Introduction
High density interconnect (HDI) printed circuit boards (PCBs) have become increasingly popular in recent years due to the growing demand for smaller, lighter, and more advanced electronics. HDI PCBs allow for finer lines and spaces, smaller vias, and higher connection densities than conventional PCB technologies. However, HDI PCBs come at a higher cost due to the more complex manufacturing processes required. In this article, we will take a deep dive into the true costs behind HDI PCB fabrication and assembly to help you determine if they are the right choice for your project.
What are HDI PCBs?
HDI PCBs refer to boards with microvia technology where the line and space can be as fine as 2-3 mil with 1 mil microvias. This allows routing traces between closely spaced surface mount components. Some key characteristics of HDI PCBs:
- Line/space of 2 mil or less
- Microvias with 1 mil diameter or less
- High density of connections and components per unit area
- More complex layer stackup with buildup dielectric layers
- Often incorporate blind and buried vias
- Allow embedding of passive components
HDI technology enables miniaturization and increased functionality for advanced electronics. Cell phones, wearables, IoT devices, and medical devices often utilize HDI due to space and weight constraints.
HDI PCB Design Costs
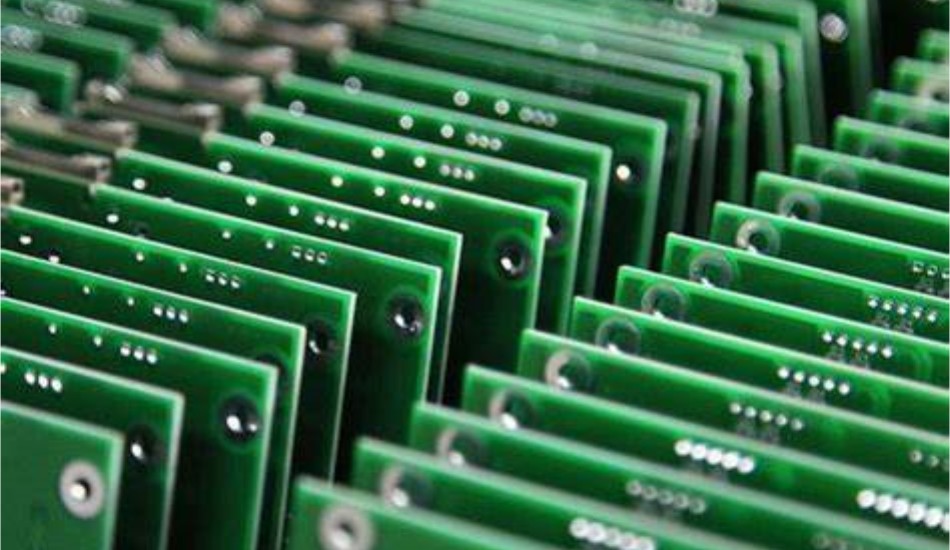
The design stage is where the additional costs of an HDI PCB first come into play. Here are some of the main factors that increase design costs:
More Complex Design Software/Tools
Specialized CAD tools for optimizing trace routing, via placement, and pad stacking at extremely high densities is required. These tools are more expensive than standard PCB layout software.
Advanced Design Expertise
Engineers must have specialized knowledge in HDI design to leverage the capabilities effectively while avoiding manufacturability issues. This expertise commands higher salaries.
Increased Design Time
Routing and optimizing complex HDI boards takes significantly more time compared to standard density designs. Additional iterations are often required.
DFM Analysis Tools
Advanced DFM (design for manufacturing) analysis tools are used to detect potential fabrication issues. This validation step adds cost.
Prototyping
Multiple prototype iterations are typically needed to check design constructs due to the tighter tolerances. Each prototype board adds cost.
Overall, HDI PCB design costs can be 2-4X higher than standard density PCBs. But this higher initial investment prevents costly mistakes later on.
HDI PCB Fabrication Costs
Once the design is complete, the next factor driving up costs is the actual board fabrication and materials involved:
Layer Stackup
HDI PCBs require more complex layer stackups like 6-16+ layers to allow routing through closely spaced surfaces. More layers means higher costs.
Tighter Tolerances
Manufacturing PCBs with 2 mil lines/spaces and 1 mil microvias requires more precise processes and materials. This precision costs more.
Advanced Materials
The dielectric materials used in HDI PCBs enable the finer features but are more expensive than standard laminates. These include high-end sandwhich constructions.
Plating Processes
To plate small microvias, specialized electrolytic and electroless copper processes are needed which add cost.
Laser Drilling
Microvias require laser drilling with very tight accuracy standards. Laser drilling machine capital costs are higher.
Testing
Electrical testing and inspection is more extensive on HDI boards and requires advanced testing systems.
Due to these factors, HDI PCB fabrication can cost anywhere from 25-50% more than standard PCBs for a given area. So for lower volumes, this difference is very apparent.
