Introduction
Printed circuit boards (PCBs) are essential components in practically every electronic device we use today. As products become more advanced and complex, the demand for high-quality PCBs continues to grow. Many companies now require PCB assembly in high volumes to meet production targets and timelines.
However, high volume PCB assembly comes with its own set of challenges. The assembly process must balance speed and efficiency with quality and reliability. Manufacturers need strategies to streamline operations, minimize errors, and deliver flawless PCBs consistently.
In this comprehensive guide, we will explore best practices and key considerations for executing high volume PCB assembly successfully.
Key Factors for Efficient High Volume PCB Assembly
Several critical factors go into efficient and high-quality PCB assembly at scale:
Component Sourcing and Inventory Management
- Maintain steady supply relationships with reputed component suppliers and distributors. Forecast demand and order sufficiently ahead of time.
- Use inventory management software to track stock levels, maintain optimal buffers, and prevent shortages or gluts.
- Store components correctly to avoid damage (e.g. anti-static bags, regulated temperature/humidity). Manage stock on first-in-first-out basis.
- Perform incoming quality checks on supplied components. Have procedures to handle defects and non-conformances.
Production Planning and Scheduling
- Detailed planning and production scheduling is vital for high volume PCB assembly. Analyze and optimize all steps of the assembly process.
- Reduce changeover times when switching between different PCB types to maximize asset utilization.
- Balance workloads across lines to prevent bottlenecks. Allow for contingencies and adjustments.
- Use long-term forecasts to plan capacity expansions when needed.
Automated Assembly Processes
- Automated assembly systems like chip shooters and pick and place machines improve speed, repeatability and accuracy.
- Maintain and calibrate automated equipment regularly. Train operators thoroughly.
- Upgrade software and tools to deploy automation in inspection, testing and other steps.
- Evaluate opportunities to adopt smart factory technologies like IoT, analytics and machine learning.
Quality Control and Inspection
- Implement rigorous quality control at every stage – incoming, in-process, final testing.
- Deploy automated optical inspection systems to detect defects like missing components or bad solder joints.
- Conduct both in-circuit tests and functional testing on finished boards. Reject defective units.
- Capture quality data for analysis. Identify root causes and take corrective and preventive action.
Efficient Supply Chain and Logistics
- Optimize supply chain to ensure steady component supplies and speedy order fulfilment.
- Establish logistics partnerships for responsive inbound and outbound transportation.
- Use barcoding and serialization to accurately track boards through assembly processes.
- Careful handling and anti-static packaging is vital to avoid shipping damage.
Best Practices for High Volume PCB Assembly
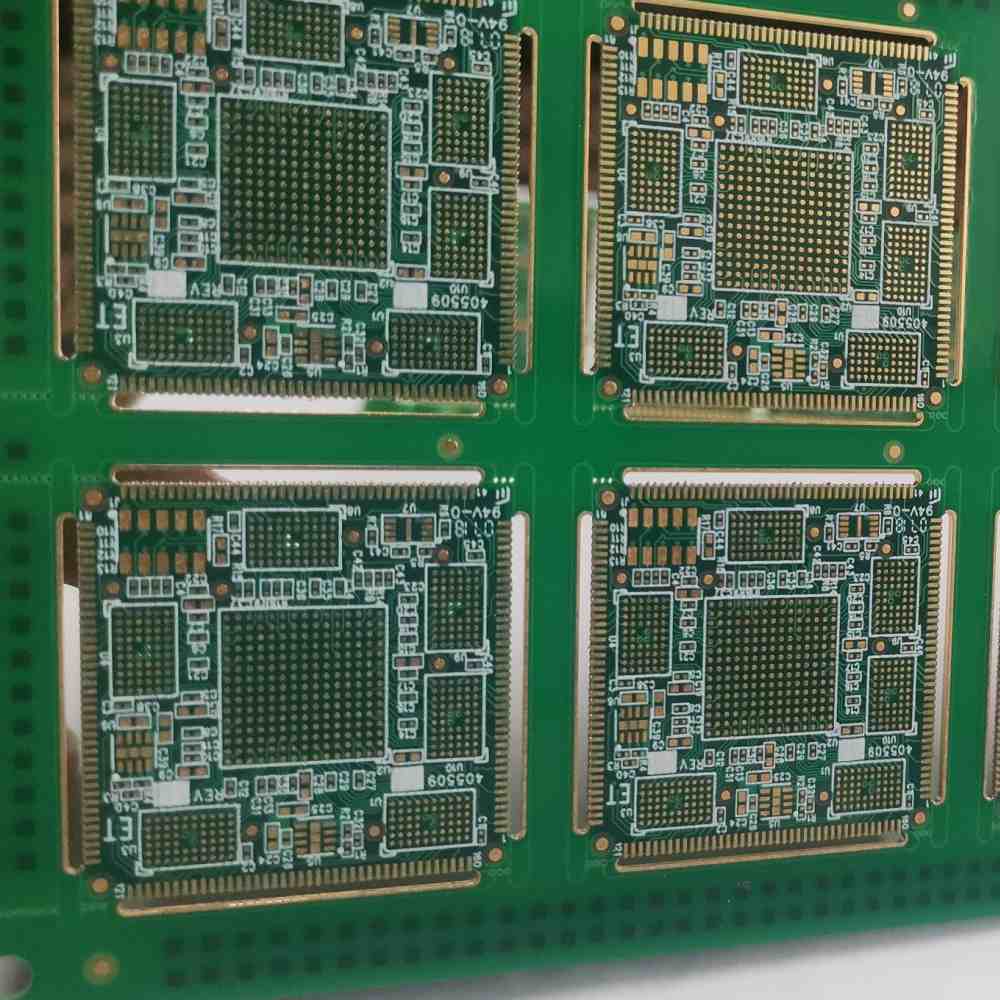
Follow these proven best practices to achieve high productivity along with quality and reliability:
1. Standardize Processes
- Create detailed standard operating procedures (SOPs) for each assembly step and process.
