Understanding Solder Escape
What is Solder Escape?
Solder escape, also known as Solder Wicking, is a phenomenon that occurs during the soldering process when molten solder is unintentionally drawn away from the intended connection point. Instead of forming a strong and reliable solder joint, the solder travels along component leads, PCB traces, or other conductive surfaces, often resulting in a weak or incomplete connection.
Causes of Solder Escape
Several factors can contribute to the occurrence of solder escape:
-
Excessive heat: Applying too much heat during soldering can cause the solder to become excessively fluid, increasing the likelihood of it being drawn away from the connection point.
-
Prolonged heating: Holding the soldering iron on the joint for an extended period can lead to solder escape as the molten solder has more time to travel along conductive surfaces.
-
Inappropriate soldering technique: Poor soldering techniques, such as applying insufficient solder, using the wrong tip size or shape, or failing to properly position the soldering iron, can contribute to solder escape.
-
Contamination: Dirt, grease, or oxidation on the surfaces being soldered can hinder the proper flow of solder and increase the risk of solder escape.
-
Inadequate surface preparation: Failing to properly clean and prepare the surfaces prior to soldering can result in poor solder adhesion and increase the chances of solder escape.
Preventing Solder Escape
To minimize the occurrence of solder escape and achieve reliable solder joints, follow these best practices and techniques:
1. Temperature Control
Proper temperature control is crucial in preventing solder escape. Follow these guidelines:
- Use a soldering iron with adjustable temperature control to ensure the appropriate heat level for the specific soldering task.
- Set the temperature according to the solder alloy being used. Refer to the manufacturer’s recommendations for the optimal temperature range.
- Avoid excessive heat by monitoring the soldering iron’s temperature and adjusting it as necessary.
Solder Alloy | Melting Point (°C) | Recommended Soldering Temperature (°C) |
---|---|---|
Tin-Lead (Sn63/Pb37) | 183 | 300-350 |
Lead-Free (Sn96.5/Ag3.0/Cu0.5) | 217 | 350-400 |
Lead-Free (Sn99.3/Cu0.7) | 227 | 350-400 |
2. Soldering Technique
Employing proper soldering technique is essential to prevent solder escape. Consider the following tips:
- Use the appropriate tip size and shape for the soldering task at hand. A tip that is too large can apply excessive heat, while a tip that is too small may not provide sufficient heat transfer.
- Apply the soldering iron to the joint at a 45-degree angle, allowing both the pad and the component lead to be heated simultaneously.
- Feed solder into the joint while the soldering iron is in contact with both the pad and the lead. Avoid applying solder directly to the tip of the iron.
- Use just enough solder to create a strong and reliable joint. Excess solder can increase the risk of solder escape.
- Remove the soldering iron and solder wire simultaneously once a sufficient amount of solder has been applied, allowing the joint to cool naturally.
3. Surface Preparation
Proper surface preparation is crucial for achieving good solder adhesion and preventing solder escape. Follow these steps:
- Clean the surfaces to be soldered using isopropyl alcohol or a dedicated PCB cleaner to remove any dirt, grease, or contaminants.
- If necessary, use a soldering iron tip cleaner or sponge to ensure the tip is clean and free of oxidation before soldering.
- Apply a small amount of flux to the surfaces to be soldered. Flux helps to remove oxides, improve solder flow, and promote better adhesion.
- Preheat the components and PCB if working with large or high-mass items to minimize the temperature gradient and reduce the risk of solder escape.
4. Component Placement and Lead Forming
Proper component placement and lead forming can help minimize the occurrence of solder escape. Consider these points:
- Ensure that component leads are properly trimmed and formed to the appropriate length. Excessively long leads can increase the risk of solder escape.
- Position components securely on the PCB, ensuring that leads are properly inserted through the designated holes or pads.
- If working with surface mount components, use tweezers or a pick-and-place tool to accurately place the components on the pads.
- Avoid applying excessive pressure or bending the leads unnecessarily, as this can cause stress on the solder joint and increase the likelihood of solder escape.
5. Selecting the Right Solder
Choosing the appropriate solder alloy and diameter can contribute to the prevention of solder escape. Consider the following factors:
- Use solder alloys that are compatible with the components and PCB materials being used. Common alloys include tin-lead (Sn63/Pb37) and lead-free options like Sn96.5/Ag3.0/Cu0.5 or Sn99.3/Cu0.7.
- Select a solder diameter that is appropriate for the size of the components and pads being soldered. A diameter of 0.5mm to 1.0mm is suitable for most through-hole and surface mount soldering tasks.
- Consider using solder wire with a rosin core, which provides a flux that helps improve solder flow and reduces the risk of solder escape.
