Introduction to Farnell and RAYPCB’s collaboration
Farnell, a leading global distributor of electronic components, and RAYPCB, a premier PCB manufacturing service provider, have recently announced their collaboration on the element14 platform. This partnership aims to provide customers with a seamless experience in designing, prototyping, and manufacturing high-quality printed circuit boards (PCBs).
What is element14?
Element14 is an online community and platform for engineers, designers, and makers to share knowledge, collaborate on projects, and access a wide range of resources related to electronic design and manufacturing. The platform is owned and operated by Farnell, which has been serving the electronics industry for over 80 years.
Benefits of the Farnell-RAYPCB collaboration
The collaboration between Farnell and RAYPCB brings several benefits to customers who use the element14 platform:
-
Access to RAYPCB’s PCB manufacturing expertise: RAYPCB has over 15 years of experience in PCB manufacturing and offers a wide range of services, including prototype and production PCBs, PCB Assembly, and more. Through this collaboration, element14 users can leverage RAYPCB’s expertise to bring their designs to life.
-
Streamlined PCB ordering process: The integration of RAYPCB’s services into the element14 platform simplifies the PCB ordering process for customers. Users can now easily upload their PCB design files, select their desired specifications, and place orders directly through the platform.
-
Competitive pricing and fast turnaround times: RAYPCB is known for offering competitive pricing and fast turnaround times for PCB manufacturing. With this collaboration, element14 users can benefit from these advantages and receive high-quality PCBs at affordable prices with quick delivery.
How the collaboration works
PCB design and ordering process
The Farnell-RAYPCB collaboration on element14 streamlines the PCB design and ordering process for customers. Here’s a step-by-step guide on how it works:
-
Design your PCB: Use your preferred PCB design software to create your PCB layout. Ensure that your design follows the manufacturing guidelines provided by RAYPCB to avoid any issues during production.
-
Upload your design files: Log in to your element14 account and navigate to the PCB ordering section. Upload your PCB design files, including Gerber files, drill files, and any other necessary documents.
-
Select your PCB specifications: Choose the desired specifications for your PCB, such as the number of layers, material, thickness, surface finish, and more. RAYPCB offers a wide range of options to suit various application requirements.
-
Review and place your order: Double-check your PCB design and selected specifications. If everything looks correct, proceed to place your order. You will receive an order confirmation with an estimated delivery date.
-
Track your order: You can track the status of your PCB order through your element14 account. RAYPCB will provide updates on the manufacturing progress, and you will be notified when your PCBs are shipped.
PCB manufacturing process at RAYPCB
Once your PCB order is placed through element14, RAYPCB takes over the manufacturing process. Here’s an overview of the steps involved:
-
Design review: RAYPCB’s engineers review your PCB design files to ensure they meet the manufacturing guidelines and are ready for production. If any issues are found, they will contact you to resolve them before proceeding.
-
PCB fabrication: The PCB fabrication process begins with the creation of a photoresist film based on your design files. This film is used to transfer the circuit pattern onto the copper-clad laminate through a process called exposure and development. The unwanted copper is then etched away, leaving behind the desired circuit pattern.
-
Drilling and plating: Holes are drilled into the PCB according to your design specifications. These holes are then plated with copper to establish electrical connections between layers.
-
Solder mask and silkscreen: A solder mask is applied to the PCB to protect the copper traces from oxidation and prevent solder bridges during assembly. The silkscreen layer is then added to provide text and symbols for component placement and identification.
-
Surface finish: The exposed copper pads on the PCB are coated with a surface finish, such as HASL, ENIG, or OSP, to protect them from oxidation and enhance solderability.
-
Electrical testing: RAYPCB conducts electrical testing on the manufactured PCBs to ensure they meet the specified requirements and are free from defects.
-
Packaging and shipping: The completed PCBs are packaged and shipped to the address provided during the ordering process on element14.
Case studies and success stories
Customer A: Automotive electronics manufacturer
An automotive electronics manufacturer needed to develop a new PCB for their latest in-vehicle infotainment system. They used the element14 platform to collaborate with RAYPCB and leverage their expertise in high-density interconnect (HDI) PCBs.
Through the streamlined PCB ordering process on element14, the manufacturer was able to quickly prototype their design and iterate based on feedback from RAYPCB’s engineers. The final PCB met all the required specifications and was delivered on time, enabling the manufacturer to bring their new product to market faster.
Customer B: Medical device startup
A medical device startup was working on a new wearable health monitoring device that required a compact and reliable PCB. They used the element14 platform to access RAYPCB’s PCB manufacturing services and benefit from their experience in producing PCBs for medical applications.
RAYPCB’s engineers worked closely with the startup to optimize their PCB design for manufacturability and reliability. The collaboration resulted in a high-quality PCB that met the stringent requirements for medical devices. The startup was able to successfully launch their product and secure funding for further development.