- Configure machines and tools identically across production lines. Standardize equipment settings.
- Document change management protocols to handle revisions.
- Standardization makes training easier and minimizes human errors.
2. Optimize Line Balancing
- Balance cycle times and workloads across lines. Avoid overloaded or idle resources.
- Combine manual and automated steps seamlessly for an efficient process flow.
- Ensure material availability. Use kanban systems and streamlined part replenishment.
- Levelled production with constant workloads results in better output.
3. Validate Processes Rigorously
- Validate all processes, jigs, fixtures, programs and equipment before full production.
- Verify process capability. Conduct capability and control studies.
- Accelerate process approvals with automated validation tests for coding, placement, soldering etc.
- Pilot test on a small batch before large production runs. Confirm repeatability.
4. Prioritize Defect Reduction Initiatives
- Identify defect prone processes through Pareto analysis of quality data. Focus improvement efforts.
- Deploy automation, poka-yokes and other solutions targeted to eliminate major defect types.
- Monitor defects per million opportunities (DPMO) as a metric. Drive towards six sigma quality.
- Leverage analytical tools to correlate root causes like temperature, vibration, component type etc.
5. Develop Operators’ Skills
- Train assembly operators extensively on processes, machines, inspection and maintenance.
- Certify personnel. Evaluate skills periodically.
- Encourage involvement of line personnel in kaizens and Poka Yoke implementations.
- Foster teamwork and open communication between shifts, lines and functions.
6. Maintain Equipment Effectively
- Follow preventive maintenance schedules for SMT machines, storage, tools etc.
- Auto-collect machine performance data through sensors and IoT. Monitor asset health.
- Perform restorative maintenance when output degrades. Seek OEM support if needed.
- Budget and plan for capital investment in new equipment.
Key Quality Considerations
PCB quality must not suffer even when maximizing assembly speeds. Keep these guidelines in mind:
Parameter | Guidelines |
---|---|
PCB Design | – Optimize design for manufacturability.<br>- Allow adequate tolerances.<br>- Follow assembly rules and standards. |
Parts Management | – Use only approved and qualified components.<br>- Avoid counterfeit or recycled parts.<br>- Control moisture sensitivity. |
Soldering | – Maintain soldering iron tip temperature.<br>- Optimize thermal profiles.<br>- Verify joint integrity. |
Cleaning | – Remove flux and other residues.<br>- Prevent electrochemical migration.<br>- Avoid static discharge damage. |
Coatings | – Apply conformal coatings correctly.<br>- Ensure full coverage on board. |
Handling | – Use ESD safe materials and procedures.<br>- Allow boards to cool properly after soldering.<br>- Prevent mechanical or shipping damage. |
Testing | – Test thoroughly – continuity, ICT, functional.<br>- Program fixtures correctly. |
Rigorously controlling these parameters helps achieve the highest possible quality and reliability.
