Understanding Thermal Conductivity
Definition and Importance
Thermal conductivity is a measure of a material’s ability to conduct heat. It is denoted by the symbol “k” and is typically expressed in units of watts per meter-kelvin (W/mK). A higher thermal conductivity value indicates that the material is a better conductor of heat.
In PWBs, thermal conductivity plays a crucial role in managing Heat Dissipation. Electronic components generate heat during operation, and if this heat is not effectively dissipated, it can lead to performance degradation, reduced reliability, and even failure of the electronic system. Therefore, accurate calculation of thermal conductivity is essential for designing PWBs that can efficiently transfer heat away from critical components.
Factors Affecting Thermal Conductivity
Several factors influence the thermal conductivity of PWBs:
-
Material Composition: The thermal conductivity of a PWB is primarily determined by the materials used in its construction. Common materials include copper, fiberglass, and various types of resins. The thermal conductivity of each material contributes to the overall thermal conductivity of the PWB.
-
Layer Thickness: The thickness of the conductive layers (such as copper) and the insulating layers (such as fiberglass) affects the thermal conductivity of the PWB. Thicker conductive layers generally enhance thermal conductivity, while thicker insulating layers can impede heat transfer.
-
Copper Coverage: The amount and distribution of copper on the PWB impact its thermal conductivity. Higher copper coverage allows for better heat conduction, as copper has a relatively high thermal conductivity compared to other materials used in PWBs.
-
Via Density: Vias are small holes drilled through the layers of a PWB to establish electrical connections between layers. The density and size of vias can influence the thermal conductivity of the board. A higher via density can improve heat transfer by providing additional pathways for heat conduction.
-
Operating Temperature: The thermal conductivity of materials can vary with temperature. As the operating temperature of a PWB changes, the thermal conductivity values of its constituent materials may also change. It is important to consider the expected operating temperature range when calculating thermal conductivity.
Methods for Calculating Thermal Conductivity
There are several methods available for calculating the thermal conductivity of PWBs. Let’s explore some commonly used approaches:
Analytical Methods
Analytical methods involve using mathematical equations and material properties to calculate the thermal conductivity of a PWB. One widely used analytical method is the effective thermal conductivity (ETC) approach.
The ETC method calculates the thermal conductivity of a multilayer PWB by considering the thermal conductivities and thicknesses of individual layers. The equation for calculating the effective thermal conductivity is as follows:
k_eff = (Σ(k_i * t_i)) / (Σt_i)
Where:
– k_eff
is the effective thermal conductivity of the PWB
– k_i
is the thermal conductivity of the i-th layer
– t_i
is the thickness of the i-th layer
To use this equation, you need to know the thermal conductivity and thickness of each layer in the PWB stack-up. The thermal conductivity values for common materials used in PWBs are readily available in literature or can be obtained from material suppliers.
Here’s an example calculation using the ETC method:
Layer | Material | Thickness (mm) | Thermal Conductivity (W/mK) |
---|---|---|---|
1 | Copper | 0.035 | 385 |
2 | FR-4 | 0.200 | 0.3 |
3 | Copper | 0.035 | 385 |
4 | FR-4 | 0.200 | 0.3 |
5 | Copper | 0.035 | 385 |
Using the given values, we can calculate the effective thermal conductivity:
k_eff = ((385 * 0.035) + (0.3 * 0.200) + (385 * 0.035) + (0.3 * 0.200) + (385 * 0.035)) / (0.035 + 0.200 + 0.035 + 0.200 + 0.035)
= 40.545 W/mK
The calculated effective thermal conductivity of the PWB is approximately 40.545 W/mK.
Numerical Methods
Numerical methods involve using computational techniques to solve complex heat transfer problems in PWBs. These methods are particularly useful when dealing with non-uniform geometries, irregular Copper Distributions, or complex boundary conditions.
One commonly used numerical method is the finite element analysis (FEA). FEA divides the PWB into small elements and solves the heat transfer equations for each element, considering the material properties, boundary conditions, and heat sources. FEA software packages, such as ANSYS or COMSOL, can be used to perform thermal simulations of PWBs.
