As flexible printed circuits (FPCs) continue to grow in popularity across industries like consumer electronics, automotive, medical devices and more, choosing the right FPC manufacturer is crucial for meeting project needs and specifications. With FPC capabilities varying greatly between manufacturers, partnering with the right producer can impact everything from product quality and durability to project timelines and budgets.
This guide will provide tips on vetting and selecting an FPC manufacturing partner for your specific application.
Key Factors to Consider in an FPC Manufacturer
When evaluating potential FPC manufacturers, keep the following key factors in mind:
FPC Design Capabilities
Look for expertise in specialized FPC design. This includes:
- Complex circuitry – Can they design high-density interconnections and multi-layer configurations?
- Fine lines/spaces – What is their minimum line/space width? At least ≤100 μm line/space width is ideal.
- High layer counts – Do they produce 6+ layer FPCs?
- Special materials – Can they work with polyimide, aluminum, copper, and other typical FPC materials?
- Design software – Do they use advanced CAD software for optimal FPC design?
A strong design team with experience across complex FPCs is essential.
Production Technology
Look for expertise in precision FPC fabrication. Key production capabilities include:
- Etching precision – Do they use photolithographic processes for intricate circuitry etching?
- Registration accuracy – Can they repeatedly align layers with <100 μm accuracy?
- Quality testing – Do they have automated optical inspection (AOI) and other testing?
- Tolerancing – How precise are their tolerances for trace widths, openings, etc?
- Miniaturization – Can they produce miniaturized flex circuits? Under 0.15 mm lines?
The right production technologies result in repeatable, high-quality FPCs.
Materials & Sourcing
- Materials expertise – Do they have experience with typical FPC materials like polyimide, copper, acrylic adhesives, etc?
- Inventory – Do they stock various FPC materials for fast turnaround? Or will they be drop shipping?
- Supply chain – Do they have reliable material suppliers already established?
Materials availability and sourcing capabilities affect production timeframes.
Industry Experience
- Applications – Do they have specific experience manufacturing FPCs for your industry and application?
- Design for manufacturing (DFM) – Will they provide DFM feedback during design to optimize manufacturability?
- Prototyping – Can they rapidly prototype new FPC technologies or product innovations?
- Testing – Do they have expertise testing FPCs for relevant industry standards?
- Qualifications – Are there relevant quality certifications like ISO 9001 or qualifications for your industry?
Relevant expertise in your application results in optimized, application-specific FPC designs.
Services
- Design support – Do they provide FPC design services or just manufacturing?
- Assembly – Can they assemble FPCs with connectors, shields or other components?
- Global production – Do they have manufacturing sites near your geography for streamlined logistics?
The range of available services impacts production capacities and timeframes.
8 Steps to Select the Right FPC Manufacturer
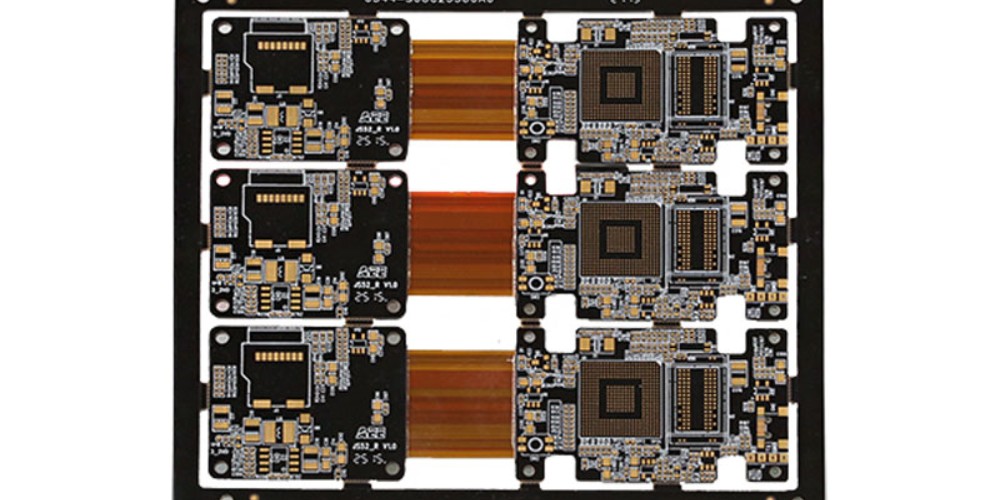
Follow these steps when vetting and selecting an FPC manufacturing partner:
1. Define Technical Requirements
Start by detailing your specific project’s FPC requirements:
- Circuit density needs
- Layer count needed
- Minimum trace tolerances
- Flexibility requirements
- Materials needs
- Any specialized features like embedded components
This creates a specifications checklist to compare manufacturer capabilities against.