Solder Diameter | Suitable Applications |
---|---|
0.5mm | Small surface mount components, fine pitch leads |
0.8mm | General-purpose through-hole and surface mount soldering |
1.0mm | Larger components, connectors, high-power applications |
Frequently Asked Questions (FAQ)
-
What is the main cause of solder escape?
The main cause of solder escape is excessive heat application. When too much heat is applied to the solder joint, the molten solder becomes overly fluid and can be drawn away from the intended connection point along conductive surfaces. -
How can I control the temperature of my soldering iron to prevent solder escape?
To control the temperature of your soldering iron, use a model with adjustable temperature control. Set the temperature according to the recommended range for the solder alloy you are using. Regularly monitor the temperature and adjust it as necessary to maintain the optimal level. -
What role does surface preparation play in preventing solder escape?
Proper surface preparation is essential in preventing solder escape. Cleaning the surfaces to be soldered, removing contaminants, and applying flux helps to improve solder adhesion and reduce the risk of solder escape. Clean surfaces allow for better solder flow and a stronger bond between the solder and the components or PCB. -
Can the choice of solder alloy affect the occurrence of solder escape?
Yes, the choice of solder alloy can impact the likelihood of solder escape. Different solder alloys have varying melting points and flow characteristics. Using a solder alloy that is compatible with the components and PCB materials, and selecting an appropriate solder diameter, can help minimize the risk of solder escape. -
What should I do if I encounter solder escape during the soldering process?
If you notice solder escape occurring during the soldering process, stop applying heat immediately. Allow the joint to cool naturally, and then assess the extent of the solder escape. If necessary, use a solder wick or desoldering pump to remove the excess solder. Clean the area thoroughly and resolder the joint using the proper technique and temperature control to achieve a strong and reliable connection.
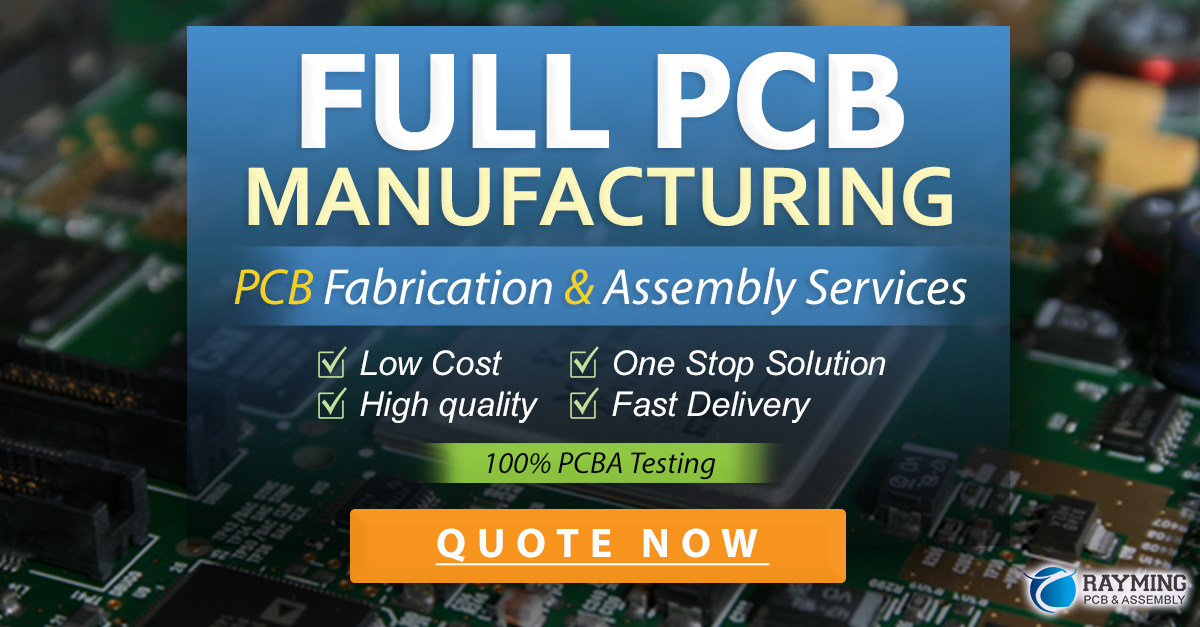
Conclusion
Preventing solder escape is crucial for achieving strong, reliable, and high-quality solder joints in electronic assemblies. By understanding the causes of solder escape and implementing best practices such as proper temperature control, correct soldering technique, thorough surface preparation, appropriate component placement, and selecting the right solder, you can significantly reduce the occurrence of this issue.
Remember to always prioritize safety when soldering by working in a well-ventilated area, using appropriate personal protective equipment, and handling hot Soldering Irons and molten solder with caution.
By following the guidelines outlined in this article and continually refining your soldering skills through practice and attention to detail, you can consistently produce professional-grade solder joints that are free from solder escape and ensure the optimal performance and longevity of your electronic projects.
Leave a Reply