Introduction to Metal Core PCBs
A metal core printed circuit board (MCPCB) is a type of printed circuit board that has a base made of a metal, typically aluminum or copper, instead of the more common FR-4 material. The metal core provides several advantages over traditional FR-4 PCBs:
- Excellent thermal performance – the metal core acts as a heat sink to dissipate heat from components
- Good thermal conductivity – heat spreads quickly through the metal base
- Ability to handle high power – the metal core can dissipate more heat than an FR-4 board
- Thinner boards possible – less insulating material needed with highly conductive metal core
- More rigid construction
Some key applications that benefit from MCPCBs include:
- LED lighting – the metal core MCPCB dissipates LED heat efficiently
- Power electronics – IGBTs, power diodes can be mounted on MCPCBs
- RF circuitry – the metal core has good electromagnetic shielding
- Automotive electronics – MCPCBs withstand high temps under hood
In this article, we’ll take a more in-depth look at metal core PCB construction, properties, benefits, and applications.
Construction of Metal Core PCBs
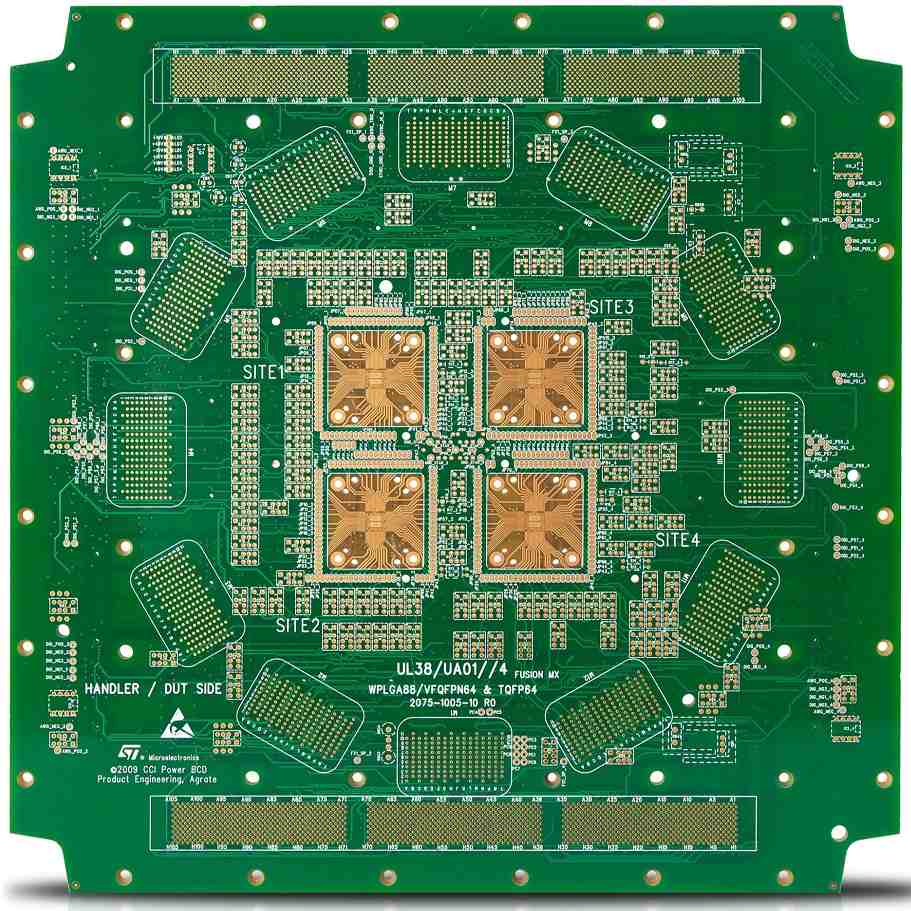
The construction of a metal core PCB starts with a flat sheet of aluminum or copper as the base layer. The thickness of this metal layer can vary based on the power requirements and mechanical needs, but is typically 0.8mm to 3mm thick.
A dielectric layer is then bonded to the metal base. This electrically insulates the metal core from the subsequently applied circuit layers. The dielectric material is typically a thin layer (0.1-0.3mm) of thermally conductive material like aluminum oxide, silicon nitride, or berlyllium oxide. This creates a metal-insulator-metal sandwich.
The circuit layers are then built up on top of the dielectric layer using standard PCB fabrication processes. This includes applying a copper foil layer, imaging the conductor pattern with photolithography, and etching away unwanted copper. Multiple circuit layers can be stacked and connected with plated through holes or vias.
A solder mask and silkscreen legend are applied to the outer circuit layers. Additional coatings like conformal coating or potting can be applied for protection, insulation, or heat transfer depending on the application.<div align=”center”>
Table 1: Typical Metal Core PCB Construction
Layer | Material | Thickness |
---|---|---|
Metal Base | Aluminum or Copper | 0.8mm – 3mm |
Dielectric | Alumina or AlN | 0.1mm – 0.3mm |
Circuit Layer 1 | Copper | 35 μm |
Circuit Layer 2 | Copper | 35 μm |
Solder Mask | LPI | 30-50 μm |
</div>
This layered construction with a metal core gives the PCB thermal, mechanical, and electrical advantages compared to standard FR-4 boards.
Benefits of Using Metal Core PCBs
Here are some of the main benefits of selecting a metal core PCB:
Thermal Performance
The thick metal base provides an excellent conduit to dissipate heat from power components mounted on the board. The dielectric layer electrically isolates the devices while the metal core spreads heat laterally through the PCB and to the board edges. This allows effective cooling of components like LEDs and power semiconductors. Metal core PCBs can operate at higher temperatures than organic boards.
Electrical Shielding
The conductive metal base provides good electromagnetic shielding from electrical noise. This helps minimize interference in sensitive RF and high-speed digital circuits.
