Introduction to PCB Classification
Printed Circuit Boards (PCBs) are essential components in modern electronics, providing a platform for interconnecting various electronic components. To ensure proper functionality and reliability, PCBs are classified based on several criteria, including their pattern complexity and drill hole requirements. Two key classifications used in the PCB industry are Pattern Class and Drill Class.
In this article, we will delve into the details of PCB Pattern Class and Drill Class, exploring their definitions, importance, and how they impact the manufacturing process. By understanding these classifications, designers and manufacturers can effectively communicate and produce high-quality PCBs that meet the required specifications.
What is PCB Pattern Class?
PCB Pattern Class, also known as Copper Foil Class, refers to the complexity and precision of the copper traces and spaces on a PCB. It is a standardized system used to categorize PCBs based on their minimum trace width and spacing requirements. The Pattern Class determines the level of precision and manufacturing capabilities needed to produce a particular PCB design.
IPC-6012 Standard for Pattern Class
The IPC (Association Connecting Electronics Industries) has established the IPC-6012 standard, which defines three main Pattern Classes for rigid PCBs:
Pattern Class | Minimum Trace Width | Minimum Spacing |
---|---|---|
Class 1 | 0.2 mm (8 mil) | 0.2 mm (8 mil) |
Class 2 | 0.1 mm (4 mil) | 0.1 mm (4 mil) |
Class 3 | 0.075 mm (3 mil) | 0.075 mm (3 mil) |
-
Class 1: This is the least demanding Pattern Class, suitable for general-purpose PCBs with larger trace widths and spacings. Class 1 PCBs are commonly used in consumer electronics and applications where high precision is not critical.
-
Class 2: Class 2 PCBs have tighter trace width and spacing requirements compared to Class 1. They are widely used in industrial, telecommunications, and medical applications where higher precision and reliability are necessary.
-
Class 3: This is the most stringent Pattern Class, requiring the smallest trace widths and spacings. Class 3 PCBs are used in high-performance applications, such as aerospace, military, and advanced medical devices, where extreme precision and reliability are essential.
Importance of Pattern Class in PCB Design and Manufacturing
Selecting the appropriate Pattern Class is crucial in PCB design and manufacturing for several reasons:
-
Design Feasibility: The Pattern Class determines the minimum trace width and spacing that can be reliably manufactured. Choosing a higher Pattern Class allows for more complex and compact designs, enabling the integration of more components and features on a smaller PCB area.
-
Manufacturing Capability: PCB Manufacturers must have the necessary equipment, processes, and expertise to produce PCBs of a specific Pattern Class. Higher Pattern Classes require more advanced manufacturing technologies, such as high-resolution imaging, precise etching, and strict quality control measures.
-
Cost Implications: As the Pattern Class increases, so does the manufacturing complexity and cost. Class 3 PCBs are generally more expensive to produce than Class 1 or Class 2 PCBs due to the higher precision requirements and specialized manufacturing processes involved.
-
Reliability and Performance: PCBs with higher Pattern Classes offer improved signal integrity, reduced crosstalk, and better overall performance. The tighter trace widths and spacings minimize electromagnetic interference (EMI) and ensure reliable operation in demanding environments.
What is PCB Drill Class?
PCB Drill Class refers to the categorization of PCBs based on the precision and size of the drilled holes required for component mounting and interconnection. Drill holes are critical features in PCBs, as they allow for the insertion of through-hole components, vias for inter-layer connections, and mounting holes for mechanical stability.
IPC-6012 Standard for Drill Class
The IPC-6012 standard also defines three main Drill Classes for rigid PCBs:
Drill Class | Minimum Drill Hole Size | Tolerance |
---|---|---|
Class 1 | 0.5 mm (20 mil) | ±0.15 mm |
Class 2 | 0.3 mm (12 mil) | ±0.10 mm |
Class 3 | 0.2 mm (8 mil) | ±0.08 mm |
-
Class 1: This Drill Class is suitable for general-purpose PCBs with larger drill hole sizes and tolerances. Class 1 drill holes are commonly used for through-hole components with standard lead diameters and non-critical mounting holes.
