Printed circuit boards (PCBs) are an essential component of most modern electronic devices. As devices become more complex and compact, there is an increasing need for high-density interconnect (HDI) PCBs that can accommodate fine lines, spaces, and high connection densities. Choosing the right HDI PCB manufacturer is critical to ensure your boards are produced reliably and cost-effectively.
What is HDI PCB Technology?
HDI refers to technology that allows for tighter packing of traces and components on a PCB. Some key characteristics of HDI PCBs include:
- Fine line/space: Lines and spaces less than 100 microns (0.1 mm). Many HDI PCBs have lines/spaces of 50 microns or less.
- Microvias: Vias with diameters less than 150 microns. These enable connections between layers in highly multi-layer boards.
- High connection density: More than 200 connections per square inch.
- Layer count: Typically from 4-16 layers, though some HDI boards may have 20 layers or more.
- Thin dielectric: Dielectric layers as thin as 25-50 microns. Allows closer spacing of circuitry.
- Laser drilling: Small via holes are made with laser drills, allowing precise small diameters.
- Sequential lamination: Dielectric and copper foil layers are added individually to build up HDI board layer by layer.
HDI technology is essential for products like smartphones, tablets, and other compact electronics. The boards provide the interconnect density needed while minimizing space requirements.
Benefits of Using an HDI PCB Manufacturer
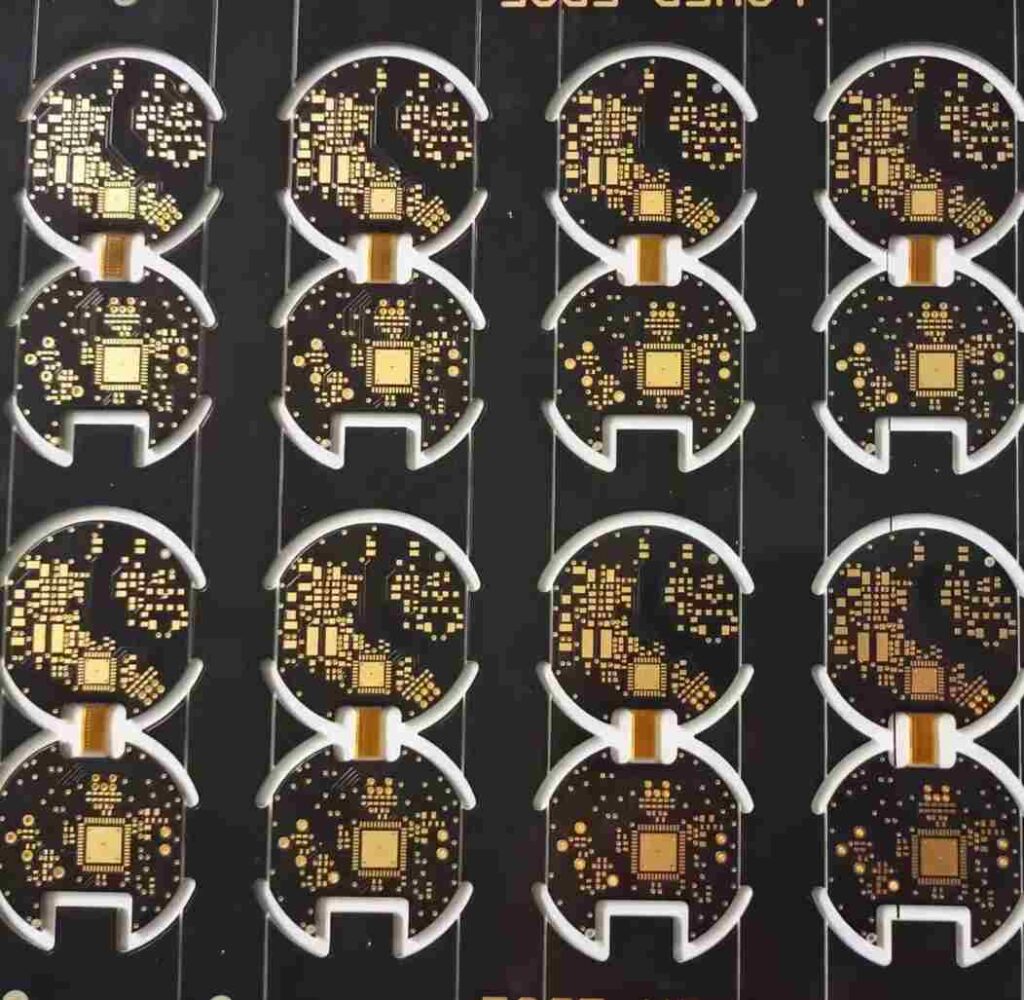
As HDI technology continues advancing, the specialized expertise and equipment required also increases. Working with a professional HDI PCB manufacturer provides important benefits:
State-of-the-Art Capabilities
Top HDI manufacturers invest heavily in equipment like high-precision laser drills, advanced materials, and the latest fabrication processes. This gives access to the newest HDI technology not feasible for in-house production.
