductivity, corrosion resistance, durability, and improved signal integrity. By understanding the types of gold plating, thickness and purity considerations, and proper maintenance and handling techniques, designers and engineers can select the most suitable gold-plated connectors for their specific applications, ensuring optimal performance and reliability in a wide range of industries and environments.
As technology continues to advance, the demand for high-performance, reliable electrical connectors will only continue to grow. Gold-plated connectors, with their proven track record and versatility, are well-positioned to meet these evolving needs and contribute to the development of new, innovative products and systems across various sectors.
Leave a Reply