Overview of Flex Circuits and Their Applications
Flexible printed circuits (FPCs), commonly known as flex circuits or flex boards, are made from flexible dielectric materials such as polyimide and polyester. They contain conductive traces etched from copper foil that provide electrical connections between components. Flex circuits can be bent, folded, and twisted to fit into tight or moving spaces in products. Some key advantages of flex circuits:
- Small, lightweight, and thin profile – ideal for compact electronics
- Can conform to irregular shapes and enable flexible or moving parts
- Durable and withstand repeated bending cycles
- Allow for high component density and complex circuitry
- Enable miniaturization of products
Flex circuits are used in a variety of industries and products including:
- Consumer electronics – cell phones, wearables, VR headsets
- Automotive – sensors, embedded control systems
- Aerospace and defense – guidance systems, engine controls
- Medical – hearing aids, imaging equipment
- Industrial – automation and robotics
With their versatility and reliability, flex circuit boards offer engineering design flexibility and are a key enabling technology in many of today’s electronic products.
Finding Flex Board Manufacturers and Assemblers
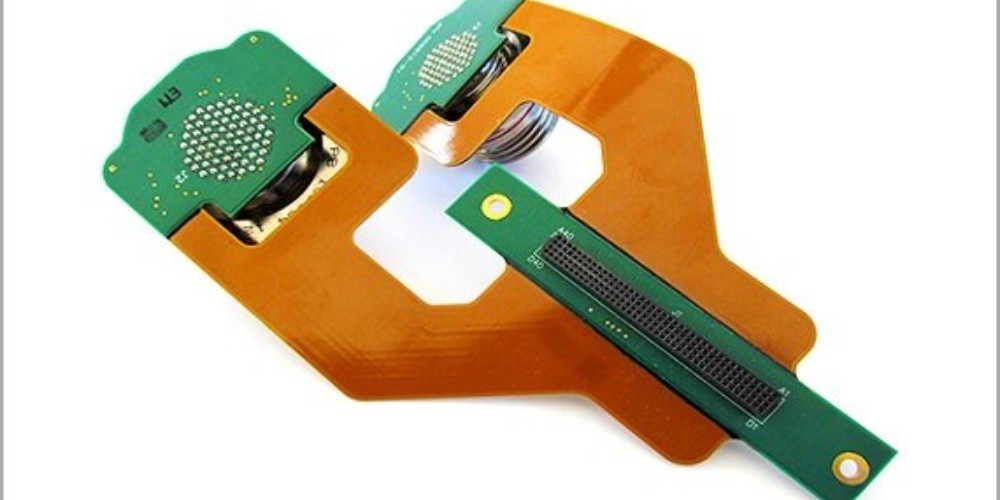
When you need custom designed and manufactured flex circuits for your product, connecting with flex board suppliers in your region can provide benefits:
- Reduce shipping costs and delays
- Ability to visit and audit supplier facilities
- Improved communication with local sales and engineering teams
- Support for quick-turn prototypes
- Conformance to local regulations and standards
Here are some ways to locate flex circuit manufacturers near your location:
Search Directories and Listings
Industry directories like Thomasnet provide searchable databases of manufacturers sorted by capabilities and locations. Use relevant keywords like “flexible printed circuit manufacturers [your state or city]” to find local suppliers.
Check Industry Associations
Many flex circuit manufacturers are members of industry trade groups like the Flexible Circuit Technology Association (FCTA) or IPC. Checking member directories on their websites is a good way to find specialized flex board providers in your area.
Attend Tradeshows and Conferences
Local events and tradeshows attract exhibitors from flex circuit suppliers in the region. Attending these events allows you to directly connect and interact with potential suppliers to assess their capabilities.
Get Referrals from Your Network
Speaking to others in your industry and getting supplier referrals from product designers, engineers, or purchasing professionals in your network is a trusted way to find reputable local flex circuit manufacturers. They may provide introductions or experiences working with certain providers.
Once you’ve identified a few potential flex board manufacturers, here are some key factors to consider in your evaluation and selection process:
Selecting the Right Flex Circuit Manufacturer
Capabilities and Expertise
- Do they specialize in and have extensive experience with designing and producing flex circuits, especially for your industry and application?