To use FEA for calculating thermal conductivity, follow these general steps:
- Create a 3D model of the PWB, including the Layer Stack-Up, copper traces, and components.
- Assign material properties, including thermal conductivity, to each layer and component.
- Define boundary conditions, such as ambient temperature and convective heat transfer coefficients.
- Specify heat sources, such as power dissipation of components.
- Mesh the model into small elements.
- Run the FEA solver to calculate the temperature distribution and heat flow in the PWB.
- Post-process the results to extract the effective thermal conductivity of the PWB.
FEA provides a more accurate and detailed analysis of thermal conductivity compared to analytical methods, as it can account for complex geometries and non-uniform heat distributions. However, it requires specialized software and expertise to set up and interpret the results.
Experimental Methods
Experimental methods involve measuring the thermal conductivity of a PWB directly using specialized equipment. One common technique is the guarded hot plate method.
In the guarded hot plate method, a PWB sample is placed between a heated plate and a cold plate. The heat flow through the sample is measured, and the thermal conductivity is calculated based on the temperature gradient and the sample thickness.
Experimental methods provide the most accurate thermal conductivity values, as they account for the actual manufacturing processes and materials used in the PWB. However, they require specialized equipment and can be time-consuming and costly.
Considerations for Accurate Thermal Conductivity Calculation
To ensure accurate calculation of thermal conductivity in PWBs, consider the following factors:
-
Material Properties: Use reliable and up-to-date thermal conductivity values for the materials used in the PWB. Consult material datasheets or conduct measurements if necessary.
-
Layer Thickness: Accurately measure or obtain the thickness of each layer in the PWB stack-up. Even small variations in thickness can impact the thermal conductivity calculation.
-
Copper Coverage: Consider the actual copper coverage on each layer, including trace widths, spacing, and copper thicknesses. Higher copper coverage generally improves thermal conductivity.
-
Via Density: Include the effect of vias in the thermal conductivity calculation. Vias act as thermal pathways and can enhance heat transfer between layers.
-
Anisotropic Properties: Some materials, such as FR-4, exhibit anisotropic thermal conductivity, meaning the thermal conductivity varies in different directions. Consider the anisotropic nature of materials when calculating thermal conductivity.
-
Boundary Conditions: Accurately define the boundary conditions, such as ambient temperature and convective heat transfer coefficients, to obtain realistic results.
-
Validation: Validate the calculated thermal conductivity values through experimental measurements or comparison with published data for similar PWB configurations.
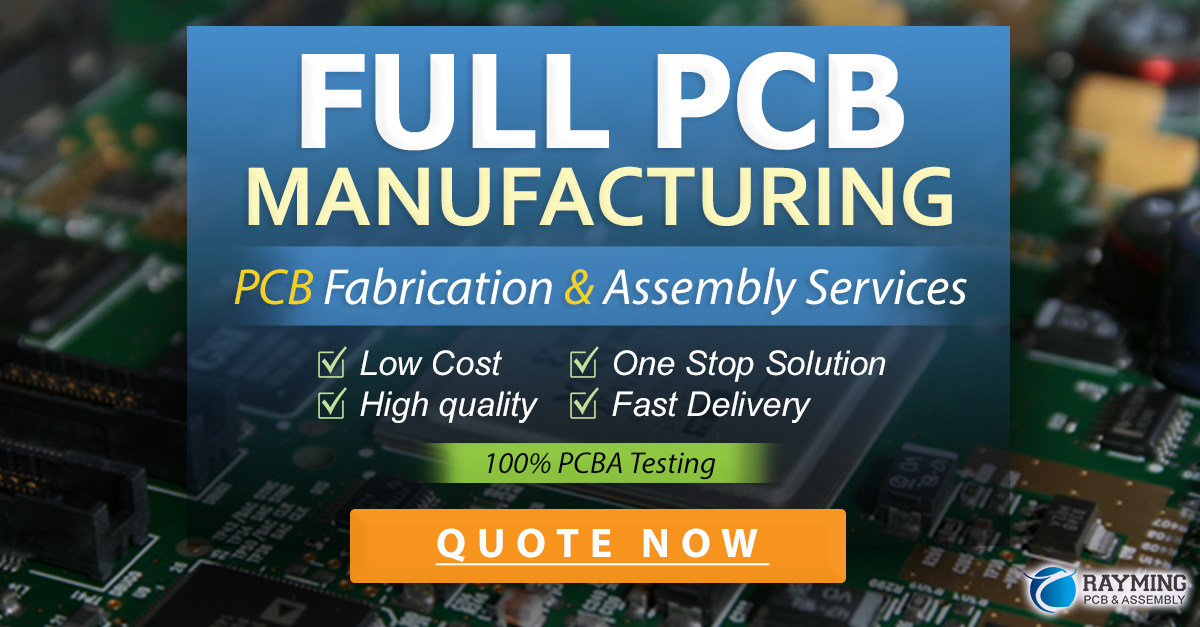
FAQ
-
What is thermal conductivity, and why is it important in PWBs?
