Introduction to Placer-assisted pick-and-place
In the world of electronics manufacturing, pick-and-place machines have become an essential tool for accurately and efficiently placing components onto printed circuit boards (PCBs). These machines have revolutionized the industry by automating the process of component placement, significantly reducing human error and increasing production speeds. However, traditional fully-automated pick-and-place machines can be costly and may not always be the best solution for low-volume production or prototyping. This is where placer camera-assisted manual pick-and-place machines come into play.
What is a Placer Camera-Assisted Manual Pick-and-Place Machine?
A placer camera-assisted manual pick-and-place machine is a semi-automated solution that combines the precision of a camera-guided system with the flexibility of manual component placement. These machines typically consist of a work table, a camera system, a monitor, and a manual placement tool. The camera system is used to guide the operator in accurately placing components onto the PCB, while the manual placement tool allows for more control and adaptability compared to fully-automated machines.
Benefits of Using a Placer Camera-Assisted Manual Pick-and-Place Machine
- Cost-effective solution for low-volume production and prototyping
- Increased accuracy compared to fully manual placement
- Greater flexibility in handling a variety of component sizes and shapes
- Easier to set up and operate than fully-automated machines
- Reduced investment in equipment and maintenance costs
How Placer Camera-Assisted Manual Pick-and-Place Machines Work
System Components
A typical placer camera-assisted manual pick-and-place machine consists of the following components:
- Work table: A flat surface where the PCB is placed for component assembly
- Camera system: One or more cameras mounted above the work table to capture images of the PCB and components
- Monitor: Displays the live camera feed and guides the operator during component placement
- Manual placement tool: A handheld device used by the operator to pick up and place components onto the PCB
- Lighting system: Ensures proper illumination of the work area for accurate camera imaging
Operating Principles
- PCB Alignment: The PCB is placed on the work table and aligned using fiducial markers or other reference points.
- Component Recognition: The camera system captures images of the components to be placed and uses image processing algorithms to determine their position and orientation.
- Placement Guidance: The monitor displays the live camera feed, overlaid with graphical indicators showing the correct placement position and orientation for each component.
- Manual Placement: The operator uses the manual placement tool to pick up components and place them onto the PCB, following the guidance provided by the monitor.
- Verification: After placement, the camera system can verify the accuracy of the placed components and alert the operator to any errors or misalignments.
Advantages of Placer Camera-Assisted Manual Pick-and-Place Machines
Cost Savings
One of the primary advantages of using a placer camera-assisted manual pick-and-place machine is the cost savings compared to fully-automated machines. These semi-automated solutions require a lower initial investment and have reduced maintenance costs, making them an attractive option for small businesses, startups, and educational institutions.
Flexibility
Placer camera-assisted manual pick-and-place machines offer greater flexibility in handling a wide range of component sizes and shapes. Unlike fully-automated machines that may require custom tooling or programming for non-standard components, manual placement allows for easy adaptation to different component types and sizes.
Ease of Use
Setting up and operating a placer camera-assisted manual pick-and-place machine is generally easier than fully-automated machines. The intuitive user interface and real-time guidance provided by the camera system make it possible for operators with minimal training to achieve accurate component placement.
Scalability
As production volumes increase, placer camera-assisted manual pick-and-place machines can easily be scaled up by adding more machines or operators. This scalability allows businesses to grow their production capacity without the need for significant capital investments in fully-automated equipment.
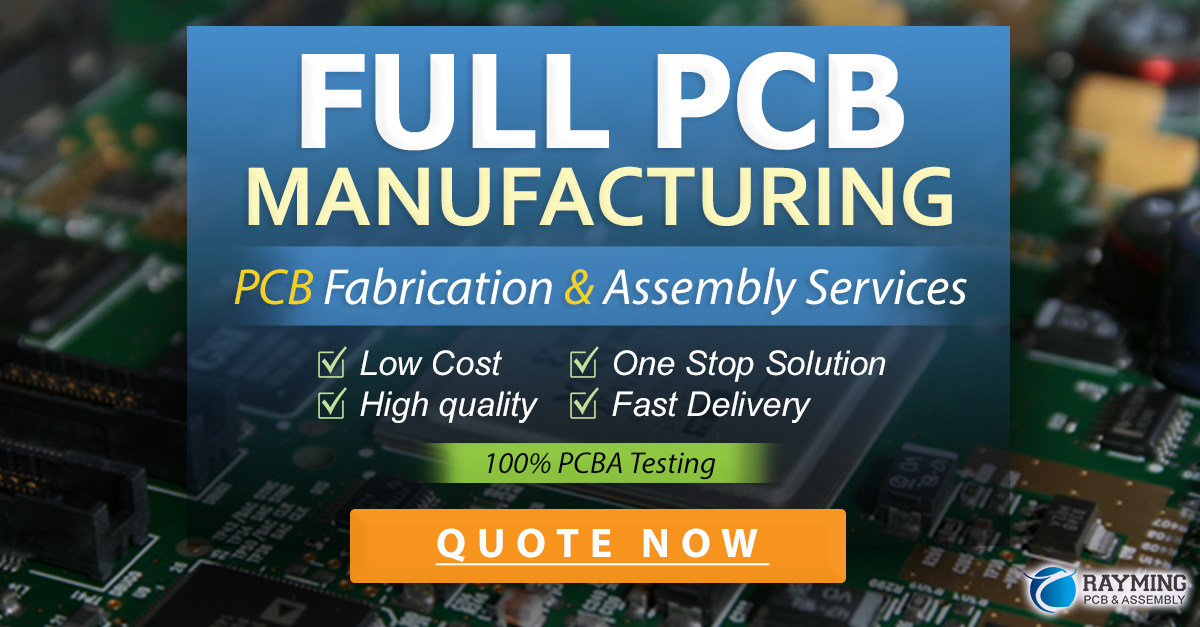
Applications of Placer Camera-Assisted Manual Pick-and-Place Machines
Prototyping and Low-Volume Production
Placer camera-assisted manual pick-and-place machines are ideal for prototyping and low-volume production runs. They allow for quick setup and changeover between different PCB designs, making them suitable for businesses that require flexibility in their manufacturing processes.
