Introduction
Printed circuit boards (PCBs) are essential components in almost all electronic devices and products. They provide the foundation on which chips, resistors, capacitors and other components are mounted and interconnected. While high-volume PCB production is often outsourced to large manufacturers, many companies require low volume PCB assembly for prototyping, testing, and low-rate production. This article provides an overview of low volume PCB assembly, including the process, challenges, and best practices.
What is Low Volume PCB Assembly?
Low volume PCB assembly refers to producing small batches of assembled PCBs, typically 25 boards or less per batch. This is in contrast to high volume production of thousands of identical boards. Low volume assembly is usually done for:
- Prototyping – Testing new PCB designs before finalizing for mass production.
- Small production runs – For niche products that don’t require large volumes.
- Engineering samples – Small batches for internal testing and evaluation.
The key characteristics of low volume PCB assembly are:
- Small quantities – Usually 25 boards or less per batch.
- High mix – Frequent changes in PCB designs.
- Low rate – Not a continuous high-speed process like mass production.
- Flexibility – Ability to quickly switch between different PCBs.
Low Volume PCB Assembly Process
While low volume PCB assembly is more flexible than high volume production, it still follows a general process:
1. Design
The PCB layout is designed in CAD software. For low volumes, designers aim to minimize unique parts to reduce assembly costs.
2. Fabrication
The bare PCBs are fabricated, usually in small panels of 1 to 6 boards. Various fabricators offer quick-turn prototype PCB manufacturing ideal for low volumes.
3. Parts Kitting
All the required components or bill of materials (BOM) are kitted – counted and bagged or arranged in reels and trays for the assembly process.
4. Solder Paste Application
Solder paste is stencil-printed onto the PCB pads. For low volume, solder paste can be manually applied.
5. Component Placement
Components are manually placed onto the solder paste-coated PCB. Low volume assembly may be done manually under a microscope or use automated pick-and-place machines.
6. Reflow Soldering
The board passes through a reflow oven, melting the solder paste to form solder joints to attach components.
7. Testing and Inspection
Assembled boards are visually inspected and electrically tested to verify proper assembly and functionality.
8. Packaging and Delivery
The finished circuit boards are packaged and shipped to the customer.
Low Volume Assembly Challenges
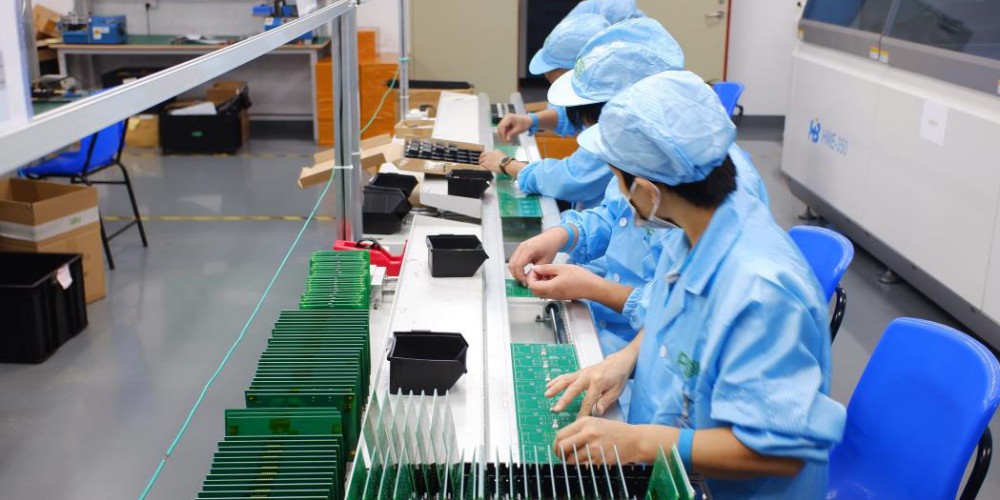
While high volume PCB assembly is well optimized for efficiency, assembling low volumes poses some unique challenges:
- Changeover – Frequent conversion between different PCB designs reduces efficiency and throughput.
- Manual processes – Small batches often rely more on manual assembly, increasing labor costs.
- Material costs – Small component quantities increase costs due to minimum order quantities.
- Testing – Must verify each board fully with no assumptions like high volume statistical sampling.
- Overhead costs – Fixed costs like programming are spread over fewer boards, increasing per unit costs.
However, a number of strategies can help maximize efficiency and reduce costs for low volume PCB assembly.
Tips for Efficient Low Volume Assembly
Here are some best practices for optimizing low volume PCB assembly:
Minimize Unique Parts
Reduce your bill of materials to the fewest unique parts needed. Reusing the same components across different PCB designs improves material supply chain and reduces changeover time.
Panelize PCBs
Fabricating multiple PCBs on a panel (like a sheet of 6 boards) improves efficiency. The entire panel can be processed together, minimizing repeated setup and handling.
Automate Processes
Automated assembly tools like pick-and-place and reflow ovens improve repeatability and throughput over manual methods for batches of 5 or more boards.
Validate Designs Upfront
Thoroughly test PCB layouts before assembly to avoid errors that require reworking assembled boards. Use design rule checks and prototyping before assembly.
Partner with EMS Provider
Work with an experienced electronics manufacturing services (EMS) provider specialized in low volume assembly. Their expertise improves quality and cost-effectiveness.