Quality and Reliability
HDI PCB production requires tight process controls and quality management. Dedicated manufacturers have the best practices in place for consistently producing defect-free boards.
Fast Turnaround
HDI fabs run multiple shifts with skilled staffing to provide quick turnaround. In-house production is typically much slower, creating delays.
Flexibility
Demand fluctuations, short production runs, and design changes are handled efficiently by HDI manufacturers. In-house would require excess capacity.
Cost Savings
Despite the high capital expenses, outsourcing to volume manufacturers leads to lower per-board costs in most cases.
Expert Support
Knowledgeable engineers at HDI fabs provide design support and recommendations to optimize manufacturability.
Key Factors When Selecting an HDI PCB Manufacturer
1. Experience with HDI Technology
Look for manufacturers with at least 5-10 years of experience specifically producing HDI boards. They should demonstrate expertise across the latest processes like laser drilling, sequential lamination, etc. Newer fabs may lack the full range of specialized HDI capabilities.
2. Quality Systems and Certifications
The manufacturer should have robust quality control processes and standards certifications related to PCB fabrication, such as:
- IPC – Institute for Interconnecting and Packaging Electronic Circuits certifications like IPC-6012 and IPC-A-600 demonstrate technical expertise.
- ISO – ISO 9001 certification indicates their quality management system meets international standards.
- AS9100 – The AS9100 aerospace standard indicates very high-reliability processes.
3. Engineering Support
Look for manufacturers that provide engineering review and feedback during design to spot any manufacturability issues early. They should also have design guidelines available to follow.
4. Customer Service
You want confident salespeople that can explain their HDI capabilities clearly. Responsiveness to design questions and quotes is also important.
5. Location
For North American customers, a fab located in the United States or Asia with local sales support is preferable. This reduces lead times and shipping costs.
6. Production Capabilities
- What is the board size range they can manufacture? Some only handle smaller boards.
- Ask about their layer count support. More than 12 layers will require advanced HDI expertise.
- What is their line/space and microvia capabilities? Under 0.1 mm lines require laser drilling.
- What materials/thicknesses do they offer? Thin dielectrics like 25 μm are key.
- What testing/inspection is done? Things like electrical testing and x-ray imaging.
- Do they handle assembly as well as bare boards?
7. NDA and ITAR Controls
If your boards contain sensitive IP or technology not allowed to be exported, the manufacturer should have confidentiality protections in place and conform to ITAR regulations. Ask about their information security practices.
8. Lead Time and Volume Capabilities
- What is their estimated lead time for your board? Shorter lead times indicate better responsiveness.
- Do they have experience handling small prototyping volumes up to high-volume production?
- Is production capacity sufficient to meet your forecasted demand?
9. Pricing
- Request pricing based on your board layer count, size, and volume. Get price breakdowns for tooling vs. board costs.
- Compare pricing between several manufacturers. HDI requires major capital investment, so low-ball pricing indicates lack of capabilities.
- Very low volume prototyping will have higher per-board costs. Estimate based on your production scale.