Education and Training
These machines are also valuable tools for education and training purposes. Universities, technical schools, and training centers can use placer camera-assisted manual pick-and-place machines to teach students about electronics manufacturing processes and provide hands-on experience with semi-automated assembly equipment.
Rework and Repair
In addition to assembly, placer camera-assisted manual pick-and-place machines can be used for rework and repair tasks. The camera system’s precision guidance allows operators to easily replace or reposition components on existing PCBs, saving time and effort compared to fully manual rework processes.
Choosing the Right Placer Camera-Assisted Manual Pick-and-Place Machine
When selecting a placer camera-assisted manual pick-and-place machine, consider the following factors:
-
Camera System: Look for a machine with a high-resolution camera system that provides clear, detailed images of the PCB and components. Some machines may offer multiple cameras for increased accuracy and coverage.
-
Lighting: Adequate lighting is crucial for accurate camera imaging. Choose a machine with an adjustable lighting system that can accommodate various PCB and component types.
-
Work Area: Consider the size of the PCBs you will be working with and ensure that the machine’s work table is large enough to accommodate them comfortably.
-
Software: Evaluate the machine’s software interface for ease of use, customization options, and compatibility with your existing design files and formats.
-
Placement Accuracy: Check the machine’s specified placement accuracy to ensure it meets your requirements for component positioning and alignment.
-
Support and Training: Look for a manufacturer that offers comprehensive support and training resources to help you get the most out of your placer camera-assisted manual pick-and-place machine.
Best Practices for Using Placer Camera-Assisted Manual Pick-and-Place Machines
To optimize the performance and efficiency of your placer camera-assisted manual pick-and-place machine, follow these best practices:
-
Ensure Proper Calibration: Regularly calibrate the camera system and work table to maintain accurate component placement.
-
Keep the Work Area Clean: Maintain a clean and organized work area to prevent debris from interfering with the camera system or component placement.
-
Use Appropriate Lighting: Adjust the lighting system to provide optimal illumination for the specific PCB and components being assembled.
-
Follow ESD Precautions: Implement electrostatic discharge (ESD) prevention measures to protect sensitive components during handling and placement.
-
Provide Operator Training: Ensure that machine operators receive proper training on the use of the placer camera-assisted manual pick-and-place machine and its software interface.
Frequently Asked Questions (FAQ)
-
Q: What is the typical placement accuracy of a placer camera-assisted manual pick-and-place machine?
A: The placement accuracy of these machines can vary depending on the specific model and configuration. However, most placer camera-assisted manual pick-and-place machines offer a placement accuracy of ±0.1 mm or better. -
Q: Can placer camera-assisted manual pick-and-place machines handle surface-mount devices (SMDs)?
A: Yes, these machines are capable of handling a wide range of component types, including surface-mount devices (SMDs). The camera system and manual placement tool allow for precise positioning of small and delicate components. -
Q: How much training is required to operate a placer camera-assisted manual pick-and-place machine?
A: The amount of training required can vary depending on the complexity of the machine and the operator’s prior experience. However, most operators can become proficient with these machines after a few hours of hands-on training and practice. -
Q: Can placer camera-assisted manual pick-and-place machines be used for double-sided PCB Assembly?
A: Yes, many placer camera-assisted manual pick-and-place machines support double-sided PCB assembly. The camera system can be used to guide the operator in placing components on both sides of the PCB accurately. -
Q: What is the typical cost of a placer camera-assisted manual pick-and-place machine compared to a fully-automated machine?
A: The cost of a placer camera-assisted manual pick-and-place machine is generally significantly lower than that of a fully-automated machine. While the exact cost difference can vary depending on the specific models and features, semi-automated machines can often be purchased for a fraction of the cost of their fully-automated counterparts.
Conclusion
Placer camera-assisted manual pick-and-place machines offer a cost-effective and flexible solution for electronics manufacturers engaged in prototyping, low-volume production, and education. By combining the precision of a camera-guided system with the adaptability of manual placement, these machines bridge the gap between fully manual and fully automated assembly processes.
When considering the implementation of a placer camera-assisted manual pick-and-place machine, it is essential to evaluate factors such as camera system quality, lighting, work area size, software usability, and placement accuracy. By selecting the right machine and following best practices for operation and maintenance, businesses can optimize their assembly processes and achieve high-quality results while controlling costs.
As the electronics industry continues to evolve, placer camera-assisted manual pick-and-place machines will likely play an increasingly important role in enabling small businesses, startups, and educational institutions to participate in the growing market for innovative electronic products. By embracing semi-automated assembly solutions, these organizations can remain competitive and responsive to the ever-changing demands of the industry.
Leave a Reply