Thermal conductivity is a measure of a material’s ability to conduct heat. In PWBs, it determines how effectively heat is transferred through the board. High thermal conductivity is crucial for dissipating heat generated by electronic components, ensuring reliable operation and preventing thermal-related failures. -
What factors affect the thermal conductivity of a PWB?
The thermal conductivity of a PWB is influenced by several factors, including the material composition, layer thicknesses, copper coverage, via density, and operating temperature. The properties and arrangement of the conductive and insulating layers, as well as the presence of thermal vias, play a significant role in determining the overall thermal conductivity of the board. -
What are the common methods for calculating thermal conductivity in PWBs?
There are three main methods for calculating thermal conductivity in PWBs: analytical methods, numerical methods, and experimental methods. Analytical methods, such as the effective thermal conductivity (ETC) approach, use mathematical equations and material properties to estimate thermal conductivity. Numerical methods, like finite element analysis (FEA), employ computational techniques to solve complex heat transfer problems. Experimental methods involve direct measurement of thermal conductivity using specialized equipment. -
How can I ensure accurate calculation of thermal conductivity in PWBs?
To ensure accurate calculation of thermal conductivity, consider the following factors: use reliable material property data, accurately measure layer thicknesses, consider copper coverage and via density, account for anisotropic properties if applicable, define appropriate boundary conditions, and validate the results through experimental measurements or comparison with published data. -
What are the benefits of accurately calculating thermal conductivity in PWBs?
Accurate calculation of thermal conductivity in PWBs offers several benefits. It enables designers to optimize the thermal management of electronic systems, ensuring proper heat dissipation and preventing thermal-related issues. By understanding the thermal conductivity of the PWB, designers can make informed decisions about material selection, layer stack-up, and component placement. This leads to improved reliability, performance, and overall system efficiency.
Conclusion
Calculating thermal conductivity in printed wiring boards is a critical aspect of electronic system design. By understanding the factors that influence thermal conductivity and employing appropriate calculation methods, designers can ensure effective heat dissipation and reliable operation of electronic components.
This article has provided a comprehensive overview of thermal conductivity in PWBs, including its importance, influencing factors, and calculation methods. We have explored analytical methods like the effective thermal conductivity approach, numerical methods such as finite element analysis, and experimental methods like the guarded hot plate technique.
To achieve accurate thermal conductivity calculations, it is essential to consider material properties, layer thicknesses, copper coverage, via density, anisotropic properties, boundary conditions, and validation techniques. By taking these factors into account, designers can optimize the thermal management of PWBs and create reliable and efficient electronic systems.
As electronic systems continue to evolve and become more complex, the importance of thermal management and accurate thermal conductivity calculation will only increase. By staying informed about the latest techniques and best practices, designers can effectively tackle the thermal challenges associated with PWBs and ensure the long-term success of their electronic products.
Leave a Reply