-
Class 2: Class 2 drill holes have smaller diameters and tighter tolerances compared to Class 1. They are used in applications where higher precision and reliability are required, such as in industrial controls, automotive electronics, and telecommunications equipment.
-
Class 3: This is the most demanding Drill Class, featuring the smallest drill hole sizes and the tightest tolerances. Class 3 drill holes are essential for high-density PCBs, fine-pitch components, and advanced packaging technologies, such as ball grid arrays (BGAs) and chip-scale packages (CSPs).
Importance of Drill Class in PCB Design and Manufacturing
Choosing the appropriate Drill Class is essential for ensuring the proper functionality and reliability of a PCB:
-
Component Compatibility: The Drill Class determines the minimum drill hole size that can accommodate specific component lead diameters. Selecting the correct Drill Class ensures that components can be properly inserted and soldered onto the PCB.
-
Manufacturing Feasibility: PCB manufacturers must have the necessary drilling equipment and processes to produce holes of a specific Drill Class. Higher Drill Classes require more precise drilling machines, smaller drill bits, and tighter process controls to achieve the required hole sizes and tolerances.
-
Cost Considerations: As with Pattern Class, higher Drill Classes generally increase the manufacturing cost of a PCB. The smaller drill hole sizes and tighter tolerances associated with Class 3 require more advanced drilling equipment and slower drilling speeds, resulting in higher production costs.
-
Reliability and Signal Integrity: Proper drill hole sizes and tolerances are critical for ensuring reliable electrical connections and minimizing signal integrity issues. Smaller drill holes enable higher-density PCB designs and improve signal performance by reducing parasitic inductance and capacitance.
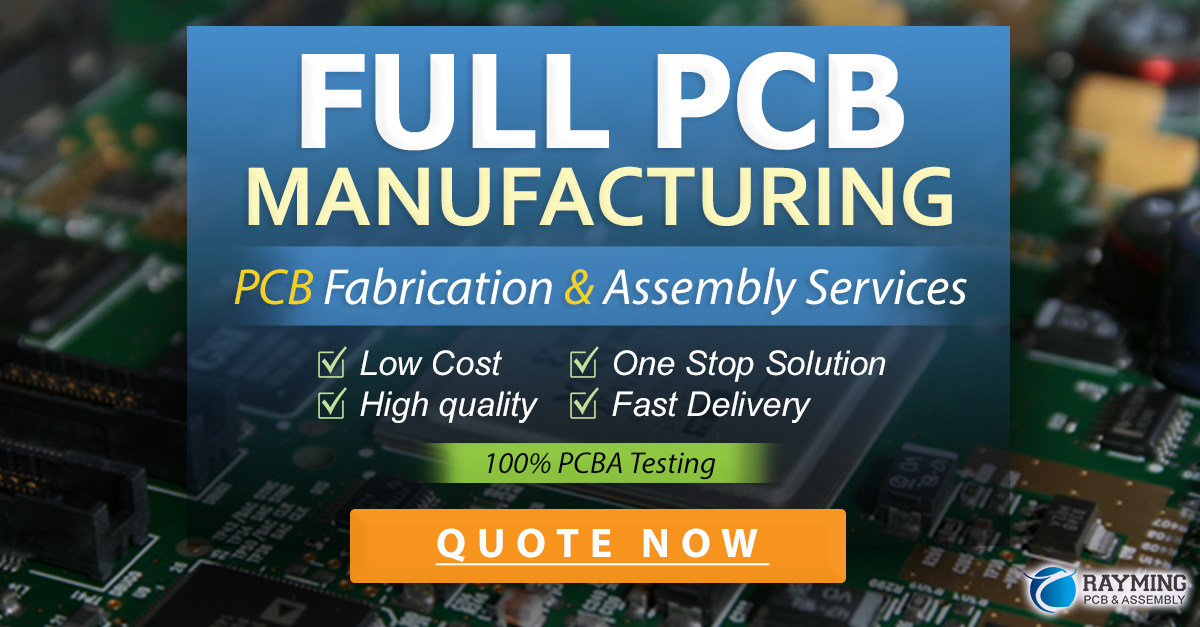
Combining Pattern Class and Drill Class in PCB Design
When designing a PCB, it is essential to consider both the Pattern Class and Drill Class to ensure that the design is manufacturable, reliable, and meets the required performance criteria. The combination of Pattern Class and Drill Class determines the overall complexity and precision of the PCB.