2. Research Industry Experience
Search for manufacturers with proven experience producing FPCs for your specific application and industry. For example, consumer electronics often have very different needs than medical devices or aerospace applications.
Look for case studies, customer lists, and application-specific qualifications.
3. Request FPC Samples
Ask manufacturers to provide samples similar to your project’s needs. For example, request 2+ layer FPCs in your required materials with fine feature sizes.
Visually inspect samples for quality and precision. Do they meet your tolerance expectations?
4. Review FPC Design Capabilities
Ask to see examples of complex FPC designs the manufacturer has produced. Gauge their expertise across:
- High layer count and dense circuit boards
- Integrating specialized features like embedded components
- Miniaturized traces and precision tolerancing
- Recommendations for optimizing manufacturability
Ideally, they will showcase advanced designs relevant to your industry.
5. Discuss Production Capabilities
Ask specific questions about their production processes and capabilities:
- What is their minimum trace width and spacing?
- What is their layer alignment accuracy?
- What testing procedures do they use to ensure quality?
- What are their lead times for prototyping vs production runs?
Ensure they can meet key requirements.
6. Review Supply Chain Management
- Do they stock FPC materials for quick turnaround?
- Who are their material suppliers? Are they well established?
- For global production, do they partner with reliable manufacturers?
- Can they provide active supply chain monitoring and risk mitigation?
Choose reliable material sourcing and global production networks.
7. Compare Services Offered
Consider which additional services are offered:
- FPC design engineering
- Component assembly prior to delivery
- Support for rapid prototyping
- Design and production certifications
Services impact production flexibility and timeframes.
8. Request Pricing Estimates
Have manufacturers provide a formal quote for your project based on your specifications. Compare pricing between 2-3 preferred suppliers.
While cost is a factor, also carefully weigh expertise, production capabilities, quality, certifications, and services.
5 Benefits of Partnering With the Right FPC Manufacturer
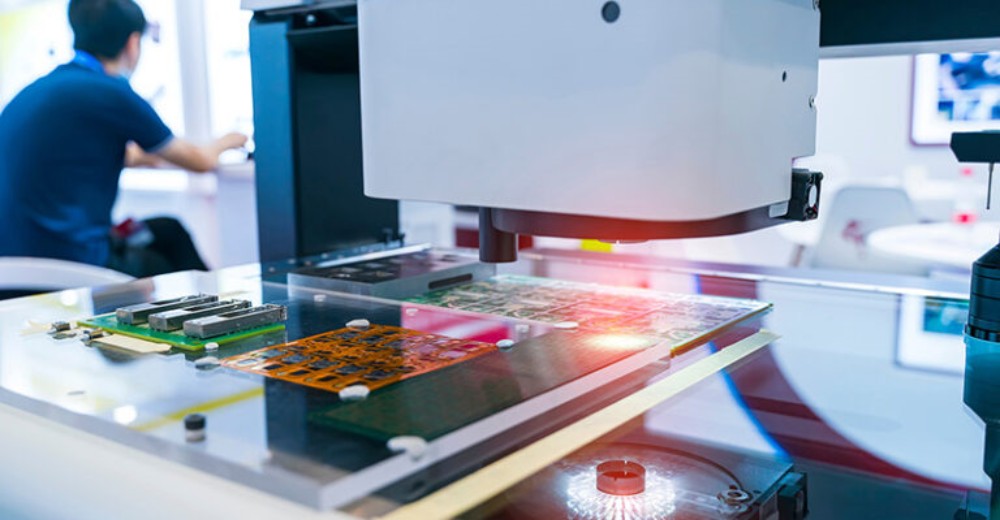
Selecting the right FPC manufacturing partner provides many benefits, including:
Optimized FPC Design
With their design expertise, an experienced FPC manufacturer can provide feedback to optimize manufacturability. This avoids errors that could impact project timelines or product quality.
Reduced Project Risk
An established FPC manufacturer has proven production processes that repeatedly deliver high-quality circuits. This reduces uncertainty and risk compared to unproven producers.
Faster Time to Market
Experienced FPC manufacturers have refined processes for fast prototyping and can accelerate complex projects. This enables bringing finished products to market faster.
Flexible Order Volumes
The right partner can support everything from low-volume prototyping to high-volume production runs. This provides maximum flexibility as project needs evolve.
Reduced Long-Term Costs
While upfront costs may be higher with a reliable FPC producer, their expertise results in fewer errors and higher quality. This reduces costs over the full product lifecycle.
Carefully qualifying and selecting an FPC manufacturing partner provides both short-term project execution benefits and long-term advantages for product quality and performance.
