The demand for heavy copper printed circuit boards (PCBs) has been steadily increasing over the past several years. As products become more complex and require higher current capacities, the need for PCBs made with thicker copper has grown. Choosing the right heavy copper PCB manufacturer is critical to ensure your boards meet design specifications and performance requirements. This guide covers key considerations when selecting a heavy copper PCB production partner.
What is Heavy Copper PCB?
Heavy copper PCBs use thicker copper foil, usually defined as 2 oz (70 μm) or thicker, compared to standard 1 oz (35 μm) foil. The increased copper thickness allows the PCB to handle higher amperages and dissipate heat more effectively. This is important for designs with high power components or devices with high current draw like motors, power supplies, LEDs, and batteries.
Benefits of Using Heavy Copper PCBs
- Improved current carrying capacity – Thicker copper can sustain much higher current loads without overheating
- Better thermal management – The extra copper provides superior heat dissipation which is vital for high power circuits
- Lower resistance – Thicker copper traces have lower electrical resistance allowing efficient power transfer
- Stronger power planes – Heavy copper inner planes distribute current evenly reducing impedance
- Longer product lifespan – The robust copper stands up to high currents and repeated thermal cycling
When to Use Heavy Copper
Heavy copper PCBs are recommended for:
- High power electronic products like EV charging stations, power supplies, inverters etc
- Designs using multiple high current components like motors, heaters, power amplifiers
- Circuits operating at high temperatures or with frequent thermal cycling
- Low impedance planes for RF circuits and multilayer boards
- Long boards/traces carrying >3A for extended periods
For moderate current applications, standard 1 oz copper may be sufficient depending on the design. Consulting with your PCB manufacturer early in the design process is recommended.
Key Considerations When Selecting a Heavy Copper PCB Manufacturer
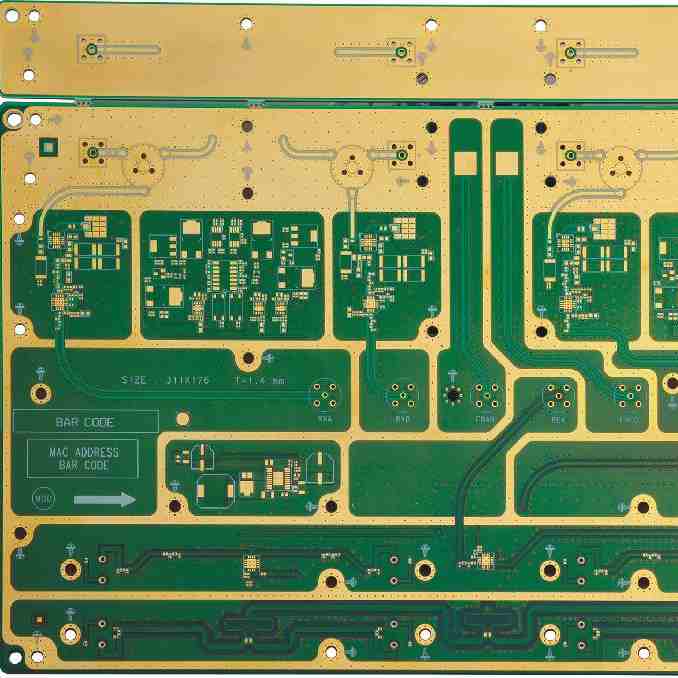
Capability with Thick Copper
Not all PCB manufacturers can reliably produce heavy copper boards, especially at 4 oz and above. Key factors to consider are:
- Available copper foil thickness – Many factories max out at 2 oz so confirm what thicknesses are supported
- Track record with thick copper – Evaluate past projects and success rate with heavy copper
- Registration accuracy – Thicker copper impacts registration which can cause issues like lower yields if not controlled well
- Specialized equipment – Thick copper may require special drill bits, plating equipment, etc.
Choose a manufacturer with proven experience and demonstrated capabilities with the copper thickness you require. Ask to see previous examples of heavy copper boards they have produced.
Quality Control and Testing
Producing consistent, high quality heavy copper PCBs is challenging and requires rigorous quality control and testing. Important capabilities to look for include:
- CAM validation – Software checks for production issues like insufficient spacing or violations
- Electrical testing – Bare board testing ensures there are no shorts or opens
- Coupon analysis – Regular sampling to confirm copper thickness across production runs
- Cross-section analysis – Cutting test samples to inspect internal layer alignment and uniformity
- ISO-certified – Certification indicates adherence to strict quality standards and procedures
Prioritize manufacturers that make quality a high priority throughout the entire fabrication workflow.
Advanced Manufacturing Technology
Heavy copper PCBs place added demands on the manufacturing processes. Evaluating the production technologies and equipment is advised.
- Imaging – Can the equipment consistently image thick copper without undercutting or damage?
- Etching – Tight process controls are needed to properly etch thick copper foils
- Oxide treatment – Surface preparation is key to get uniform plating over heavy copper
- Plating distribution – Even plating is needed to avoid thickness variations
- Drilling – Rigid drills bits and backup boards may be required for high layer count boards
- Punching/routing – Tools must be sharp to avoid cracking or tearing thick copper
Choose a manufacturer that has invested in advanced machinery optimized for heavy copper production.
Design for Manufacturability
Work with your PCB manufacturer early in the design process to design for manufacturability (DFM). Thick copper impacts many aspects of manufacturing so a DFM review is highly recommended to avoid issues.
- Review spacing rules – Increased copper thickness reduces spacing between traces
- Confirm registration capabilities – Tighter tolerances required with thick copper
- Check drill aspect ratios – Higher aspect ratios impact drill rates
- Use thermal reliefs – Help avoid copper tearing when soldering thick traces
- Incorporate test points – Needed for validating impedance control and dielectric integrity
- Allow for panel utilization – Heavy copper typically requires smaller panel sizes
An experienced manufacturer can guide you through design adjustments to ensure your heavy copper PCBs can be fabricated successfully.
Supply Chain Reliability
Like many industries, electronics manufacturing has been impacted by global supply chain disruptions. Ensure your heavy copper PCB supplier has qualified back-up sources for raw materials like copper foil, laminates, etc. Diversity of supply helps minimize risk of stock-outs or lead time delays.
Location and Logistics
For time-sensitive projects, the manufacturer’s location and logistics capabilities are important considerations:
- Where is the factory located? Can production be localized?
- How reliable and fast is the shipping/transport?
- Are there export/import restrictions to consider?
- What is the packaging expertise and support?
A manufacturer with global operations and packaging expertise provides flexibility and speed.
5 Key Questions to Ask Heavy Copper PCB Manufacturers
- What is your experience with producing heavy copper PCBs at 2 oz, 4 oz, 6 oz and above? Can you share some examples?
- What is your defect rate and yield for heavy copper PCBs? How do you ensure quality and consistency across production lots?
- What advanced manufacturing equipment do you use for imaging, etching, plating, drilling and routing heavy copper PCBs?
- How can your team assist with design for manufacturing (DFM) reviews and making suggestions to optimize designs for heavy copper fabrication?
- What supply chain measures are in place to mitigate risk of material shortages or lead time delays? Do you have back-up sources qualified?
Conclusion
Heavy copper PCBs require specialized capabilities in fabrication, quality control, and manufacturing technologies. Selecting the right partner is key to achieving success on heavy copper PCB projects with high reliability. Focus on manufacturers with proven experience, rigorous quality systems, advanced production equipment, DFM expertise, and resilient supply chains. With the right heavy copper PCB partner, your high current, high heat designs can be brought to reality.
Leave a Reply