- Can they provide the circuit density, layer counts, and minimum trace/space width needed?
- Do they have in-house flex PCB designers?
- Ask for examples of complex flex circuits they’ve produced previously.
Quality and Certifications
- Are they certified to quality standards like ISO 9001, ISO 13485, AS9100, or IATF 16949?
- Do they have a robust quality control and inspection process?
- Can they provide analysis testing (thermal, vibration, shock) if needed?
- Ask for process quality data and audit results.
Production Capacity and Lead Times
- What is their current customer demand and factory utilization?
- Can they handle your prototype and production volume requirements?
- How quickly can they ramp up additional capacity if needed?
- What are standard lead times for prototypes and production runs?
Location and Logistics
- Where are their manufacturing facilities located? Is it convenient for visits and shipping?
- Do they warehouse components and finished circuits locally?
- Can they accommodate quick-turnaround for prototypes at short notice?
Pricing and Cost Management
- Are their base pricing, tooling/NRE charges, and minimum order quantities competitive?
- What design support and DFM analysis do they provide to optimize cost?
- Can they recommend alternative material choices if needed to reduce cost?
- Do they have electronic data interchange (EDI) and inventory management to reduce administrative costs?
By carefully vetting and selecting your flex board supplier using these criteria, you can find the right manufacturing partner to meet your specific project and product needs.
Key Flex Board Manufacturers to Consider in the United States
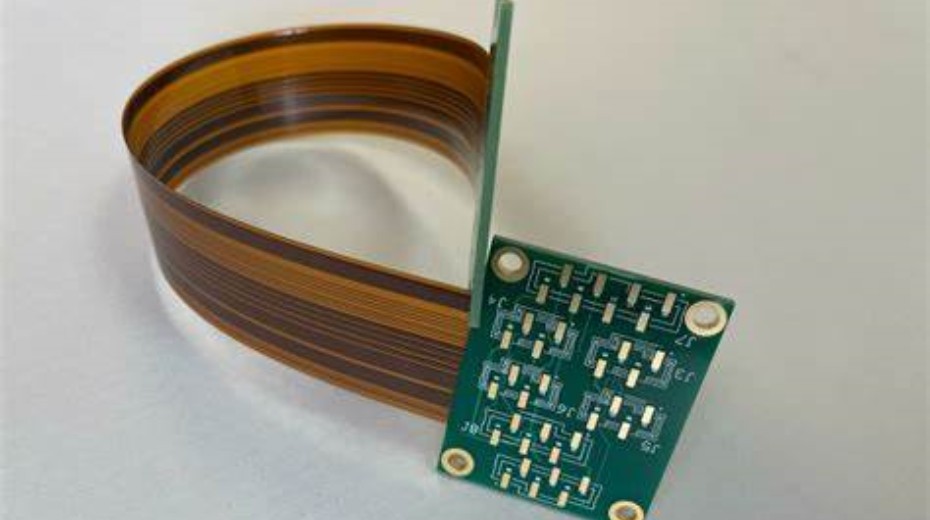
To help you get started in your flex circuit supplier search, here are some of the top manufacturers serving locations across the US:
Minnesota Flex
- Headquarters: Minneapolis, MN
- Facilities: MN, WI, AZ, CA
- Capabilities: quick-turn prototypes, 0.5 mil lines/spaces, stacked vias, rigid-flex
- Industries served: medical, military, aerospace, industrial
- Certifications: ISO 9001, ISO 13485, AS9100D
Innovative Circuits
- Headquarters: Alpharetta, GA
- Facilities: GA, NH, CA
- Capabilities: multilayer flex and rigid-flex, very low volume, cutting-edge technologies
- Industries served: defense, aerospace, medical, robotics
- Certifications: ITAR Registered, ISO 9001, ISO 13485
Flexible Circuit Technologies
- Headquarters: Milwaukee, WI
- Facilities: WI, MN
- Capabilities: quick-turn prototypes, design support, pilot and high volume production
- Industries served: consumer electronics, automotive, telecom, medical
- Certifications: ISO 9001, IATF 16949
Advanced Flexible Circuits
- Headquarters: Minneapolis, MN
- Facilities: MN
- Capabilities: multilayer rigid-flex, flex-to-fit shields, chemical milling
- Industries served: medical, industrial, transportation, instrumentation
- Certifications: ISO 13485
Lenthor Engineering
- Headquarters: Chagrin Falls, OH
- Facilities: OH, VA, CA, MA
- Capabilities: multilayer rigid-flex, ultra-fine lines down to 0.001″, blind and buried vias
- Industries served: medical, communications infrastructure, aerospace and defense
- Certifications: AS9100C
This list provides an overview of some of the leading domestic flex circuit manufacturers with locations and production facilities across the US. Be sure to evaluate suppliers specifically in your region by going through the steps outlined above.
