Printed circuit boards (PCBs) are essential components in modern electronics. A PCB serves as the base for mounting and electrically connecting electronic components using conductive pathways etched from copper sheets laminated onto a non-conductive substrate. During PCB assembly, a solder stencil is used to apply solder paste to the PCB in the exact locations where components will be placed. Choosing the right PCB stencil manufacturer is critical for ensuring high quality and reliable solder joints. This article provides guidance on selecting the optimal stencil supplier for your needs.
Key Considerations When Choosing a PCB Stencil Manufacturer
Stencil Material
PCB stencils are commonly made from stainless steel, nickel alloy, or brass. Stainless steel offers high durability and longevity. Nickel alloy stencils provide good release from solder paste. Brass stencils are lower cost but wear faster than steel or nickel. Consider the stencil material based on your budget, PCB design, and production volume.
Stencil Thickness
Stencil thickness ranges from 3 mils to 8 mils, with 5 or 6 mil being standard. Thinner stencils allow for finer features but warp easier. Thick stencils are sturdier but limit resolution. Select a thickness able to support your smallest solder pads and component lead spaces.
Stencil Design
The stencil design must align precisely with the PCB design to ensure accurate solder paste deposition. Work with a manufacturer capable of translating your Gerber files into an optimal stencil layout. They should advise on the best aperture shapes and sizes.
Stencil Manufacturing Process
Stencils are produced by laser cutting or electroforming. Laser cutting can create complex apertures but has limitations on size and roughness. Electroforming involves plating metal through a photoresist mask to form smooth walls ideal for small apertures. Choose the process suited for your design.
Stencil Tolerances
The tightest tolerances ensure solder paste prints accurately on chip packages with ultra-fine pitch. Ask the manufacturers about their capabilities for holding X-Y positional tolerances and achieving tight aperture dimensions.
Stencil Surface Finish
A smooth stencil surface allows consistent solder paste release. Electroformed stencils provide the best finish. Laser cut stencils may require electropolishing to smooth edges. Inquire about surface roughness measurements.
Stencil Cleaning
Some stencil manufacturers offer cleaning and nano-coating services to maintain stencil performance. This prolongs stencil life and prevents solder paste build up during re-use. Consider including these services for high volume production.
Comparing Leading PCB Stencil Manufacturers
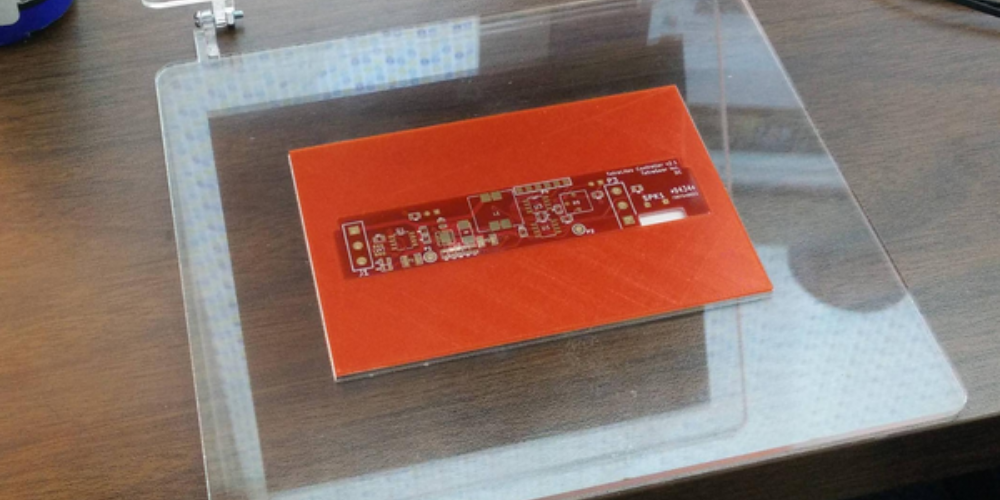
Here is an overview of top stencil suppliers and their key capabilities:
Manufacturer | Materials | Thicknesses | Tolerance | Finish | Other Services |
---|---|---|---|---|---|
Stencils Unlimited | Stainless Steel, Brass | 3-10 mil | +/-0.002 in | Laser cut, Electropolish | Cleaning, nanocoating |
Metal Etch Services | Stainless, Brass, Nickel | 2-8 mil | +/-0.001 in | Laser, Electroform | Cleaning, inspection |
Swift Precision Stencils | Stainless, Nickel | 4-8 mil | +/-0.001 in | Laser, Electroform | Prototype stencils |
Best Stencils | Stainless, Brass | 3-6 mil | +/-0.0005 in | Laser, Electroform | Next day turnaround |
ProtoPoint | Stainless, Nickel, Brass | 3-6 mil | +/-0.001 in | Laser, Electroform | Prototype stencils |
This table summarizes specifications for some well-known stencil companies. Compare their capabilities and lead times to find the best match for your specific needs. ProtoPoint and Best Stencils are good choices for fast prototype stencils. Metal Etch Services offers the tightest tolerances. Stencils Unlimited provides the widest range of materials and services.
What To Look For When Evaluating PCB Stencil Manufacturers
- Experience with your type of PCB – Select a manufacturer familiar with your board technology, components, and solder paste. They can recommend the optimal stencil design.
- Range of capabilities – Look for the ability to manufacture stencils for conventional and fine pitch SMT boards, thick/thin boards, and other specialized PCBs.
- Quality certifications – Ask for evidence of quality systems such as ISO 9001 or IPC certifications. This ensures repeatable and reliable processes.