Questions to Ask Prospective HDI PCB Manufacturers
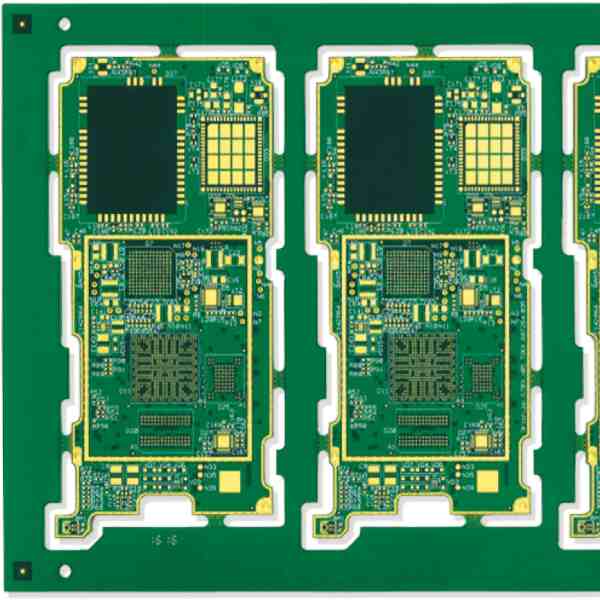
Beyond the factors above, you should prepare specific questions for each manufacturer you are evaluating. Here are some examples:
- Can you describe the key differentiators of your HDI technology and services?
- What is your current line/space and microvia capability? How does this compare to other manufacturers?
- Do you have in-house laser drilling, or is this outsourced? What machines are used?
- How long have you been manufacturing HDI boards? Can I see examples of complex boards recently produced?
- How will you ensure quality for my boards? Describe your quality control and inspection practices.
- Who will be the primary engineering and customer service contacts for my project?
- What design guidelines or considerations do you recommend for this board?
- Can you accommodate quickturn prototyping in 1 week, as well as volume production?
Frequently Asked Questions (FQA) About HDI PCB Manufacturing
Here are some common questions about working with and selecting an HDI PCB manufacturing partner:
Q: Why go with an HDI PCB manufacturer rather than producing boards in-house?
A: HDI manufacturing requires major investment in advanced equipment as well as specialized expertise built up over many years. Attempting to create an internal HDI fabrication line with comparable capabilities to external manufacturers would not be feasible or cost-effective for most companies
Q: How does HDI technology enable smaller and higher performance PCBs?
A: The combination of laser drilling, thin dielectric layers, fine lines and spaces, and microvias allows packing interconnect density that cannot be achieved with standard PCB fabrication. HDI provides the foundation for continuing miniaturization and performance increases.
Q: What design considerations are important when leveraging HDI?
A: With HDI it becomes even more critical to design for manufacturability. Work closely with your PCB manufacturer early in the design process. Key considerations include matching board layouts to manufacturing capabilities, minimizing via aspect ratios, allowing adequate spacing for fine features, and minimizing unused areas that increase cost.
Q: Can HDI boards incorporate embedded components?
A: Yes, HDI allows integration of components like capacitors and resistors within the PCB layers. This enables higher component densities as well as improved electrical performance compared to surface-mount components. Your HDI PCB manufacturer can advise on recommended approaches for embedded components.
Q: How much does HDI PCB fabrication cost relative to standard multilayer boards?
A: Due to the specialized materials and processes involved, HDI boards have a higher cost per square inch compared to conventional PCBs. However, by enabling miniaturization and integration, overall system cost savings are often achieved. The expertise of the HDI manufacturer is key to optimizing cost for a given design.
Conclusion
As products require increased functionality in limited space, HDI PCB technology provides the interconnect density needed. Partnering with the right HDI PCB manufacturer ensures you can leverage the latest HDI capabilities to meet your technical and commercial objectives. Do thorough due diligence using the guidelines covered here – evaluate expertise, quality systems, production capabilities, customer service, and costs when selecting your manufacturing partner. The right manufacturer becomes an invaluable extension of your own team.
Leave a Reply