Key Factors to Review in Flex Circuit Supplier Proposals
Once you’ve identified a few potential flex circuit suppliers, you’ll want to get detailed written proposals before selecting a manufacturing partner. Here are some of the important elements to look for in their proposal documentation:
Technical Capabilities Summary
The proposal should outline the supplier’s specific capabilities that match your flex circuit requirements:
- Available substrate materials and thicknesses
- Minimum trace width and spacing
- Available layer count for rigid, flex, and rigid-flex designs
- Line resolution and electrical testability
- Available special processes like vias, outer layer imaging, coatings
Quality Certifications
Suppliers should provide a summary of their relevant quality certifications like ISO, AS9100, IATF 16949, showing they adhere to the latest quality standards and procedures.
Previous Flex Circuit Experience
Relevant examples of previous flex circuit designs and projects similar to yours, along with references from those customers, demonstrate the supplier’s applicable expertise.
Engineering and Design Support
Details about upfront design support, DFM analysis, preliminary layouts, 3D modeling, prototyping, and design reviews that will be included. This shows the level of design collaboration you can expect.
Standard Pricing Matrix
Pricing table showing typical base costs by layer count, minimum quantities, and lead times provides a baseline to evaluate cost proposals. Understanding their cost drivers helps negotiate final pricing.
Test and Inspection Capabilities
Description of standard test procedures (AOI, electrical testing) and available additional testing services shows how thoroughly they validate quality.
Supply Chain and Logistics
Details about manufacturing locations, component sourcing lead times, and shipping capabilities help determine total delivery timelines.
Program Management and Review Plan
Proposed schedule and meetings for program reviews, testing results, design approvals, and production status tracking ensures you have visibility into progress.
By using this checklist when reviewing proposals, you can accurately assess the supplier’s technical capabilities, experience, quality control, costs, lead times, reporting and program management against your specific project requirements.
Flex Circuit Design and Manufacturing Process Overview
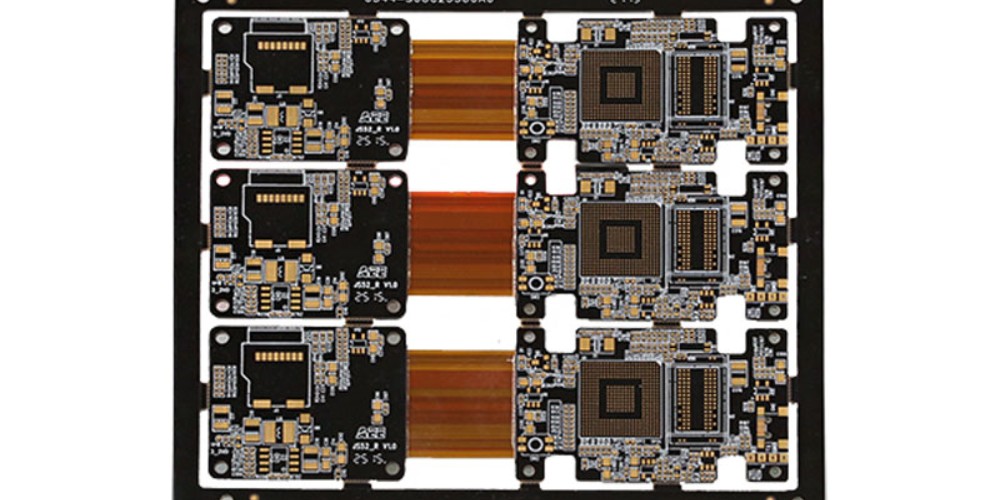
Understanding the overall process steps involved in taking your flex circuit design from concept to high volume production will help you plan your project timeline and expectations when working with a manufacturer:
1. Concept Review
- Gather design inputs and performance requirements from your engineering team
- Review environmental conditions, space constraints
2. Initial Design
- Create preliminary flex circuit layouts and schematics
- Determine layer count, trace widths, substrate material
- Model design in 2D and 3D as applicable
3. DFM Analysis
- Simulate bend radius, thermal response, and other analyses
- Optimize design for manufacturability and cost drivers
- Finalize materials selection, layer stackup
4. Prototype
- Validate electrical performance with tests like in-circuit or flying probe
- Refine design based on prototype feedback
5. Pilot Build
- Produce small test run with all manufacturing processes and test equipment in place
- Confirm manufacturing processes meet quality requirements
- Make final design adjustments if needed
6. Full Production
- Ramp up production with approved processes and tests
- Perform statistical sampling for quality control
- Continual process monitoring and optimization
Understanding this high-level workflow in advance allows you to collaborate effectively at each stage and helps avoid mismatched expectations. Be sure to align with your supplier on schedule, deliverables, and reviews for each milestone.