Questions to Ask When Qualifying an FPC Manufacturer
Use this checklist of questions when engaging with prospective FPC manufacturers to help qualify their capabilities:
FPC Design Experience
- How many years have you manufactured FPCs?
- Can I see examples of complex, high layer count FPCs you’ve produced?
- What specialized FPC features like embedded components have you worked on?
- What design software and tools do you use? Are they the industry standard?
Production Technology
- What etching methods do you use? Are they photolithographic?
- What is your registration alignment accuracy? Are you below 100 μm?
- Do you offer automated optical inspection or other testing?
- How precise are your trace width and spacing tolerances?
Quality Certifications
- Are you ISO 9001 or AS9100 certified?
- Do you have any industry-specific qualifications or certifications?
- Can you provide FPC quality reports from past projects?
Materials & Supply Chain
- What types of FPC materials do you have in inventory?
- Who are your main material suppliers? How long have you worked with them?
- For global production, where are your manufacturing facilities located?
Services
- Do you offer FPC design services or just fabrication?
- Can you provide application-specific design recommendations?
- Do you offer component assembly prior to delivery?
- What are your typical lead times for prototypes vs production?
Pricing
- What is your pricing model? Per design, area, units?
- What volume breaks do you offer for production runs?
- Do you offer discounted prototyping pricing?
Asking detailed questions across all these factors will reveal the manufacturer’s core competencies and potential limitations. Use the answers to guide your selection decision.
Tips for Sourcing the Right FPC Manufacturer
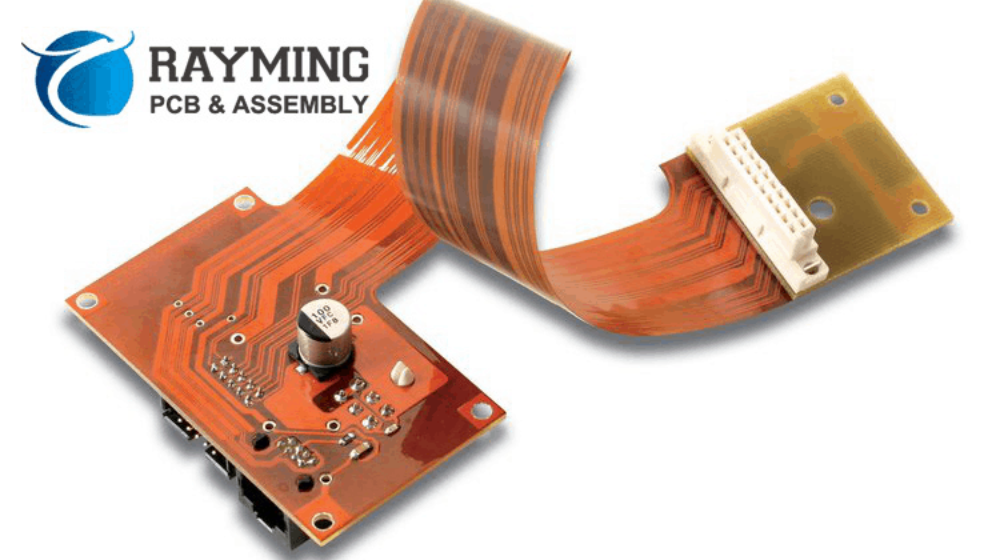
Follow these tips when researching and sourcing an FPC manufacturing partner:
- Get referrals – Ask colleagues who they partner with for FPC production. Referrals provide a trustworthy starting point.
- Attend trade shows – Meet FPC manufacturers firsthand at events like the DesignCon Conference.
- Check certifications – Search for ISO 9001 or AS9100 certified manufacturers for guaranteed quality systems.
- Review case studies – Look for manufacturers with case studies relevant to your specific application.
- Request prototypes – Ask to see application-specific FPC samples to assess quality.
- Compare globally – Consider both domestic and overseas manufacturers to balance cost and logistics.
- Visit facilities – Tour a manufacturer’s production facilities in person to view capabilities.
- Get DFM feedback – Ask manufacturers to assess designs for optimization opportunities.
- Interview multiple – Contact at least 2-3 manufacturers before making a selection.
With so many FPC manufacturers to choose from globally, following a thorough sourcing process ensures finding the best fit.