Designers should follow these guidelines when selecting Pattern Class and Drill Class:
-
Understand the Application Requirements: Consider the specific requirements of the application, such as signal integrity, component density, and environmental factors, to determine the necessary level of precision for both the copper traces and drill holes.
-
Consult with PCB Manufacturers: Engage with PCB manufacturers early in the design process to discuss their capabilities and limitations regarding Pattern Class and Drill Class. This collaboration helps ensure that the design is feasible and can be manufactured reliably.
-
Balance Cost and Performance: Evaluate the trade-offs between cost and performance when selecting Pattern Class and Drill Class. Higher classes offer better precision and performance but come with increased manufacturing costs. Strike a balance that meets the application’s requirements while considering budget constraints.
-
Design for Manufacturability (DFM): Follow DFM guidelines to ensure that the PCB design is compatible with the chosen Pattern Class and Drill Class. This includes adhering to minimum trace widths, spacings, and drill hole sizes, as well as considering aspects such as copper balance, solder mask design, and panelization.
FAQ
1. What is the difference between Pattern Class and Drill Class in PCB classification?
Pattern Class refers to the complexity and precision of the copper traces and spaces on a PCB, while Drill Class pertains to the precision and size of the drilled holes required for component mounting and interconnection.
2. How do I choose the appropriate Pattern Class and Drill Class for my PCB design?
The selection of Pattern Class and Drill Class depends on the specific requirements of your application, such as signal integrity, component density, and environmental factors. Consult with PCB manufacturers and consider the trade-offs between cost and performance to make an informed decision.
3. Can I mix different Pattern Classes and Drill Classes on the same PCB?
While it is technically possible to have different Pattern Classes and Drill Classes on the same PCB, it is generally not recommended. Mixing classes can complicate the manufacturing process, increase costs, and potentially compromise the overall reliability of the PCB. It is best to design the entire PCB to the highest required class for consistency and manufacturability.
4. How do higher Pattern Classes and Drill Classes affect the cost of PCB manufacturing?
Higher Pattern Classes and Drill Classes generally increase the manufacturing cost of a PCB. The tighter tolerances and smaller features associated with higher classes require more advanced manufacturing equipment, specialized processes, and slower production speeds, resulting in higher overall costs.
5. Are there any additional classifications beyond Pattern Class and Drill Class for PCBs?
Yes, there are several other classifications and standards used in the PCB industry, such as material classification (e.g., FR-4, polyimide), surface finish (e.g., HASL, ENIG), and solder mask color (e.g., green, black). These classifications address different aspects of PCB design and manufacturing, ensuring compatibility, reliability, and adherence to industry standards.
Conclusion
PCB classification based on Pattern Class and Drill Class is essential for ensuring the proper design, manufacturing, and reliability of printed circuit boards. Understanding these classifications enables designers to create PCBs that meet the required precision, performance, and manufacturability standards.
By selecting the appropriate Pattern Class and Drill Class, designers can balance the complexity, cost, and reliability of their PCB designs. Collaborating closely with PCB manufacturers and following industry guidelines, such as the IPC-6012 standard, helps streamline the design and manufacturing process, ultimately resulting in high-quality PCBs that meet the demands of various applications.
As technology advances and electronic devices become increasingly sophisticated, the importance of PCB classification will only continue to grow. Designers and manufacturers must stay up-to-date with the latest standards and best practices to ensure the successful development and production of PCBs that drive innovation across industries.
Leave a Reply