Thermal Stability
Since the metal core has a low coefficient of thermal expansion (CTE), MCPCBs are more dimensionally stable over a range of temperatures. This helps maintain reliable solder joints and bonds during thermal cycling.
High Power and Current
Metal core PCBs can handle higher power dissipation and current levels than standard FR-4 boards. The metal base acts as a heat spreader while also providing a thermal mass to dampen temperature swings.
Thin Profile
With an MCPCB, you can use a thinner dielectric layer since the metal core provides mechanical rigidity. This allows more compact PCB stacks and thinner end products.
Light Weight
Aluminum has a density one-third that of copper, so aluminum core PCBs provide a lighter-weight option than copper for aerospace and portable electronics applications.
Applications and Examples
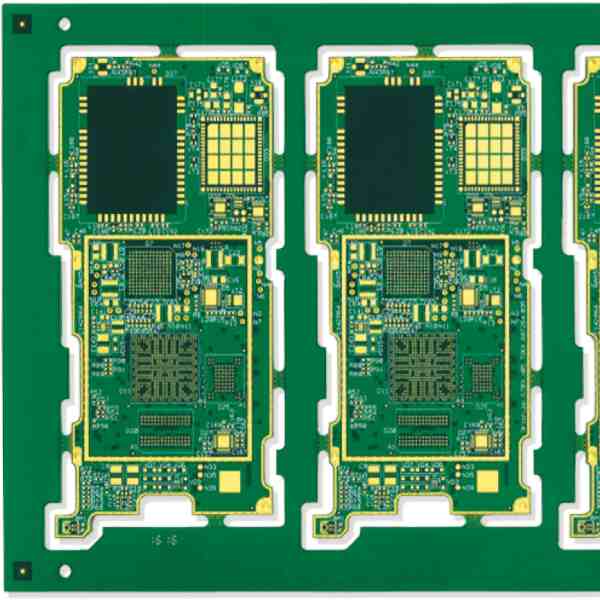
The unique thermal and electrical properties of MCPCBs make them well suited for a variety of applications:
LED Lighting
Metal core PCBs are the preferred choice for LED lighting modules and luminaires. The LEDs can be mounted directly on the metal core to dissipate heat, allowing high power density designs. The PCB can withstand the operating temperature (>85°C) within a lighting fixture.<div align=”center”>
LED star MCPCB for a lighting module (Image credit: MCPCB Manufacturer)</div>
Automotive Electronics
For automotive underhood electronics like engine control units (ECUs) and LED headlights, MCPCBs can withstand high temperatures and thermal cycling in the engine compartment. Integrated thermoelectric coolers can be mounted directly on the PCB.
Power Converters
Switched-mode power supplies, DC-DC converters, and solar microinverters require efficient cooling of high-power semiconductors. Mounting devices like IGBTs and MOSFETs on MCPCBs allows higher power density.
RF and Microwave PCBs
The electromagnetic shielding of metal core PCBs helps minimize interference in sensitive RF, microwave, and millimeter-wave circuits. Lightweight aluminum cores are used in radar and 5G applications.
Design and Layout Considerations
Here are some key considerations when designing and laying out PCBs using metal core boards:
- Place heat-generating components in direct contact with metal core to dissipate heat. Use thermal vias if needed.
- Manage thermal expansion mismatch between components and the metal core.
- Provide isolation keepouts around sensitive analog circuits on the PCB.
- Use thermal reliefs and openings in copper layers to facilitate heat transfer.
- Include thermal sensors to monitor board temperature.
- Place components with high current draw close together to minimize conductive losses.
- Use a finish like ENIG or immersion silver that withstands high temperatures.
- Select solder mask and legend inks rated for high temperatures.
- Incorporate standoffs, guides, or other mounts to manage board flexing.
- Work closely with your PCB manufacturer to optimize design for manufacturability.
Cost Considerations
Metal core PCBs tend to have a higher cost compared to standard FR-4 boards due to material expenses and more complex manufacturing processes. However, MCPCBs provide lifecycle cost savings by enabling:
- Higher power density resulting in smaller and lighter end products
- Improved reliability and product lifetime at high temperatures
- Elimination or downsizing of heat sinks and cooling systems
For moderate volume production runs where the benefits of metal core PCBs outweigh the additional cost, they can be a sound investment to improve the product performance.
Frequently Asked Questions
Here are some common FAQs about metal core printed circuit boards:
What are the most common base metals used in MCPCBs?
Aluminum and copper are the two predominant options. Aluminum is lighter weight but has slightly lower thermal conductivity than copper. Copper offers the best thermal performance.
What thickness of metal base is typically used?
Base thickness ranges from about 0.8mm to over 3mm. Thicker bases provide better power dissipation but increase weight and cost. 1-2mm is commonly used for many applications.
What are some good dielectric materials for electrical isolation?
Alumina (aluminum oxide), aluminum nitride, silicon nitride, and beryllium oxide are popular choices. These have high dielectric strength and thermal conductivity.
How many circuit layers can you have in an MCPCB?
Although 2-layer boards are common, multi-layer boards with 4 or more layers are certainly possible with metal core PCBs depending on the fabrication process used.
How are components and devices attached to MCPCBs?
Soldering is standard, as are conductive epoxies for high temperature applications. Some power devices are sintered or diffusion bonded to aluminum core boards.
Conclusion
Metal core printed circuit boards provide unique advantages for thermal management, shielding, and power handling compared to standard FR-4 PCBs. The thermally conductive metal base allows effective cooling of heat-generating components, enabling lightweight and compact designs.
With LED lighting, automotive, power electronics, and microwave applications continuing to demand higher power densities, metal core PCBs present an attractive option to dissipate heat and achieve next-generation product performance.
Leave a Reply