Introduction to PCB Classification
Printed Circuit Boards (PCBs) are essential components in modern electronics, providing a platform for interconnecting electronic components and facilitating the flow of electrical signals. To ensure the proper functioning and reliability of PCBs, it is crucial to classify them based on various criteria. Two key aspects of PCB classification are pattern class and drill class, which play significant roles in determining the manufacturing process, cost, and overall quality of the PCBs.
In this article, we will delve into the details of PCB classification, focusing on pattern class and drill class. We will explore the different categories within each class, their characteristics, and their implications for PCB design and manufacturing. Additionally, we will discuss the importance of understanding these classifications and how they contribute to the successful production of high-quality PCBs.
What is Pattern Class?
Pattern class, also known as feature size or line width/spacing, refers to the minimum width of the copper traces and the spacing between them on a PCB. It is a critical factor in determining the manufacturing capabilities and limitations of a PCB Fabrication facility. The pattern class directly influences the design rules, which dictate the minimum trace width, spacing, and other geometric constraints that must be adhered to during the PCB design process.
Pattern Class Categories
PCBs are typically classified into different pattern classes based on the minimum feature size they can accommodate. The most common pattern class categories are as follows:
Pattern Class | Minimum Line Width/Spacing |
---|---|
Class 1 | 0.100 mm (4 mil) |
Class 2 | 0.075 mm (3 mil) |
Class 3 | 0.050 mm (2 mil) |
Class 4 | 0.025 mm (1 mil) |
Class 5 | 0.015 mm (0.6 mil) |
Class 6 | 0.010 mm (0.4 mil) |
As the pattern class increases, the minimum feature size decreases, allowing for finer traces and closer spacing between them. Higher pattern classes enable the design of more compact and dense PCBs, which is particularly important for applications requiring miniaturization and high-density interconnects.
Implications of Pattern Class
The choice of pattern class has several implications for PCB design and manufacturing:
-
Design Complexity: Higher pattern classes allow for more intricate and complex PCB designs, enabling the integration of a larger number of components and interconnects within a smaller footprint.
-
Manufacturing Capability: Not all PCB fabrication facilities are equipped to handle higher pattern classes. As the pattern class increases, the manufacturing process becomes more challenging and requires advanced equipment and expertise.
-
Cost: PCBs with higher pattern classes generally cost more to manufacture due to the increased complexity and precision required in the fabrication process.
-
Signal Integrity: Finer traces and closer spacing associated with higher pattern classes can impact signal integrity, requiring careful design considerations to mitigate issues such as crosstalk and impedance mismatches.
What is Drill Class?
Drill class refers to the classification of PCBs based on the smallest hole diameter that can be drilled on the board. The drill holes are used for various purposes, such as mounting through-hole components, creating vias for inter-layer connections, and providing mechanical support. The drill class determines the capabilities and limitations of the PCB fabrication process in terms of hole size and accuracy.
Drill Class Categories
PCBs are classified into different drill classes based on the minimum hole diameter they can accommodate. The most common drill class categories are as follows:
Drill Class | Minimum Hole Diameter |
---|---|
Class 1 | 0.800 mm (31.5 mil) |
Class 2 | 0.500 mm (19.7 mil) |
Class 3 | 0.350 mm (13.8 mil) |
Class 4 | 0.250 mm (9.8 mil) |
Class 5 | 0.200 mm (7.9 mil) |
Class 6 | 0.150 mm (5.9 mil) |
As the drill class increases, the minimum hole diameter decreases, allowing for smaller and more precise drilling on the PCB. Higher drill classes enable the use of smaller components and more compact PCB designs.
Implications of Drill Class
The choice of drill class has several implications for PCB design and manufacturing:
-
Component Selection: The drill class determines the types and sizes of components that can be used on the PCB. Higher drill classes allow for the use of smaller through-hole components and more compact component placement.
-
Manufacturing Capability: Similar to pattern class, not all PCB fabrication facilities are equipped to handle higher drill classes. As the drill class increases, the drilling process becomes more challenging and requires specialized equipment and skilled operators.
-
Cost: PCBs with higher drill classes generally cost more to manufacture due to the increased precision and specialized equipment required in the drilling process.
-
Reliability: Smaller drill holes associated with higher drill classes can impact the mechanical strength and reliability of the PCB, particularly in applications subjected to vibration or mechanical stress.