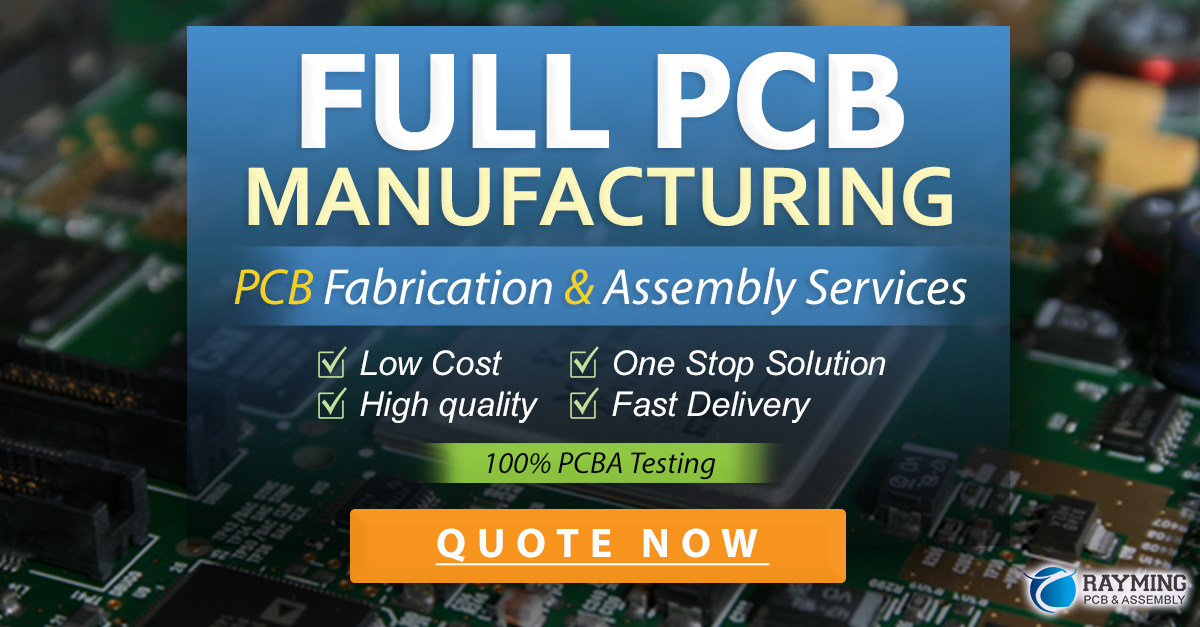
Future developments and enhancements
The Farnell-RAYPCB collaboration on element14 is continuously evolving to better serve the needs of customers in the electronics industry. Some of the planned future developments and enhancements include:
-
Expansion of PCB manufacturing capabilities: RAYPCB is investing in new equipment and technologies to expand their PCB manufacturing capabilities, such as advanced HDI processes, flexible PCBs, and embedded components. These enhancements will enable element14 users to access a wider range of PCB Solutions for their projects.
-
Integration of PCB assembly services: In addition to PCB fabrication, RAYPCB also offers PCB assembly services. The collaboration aims to integrate these services into the element14 platform, allowing customers to order complete PCB assemblies through a single interface.
-
Improved design for manufacturing (DFM) tools: Element14 and RAYPCB are working on enhancing the DFM Tools available on the platform. These tools will help users identify and resolve potential manufacturing issues early in the design process, reducing the risk of delays and additional costs.
-
Educational resources and webinars: To support the electronics community, element14 and RAYPCB plan to offer more educational resources and webinars related to PCB design and manufacturing. These resources will help users stay up-to-date with the latest industry trends and best practices.
Conclusion
The collaboration between Farnell and RAYPCB on the element14 platform represents a significant step forward in providing customers with a seamless experience for PCB design and manufacturing. By combining Farnell’s global distribution network and element14’s online community with RAYPCB’s PCB manufacturing expertise, this partnership enables users to access high-quality PCB solutions with competitive pricing and fast turnaround times.
As the collaboration continues to evolve and introduce new enhancements, it is expected to benefit a wide range of customers in the electronics industry, from startups and small businesses to large enterprises. The success stories of customers who have already leveraged this collaboration demonstrate its potential to accelerate product development and drive innovation in the industry.
Frequently Asked Questions (FAQ)
-
Q: What is the minimum order quantity for PCBs through the Farnell-RAYPCB collaboration on element14?
A: There is no minimum order quantity for PCBs ordered through the element14 platform. Users can order prototype quantities starting from a single piece. -
Q: What are the available PCB Surface Finishes offered by RAYPCB?
A: RAYPCB offers a variety of PCB Surface Finishes, including HASL (Hot Air Solder Leveling), ENIG (Electroless Nickel Immersion Gold), OSP (Organic Solderability Preservative), and more. The specific options available may vary based on the PCB specifications. -
Q: How long does it take to receive PCBs ordered through the element14 platform?
A: The turnaround time for PCBs ordered through element14 depends on the complexity of the design and the selected manufacturing options. Typical turnaround times range from 3-5 days for standard PCBs to 7-10 days for more complex designs. Expedited manufacturing options may be available for urgent requirements. -
Q: Can I request a custom PCB thickness or material that is not listed on the element14 platform?
A: If you have a specific requirement for PCB thickness or material that is not listed on the element14 platform, you can reach out to RAYPCB’s customer support team through the platform. They will assess your request and provide guidance on the feasibility and any additional costs involved. -
Q: What file formats are accepted for PCB design submission on element14?
A: The element14 platform accepts standard PCB design file formats, including Gerber files (RS-274X), drill files (Excellon), and ODB++ files. It is recommended to generate these files from your PCB design software according to the manufacturing guidelines provided by RAYPCB to ensure smooth processing of your order.
Leave a Reply