Optimizing High Volume PCB Assembly Lines
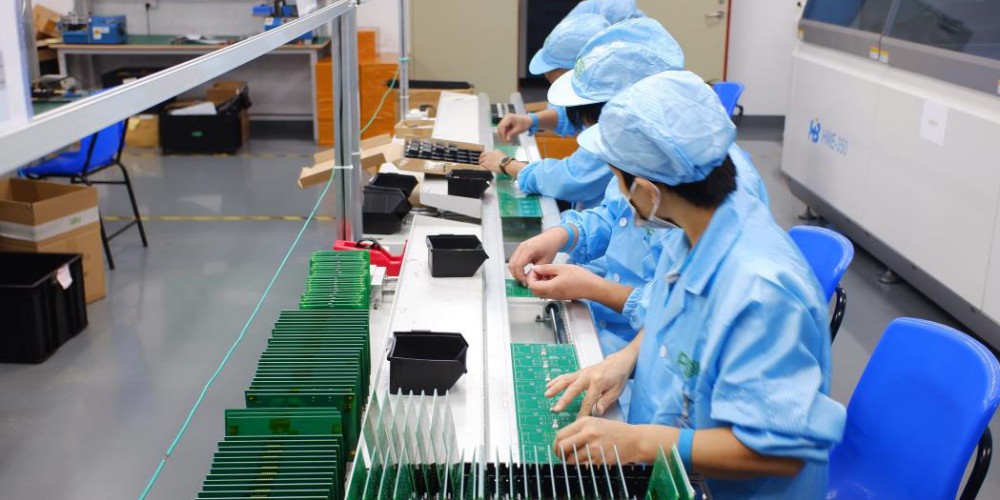
Large PCB assembly facilities typically contain multiple production lines with a combination of manual insertion and automated SMT assembly.
Here are some tips for optimizing high volume PCB assembly lines:
- Line Balancing – Carefully balance cycle times across lines to maximize output. Avoid uneven bottlenecks.
- Changeovers – Reduce equipment changeover times when switching PCB types through quick tooling and preset recipes.
- Feeders – Use tape and stick feeders for SMT components to avoid loading delays. Place fastest moving reels near the feeder edge.
- Scheduling – Schedule higher volume PCBs during full shifts. Keep complex boards with many changeovers for smaller batches or night shifts.
- Maintenance – Schedule preventive maintenance during planned downtime to minimize disruption.
- Buffer Stock – Keep sufficient inventory buffer of components near assembly lines for quick replenishment.
- Work Instruction – Clearly display SOPs, work instructions and sample boards at each assembly station.
- Data Capture – Deploy data collection terminals, scanners and readers at each step to transmit information in real-time.
- Traceability – Track PCBs accurately through the assembly process through serial numbers and barcodes.
- Process Validation – Continuously gather process data to validate and improve assembly settings, quality benchmarks etc.
Key Metrics for Monitoring
Manufacturers should track a range of operational and quality metrics to get visibility into high volume PCB assembly performance. Some important metrics include:
- Utilization – Overall Equipment Effectiveness (OEE), line utilization percentages, operator productivity
- Cycle Times – Assembly cycle time by product type and line, aging of work in progress (WIP)
- Quality – Defect rates, rework rates, yield, DPMO, Customer rejects
- Costs – Cost per board, scrap costs, downtime costs
- Service – On-time delivery, lead times
Data should be visualized using dashboards and analytics tools to derive insights. Production and quality issues can be identified early for quick intervention.
Frequently Asked Questions
Q1. How can manufacturers ensure component quality for high volume PCB assembly?
Follow a rigorous supplier and component qualification process. Perform incoming inspections and sample testing on purchased parts. Maintain traceability back to qualified suppliers. Use statistical process control to flag significant deviations.
Q2. What are some best practices for storage and kitting of components?
Use automated storage systems for managing SMT components and kits. For moisture sensitive parts, follow recommended bake and dry pack processes. First-in-first-out (FIFO) stock rotation helps avoid aging. Barcode labeling ensures accuracy.
Q3. How can automated inspection systems improve quality in high volume PCB assembly?
Automated optical inspection immediately after SMT assembly can detect issues like missing components, misalignments or tombstoning before boards proceed further. This drastically reduces escapes and rework later. Sophisticated 3D SPI tools now enable inspection of hidden solder joints.
Q4. What are some key soldering parameters to control for reliable PCB assemblies?
Maintain solder iron tip temperature within optimum range. Use calibrated profiling for consistent solder reflow oven heating. Verify thermal profiles match solder alloy specifications. Solder paste storage conditions also impact solder joint quality and should be controlled.
Q5. Why is traceability important in high volume PCB assembly?
Accurate traceability mechanisms using serial numbers, barcodes and data capture enables tracking each board through assembly steps. This facilitates quality analysis and helps isolate problematic processes if issues arise during or after assembly. Traceability is also important for compliance in regulated sectors like automotive and aerospace.
Conclusion
Success in high volume PCB assembly requires extensive planning, disciplined process execution and a data-driven, quality-focused culture. Investments in automation, quality systems and workforce training help maximize efficiency and minimize risks. This guide summarized key aspects manufacturers must get right to achieve the challenging twin goals of high productivity and uncompromising quality. With rigorous attention to these best practices, PCB assemblers can thrive and support their customers’ needs for advanced, flawless boards in high volumes.
Leave a Reply