- Responsiveness – Choose a provider that is easy to contact for technical questions, design reviews, and turnaround time inquiries.
- Pricing/lead time tradeoffs – Compare price versus lead time to find the best value. Fast turnaround proto stencils often cost more.
- Willingness to partner – Look for a manufacturer interested in becoming an extension of your team for the long term stencil supply chain.
Selecting a qualified stencil maker that meets these criteria will help ensure high quality solder paste printing and a smooth PCB assembly process. Investing in the right supplier relationship generates value over time through optimized stencil performance.
When Is It Advisable To Change PCB Stencil Manufacturers?
Sometimes it makes good business sense to switch stencil suppliers even after establishing a relationship. Reasons why a manufacturer change may be warranted:
- The current supplier lacks capabilities needed for new PCB technologies or design requirements.
- They have consistent quality problems that impact stencil or PCB assembly yield.
- Lead times stretch out and cannot meet production schedules.
- Pricing increases substantially year over year with no added value.
- Mergers or acquisitions alter their focus away from your business segment.
- The provider shows poor responsiveness or lack of interest in partnership.
- You identify a supplier who offers demonstrably better service at lower cost.
Changing stencil manufacturers involves a transition period and new qualification process. Weigh this effort against the long-term benefits of improved quality, capability, lead times, pricing, or service levels before switching. Get stakeholder input and make data-driven decisions.
Tips For Successfully Switching PCB Stencil Manufacturers
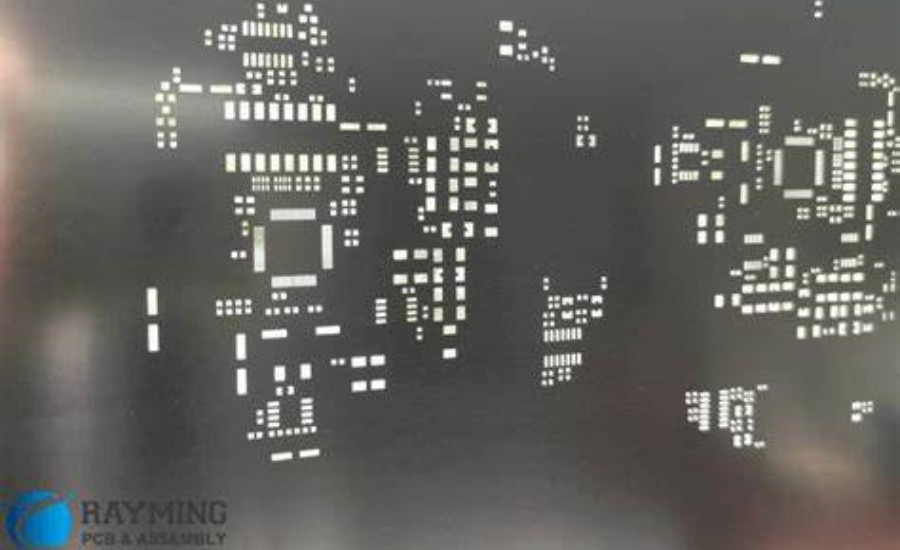
If a change is needed, follow these best practices to ensure a smooth transition:
- Do a thorough supplier evaluation – Review multiple vendors on all critical requirements using scorecards or weighted criteria.
- Begin communications early – Initiate technical discussions for design file transfer, process review, lead time targets, etc.
- Phase in the change – Run some parallel builds with both suppliers during qualification to validate process compatibility.
- Get alignment internally – Make sure assemblers, process engineers, and management all support the change. Address any objections.
- Validate first articles – Order prototype stencils to verify quality before full production switch.
- Analyze results – Monitor key metrics compared to prior supplier to confirm improvements gained. Share data internally.
- Provide feedback – Have open discussions with the new supplier on progress and any issues to resolve during ramp up.
With careful upfront preparation, appropriate qualification, and ongoing communications, OEMs can change PCB stencil partners to achieve better technical, quality and commercial outcomes.
Frequently Asked Questions About PCB Stencil Manufacturers
Here are answers to some common questions about selecting and working with PCB stencil manufacturers:
Why is stencil quality so critical for PCB assembly?
The solder stencil transfers precise amounts of solder paste to establish reliable electrical and mechanical connections between surface mount components and solder pads on the printed circuit board. Defects such as clogged apertures, dimensional errors, or warp in the stencil lead directly to solder paste printing issues that can impact product quality and yields.
What are recommended stencil inspection criteria?
Key criteria are: stencil thickness uniformity, aperture positional accuracy, aperture width/length to CAD, aperture perpendicularity, surface finish/defects, cleanliness, frame flatness, and laser cut edge roughness (for laser cut stencils). These should match specifications agreed with the stencil manufacturer.
How often should stencils be cleaned during PCB production?
A general rule of thumb is to clean the stencil after every 8-10 print cycles. However, the optimal cleaning frequency depends on factors such as solder paste type, board complexity, aperture size, and environmental conditions. Work with your stencil supplier and solder paste vendor to determine the ideal interval.
What is nanocoating and when should it be applied to stencils?
Nanocoating is an ultra-thin polymer layer applied to stencil surfaces to control the wetting and release characteristics of solder paste. Nanocoating helps maintain consistent paste transfer through many reuses of the stencil. It should be reapplied per the coating supplier’s recommendations based on usage volume.
How can I determine if it is time to replace a stencil?
Signs that a stencil should be replaced include severe aperture clogging not removable with cleaning, permanent frame damage/warpage, tears or breaches in the stencil foil, and unrecoverable dents or scratches preventing paste release. Gradual dimensional changes also indicate replacement is needed.
Leave a Reply