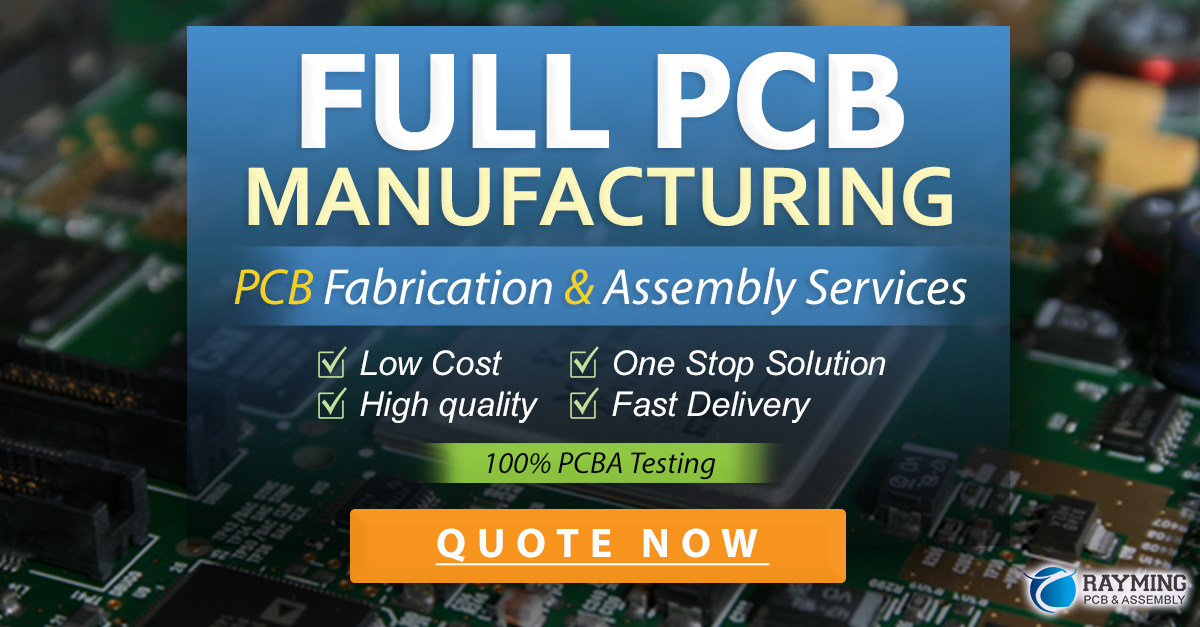
Importance of Understanding PCB Classification
Understanding PCB classification based on pattern class and drill class is crucial for several reasons:
-
Design Optimization: Knowledge of the available pattern and drill classes enables PCB designers to optimize their designs, ensuring compatibility with the manufacturing capabilities of the chosen fabrication facility.
-
Cost Estimation: Understanding the cost implications of different pattern and drill classes helps in accurately estimating the manufacturing costs of PCBs, allowing for informed decision-making during the design phase.
-
Manufacturability: Familiarity with the limitations and capabilities of different pattern and drill classes ensures that PCBs are designed with manufacturability in mind, reducing the likelihood of production issues and delays.
-
Supplier Selection: When choosing a PCB fabrication supplier, understanding their capabilities in terms of pattern and drill classes is essential to ensure they can meet the specific requirements of the PCB design.
-
Quality Assurance: Adhering to the appropriate pattern and drill class guidelines helps maintain the quality and reliability of the manufactured PCBs, reducing the risk of defects and failures.
Frequently Asked Questions (FAQ)
-
Q: What happens if I design a PCB with a pattern class that exceeds the capabilities of the chosen fabrication facility?
A: If a PCB design includes features that exceed the capabilities of the chosen fabrication facility, it may result in manufacturing issues, delays, or even the inability to produce the PCB. It is essential to ensure that the PCB design aligns with the capabilities of the selected fabrication facility to avoid such problems. -
Q: Can I mix different pattern classes or drill classes within the same PCB?
A: While it is technically possible to have different pattern classes or drill classes within the same PCB, it is generally not recommended. Mixing different classes can complicate the manufacturing process, increase costs, and potentially impact the overall quality and reliability of the PCB. -
Q: How do I determine the appropriate pattern class and drill class for my PCB design?
A: The choice of pattern class and drill class depends on several factors, including the complexity of the PCB design, the components used, the intended application, and the manufacturing capabilities of the chosen fabrication facility. It is advisable to consult with the fabrication facility or an experienced PCB designer to determine the most suitable classes for your specific requirements. -
Q: Are there any industry standards for PCB classification?
A: Yes, there are industry standards that provide guidelines for PCB classification. One widely recognized standard is the IPC-2220 series, which defines various aspects of PCB design and manufacturing, including pattern class and drill class. -
Q: How do pattern class and drill class affect the lead time for PCB manufacturing?
A: Higher pattern classes and drill classes often require more specialized equipment and skilled operators, which can impact the lead time for PCB manufacturing. PCBs with higher classes may have longer lead times compared to those with lower classes due to the increased complexity and precision required in the fabrication process.
Conclusion
PCB classification based on pattern class and drill class is a fundamental aspect of PCB design and manufacturing. Understanding these classifications is crucial for creating PCBs that are manufacturable, reliable, and cost-effective. By considering the capabilities and limitations of different pattern and drill classes, designers can optimize their PCB designs, select appropriate components, and ensure compatibility with the chosen fabrication facility.
Moreover, clear communication and collaboration between PCB designers and fabrication facilities are essential to ensure that the designed PCBs meet the required specifications and can be manufactured efficiently. By adhering to industry standards and best practices related to pattern class and drill class, designers and manufacturers can work together to produce high-quality PCBs that meet the demands of modern electronic applications.
As technology advances and the demand for more complex and compact PCBs grows, staying updated with the latest developments in PCB classification becomes increasingly important. Designers and manufacturers must continually adapt to new challenges and leverage advancements in materials, processes, and equipment to push the boundaries of PCB design and manufacturing capabilities.
In summary, understanding PCB classification based on pattern class and drill class is a vital skill for anyone involved in PCB design and manufacturing. By mastering these concepts and applying them effectively, designers and manufacturers can create PCBs that are optimized for performance, reliability, and cost-effectiveness, ultimately contributing to the success of electronic products in various industries.
Leave a Reply