HDI PCB Assembly Costs
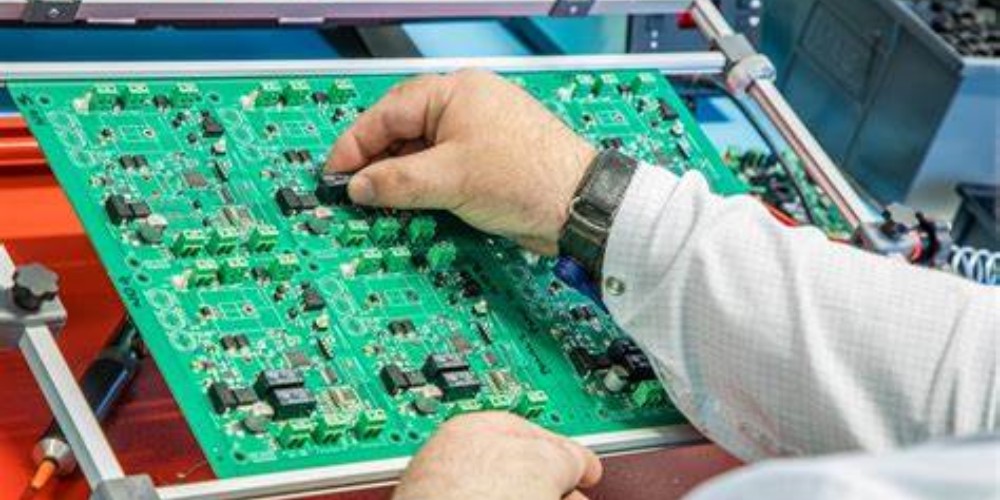
In addition to fabrication, assembling components onto HDI PCBs requires advanced capabilities that increase costs:
High Precision Assembly
Placing and soldering tiny chip components onto HDI PCBs requires specialized equipment with high precision and accuracy.
Miniaturized Components
The small package components used on HDI boards are more expensive due to lower demand.
Rework Difficulty
Once assembled, reworking faulty components on HDI PCBs is very difficult and sometimes impossible. This can lead to more scrap costs.
Testing
Extensive testing is crucial after assembly to catch any faults. Flying probe, X-ray, and computed tomography testing is often used.
Due to these challenges, assembly prices are generally 20-40% higher per unit for HDI PCBs compared to standard density designs.
Cost Per HDI PCB by Quantity
To illustrate how quantity impacts cost, here is a sample price chart from a major HDI PCB manufacturer for their ~6 layer boards:
Quantity | Cost per Board |
---|---|
1-49 | $1,500 |
50-99 | $1,000 |
100-249 | $750 |
250-499 | $500 |
500-999 | $250 |
1000+ | $125 |
For prototypes in the 1-49 quantity range, HDI PCBs can be very expensive at around $1500 each. However, prices drop dramatically as volumes increase due to economies of scale in production. In the 1,000+ range, prices become much more competitive at $125 per board.
So HDI PCB technology makes most sense for small designs with production volumes of at least a few hundred boards. The high initial costs are challenging for very low volume or prototype projects.
Reducing HDI PCB Costs
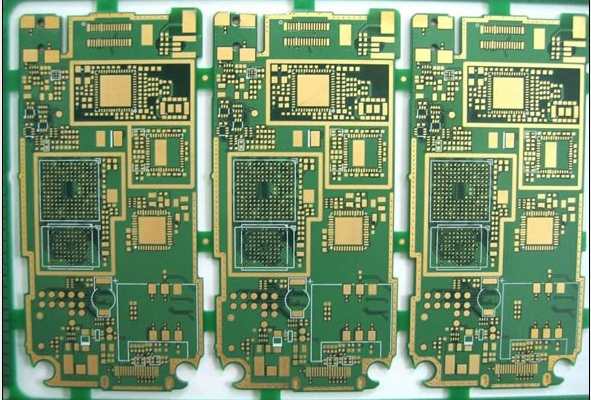
Here are some tips to help mitigate the higher costs associated with HDI PCB technology:
- Leverage design tools and resources fully – Use all available features in CAD tools and seek help from experts when needed to avoid unnecessary revisions.
- Start with simplest design first – Make the design as straightforward as possible in the beginning and only add complexity where absolutely required.
- Use a trusted manufacturer – Choose a fab with proven HDI capabilities as mistakes will be costly. Get quotes from multiple sources.
- Build prototypes judiciously – Limit the number of prototype iterations to the bare minimum to validate the design.
- Order larger volumes – The cost per board drops dramatically at higher quantities, so produce more to reduce overall costs.
- Negotiate discounts – If ordering large volumes with the same manufacturer regularly, negotiate for quantity discounts.
- Consider design alternatives – Weigh the pros and cons of advanced packaging techniques like SiP as alternatives to HDI based on cost tradeoffs.
Careful design, strict volume management, and shrewd negotiation allows maximizing the benefits of HDI while minimizing the higher production costs.
Conclusion
While HDI PCB technology provides powerful capabilities for miniaturized electronics, it comes at a significantly higher cost due to more complex design requirements, tighter fabrication tolerances, and precision assembly operations. Costs can be 2-4X higher for low volume prototype boards, but decrease substantially at higher volumes. To leverage HDI most effectively, pay close attention to design optimization, manufacturing partnerships, volume management, and budget negotiations whenever employing this advanced PCB technology. The higher initial investment will pay off with a remarkably functional end product.
HDI PCB Cost FAQs
What are the main factors increasing HDI PCB costs?
The main drivers of higher costs are the more advanced design tools and expertise required, additional fabrication processes needed to produce microvias and fine features, specialized assembly equipment to place tiny components precisely, and extensive testing procedures.
How much more does HDI PCB design cost versus standard PCBs?
Typical estimates are that HDI PCB design costs can range from 2-4 times higher than standard density PCBs. The specialized tools, engineering skills, and increased development time contribute to this.
What is a typical price per board for small quantity HDI PCB orders?
For small prototype quantities of 1-49 boards, HDI PCB costs are generally $1500 or more per board from most manufacturers. At these low volumes, prices are very high.
How can I reduce costs for my HDI PCB project?
Strategies like optimizing the design, building the bare minimum prototypes, ordering larger volumes, negotiating discounts, and exploring alternative packaging can help lower total project costs when using HDI technology.
At what quantities do HDI PCB costs become more affordable?
Once volumes reach the 500+ unit range, HDI PCB prices tend to drop below $300 per board for a given size. And at 1,000+ units, $125 per board or less is common. Higher volumes provide economies of scale.
Leave a Reply