Key FPC Manufacturer Selection Criteria Summary
To recap, use the following criteria when evaluating and selecting an FPC manufacturing partner:
Expertise and Experience
- Proven experience manufacturing FPCs for your specific application and industry
- Capabilities producing high complexity FPCs, miniaturized features, and specialized technologies like embedded components
- Expertise providing application-specific design recommendations and design for manufacturing (DFM) feedback
Production Technologies
- Photolithographic etching and precision laser processing abilities
- Registration accuracy < 100 μm
- Rigorous quality testing procedures like automated optical inspection
- Exacting tolerances meeting your product needs
Quality and Certifications
- Relevant quality management certifications like ISO 9001
- Compliance with industry standards like IPC specifications
- Evidence of past quality FPC deliverables like customer reviews
Supply Chain Capabilities
- Readily available FPC materials inventory for fast lead times
- Established material supply partners
- Capable global manufacturing facilities if required
Breadth of Services
- End-to-end FPC design engineering if needed
- Component assembly prior to delivery
- Rapid prototyping services
- Relevant design and production certifications
Matching an FPC manufacturer against these criteria provides the best indicator that they can deliver on your specific project requirements while meeting budget and timeline needs.
Major Global FPC Manufacturers
To give you a starting point, here is an overview of some of the major global FPC manufacturers to consider:
Multi-Layer FPC Manufacturers
Manufacturer | Locations | Certifications |
---|---|---|
Flexium Interconnect | China, Thailand, USA | ISO-9001, ISO-14001 |
MFS Technology | Singapore, China, USA | ISO-9001, ISO-13485, AS9100D |
Flex | Global Manufacturing | ISO-9001, ISO-14001, AS9100, TS 16949 |
High Density Interconnect FPC Manufacturers
Manufacturer | Locations | Certifications |
---|---|---|
SI Flex | USA | ISO 9001, AS9100, ITAR Registered |
DSBJ | China | ISO-9001, UL, TS16949 |
Danbang | China | ISO-9001, IATF 16949 |
Single & Double Layer FPC Manufacturers
Manufacturer | Locations | Certifications |
---|---|---|
Flexium | China, USA | ISO-9001 |
Sumitomo | Japan, China, Malaysia | IATF 16949 |
Fujikura | Japan, China, Thailand, USA | ISO-9001 |
This provides a starting point for major global FPC manufacturers to investigate. Be sure to fully qualify capabilities against your specific needs.
FPC Manufacturer Request for Proposal (RFP) Template
When you are ready to contact manufacturers, using a structured FPC manufacturer RFP template can help assess capabilities against your needs consistently.
Include details on:
- Project background
- FPC design requirements
- Layers
- Density
- Materials
- Special features
- Minimum trace widths
- Volume needs
- Lead time targets
- Design and assembly services required
- Quality assurances
- Pricing request
Adjust the template based on your specific project goals and send to multiple manufacturers. Evaluate responses against your criteria to select the right partner.
Conclusion
Choosing the right FPC manufacturing partner is crucial for executing complex flexible printed circuit board projects. Performing due diligence by vetting expertise, production capabilities, services, and quality systems can improve quality, reduce costs, and accelerate timelines. Use the criteria provided in this guide to help select the best FPC producer for your specific needs. Partnering with the right manufacturer provides assurance you will receive high-performance flexible circuits purpose-built for your application.
FPC Manufacturer Selection – Frequently Asked Questions
Here are some common questions on finding the right FPC manufacturer:
What are the most important factors when selecting an FPC manufacturer?
The most important factors are:
- Expertise specifically manufacturing FPCs for your application and industry
- Advanced FPC design capabilities for complex, dense circuits and specialized features
- Precision fabrication technologies and tight tolerances
- Relevant quality and compliance certifications
- Availability of needed FPC materials and established supply chain
- Services like design support and component assembly
Matching against these criteria indicates they can deliver high-quality FPCs for your needs.
Should I focus on domestic or overseas FPC manufacturers?
There are benefits to both domestic and overseas manufacturers:
- Domestic – Closer proximity can enable tighter collaboration and rapid prototyping.
- Overseas – Often have lower production costs, enabling better pricing.
Ideally, assess both domestic and overseas producers to balance cost, quality, logistics, and other factors important to your specific project.
How many FPC manufacturer candidates should I evaluate?
It’s recommended to evaluate at least 2-3 potential FPC manufacturers before making a selection. Comparing multiple producers gives you a broader perspective on capabilities and pricing models. Be sure to get formal quotes from final candidates.
What questions should I ask FPC manufacturer candidates?
Key questions include: experience level manufacturing FPCs for your needs, production capabilities and tolerances, certifications held, supply chain resources, services offered like design support, and pricing structure. See the “Questions to Ask” checklist earlier in the article for details.
What are signs an FPC manufacturer may not be qualified for my project?
Watch for: lack of case studies for your application, limited design experience with high complexity FPCs, lack of robust quality certifications, inability to provide tight tolerances, long lead times, and inability to provide samples relevant to your industry.
Leave a Reply