Build Small Batches
Group assembly in small batches ideally of the same PCB design. For example, build 5 copies of 3 different designs rather than 15 mixed boards.
Proactively planning for and mitigating the challenges of low volume PCB assembly helps ensure fast, high quality, and cost-optimized results.
Low Volume Assembly Equipment
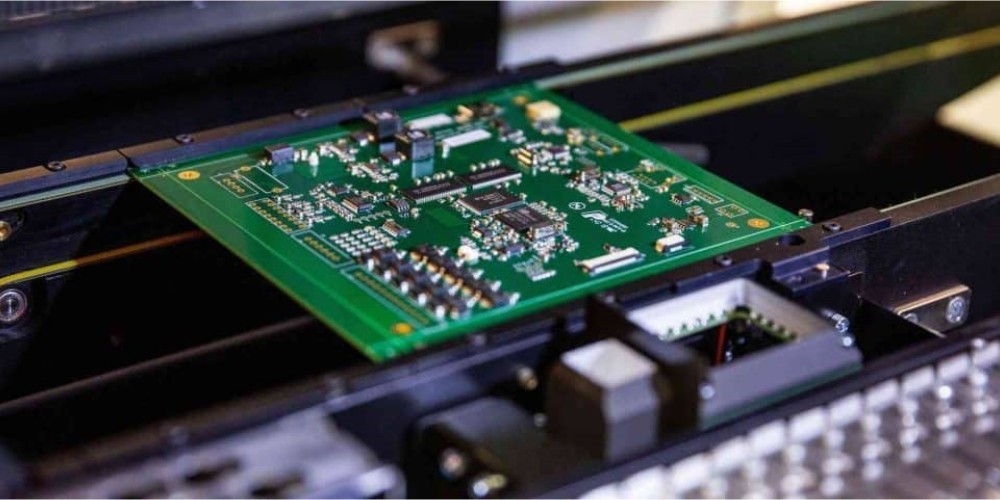
Specialized equipment is available to improve automation and repeatability for low volume PCB assembly. Here are some key types of equipment used:
Solder Paste Printer
Prints solder paste on PCB pads through a stencil. Semi-automated printers are well suited for low volumes instead of fully automated screen printers used in high volume.
Pick and Place Machine
Automatically picks components from reels, trays or sticks and places them on the PCB. Flexible benchtop units can handle a range of component sizes.
Reflow Oven
Uses precisely controlled heating zones to form solder joints by melting the solder paste. Small conveyor or batch ovens meet low volume needs.
Inspection Microscope
High magnification microscope used to visually inspect solder joints, component placement, and board quality.
Flying Probe Tester
Tests electrical connectivity and functions using probes that automatically move and contact test points on a bare or loaded board.
By combining automated equipment with manual assembly, low volume PCB production can be fast, flexible, and deliver consistent, high quality results. Proper investment in the right equipment for small-batch assembly pays dividends across prototyping and production.
Choosing a Low Volume Assembly Partner
For companies lacking in-house assembly capabilities, partnering with a contract electronics manufacturer (CEM) is the ideal solution for cost-effective, high quality low volume PCB assembly. Here are some tips for choosing an EMS partner:
Expertise and Experience
Seeks a CEM thoroughly experienced in low volume PCB assembly. They should understand the unique challenges and how to optimize the process.
Services
Look for an EMS that provides end-to-end services including PCB fabrication, test, box build assembly, etc. A one-stop shop simplifies logistics.
Quality Systems
Choose a CEM with robust quality systems like ISO 9001 certification to ensure assembly quality and reliability.
Flexibility
Seeks an EMS able to handle high mix, changing production needs, short lead times, and other flexibility required for low volumes.
Cost Optimization
A strong EMS partner will actively work with you to optimize the design, BOM, and process to reduce assembly costs for low quantities.
Communication
Frequent project communication and visibility into order status, potential issues, etc. is essential when working in low volumes.
With an experienced, capable low volume assembly partner, companies can introduce new products faster and more cost effectively by overcoming the inherent challenges of small-batch PCB assembly.<hr>
Frequently Asked Questions
Q: What are some examples of products that require low volume PCB assembly?
A: Low volume PCB assembly is commonly used for niche consumer products like high-end audio equipment, IoT devices, drones, robots, and hobbyist electronics. It also serves prototyping and R&D for nearly all electronics industries including automotive, aerospace, medical, computing, and communications.
Q: What is the typical lead time for low volume PCB assembly?
A: Lead times for low quantity assembly often range from 2 days to 2 weeks. The fastest turnarounds are usually for simple boards with standard components. More complex designs require longer lead times. However, experienced low volume assemblers can often expedite urgent orders.
Q: What are the typical order quantities for low volume assembly?
A: Typical low volume batch sizes range from 1 to 25 assembled boards. Some assemblers specialize in ultra-low volumes of 1 to 5 boards for prototyping needs. Higher volumes of ~25-250 boards are sometimes called medium volumes.
Q: How do you ensure quality with low volume PCB assembly?
A: Quality procedures are essential – components must be ESD protected, using solder paste inspection, automated optical inspection of assembly, and 100% electrical testing of completed boards. Choosing an assembler with strong quality control and process verification is recommended.
Q: How can you reduce costs for low volume PCB assembly?
A: Strategies like panelizing boards, optimizing component selection to use fewer unique parts across board designs, and working with an assembler experienced in cost-effectively supporting lower volumes can significantly reduce assembly costs.
Leave a Reply