Tips for Lowering Flex Board Costs
Here are some tips to work with your flex circuit manufacturer to optimize the design and production process and reduce overall costs:
Simplify layer count – Reduce the number of conductive and dielectric layers where possible.
Use standard materials – Selecting commonly used substrate materials and copper instead of more exotic metals lowers costs.
Design panels efficiently – Panelizing circuit patterns to maximize material utilization saves on material waste.
Adjust tolerances – Allowing slightly looser tolerances where possible can optimize manufacturing processes.
Leverage DFM – Early DFM analysis identifies and avoids potential manufacturability issues.
Review flex vs. rigid-flex – Rigid sections may only be needed in limited zones rather than full outline.
Consider lower-cost processes – Evaluate whether stamped circuits can meet requirements instead of etched.
Consolidate testing – Grouping electrical and quality tests where possible minimizes overhead.
Standardize components – Reusing previously qualified components rather than custom parts lowers procurement costs.
Minimize special processes – Additional steps like extra coating, solder mask, or tolerances add costs.
The most significant opportunities for cost reduction usually come from decisions made in the early design phase. Working collaboratively with your supplier through DFM analysis and prototyping can yield insights for the most cost-effective approaches.
FAQ About Flex Circuit Manufacturing
How long does it typically take to get flex circuit prototypes?
For simple single or double-sided flex boards, prototypes can often be delivered in 5-10 days from completing the design. For more complex multilayer circuits, allow 15-20 days.
What design file formats do manufacturers accept?
Most accept industry standard Gerber and drill files. Many also accept CAD files like AutoCAD DXF/DWG for collaborating on native designs.
Can flex circuit suppliers assemble components onto the boards too?
Many have in-house assembly capabilities or partner with external assembly providers. Discuss your complete assembly needs upfront.
How many bend cycles can flex circuits support?
Properly designed flex circuits can endure hundreds of thousands of bend cycles for dynamic flexing applications. The bend radius is a key parameter.
How are costs for flex circuits typically structured?
There are typically base pricing per layer, tooling/NRE charges, and piece part cost based on quantities. Talk through all cost drivers with your supplier during design.
How are flex circuits tested during manufacturing?
Typical tests include automated optical inspection (AOI), bare board testing, flying probe, and functional testing after assembly.
How long do flex boards typically take to manufacture in full production?
Production lead times range from 2-6 weeks depending on quantities and current demand. Discuss throughput requirements with your supplier.
Can transparent flexible circuits be produced?
Yes, polyester-based transparent flexible materials allow see-through flex circuits for display and lighting applications.
Do flex circuit suppliers deliver direct to end customers?
Many offer direct shipment to your end customers. Alternatively, they can ship panels or reels to your location for final delivery.
Conclusion
I hope this guide provides a helpful overview of finding flex circuit manufacturing partners in your region and gives you insights into the flex board design, production, and qualification process to get your custom boards produced successfully. Connecting with specialized flex circuit suppliers with proven expertise enables creating innovative products and devices with maximum reliability and quality. Leveraging local manufacturers brings added benefits through collaboration, communication, rapid prototyping, and supply chain efficiency.
Leave a Reply